You’ve worked hard, maybe for years, to invent a plastic product that will either increase efficiency or improve the user experience in some way.
So how do you take that next step? And after that, how do you take it from concept to consumer?
It can be a stressful process figuring out where to start. Here, we’re breaking down everything you need to know to take your plastic product to the next level.
Getting Started
First, talk to a plastic molding company about designing your piece for production.
In order for an injection molder to take your idea to the next level, it needs to be designed specifically for the industry that you wish to target.
Ideally, working with someone that can design and manufacture your product will help make it a smoother process.
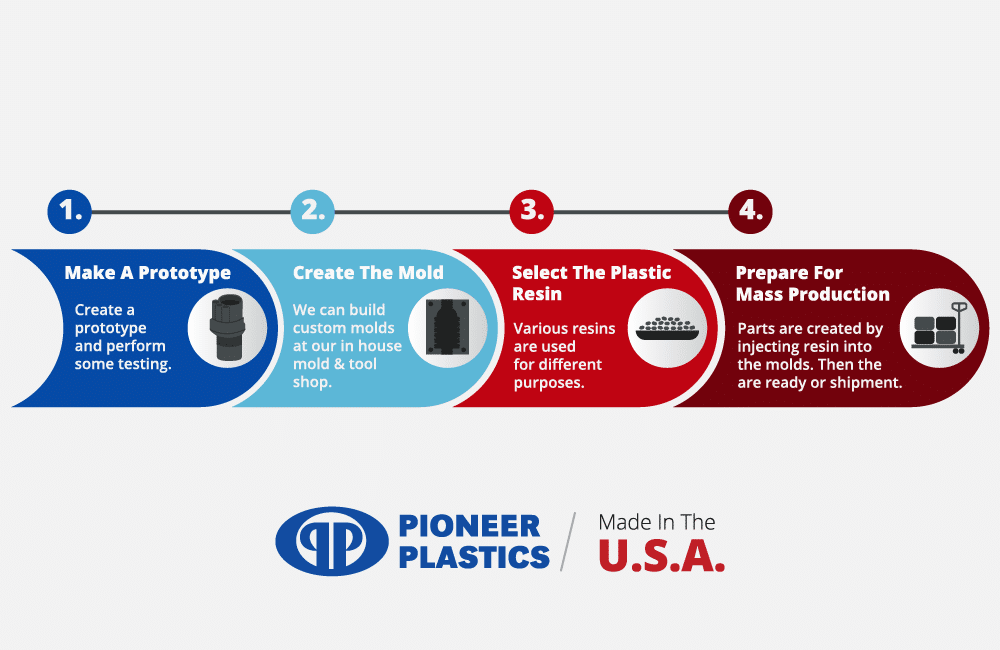
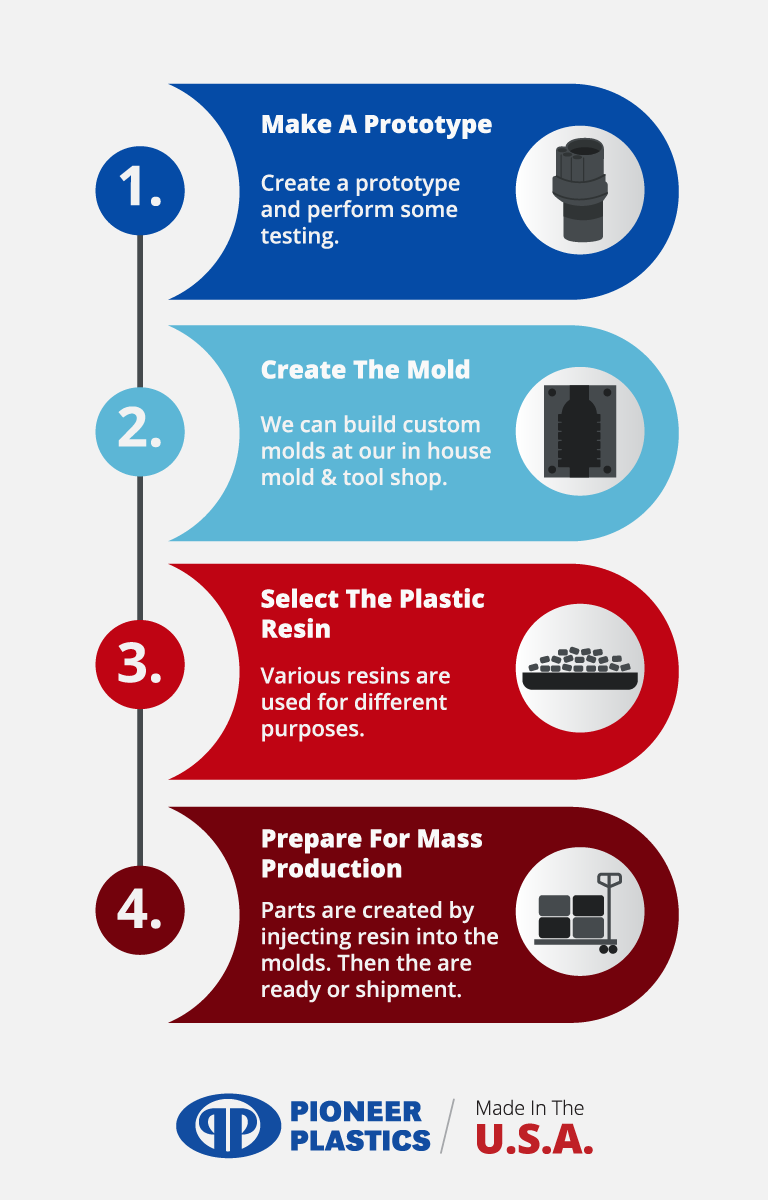
Make a Prototype
They’ll create a prototype that will allow you to experiment with the finished product.
You’ll need to spend some time with it, testing durability and ease-of-use. You have to know that it works correctly first!
