When we hold plastic parts in our hands, we usually aren’t thinking of how it was manufactured or what machines were used in the process.
However, if you take a closer look at the intricacies of the product, you’ll realize that it takes a very sophisticated process and similarly sophisticated machinery to make that part.
Here’s a helpful guide that explains what these machines are and how they work.
First, after a part is designed, a skilled tool and die craftsman using state-of-the-art machinery like lathes, mills, or CNC machines creates a mold out of metal. This mold is created precisely for the specific plastic part.

Then, this mold is transferred to an injection molding machine, where the actual “molding” occurs.
Plastic part manufacturers typically have various sizes of injection molding machines that are capable of manufacturing different-sized parts.
For example, Pioneer Plastics currently operates 22 modern plastic injection molding machines ranging from a 75-ton to an 880-ton clamp force.
An Example of a Larger Machine – The Cincinnati
- 880-ton clamping force
- 232 oz shot size (1000 ton platen size)
Product Capabilities for Larger Machines:
Larger machines can produce pieces like refrigerator shelves, vent covers, washer and dryer doors, and much more.
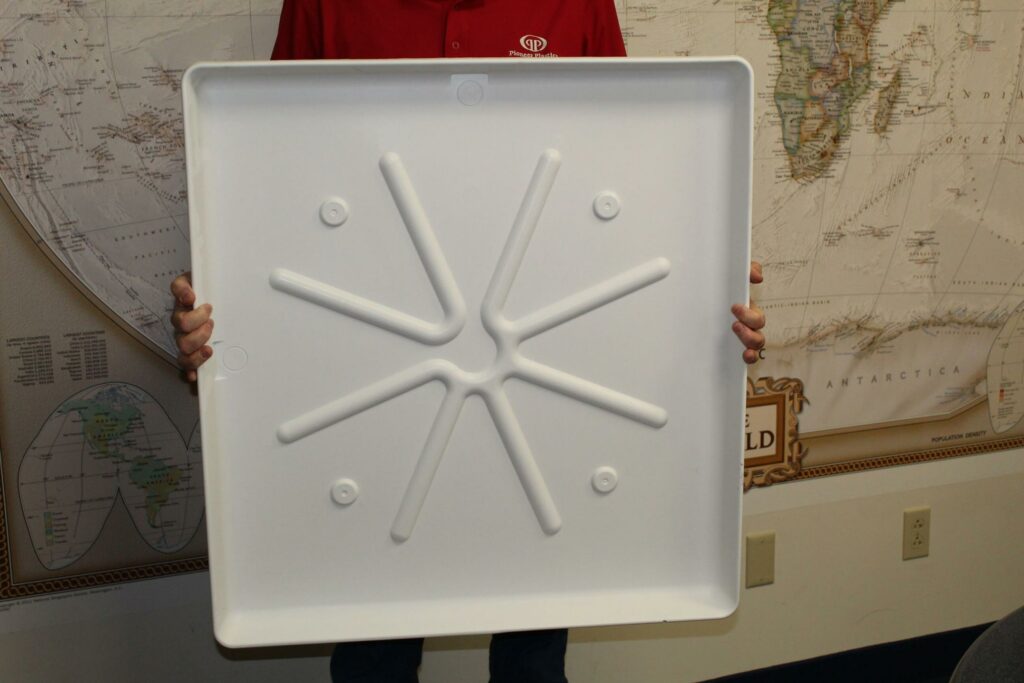
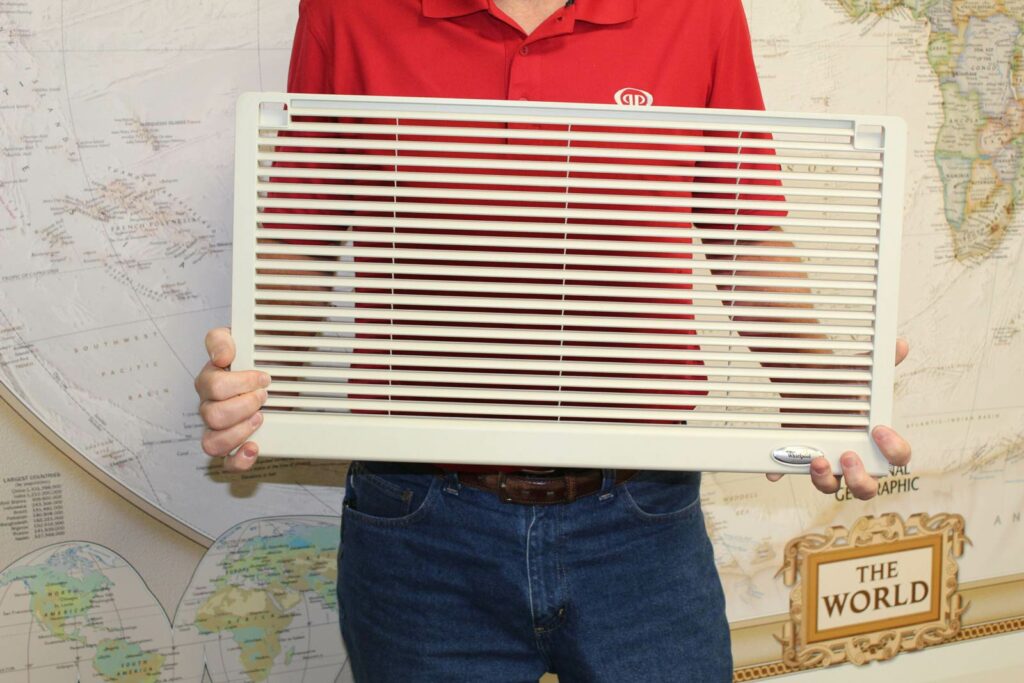
An Example of a Small Machine – The Nissei
- 75-ton clamping force
- 5 oz shot size
Product Capabilities for Smaller Machines:
Smaller machines like the Nissei are capable of producing plastic parts as small as golf tees, tacks, toy car display cases, buttons, and various other small items.
