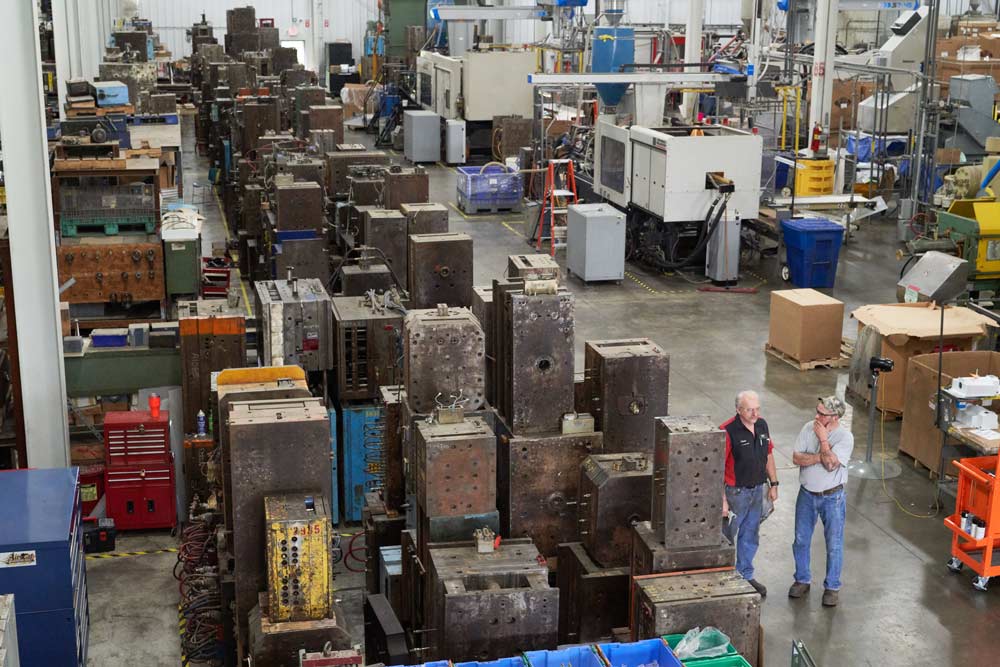
How Machinery is Used in Custom Injection Molding
When we hold plastic parts in our hands, we usually aren’t thinking of how it was manufactured or what machines were used in the process.
Our in-house tooling and design experts handle custom injection molding and plastic part design with quality and precision, lowering your labor costs, saving you time and money.
We can produce high quantities of parts at a fraction of the cost without compromising quality. When you work with one partner from design to production the entire injection molding process is much more cost effective.
Our experienced design engineers can help create prototypes using our 3D printers to ensure the perfect design of your custom part. Extremely complex parts can be created with our injection molding process.
Our manufacturing process allows for a rapid turnaround which saves you money.
Our custom plastic parts are made with engineering-grade resins making them durable and long-lasting. Our injection molding process also ensures strong parts by incorporating thick walls and ribs.
The plastic injection molding process is repeatable and produces low waste. Scrap can be remelted and reused in another mold. Our plastic parts are also high quality and long lasting so fewer are thrown away.
We work through design and details to simplify your plastic product, always thinking about the end use for when it comes time to assemble.
Our in-house rapid prototyping, custom plastic injection mold design, mold making, and production of tools give your company the ability to transform your project from concept to reality.
Pioneer is the industry leader for plastic product distribution and shipping. We ship your finalized product directly to you, your consumers, or your retail partners.
Work with our experienced engineering and design team to bring your product concept to reality. We offer rapid prototyping and short lead times so your product can be in the hands of the consumer quicker. We use engineering grade resin that is injected into molding machines. All of our products go through a rigorous quality control inspection process so your final product is perfect and ready for shipment.
Our toolmakers are fully equipped to manage the the development and build of new molds, operate molds and service and maintain tools.
Good design and engineering is the key to high quality parts for lower costs. Pioneer Plastics has over 200 years of injection molding company experience in our design team – we know what makes a good part based on what your needs are. You will get to work directly with our engineers who have access to state-of-the-art-equipment.
Before the mold is created, we can create a prototype of the part using our 3D-printer. This allows you to experiment with the product and make any necessary adjustments before the mold is built.
Pioneer Plastics’ advanced 3D printing technology provides a fast and efficient solution for prototyping and low-volume production with precision and versatility.
Custom injection molding is the ideal cost-effective solution for scaling the production of large quantities of products. Custom injection molding allows for even the most complex parts to be produced quickly.
Simply put, plastic, also known as resin, is melted down and poured (or injected) into molds that are in the shape of the final product. Once the plastic cools and hardens, the final product is removed from the molds.
Due to the high cost of the mold, injection molding is typically a good choice if you need a higher volume/quantity of your part. If you only need 1,000 parts, injection molding may not be right for you. This depends on your budget and how critical the part design is to your project’s success.
Depending on the complexity of the part, the number of cavities, parts in the mold, and the size of the mold, it can take anywhere from 2 to 26 weeks to build a new mold.
Yes, all molds at Pioneer Plastics are on a PM (preventive maintenance) schedule.
Any industry can benefit from plastic injection molding. However, some of the most common industries we work with include, food & beverage, agriculture, food packaging, arts & crafts, and home appliance industries. Other industries that commonly use injection molding include aerospace, medicine, industrial manufacturing, sports equipment, electronics and consumer products.
Injection molds can cost anywhere from $10,000 – $100,000+ depending on size and complexity. If your product only requires 1,000 pieces, this may not be the solution for you.
Depending on the product and it’s usage, different plastic materials can be used. The 4 most common are:
We are committed to taking your concept and turning it into a reality that is ready to ship directly to the end consumer. In addition to injection molding we also offer:
Re-shoring your production to the United States ultimately gives you more control. Global events have made global supply chains unpredictable and unreliable.
When you move production back to a reliable injection molding company in the U.S., your designs are more protected, quality of products is higher and your distribution costs are likely to decrease.
We place a high demand on client retention. We understand how difficult customers are to find within the injection molding industry, and how important they are to keep. We strive to go above what's required to make sure our clients know we value their business.
Please fill out the form below, chat with us, or call 1-800-951-1551.
Before you proceed with your inquiry for custom injection molding services, please consider the following to ensure this is the right fit for your needs:
Custom injection molding involves significant up-front costs, typically ranging from $10,000 to $250,000, influenced by the size and complexity of the mold. If your project involves producing 1,000 units or fewer, alternative manufacturing methods may be more cost-effective.
When we hold plastic parts in our hands, we usually aren’t thinking of how it was manufactured or what machines were used in the process.
Are you struggling with getting plastic replacement parts from your supplier? Short run plastic production could be the game-changer you’ve been searching for. By embracing this
As the demand for higher-performing plastics mounts, advanced features that enhance product usability and aesthetics are becoming more common. However, integrating undercuts, thin walls, living