Create the Mold
Mold creation is all about building a high-quality injection mold that will produce your part.
Select the Plastic Resin
This is perhaps the most important step.
Once the prototype is approved, the plastic molding company will help you decide what resin would work best for your plastic part. You might not realize it, but each type of resin has a specific use-case. Find out more about resin variations below.
Prep Your Plastic Part for Mass Production
Once you give final approval on the plastic part, a full-service plastic molding entity will begin the molding process. The resin they choose to use for your product will be injected into the mold and formed to the specified shape, creating your part. Then they’ll ship it out to the masses.
Now that you understand the plastic molding process, let’s dive a little deeper into each step.
Design
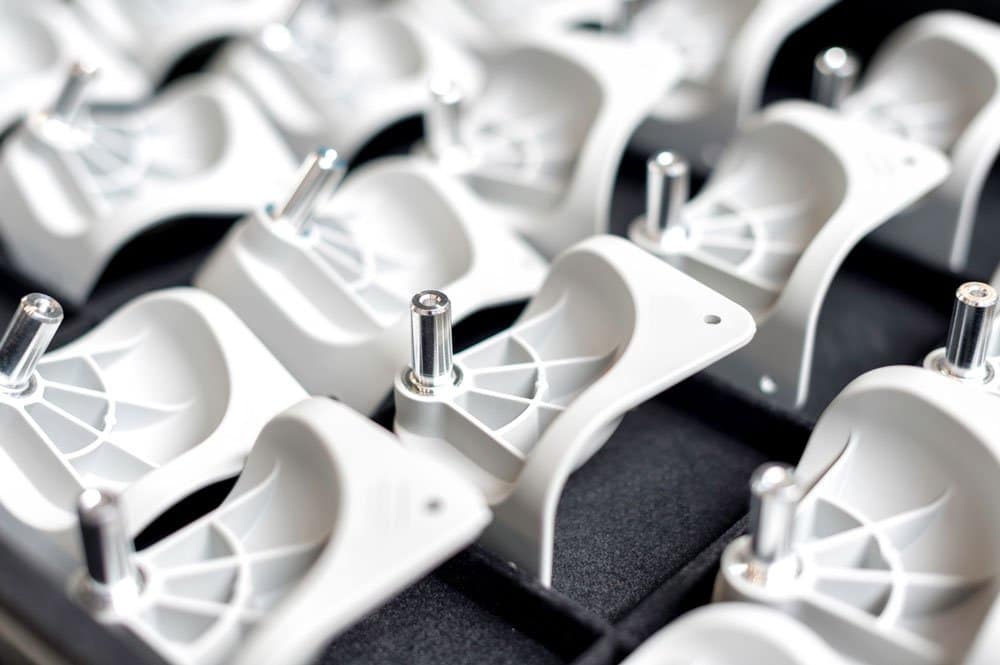
When designing your plastic part, it’s crucial to consider what the part’s fit and function will be.
