In the world of mass production, efficiency, cost-effectiveness, and quality are non-negotiable factors.
This is precisely why injection molding has emerged as a preferred choice for many businesses.
This blog post will delve into the world of injection molding, exploring its advantages and highlighting its pivotal role in the manufacturing industry.
From discussing the process’s efficiency and cost-effectiveness to its versatility and impact on the end product’s quality, we will unfold why injection molding has become a cornerstone in mass production.
Whether you are a business owner, a product manufacturer, an industrial engineer, or simply an enthusiast curious about the manufacturing industry, this comprehensive guide will illuminate the benefits and the immense potential of the injection molding process.
Understanding the Custom Injection Molding Process
Custom injection molding is a commonly used manufacturing process for the fabrication of plastic parts.
The process starts with the feeding of plastic granules into the machine’s heating barrel. The molten plastic is then injected under high pressure into the mold, which is made from a heat-resistant material and designed in the shape of the final product.
The plastic fills the mold and is left to cool, taking on the form of the mold as it does so. Once cooled and solidified, the component is ejected from the mold, completing the process. This cycle repeats continuously which is why it’s the preferred option for high-volume production.
4 Key Reasons Businesses Choose Injection Molding for Mass Production
There are several compelling reasons for businesses to choose injection molding as their preferred manufacturing process. Here are 4 Key reasons to consider:
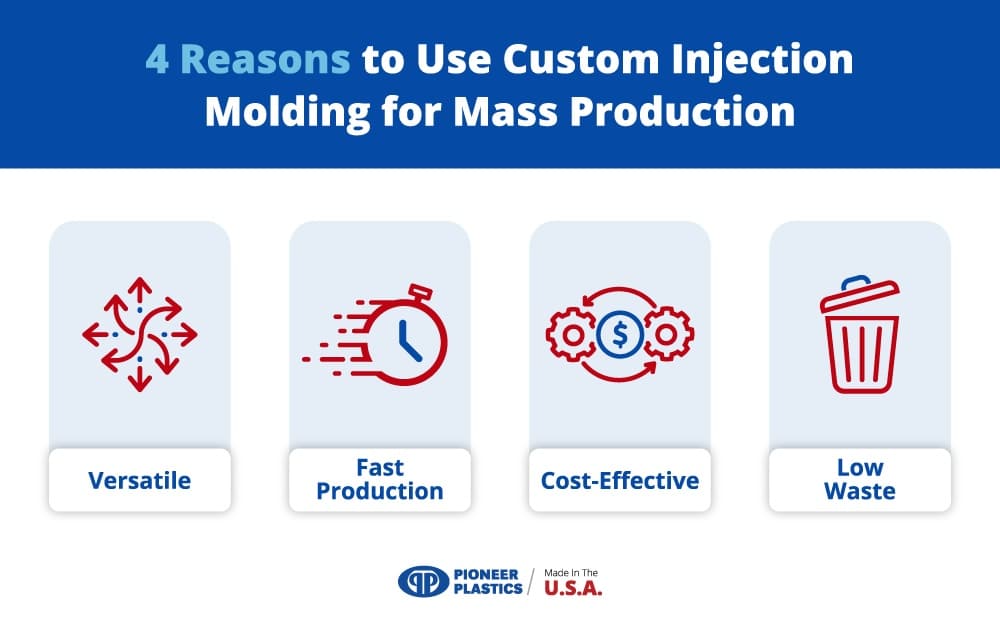
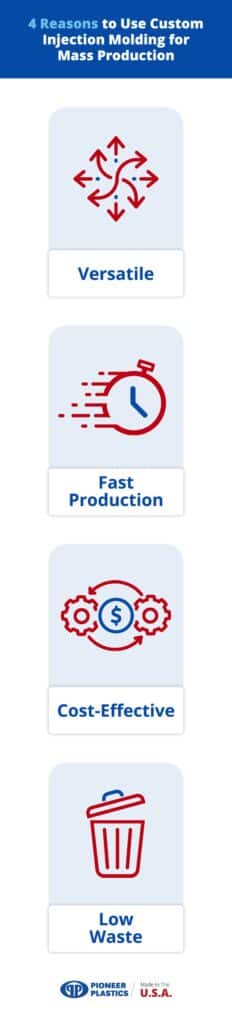
1. The Versatility of Injection Molding
Injection molding boasts significant versatility, making it a go-to solution for diverse manufacturing needs. It caters to the production needs of various industries, from agriculture to the pharmaceutical field, and even the consumer goods sector.
Moreover, injection molding isn’t limited to producing simple designs. In fact, it stands out for its capacity to produce complex and intricate designs without compromising efficiency or precision.
This feature opens up a world of opportunities for industries requiring detailed components, from appliance parts to electronics, and even intricate medical devices. This flexibility allows businesses to expand their product range and cater to diverse market demands, making it a prime choice in mass production scenarios.
2. The Efficiency of Injection Molding
Apart from being highly adaptable, injection molding also offers the advantage of reduced time-to-market for high volume production. The process is an industry champion when it comes to producing large volumes as it is designed to create thousands, even millions, of identical items in a short timeframe.
The efficiency of injection molding also owes much to automation. Machines can be programmed to perform the molding process with minimal human intervention, allowing continuous production with less downtime.
This automation not only increases production speed but also minimizes the potential for human error, leading to greater productivity and efficiency. The result is a smooth, swift production line that can cater to the high demands of mass production with ease.
3. Cost-Effectiveness of Injection Molding
Another enticing factor for businesses is the element of cost reduction. The high efficiency and automation of injection molding result in substantial savings in the long run, especially when producing mass quantities.
Since automated machines can manage most of the work, you’ll also see a reduction in manual labor costs. These machines operate with precision and consistency, further enhancing productivity and cost efficiency.
