First patented by John and Isaiah Wyatt in 1872, the first plastic injection molding products were combs, buttons, and collar stays, and the machine that built them consisted of little more than a hypodermic needle injecting molten resin into a die. The technology has come a long way since then.
Now capable of fabricating a wide array of products with many different properties and designs, plastic injection molding is one of the most common ways that manufacturers build their parts. This cost-effective, high-volume process is an excellent way to build products according to the exact specifications that their industry requires, and it offers several advantages over metal fabrication. We’ll take a look at the benefits of injection molding over other materials, and which industries depend on it the most.
The Advantages of Plastic Injection Molding Products
Although the process first took the manufacturing stage during World War II as an inexpensive alternative to metal fabrication, plastic injection molding has since proven that it offers several advantages over other processes. Metals were once used for most products, but when plastics became commonplace as a substitute, manufacturers and consumers both began to prefer the material properties they possess. Here’s a look at a few of the properties that set plastic apart.
- Cost – Arguably the greatest advantage of plastics over metals is that they are a fraction of the cost. Although their prices vary, metals are considerably more expensive than plastics — and the products made from them will cost more as well.
- Versatility – While a wide number of options exist for metal injection molding (MIM), there are over 20,000 unique formulations of plastic resins that designers can choose from to build their parts. With so much flexibility, manufacturers may be more likely to find the material properties they need if they choose plastic over metal.
- Durability – Whether it’s corrosion resistance in the oil and gas industries or electrical and thermal insulation to protect valuable electronics, plastics can withstand environmental conditions that metals can’t. Remaining intact when metals may fail, plastics are built to last.
- Flexibility – Some applications like the food packaging industry require a flexible part. Harmful shavings may result if metal products break or bend, so plastics are often safer.
- Colors – Some products must be color-coded for safety reasons, and others require elaborate color schemes to market the brand. Plastic pellets come in a wide variety of colors, and can even be clear to showcase the product inside.