First and foremost, the function of the product will affect the fit and form of the plastic part in almost every case. So as you draw out your design, make sure you’re cognizant of its fundamental usage.
The Design & Discovery Process
What special properties need to be included to make your plastic part stand out as more functional than potentially competing products?
Ask yourself these function-related questions:
- What is the minimum required strength required for your product to perform successfully?
- What is your product’s intended longevity?
- Does your product need to be created with impact resistance in mind?
These, among many other product-specific questions, should be answered before you worry about the style of your custom plastic product.
Answering these questions provides you with a better understanding of what type of resin should be used to manufacture your part.
Determining Your Product’s Fit
Now that you understand exactly what your part needs to do, you’ll need to figure out what it will look like, how it will feel, and how it will interact with other elements within the product’s environment.The goal is to strive for optimal performance.
In this context, “Fit” refers to how a plastic part mates to another part or occupies a specified amount of cubic inches within a box or on a shelf. *
For Example:
- How a container lid mates to its container
- How the plastic housing envelopes a motor
- How the product occupies shelf space at Walmart
Some Tips for Perfecting Your Product’s Fit
The thickness of the part’s walls should stay consistent whenever possible.
Inconsistencies in the wall thickness can cause the plastic to warp. When the plastic cools, it cools from the outside inward which can cause the outside walls to be pulled inward (called sinks), internal stress, or internal voids.
Make sure the walls of the part aren’t exactly perpendicular
This wall feature is called a draft angle. It allows the part to come out of the mold smoothly. We recommend a draft angle of between 2 and 5 degrees.
Consider Rounded corners
Rounded corners allow material to flow through the part more efficiently. This also reduces stress on the material during the cooling process, in turn reducing its tendency to crack, bow, warp, or have fragile corners.
Make note of parting lines
A parting line is a line where the two halves of the mold meet. This can create a thin blemish around the part depending on how it was designed. If you need a sharp edge on your part, you can reduce blemishes incorporating that edge in the parting line.
Consider hole depth to diameter ratio
Most plastics companies recommend the hole depth-to-diameter ratio to stay under two. There are two types of holes:– Through Holes– Blind Holes
Unlike through holes, blind holes don’t protrude through the plastic part. The pins that are used to make these blind holes shouldn’t be too long, because the heat and pressure can potentially warp the insertion area.
Eliminate undercuts if possible
To save money, it would be wise to avoid using undercuts. Undercuts will almost always result in a more expensive part, due to a more complex mold design and typically more process time is needed to create them.
An undercut is any protrusion or indentation that houses any non-standard mating part of the plastic. (For example: A T-shaped connector)
Consider utilizing ribbed features
If you want to strengthen the molded part without adding additional wall thickness, ribbing is a great way to accomplish this. Taller ribs can lead to issues like warping and bending. But if your piece has subtle and simple ribbing, it should serve the function well.
How to Design Your Plastic Part For the Shelves of Walmart and Other Retailers
It’s all about the cubic inches.
Let’s say you own an ice cream company, and you’re hoping to modernize the ice cream container so that it increases user-friendliness and fits perfectly in the frozen section at Walmart.
You’ll need to design for a specific amount of shelf space.
It’s important to know that this shelf space allotted varies for each product type. For example, Walmart won’t accept a 10-gallon ice cream tub.
Your contact for any of these big box retailers will be able to provide you with the exact amount of cubic inches your product can occupy. Be careful, because if you don’t abide, they don’t have to stock your product.
Design Hint: You’ll need to understand the Supplier Standards, obtain a Universal Product Code (UPC), and you must carry Product Liability Insurance to sell your product in big box stores.
Also, you’ll need to notify your plastic part manufacturer that the retail market is your end goal!
