In the intricate world of injection molding, both hydraulic and electric injection presses are used for custom injection molding projects.
While hydraulic machines have been the backbone of the industry for decades, electric machines have been gaining popularity in recent years.
This blog post seeks to demystify the similarities and differences in these machines, offering a comprehensive comparison of aspects such as energy efficiency, precision, and applicability.
Understanding the Custom Injection Molding Process
Custom injection molding is a highly versatile process used to manufacture a vast range of plastic parts in large quantities. It involves injecting molten plastic material into a mold cavity, allowing it to cool and solidify before ejecting the finished product.
This process is highly versatile and can be used to create a wide range of plastic parts, from simple to complex shapes. These parts can also vary in size and material, making the type of machinery used a critical factor in achieving the desired results.
How Does the Process Work?
The injection molding process starts with the design of the mold, which is then created out of steel or aluminum. The mold consists of two halves, a stationary half and a moving half. The two halves are clamped together, and plastic material is injected into the mold cavity, where it takes the shape of the part. The mold is then cooled, and the solidified part is ejected, ready for finishing and assembly.
What is "Shot Size" and Why Is it Important?
In custom injection molding, “shot size” refers to the amount of molten material injected into the mold cavity during a single injection cycle. It is measured in ounces or grams and is a critical parameter in determining the size and weight of the final molded part.
The shot size requirement varies depending on the specific part being produced, and different machines are designed to accommodate different shot size ranges.
