Custom injection molding is one of the most versatile processes for creating a custom plastic part. There are many benefits to the process of custom injection molding.
Strength & Stability
The custom injection molding process offers numerous ways to ensure parts are strong and durable. Wall thickness, ribs (for support), and plastic material selection are just a few options.
Thicker walls are more expensive due to longer cycle times and more material but can provide a very durable part.
Ribs in key areas can give extra durability where needed and not have the cost issues of thicker walls.
Parts made from engineering-grade resins are able to withstand extreme temperatures, friction, and corrosion. This makes them more durable than commodity grade resins, which are typically used in consumer products like packaging.
Environmentally Friendliness
Parts that are created using plastic molding tend to last longer due to their quality and strength which reduces the number of parts that get thrown away over time.
The molding process doesn’t waste materials. When a broken or unusable part is produced, it can be remelted and reused.
Complex Capabilities
A variety of sizes, colors, shapes, and finishes can be created through custom injection molding.
Techniques like insert molding are used to inject resin over another material. An example of this is threaded fasteners that have metal in the center and a plastic shell. Plastic overmolding is most commonly used to enhance the appearance or function of a molded part, like adding a softer layer of resin to the handle of a part.
It can be used for assembly and decoration, as well. If pieces need to be labeled or decorated, in-mold labeling may be used. Connectivity techniques like heat staking and ultrasonic welding can be used to join two or more parts together.
Cost-Effectiveness
It is important to pick a partner that handles the entire process – from design to actual injection molding. This is much more cost-effective because the process is handled by one manufacturer from design to distribution.
Custom injection molding can handle large scale manufacturing without compromising quality or adding costs to the manufacturing process. If you’ll be producing a large volume of your part in every run, plastic custom injection molding will be a cost-effective option.
Flexibility in Design
All of the needs mentioned above can be solved with a good design. Pioneer Plastics has over 20 years of injection molding engineering experience in our design team – we know what makes a good part based on what your needs are.
Before the injection molding is created, we can create a prototype of the part using our 3D-printer. This allows you to experiment with the product and make any necessary adjustments before the mold is built.
Pioneer Plastics is a turnkey injection molding company and produces everything in the United States – no international trade/shipping concerns. We are equipped to take your part from concept to consumer. Contact us today to get started on your custom injection molding.
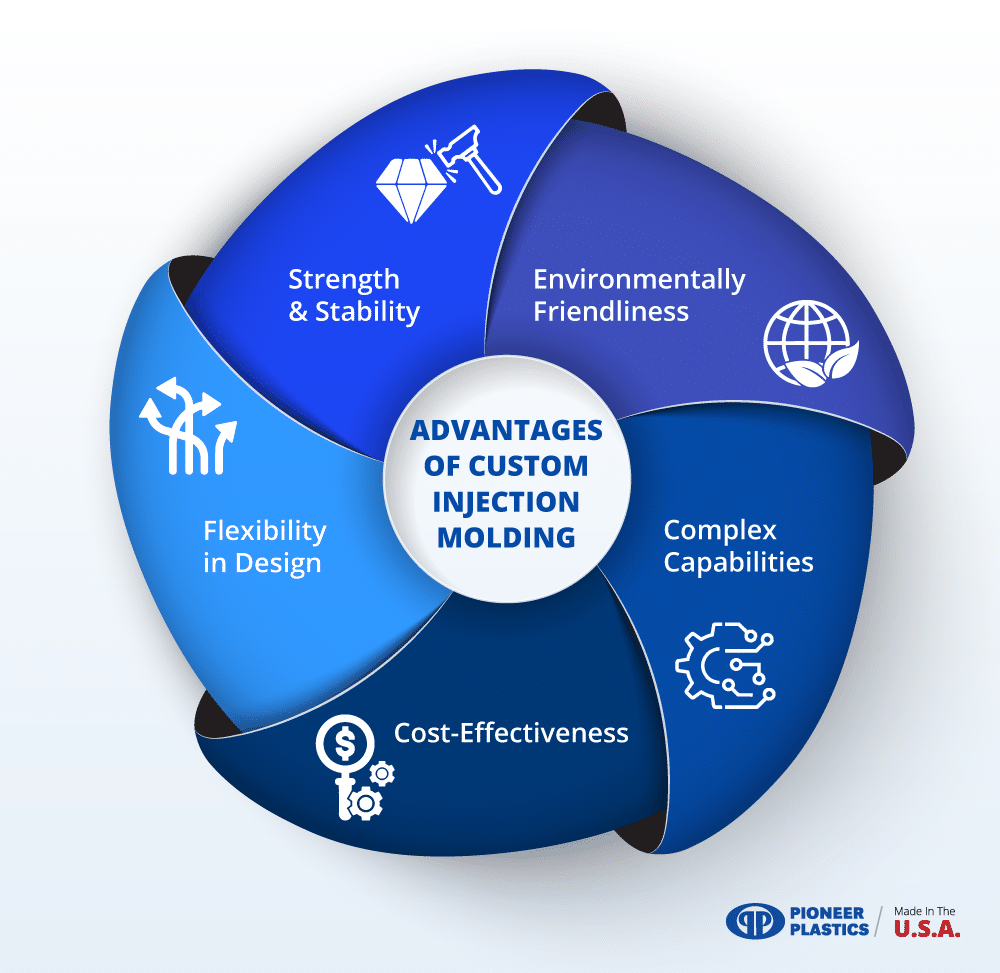
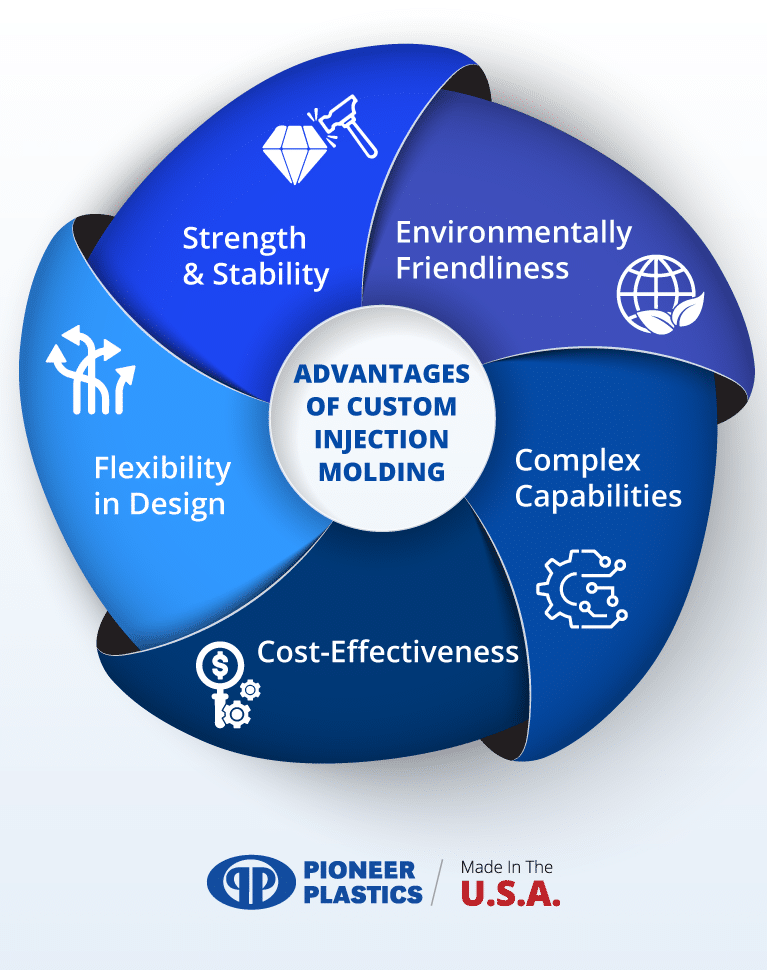