Mold Making
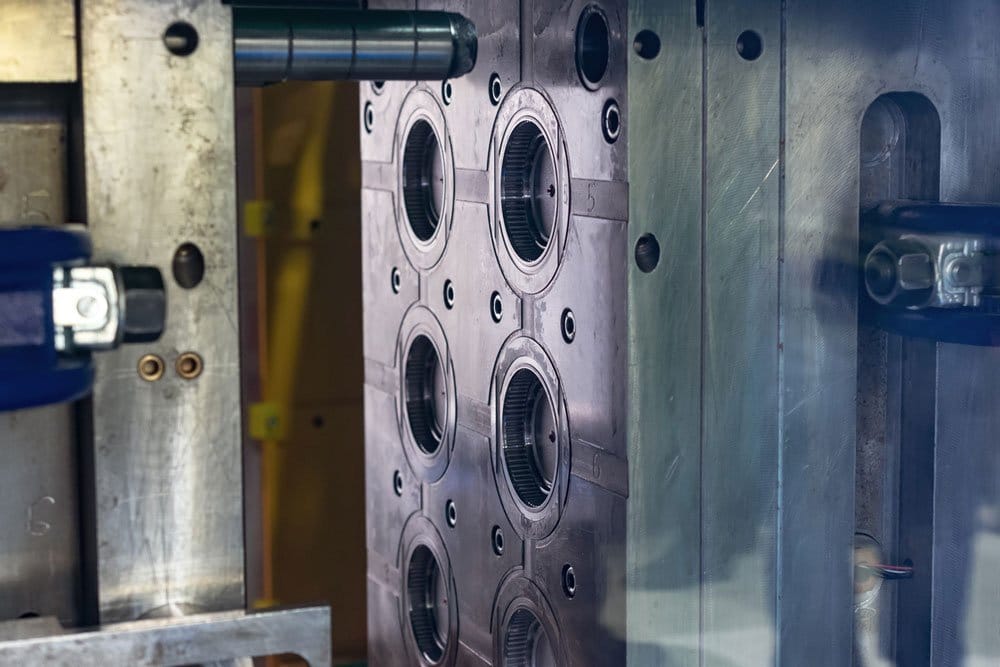
First, after a part is designed, a skilled tool and die craftsman using state-of-the-art machining like lathes, mills, or CNC machines creates a plastic injection mold out of metal. This mold is created precisely for the specific plastic part.
Then, this mold is transferred to an injection molding machine, where the actual “molding” occurs.
Plastic part manufacturers typically have various sizes of plastic molding machines that are capable of manufacturing different-sized parts. For example, Pioneer Plastics currently operates 22 modern plastic injection molding machines ranging from a 75-ton to an 880-ton clamp force.
An Example of a Larger Machine – The Cincinnati
- 880-ton clamping force
- 232 oz shot size (1000 ton platen size)
Product Capabilities for Larger Plastic Molding Machines:
Larger machines can produce pieces like refrigerator shelves, vent covers, washer and dryer doors, and much more.
An Example of a Small Machine – The Nissei
- 75-ton clamping force
- 5 oz shot size
Product Capabilities for Smaller Plastic Molding Machines:
Smaller machines like the Nissei are capable of producing plastic parts as small as golf tees, tacks, toy car display cases, buttons, and various other small items.
What is clamping force? Clamping force refers to the force applied to the mold (or plastic part) by the clamping unit of an plastic molding machine. In general, the bigger the part, the more clamping force required.
What is shot size? Shot size refers to the maximum amount of plastic that can be injected in one cycle of injection molding. The bigger the part, the larger shot size required.
So How Do These Injection Molding Machines Actually Work?
Since this can be a complicated process, we’ll compare it to the process of making fun Jell-O® shapes.
- Resin (a pile of plastic pellets) is fed into a hot, cylindrical barrel and is melted into a liquid. This is like when you mix the boiling water with gelatin in a big bowl.
- This molten plastic is mixed together with a large screw, which pushes it into a mold cavity. Think of this cavity as the Jell-O mold. It’s where the material forms to the specific shape.
- The resin inside this mold needs to cool. This is like when you let the Jell-O sit in the fridge for a few hours to form.
- The plastic part is ready to use! The Jell-O is ready to eat!
To boil it all down, these machines inject resin into a mold, which shapes the polymer into a functional plastic part after it’s cooled.
There are also plastic molding machines used specifically for assembly & decoration:
The assembly and decoration processes occur after the plastic parts undergo the injection molding process.
- Assembly – the pieces of plastic parts are connected (if necessary)
- Decoration – Hot stamping, in-mold labeling, and printing are some methods used to decorate the plastic parts.