The high-volume production nature of injection molding is another main contributor to its cost-effectiveness. When producing large quantities of an item, the initial setup and tooling costs are spread across a greater number of units. This leads to a lower cost per unit, making injection molding an economically viable option for businesses looking to mass produce a product without compromising on quality.
4. The Low Waste from Injection Molding
The low waste production of injection molding not only benefits the environment but also helps businesses reduce material costs and optimize their production processes. It aligns with the increasing focus on sustainability and waste reduction in today’s manufacturing industry, making it an environmentally friendly choice.
The process begins with the injection of molten plastic into the mold, ensuring that the material is distributed evenly and fills all the necessary cavities. This eliminates the need for excess material that would otherwise be trimmed, cut, or discarded in other manufacturing methods.
This efficient use of materials in a precise and controlled nature, not only reduces waste but also cuts down on the overall cost of production.
Additionally, injection molding allows for the efficient use of recycled or regrind materials. These materials can be mixed with new plastic pellets, reducing the overall amount of virgin plastic used in production.
By choosing injection molding for mass production, businesses can minimize waste and maximize the utilization of materials, leading to a more efficient and environmentally friendly manufacturing process that ultimately leads to cost savings for the business.
Custom Injection Molding—Your Solution for Quality AND Quantity
The precision and accuracy of the process, combined with the ability to reproduce complex designs with a high level of detail, result in superior product quality.
The injection molding process offers high precision and accuracy in the manufacture of products. This is due to the pressure exerted when injecting the molten material into the mold, which ensures all areas are filled and the product shape is accurately formed.
As a result, injection molding can accurately reproduce complex designs with a high level of detail. The process also allows for in-mold decoration or labeling, contributing to the high-quality finish of the end products.
Once the mold is designed and set up correctly, each part that comes out of it will have identical dimensions. This makes injection molding THE choice for mass production where uniformity of all products is crucial.
Pioneer Plastics—A Trusted Partner for Custom Injection Molding
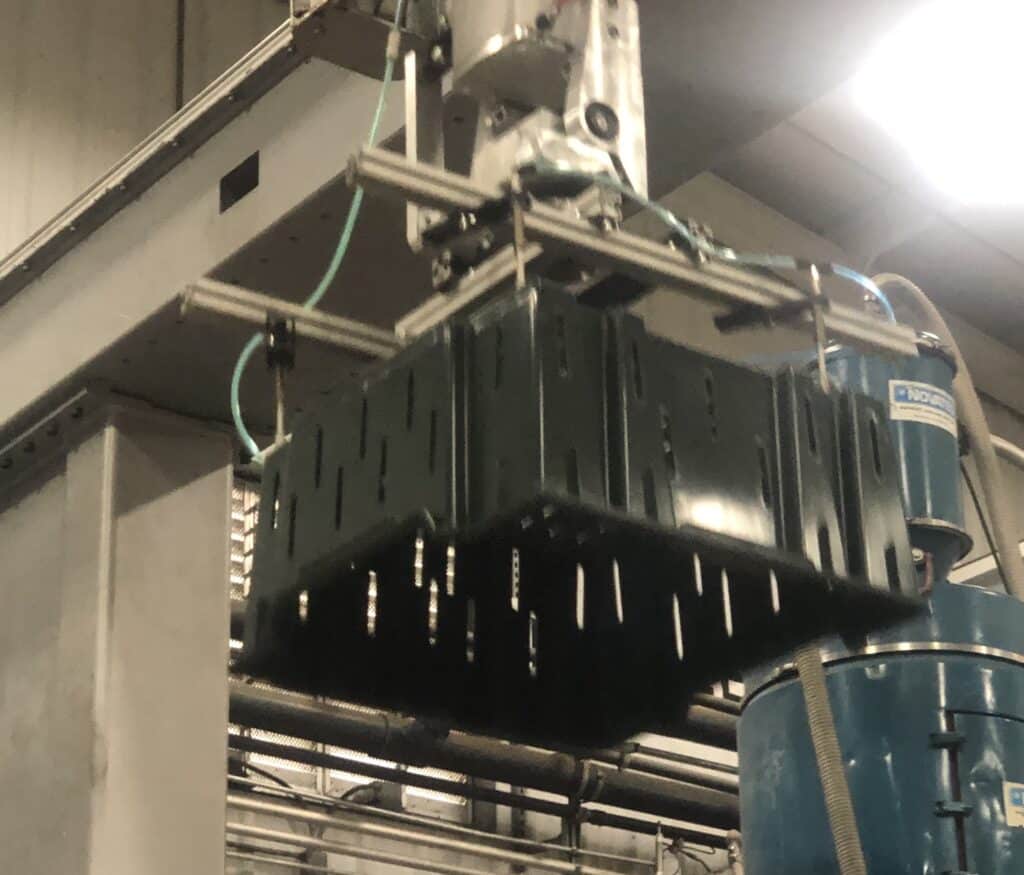
As we’ve explored, injection molding is an unmatched solution for mass production thanks to its efficiency, cost-effectiveness, versatility, and the high quality of the end product.
The high-volume production nature of injection molding can lead to lower per-unit costs, allowing your business to offer competitive pricing which leads to higher profit margins.
The high precision and accuracy of this process enable businesses to deliver superior products that meet and exceed customer expectations.
If you’re considering incorporating injection molding into your manufacturing process or require top-notch, custom plastic parts, Pioneer Plastics is equipped and ready to assist.
Remember, the key to successful production lies in finding the right partner. With over 35 years of experience in custom injection molding and a comprehensive list of services, Pioneer Plastics can help you take the guesswork out of mass production.
Reach out to Pioneer Plastics today and let’s explore how we can elevate your production process together.