- Surface Finish – Many metal products must be machined to achieve the final surface finish after they’re built, but injection molding plastics come out smoother, and require less machining, if any. This also reduces the total cost of production — and they can still be machined if a different surface finish is needed.
Common to both metals and plastics, injection molding enables manufacturers to fabricate a large number of parts at once. It also can be used to build highly intricate parts, making it ideal for smaller products.
Which Industries Use Injection Molded Products the Most?
Cost-effective, scalable, and efficient, the many advantages of plastic injection molding have made it a staple in the manufacturing world — but which industries use it the most?
1. Food, Beverage, and Agriculture
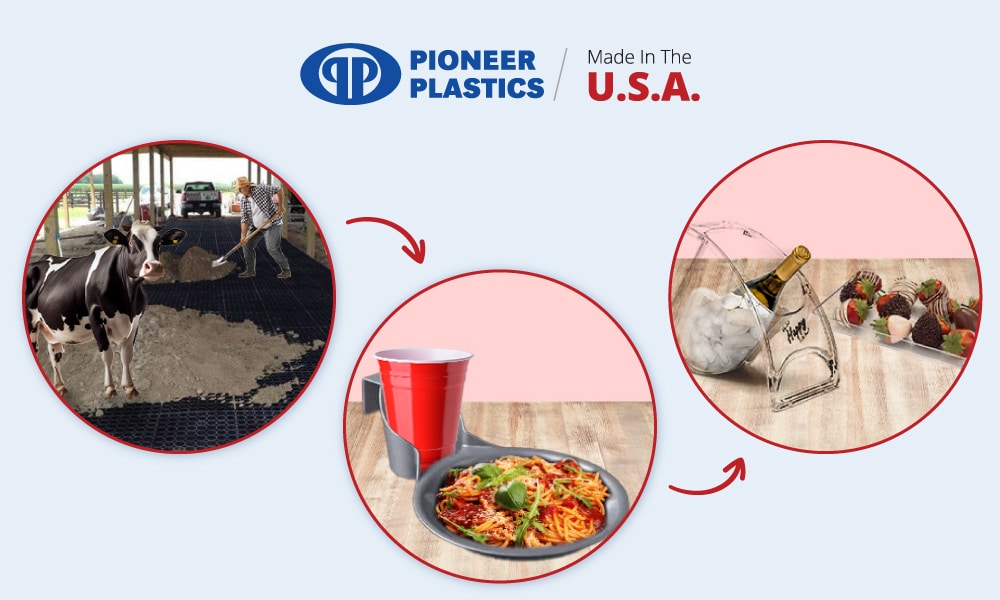
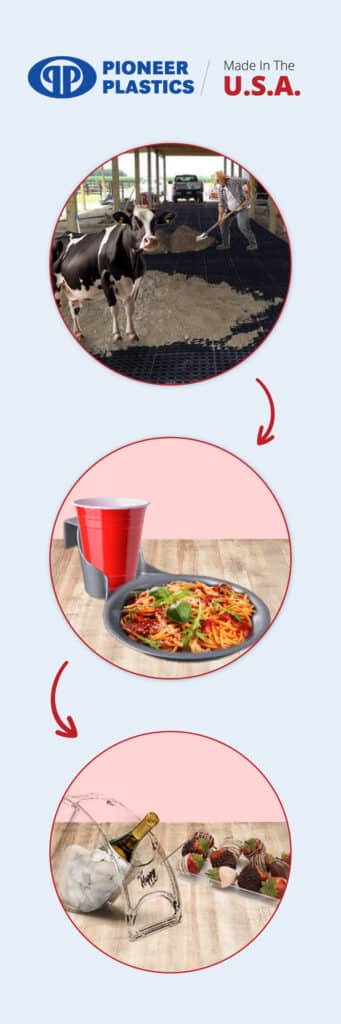
From agriculture and farms to restaurants and food preparation facilities, the food and beverage industry depends heavily on injection molded plastic parts. This industry is heavily regulated to protect our health, so stringent quality metrics must be followed — which is part of why plastic injection molded products are so often used. Their resistance to the elements makes injection molding products ideal for agricultural tools like feeding troughs and stable ground grids. Their lightweight durability makes them a suitable choice for tractor components, cooking utensils, or brewing machinery.
Manufacturers in the food, beverage, or agricultural industries must also see to it that their products that come into contact with food are food-grade safe. Otherwise, they may risk violating important safety standards. At Pioneer Plastics, we are ISO 9001:2015 certified and all of our products are BPA-free. That means that companies working with Pioneer Plastics will know their food-grade products are safe.
2. Food Packaging
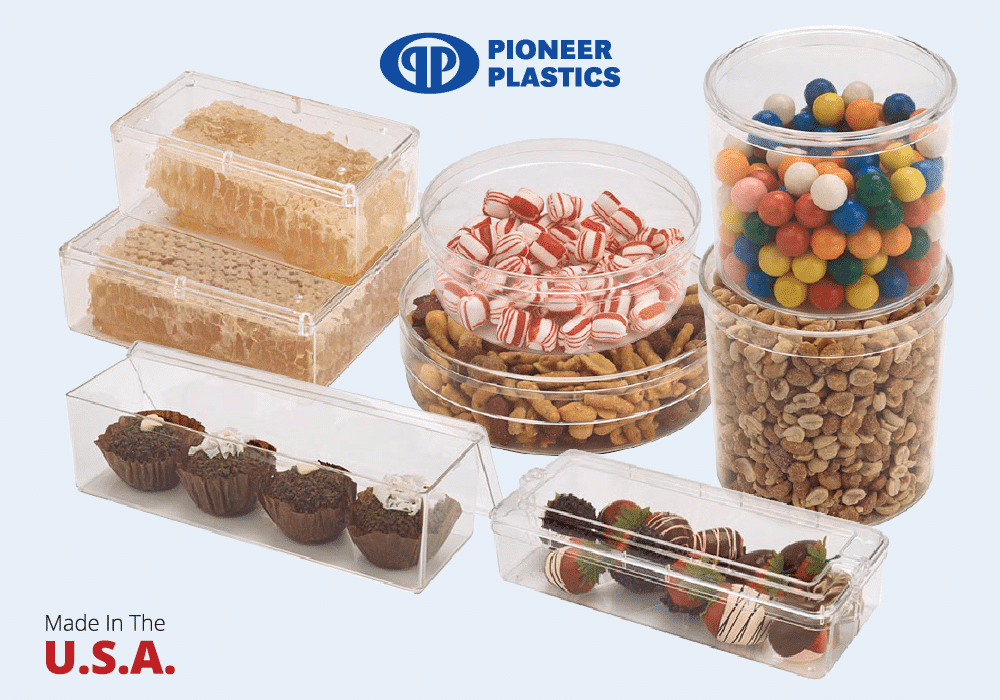
The food industry’s reliance on injection molded plastic parts doesn’t stop with agriculture. The food packaging industry makes heavy use of these parts too, and versatility is often a must. One size rarely fits all in this industry, so custom molds are often needed to aid in food preparation and storage. However, because food packaging products are also often made in large quantities, manufacturers must find a solution that is both customizable and high-volume. Injection molding plastics do both.