Resin
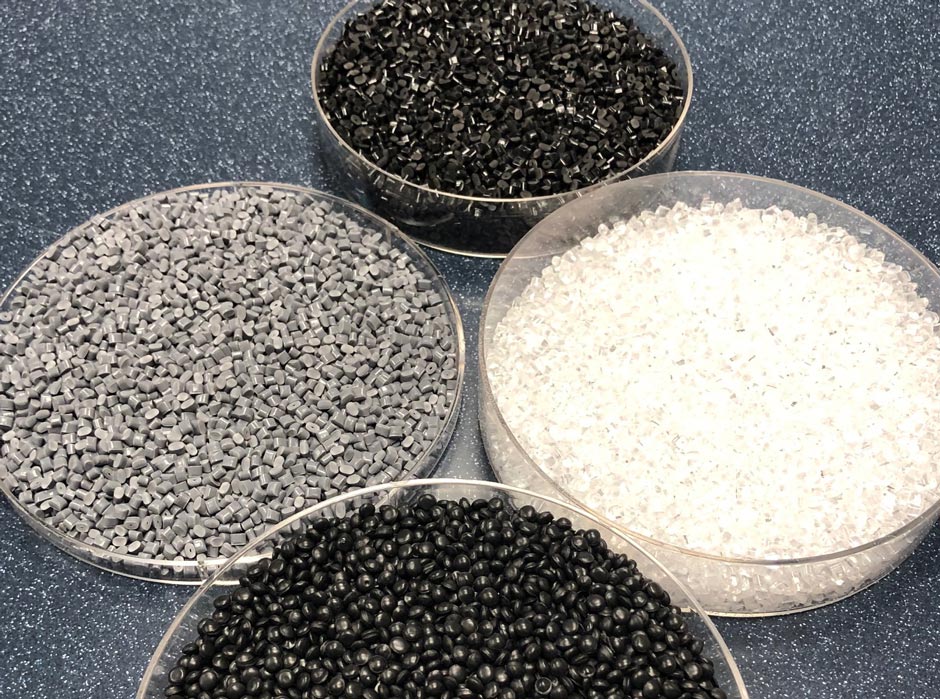
Resin is the plastic material that everything plastic is made of.
Once heated, Resin is a free-flowing polymer used in plastic part production. In the injection molding industry, this highly-viscous material is what’s actually injected into the mold to create a product.
Resin starts in pellet form. You’ve probably seen them before.
Resin pellets are typically either cylindrical or disc-shaped. Here are some styles of resin pellets that most plastic molding facilities offer:
- Low-density polyethylene pellets
- High-density polyethylene pellets
- Linear low-density polyethylene pellets
- Polystyrene pellets
- Polypropylene pellets
- Polyethylene terephthalate pellets
- Polyvinyl chloride pellets
How Do You Choose the Right Type of Resin?
One of the most important parts of the manufacturing process is picking out the best type of resin for your plastic product.
There are over 100 different varieties of resin. So how do we choose the right one?
First, we get a good understanding of what your product is going to be used for. Then, using our knowledge of the industry, we’ll pick the resin based on those needs.
For example:
- Some products need a material that can handle high heat.
- Some need a material that can handle chemicals.
- Some need FDA approval.
- Some need to be crystal clear.
- Some need impact resistance.
- Some need to be able to hold a lot of weight.
- Some need a combination of the above.
Based on these unique product needs, we will find the resin to meet your needs.
There Are Two Grades of Resins:
- Commodity Grade Resin
- Engineering Grade Thermoplastic Resin
What’s the Difference?
Commodity grade resins are usually less expensive, and they’re typically easier to manipulate and process. This is usually the material used in consumer products like toys and packaging.
Examples of commodity grade resins:
- Polypropylene
- Polyethylene
Engineering Grade Thermoplastic Resin, while more expensive, has better thermal properties than commodity grades.
Because of this ability to withstand extreme temperatures and corrosion, this extremely durable material is usually used in equipment where there’s frequent friction.
For example, engineering grade resin is commonly used for items like replacement bearings or other steel parts.
Examples of engineering grade resins:
- Nylon
- Polycarbonate
High Heat
Most plastics used in the market are only suitable for use at temperatures below 275°F. Resins that are resistant to high heat can withstand temperatures ranging from 275°F to 500°F without losing its shape and/or properties.
Uses
Plastics that are resistant to high temperatures are a light, versatile alternative to metal, ceramics, and older-generation polymers.
Thermoplastic material is most commonly used in consumer products (like milk jugs) that won’t need to withstand very high temperatures. Thermoplastics are also great for prototyping because the material can be reused for another prototype or for final production. Thermoset material is most commonly used for parts that need to withstand extremely high temperatures.
Examples of industries that use thermoset (high heat) resins in their products are:
- Automotive – gears, hot fuel systems, fuel reservoirs, ignition modules, oil screens.
