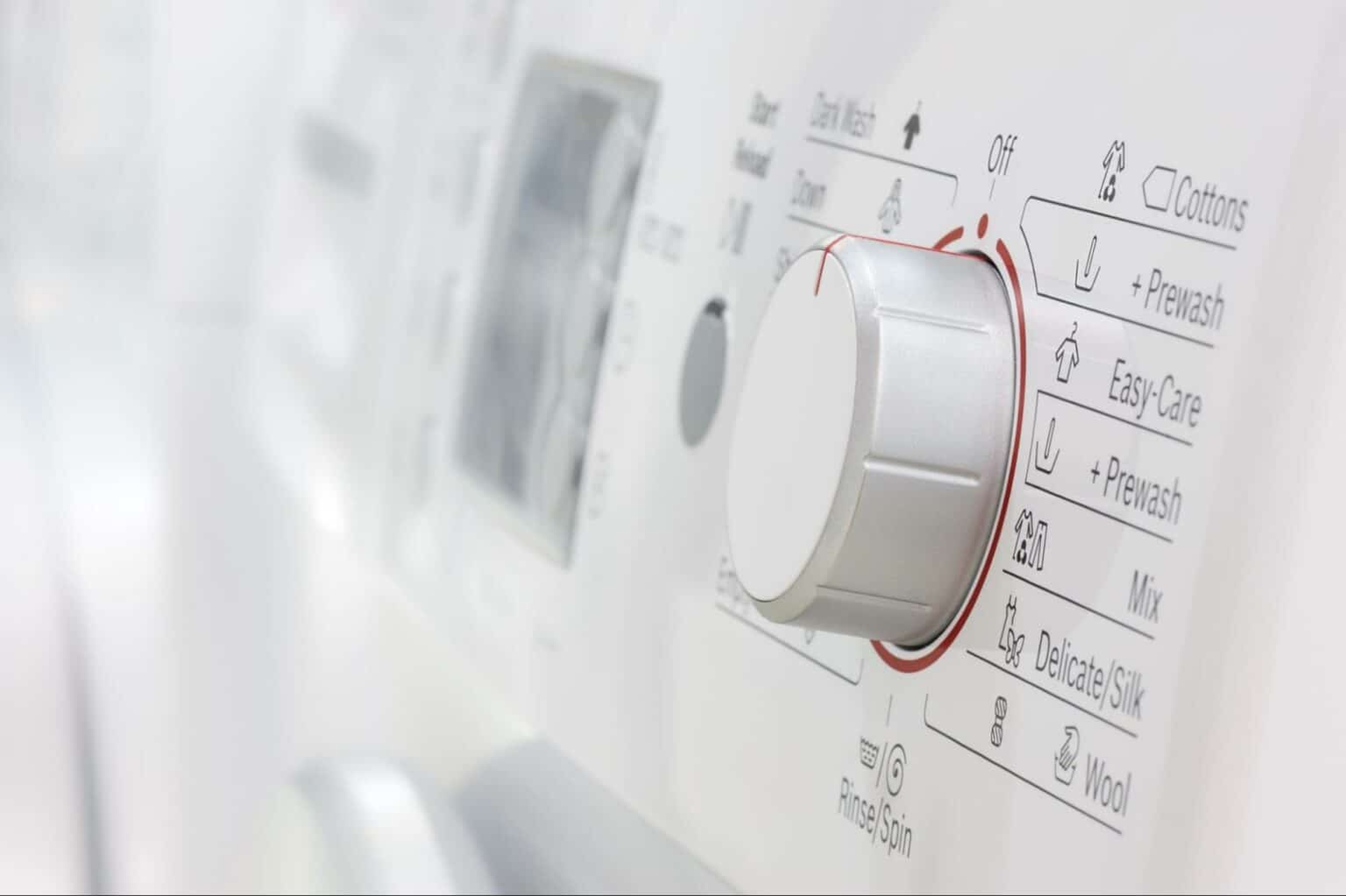
Revolutionize Your Appliance Manufacturing with Smart Short Run Plastic Production
Are you struggling with getting plastic replacement parts from your supplier? Short run plastic production could be the game-changer you’ve been searching for. By embracing this