For example, companies that sell clear plastic boxes or trays for products like candy, nuts, or honey will require large orders that often need to be custom made. They may also need their packaging to possess specific material properties like temperature resistance to preserve the treats inside.
At Pioneer Plastics, we offer a wide variety of standard and custom packaging solutions, and can produce packages with properties that will help protect the foods they hold. Those that only require standard containers may find our round, square, or candy tray options to be the perfect choice, while those in need of a more intricate design can make use of our custom injection molding services to design the packaging they need. We have even worked with industry-leading restaurants to design innovative custom plastic molding solutions that promote safer food delivery — and received awards for our results.
3. Home and Appliance
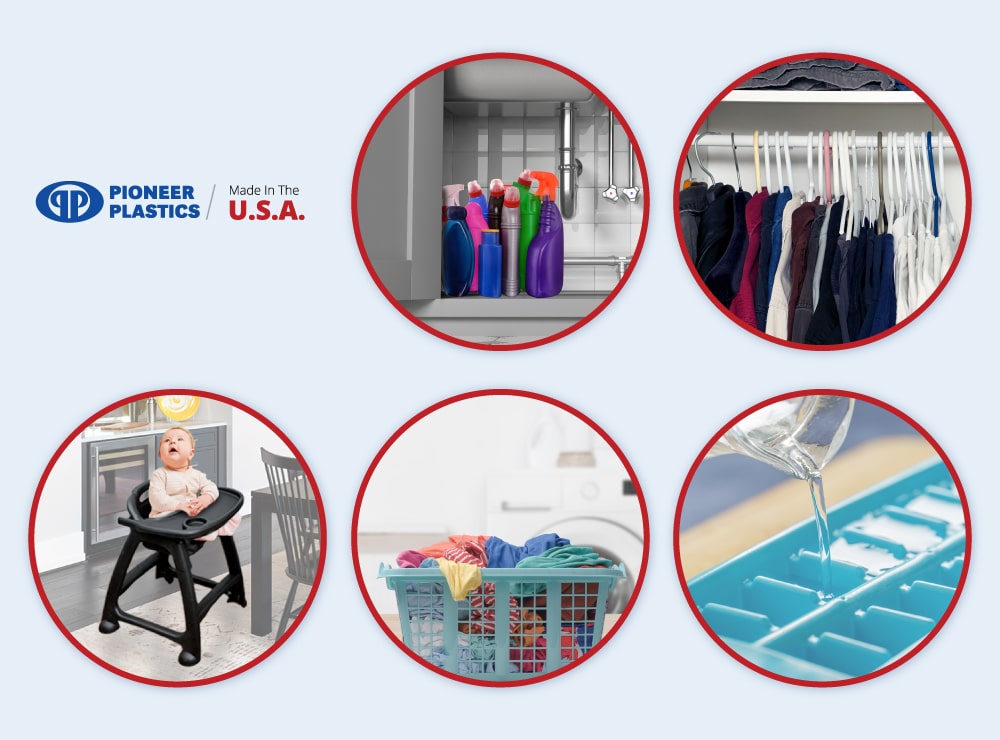
Plastic injection molding parts are everywhere in your home. From appliances to lawn and garden tools and supplies, or even tools in your garage, injection molded plastic parts are found in many places that homeowners may not expect. A few common injection molding products that you’ll find around the house are:
- Cleaning products
- Cosmetics and toiletries
- Drawers, handles, and shelves
- High chairs, playpens, and toys
- Racks, cabinets, and hangers
- Containers, vessels, and jars
- Light fixtures and decorations
- Gardening tools and landscaping supplies
- Tool components
As versatile as their applications are, something all of these products have in common is their need for rapid mass production — a key factor in why plastic injection molding is the chosen means of production. Injection molding may not be the most cost-effective route for product orders of 100 or less, but when large volumes of products must be built in a short period of time, it’s often the best process to choose.