- Aerospace – lightweight aerospace components like brackets, gaskets, guides, seals, spacers, and washers.
- Electrical – wiring, cabling, sleeving and electrical shielding products.
- Medical – electronic equipment.
- Industrial – Welding masks.
- Restaurants – Pans, lids, and trays.
FAQ's About Injection Molding
If you have an idea for a custom plastic part, you may have a lot of questions about the manufacturing process. Injection molding is a time-efficient and cost-efficient way to achieve the quality part you need.
Here are answers to some of the most frequently asked questions about custom injection molding:
How do you know if injection molding is the right process for a product?
There are several ways to manufacture a plastic part. Understanding and knowing the part design, the end function of the part, the quantity needed, and the target part cost will help determine if injection molding is right for you.
What is the minimum number of units required for a new plastic molding project?
Due to the high cost of the plastic mold ($10,000 – $200,000), injection molding is typically a good choice if you need a higher volume/quantity of your part. If you only need 100 parts, injection molding may not be right for you. This depends on your budget and how critical the part design is to your project’s success.
Will a prototype be tested for durability and usability before the mold and lot are produced?
Sometimes yes, only if the customer requests it and or if it’s recommended by our engineering team. There are two types of prototypes: prototype parts made by a 3D printer (extremely small volume) and prototype molds (which will produce exactly what the production mold will produce). The prototype mold is used to produce many parts for sizing and extensive physical testing, prior to production mold build.
How do you know what type of resin is best for a product?
Since there are over 100 different types of resins, we’ll need a good understanding of your vision for the product and what it will be used for. If it needs to have physical requirements like a special color or specific heat resistance, among many other possible factors will help determine which type of resin will meet those needs. Learn more about resins here.
How long does it take to build a new mold?
Depending on the complexity of the part, the number of cavities (parts in the mold), and the size of the mold, it can take anywhere from 2 to 26 weeks to build a new mold.
What Goes Into The Cost of Plastic Molding?
No two plastic molding projects are the same, so working with someone that understands all the aspects of part design and manufacturing is important.
Prototyping
You might want to test your concept with a prototype to make sure that it fits and functions well. The cost of a prototype depends on two things: the completeness of the design and the size of the part being designed.
If a design is flawless, it will likely be easy to get a prototype 3D-printed. On the other hand, if a lot of design work is needed before it can be printed, designing could be the most expensive part of the process. Here are a few scenarios that illustrate this:
- For a small part (1” square) with a good design, the prototype can be done for under $100.
- A concept for that same part but with no design could cost around $2,000 for design work and under $100 for the prototype.
- For a large part (24” square) with a good design, the prototype could cost around $2,000.
- A concept for that same part but with no design could get up to $10,000 for design work and $2,000 for the prototype.
Mold & Size
When the part is ready for production, the mold needs to be built. One of the biggest drivers of cost is the size of the part. If a part is bigger, it’s going to require more material, tooling, and time to build the mold.
In looking at parts with simple designs, a small part with simple design could have a mold cost between $10,000 – $20,000. A small part with no design work could have the same mold cost with $2,000 added for design.
For large parts with a simple design, the mold could cost between $30,000 – $100,000. If the part is large but has no design work, it will have an additional $10,000 added for design.
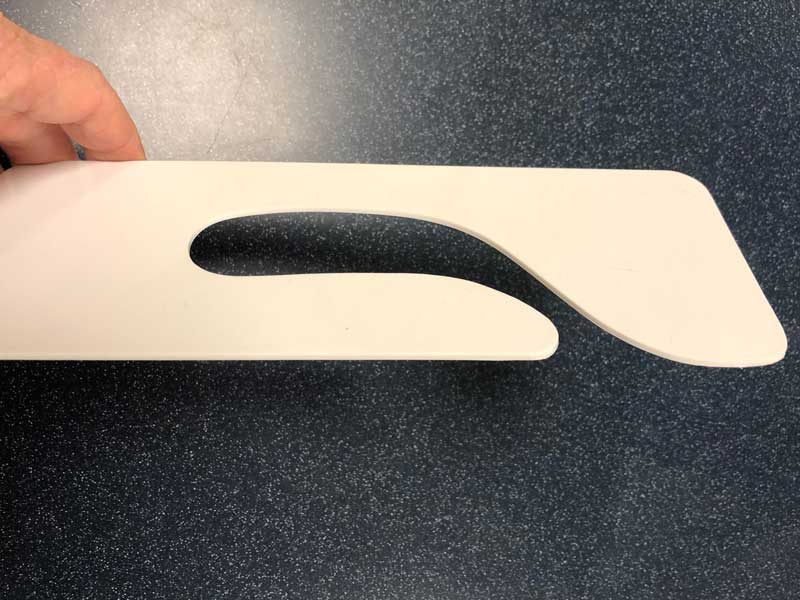
Complexity
Similarly, the more complex the part is, the more time it takes to make the mold – and, well, time is money. Some parts may require cams, lifts, or core pins, which are additions to the mold that help achieve certain features a part may require. If the part has a higher volume, the mold would require more cavitation (parts molded per cycle) which adds cost to the mold and parts handling equipment (conveyors, chutes, bowl feeders, robots, etc.).