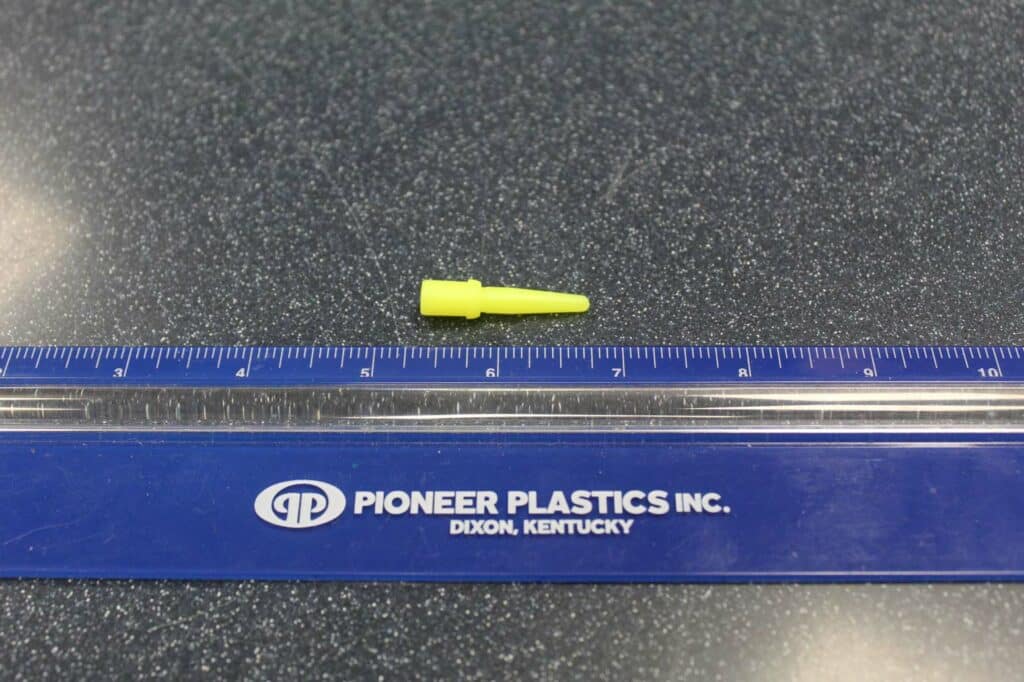
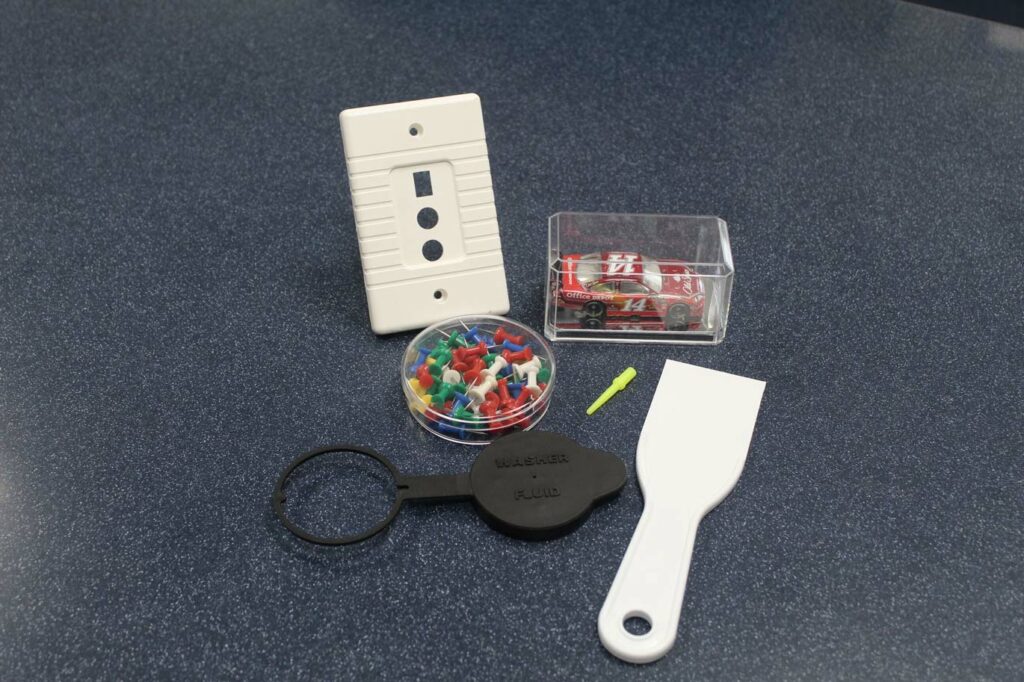
Clamping force refers to the force applied to the mold (or plastic part) by the clamping unit of an injection molding machine. In general, the bigger the part, the more clamping force required.