At Pioneer Plastics, we have both the equipment and expertise to fill large orders and shorten your product’s journey from concept to reality. The extensive experience of our plastic designers and engineers enables us to provide design for manufacturability (DFM) feedback, and our rapid prototyping services help you work through multiple design iterations until the final model is flawless. Our facilities are also large enough to handle many high-volume orders, so you can build enough parts. That way, the design will be perfect on the first production run.
4. Arts and Crafts
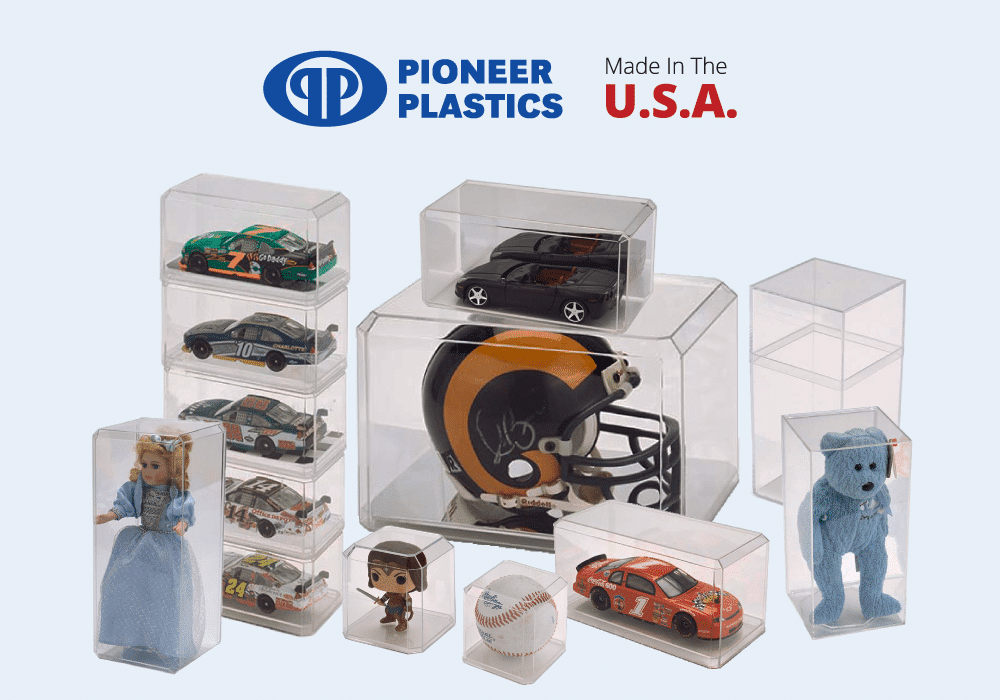
The flexibility, transparency, and protection that plastic injection molding products offer also makes them ideal for industries involving arts and crafts. Some applications include:
- Display cases
- Toys and antiques
- Trophy stands
- Clear containers
- Collectible items
- Memorabilia storage
- Decorative coverings
Many collectibles, arts, and crafts are put on display, but careful thought must be given to the conditions in which they are stored. For example, sports cards, autographed items, or antiques with original paint must be well-lit to show them off, but must be protected from UV rays that would damage their pigments or appearance. Injection molded plastic parts are perfect for protecting such collectibles. The transparency that many plastic resins provide gives observers a clear view of these valuable products, while the UV-protectant can guard them from light damage. Visibility and protection are essential for any display, and injection molded plastics offer both.
Pioneer Plastics: Paving the Way in Injection Molding Products
There are many other industries that make use of plastic injection molding — automotive, medical and pharmaceutical, and aerospace, to name a few — and with so many advantages, it’s easy to see why. Plastic injection molding is cost-effective, fast, FDA and ISO compliant. The result is an efficient, high-volume product that adheres to the highest industry standards, and that can stand up to the wear and tear of the harshest environments.
At Pioneer Plastics, our team of plastics experts has over 40 years of industry experience, and we continue to stay on the cutting edge of our field. Before we ever create the mold for your plastic injection molding project, we build a prototype with our 3D printer, so that you can identify areas for improvement beforehand — and that’s just one way that we optimize our processes to give you the best experience possible. We strive to create short lead times for new custom plastic component products and replacement parts with rapid prototyping, expert product design guidance, and having the design done correctly the first time. Contact us to see what our custom injection molding and custom plastic parts services can do for your build. Bring your design to life today!