In addition, if the demand for a part is very high (hundreds of thousands of pieces), a multi-cavity tool may be required which also increases the cost.
In looking at parts with complex designs, a small part with complex design could have a mold cost between $20,000 – $40,000. A small part with no design work could have the same mold cost with $2,000 added for design.
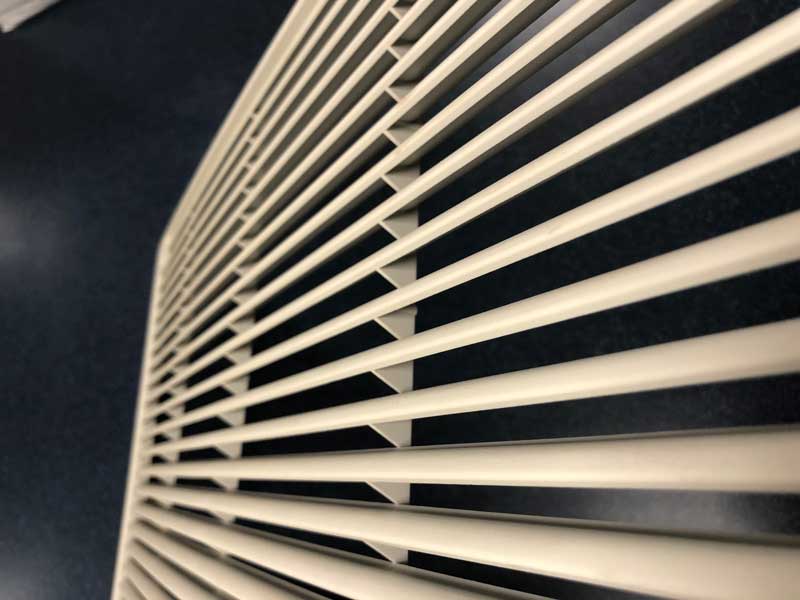
Resin
With over 100 different varieties of resin, it can be difficult to determine which one is best for your part. Once we understand the characteristics that the part requires and the end use of the part, we can help you narrow down choices and choose the ideal option. Some examples of these characteristics are:
- Requires FDA approval
- Resistant to impact
- Chemical resistant
- Transparent
- Durable against high temperatures or low temperatures
Commodity grade resins are typically less expensive than engineering grade resins. However, engineering grade resins will likely be able to withstand extreme temperatures and friction better than commodity resins. Understanding the purpose and function of the part will ultimately determine the best material for it.
Additional Services
There are services that you might want in addition to the creation of the mold and the part. This plastic molding technology allows you to customize your part in many different ways.
- In-mold decorating allows for colorization, stylization, and other effects to be added during the molding process.
- Pad printing allows for two-dimensional images to adhere to three-dimensional plastic products.
- Plastic packaging can be designed and created specifically for your product.
- Assembly can be conducted for complex parts.
Advantages of Plastic Molding
Injection molding is one of the most versatile processes for creating a custom plastic part. There are many benefits to the plastic molding process.
Strength & Stability
The injection molding process offers numerous ways to ensure parts are strong and durable. Wall thickness, ribs (for support), and material selection are just a few options.
Thicker walls are more expensive due to longer cycle times and more material but can provide a very durable part.
Ribs in key areas can give extra durability where needed and not have the cost issues of thicker walls.
Parts made from engineering-grade resins are able to withstand extreme temperatures, friction, and corrosion. This makes them more durable than commodity grade resins, which are typically used in consumer products like packaging.
Environmentally Friendliness
Parts that are plastic injection molded tend to last longer due to their quality and strength which reduces the number of parts that get thrown away over time.
The plastic molding process doesn’t waste materials. When a broken or unusable part is produced, it can be remelted and reused.