The Role of Hydraulic and Electric Injection Molding Machines
Injection molding machines are the backbone of the custom injection molding process, providing the necessary pressure and force to inject the material into the mold cavity. While there are various types, two main categories are hydraulic and electric injection molding machines. Each type has its unique strengths and capabilities, making them suitable for different applications.
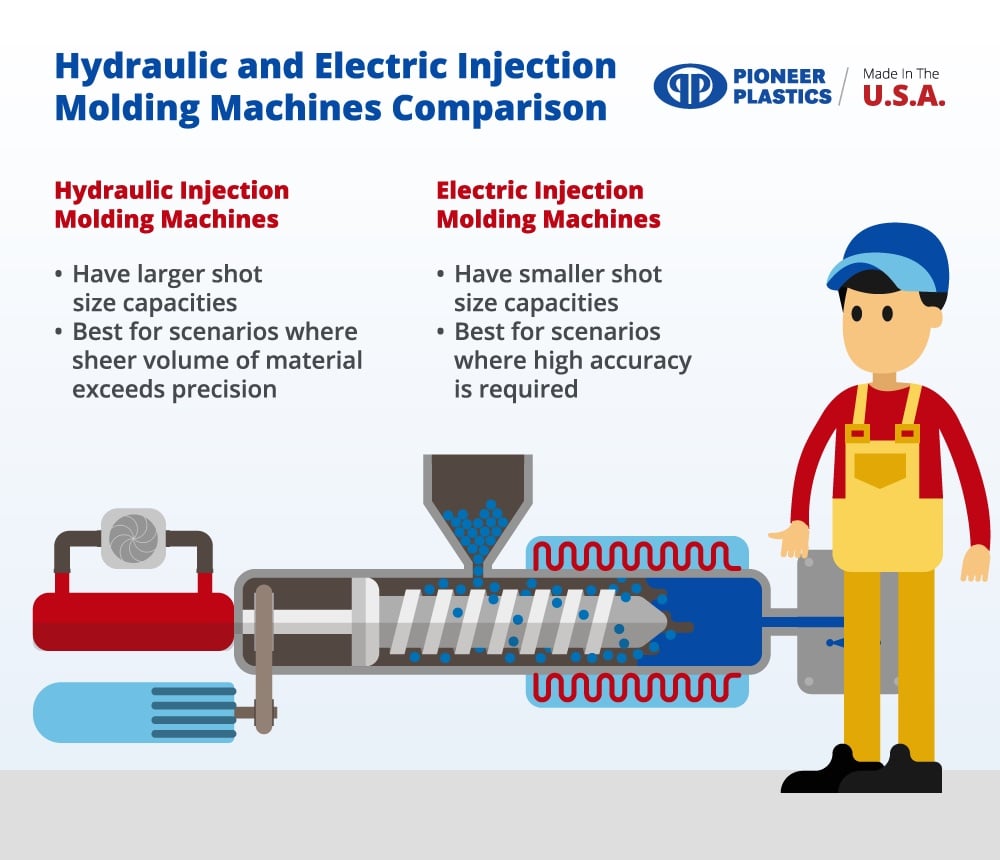
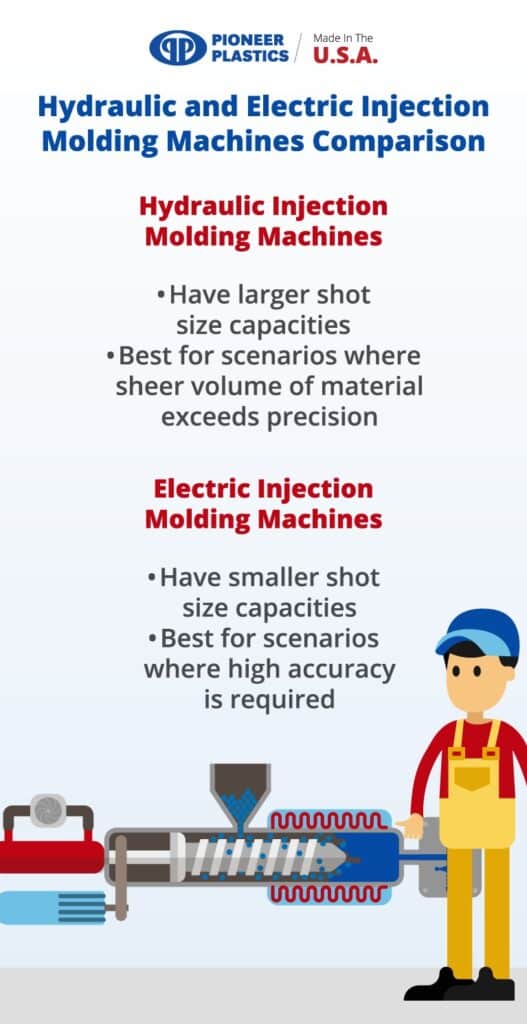
Hydraulic Injection Molding Machines
Hydraulic injection molding machines utilize hydraulic pressure to drive the clamping and injection processes. These machines are known for their ability to generate immense clamping force, making them suitable for a wide range of part sizes, including very large shot sizes.
These machines dominate in scenarios where the sheer volume of material exceeds the efficient capacity range of all-electric counterparts. Large-scale components for automotive, storage, and industrial applications often necessitate the robust power and expansive capacity that hydraulic machines are renowned for, as they are a cost-effective solution for producing these large shot size plastic parts.
Hydraulic injection molding machines rely on hydraulic pumps and valves to operate. While they can achieve high levels of precision, the inherent variability in hydraulic pressure and flow can introduce slight inconsistencies between cycles. This can be particularly noticeable when producing large volumes of parts, where even minor deviations can accumulate over time. For applications demanding utmost precision, electric machines may provide the better solution due to their superior repeatability and control over the molding process.
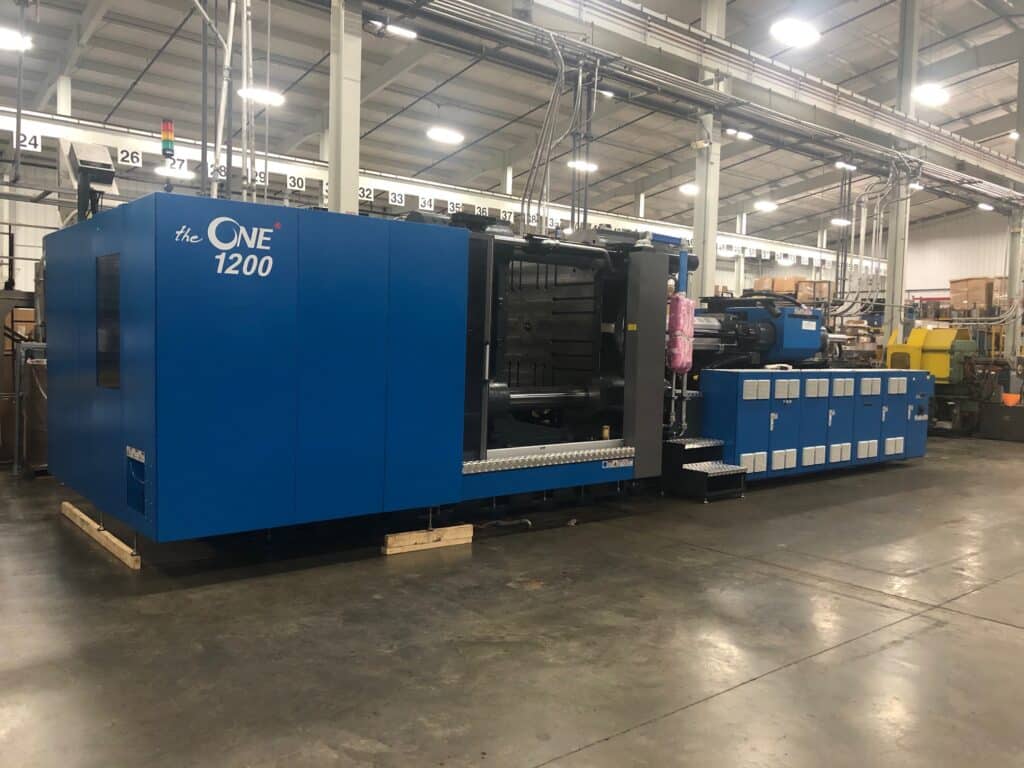
Electric Injection Molding Machines
Precision and repeatability are paramount in custom injection molding, where consistent quality and adherence to design specifications are critical.