What is shot size?
Shot size refers to the maximum amount of plastic that can be injected in one cycle of injection molding. The bigger the part, the larger shot size required.
So How Do These Injection Molding Machines Actually Work?
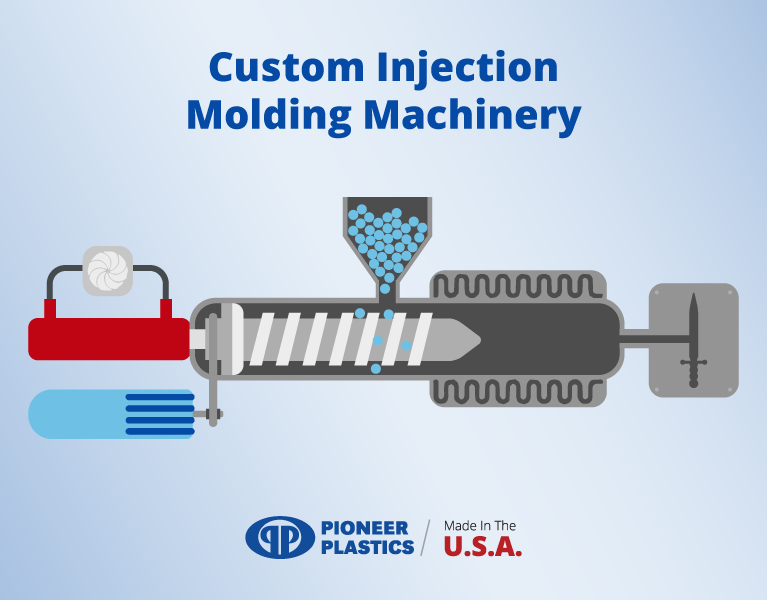
Since this can be a complicated process, we’ll compare it to the process of making fun Jell-O® shapes.
- Resin (a pile of plastic pellets) is fed into a hot, cylindrical barrel and is melted into a liquid.
This is like when you mix the boiling water with gelatin in a big bowl. - It’s mixed together with a large screw, which pushes the resin into a mold cavity. Think of this cavity as the Jell-O mold. It’s where the material forms to the specific shape.
- The resin inside this mold needs to cool.
This is like when you let the Jell-O sit in the fridge for a few hours to form. - The plastic part is ready to use!
The Jell-O is ready to eat!
To boil it all down, these machines inject resin into a mold, which shapes the polymer into a functional plastic part after it’s cooled.
There are also machines used specifically for assembly & decoration:
The assembly and decoration processes occur after the plastic parts undergo the injection molding process.
- Assembly – the pieces of plastic parts are connected (if necessary)
- Decoration – Hot stamping, in-mold labeling, and printing are some methods used to decorate the plastic parts.
Assembly & Decoration Machines
- 1000 watt ultrasonic welders
- Vertical hot stamp machines
- Horizontal roll-on hot stamp machines
- Heat transfer machine
- Pad printer
- Blister pack machine
The injection molding process requires an incredible amount of machinery to produce one small piece of functional plastic. However, these plastic parts, along with the equipment involved, create the backbone to many industries like food processing, packaging, and home appliance manufacturing.
If you’d like to learn even more about the custom plastic part manufacturing process, click here.
Why choose Pioneer Plastics to create your next plastic part?
Our 100,000+ square foot production and distribution facility is located in the heart of the Midwest, just a few hours from Indianapolis, St. Louis, Louisville, and Nashville. We have excellent access to all major transportation networks, allowing us to ship your products efficiently.
If you have a design for a plastic part or a custom injection molding project, contact us to see what Pioneer Plastics can do for you.
Regardless of the size of your plastic part, we can produce it.