Complex Capabilities
A variety of sizes, colors, shapes, and finishes can be created through custom injection molding.
Techniques like insert molding are used to inject resin over another material. An example of this is threaded fasteners that have metal in the center and a plastic shell. Overmolding is most commonly used to enhance the appearance or function of a part, like adding a softer layer of resin to the handle of a part.
It can be used for assembly and decoration, as well. If pieces need to be labeled or decorated, in-mold labeling may be used. Connectivity techniques like heat staking and ultrasonic welding can be used to join two or more parts together.
Cost-Effectiveness
It is important to pick a partner that handles the entire process – from design to actual injection molding. This is much more cost-effective because the process is handled by one manufacturer from design to distribution.
Injection molding can handle large scale production without compromising quality or adding manufacturing costs. If you’ll be producing a large volume of your part in every run, plastic molding will be a cost-effective option.
Flexibility in Design
All of the needs mentioned above can be solved with a good design. Pioneer Plastics has over 200 years of injection molding engineering experience in our design team – we know what makes a good part based on what your needs are.
Before the mold is created, we can create a prototype of the part using our 3D-printer. This allows you to experiment with the product and make any necessary adjustments before the mold is built.
Plastic Molding Defects & How to Avoid Them
Here is a list of common injection molding defects and how to avoid them:
Flow Lines
Flow lines are lines commonly caused by a variation in the cooling speed of the material as it flows through the mold. They often appear in a wavy pattern and might be a slightly different color than the rest of the piece. Flow lines don’t typically impact the integrity of the piece, but they can be unsightly and unacceptable in certain products (like high-end frames for glasses).
How to Avoid Them:
Flow lines can be avoided by increasing the injection speed and pressure to ensure the material fills the mold before cooling. You can also try rounding the corners of the mold to increase wall thickness and keep flow rate consistent.
Burns
Burns can be caused by trapped air or overheated resin in the mold during injection. Excessive heat or increased plastic injection speeds can cause overheating, in turn causing the resin to burn. Burns can appear as black or brown colored spots on the edge or surface of the part.
How to Avoid Them:
To prevent burns, lower the melt and mold temperature to prevent overheating, reduce the injection speed to limit the risk of trapping air, and shorten the mold cycle time so that trapped air and resin doesn’t have time to overheat.
Warping
Most commonly heard when referring to wood that has dried unevenly, warping is a deformation that appears when different components of the plastic part shrink unevenly. During the cooling process, uneven shrinkage can put stress on parts causing bending or twisting. Most often, the cause of warping is the cooling process happening too quickly.
How to Avoid It:
Warping can be prevented by ensuring the cooling process is long enough to prevent uneven stresses on the material and by lowering the temperature of the material or mold.
Sinking
Sink marks are depressions on an otherwise flat surface of a part. These can occur when the inner part of the mold shrinks (or cools too slowly), pulling the outside inward before it has a chance to completely cool.
How to Avoid It:
To avoid sinking, increase cooling time and increase holding pressure to allow the material at the part’s surface to cool.
Air Pockets
Air pockets are trapped air bubbles in the finished part. Air bubbles are commonly caused by inadequate pressure to force air out of the mold. Larger air pockets can weaken the part.
How to Avoid Them:
To avoid air pockets in the mold, raise the injection pressure to force out trapped air pockets.
Weld Lines
Weld lines are a result of weak material bonding. They appear on the surfaces of parts where the material has come back together after splitting into two or more directions in the mold. If the material bonding is weak, the overall strength of the part is lowered.
How to Avoid Them:
Weld lines can be avoided by increasing the material temperature to prevent uneven solidification and increasing injection speed and pressure to limit cooling before the mold is filled.
Jetting
Jetting occurs in molded parts when the initial jet of molten material starts solidifying before the rest of the material fills the mold. Jetting looks like squiggly lines on the surface of the part.
How to Avoid It:
Jetting can be avoided by reducing injection pressure (to prevent rapid movement of the material into the mold) and increasing material and mold temperature (to keep the material from solidifying too early).
Turnkey Plastic Injection Molding
Turnkey injection molders, like Pioneer Plastics, are full-service manufacturers who build the mold and handle the injection molding process. Keeping the part in-house from beginning to end makes the process more time-efficient and cost-efficient.
Being skilled in all aspects of the process allows us to help you with design, selecting materials, and any questions you may have. Contact us to get started on your custom part.