Electric injection molding machines offer an advantage in this domain thanks to their servo drives. These machines operate using electric servo motors, which control the injection and clamping actions. These advanced drives control the injection and clamping processes with high precision, ensuring that each cycle is as uniform as the last.
This level of accuracy is essential for producing intricate parts and maintaining strict tolerances, which is often required in industries such as medical device manufacturing and aerospace.
These machines are designed to provide the exact amount of force required for the injection process without any excess energy use. Since electric machines typically have smaller shot sizes, they are ideal for precision molding of smaller parts.
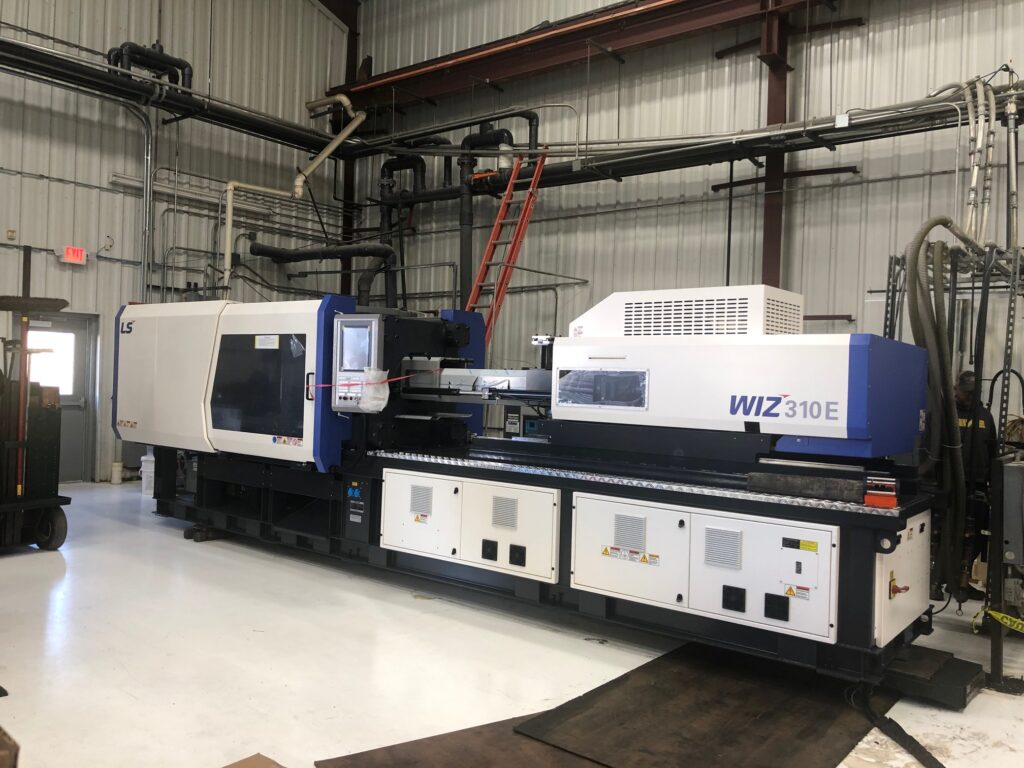
Which Machine is More Energy Efficient?
The superiority of all-electric injection molding machines in energy efficiency is notable, with these machines typically offering 20%-40% electricity savings compared to their hydraulic counterparts. This significant reduction in energy use stems from the ability of electric machines to consume power only during the actual molding process rather than maintaining the operation of hydraulic pumps constantly, even during idle periods.
Hydraulic injection molding machines, on the other hand, tend to consume more energy due to the need for oil to be continuously cycled through the system, regardless of whether active molding is taking place. This can lead to excess energy expenditure, which is not only costly but also less environmentally friendly. Retrofitting these machines with energy-saving modular valves and control systems may help reduce energy waste, but it introduces additional costs and maintenance demands, often making it a less attractive option for manufacturers looking to streamline operations and reduce overhead.
Which Machine is Best for Your Custom Molding Needs?
Selecting the ideal injection molding machine for custom projects hinges on understanding the specific requirements of the job at hand.
The decision between hydraulic and electric machines often comes down to the size of the molded part and the necessary shot capacity. While hydraulic machines excel in accommodating larger shot sizes, electric machines are preferred within their operational range for their energy savings and precision.
Factors such as the complexity of the parts, the materials used, and the desired production speed also play a crucial role. It’s essential to weigh these variables against the initial cost and potential long-term savings in energy and maintenance when choosing the right machine for custom injection molding needs.
Working with a company that specializes in custom injection molding and has the expertise to determine the most suitable method, whether hydraulic or electric, can be invaluable for businesses.
A reputable company will have an in-depth knowledge of the intricacies of the molding process, combined with access to the appropriate machinery. This leads to valuable guidance in selecting the best approach for specific custom molding needs.
This expertise can ultimately lead to optimized production processes, improved product quality, and cost-effective solutions tailored to the unique requirements of each project.
Pioneer Plastics' Commitment to Custom Injection Molding Solutions
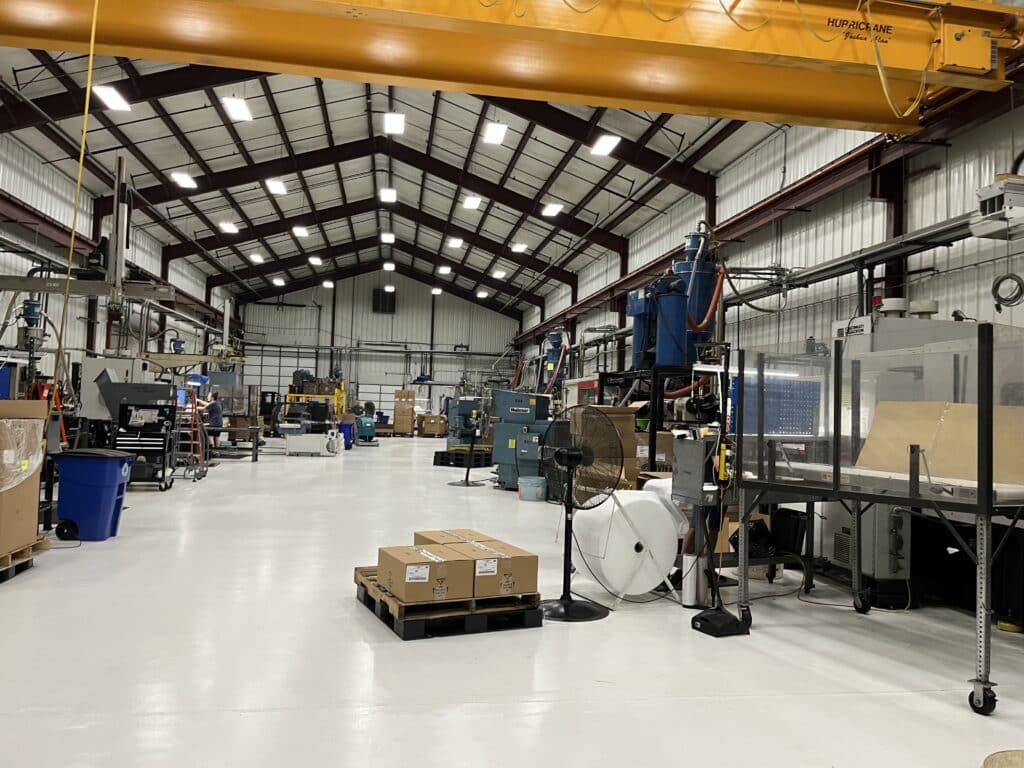
While both hydraulic and electric presses have their merits, the choice of which machine is best comes down to your specific needs and goals.
At Pioneer Plastics, we empower you with the knowledge and resources to make informed choices that align with your custom molding projects. We encourage you to get a quote today and consider joining our network of satisfied clients who have seen their visions realized through our dedicated partnership.
Pioneer Plastics demonstrates a steadfast commitment to delivering top-notch custom injection molding solutions tailored to meet the unique needs of various industries. With an array of services and custom molding machinery, including both electric and hydraulic, we are well-equipped to handle simple and complex projects. Our team’s deep expertise ensures clients receive comprehensive support throughout the entire injection molding process.
Reach out to us at Pioneer Plastics, and let’s discuss how our array of hydraulic and electric injection molding solutions can bring your project to life with precision and efficiency.