The modern manufacturing world is full of options for businesses like yours to create products and components. It can be overwhelming if you don’t understand how different solutions work. If you need a lot of products and you need them fast, you don’t have time to waste deciphering manufacturing processes. You need a quick and effective crash course. Here’s everything you need to know about injection molding, from its history to how it works to its most common uses today.
The History of Injection Molding
Injection molding has been around for almost as long as plastic. John W. Hyatt, one of the first to patent a celluloid production method, was also the first to inject celluloid into a mold. In 1872, Hyatt and his brother Isaiah patented a machine that injected celluloid plastic into a mold through a heated cylinder. Much like today, this process was used to create buttons and hair combs quickly and easily.
The original injection molding machine was slowly refined over the next 70 years as plastics improved. A major step towards modern injection molding was the invention of Bakelite by Leo Hendrik Baekeland in 1912. Bakelite was the first entirely synthetic plastic. Unlike celluloid, which was derived from plant cellulose, Bakelite was made from wholly artificial materials. It was smoother and more uniform than cellulose, which made it easier to produce consistent injection-molded products.
The next revolution came about during World War II. Scientists were working to improve the injection molding process to meet the needs of consumers and the government. In 1946, James Hendry made a major breakthrough when he built the first screw injection molding machine. This allowed manufacturers to do things like add new colors, mix before injection, and generally create more exciting and robust objects.
Hendry also produced the first gas-assisted injection molding process. That made it possible to create long, hollow objects like never before. Today, the vast majority of injection molding manufacturers still use screws and gas assistance in their injection machines.
How Injection Molding Works
The injection molding process is a marvel of engineering, one of those rare solutions that’s both intuitive and uniquely complex. The fundamental process of injection molding is simple: plastic is heated up until it melts. The liquid plastic is then pushed or poured (injected) into a mold in the shape of the final object. The plastic is allowed to cool and harden, then it’s removed from the mold.
Some types of injection molding can be slightly more complex. Screw injection molds use a heated barrel with a fitted screw to push the plastic into the mold. The machine feeds plastic pellets from a hopper into the heated barrel, and the screw spins to move these pellets forward into the mold as they melt.
Gas-assisted molding also involves extra steps. It creates hollow objects that can’t be quickly produced with a traditional mold. The plastic is injected as usual, but a small tube blows in an inert gas alongside it. This gas essentially blows a bubble in the liquid plastic, pressing it against the edges of the mold but leaving the interior hollow. The pressure of the gas is maintained until the plastic hardens. Then it’s released to create an object with a hollow interior and no seams.
Types and Kinds of Injection Molding
It’s possible to use many different types of plastic in the injection process. Various plastics have unique properties that can stand up to a variety of environments and use cases. The majority of plastics used in the industry are known as amorphous plastics.
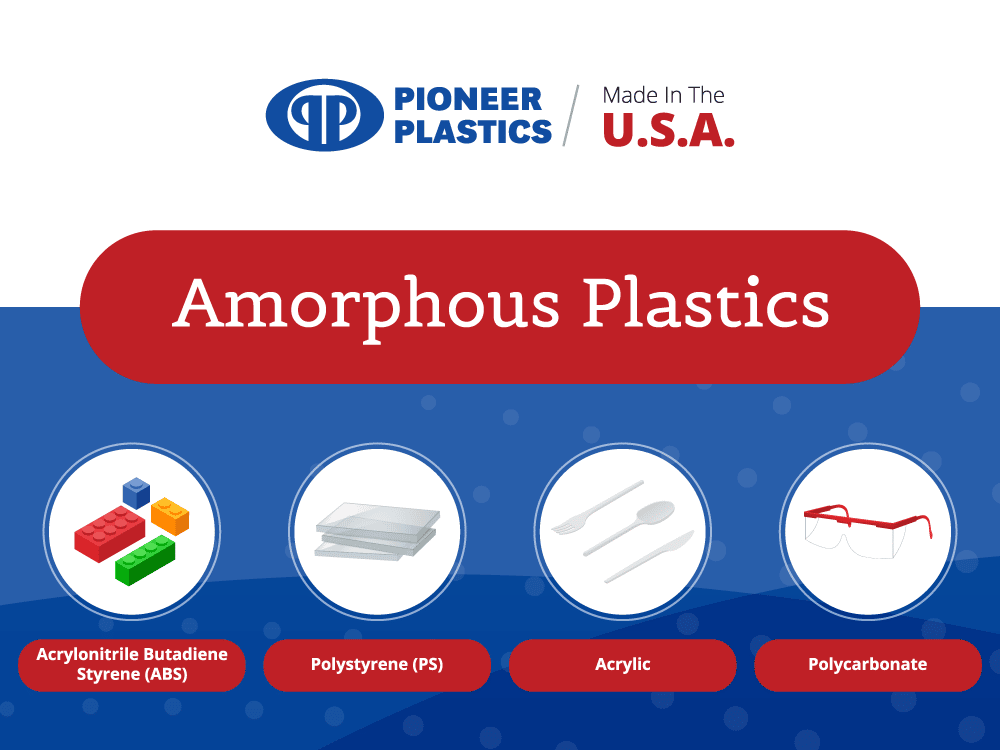
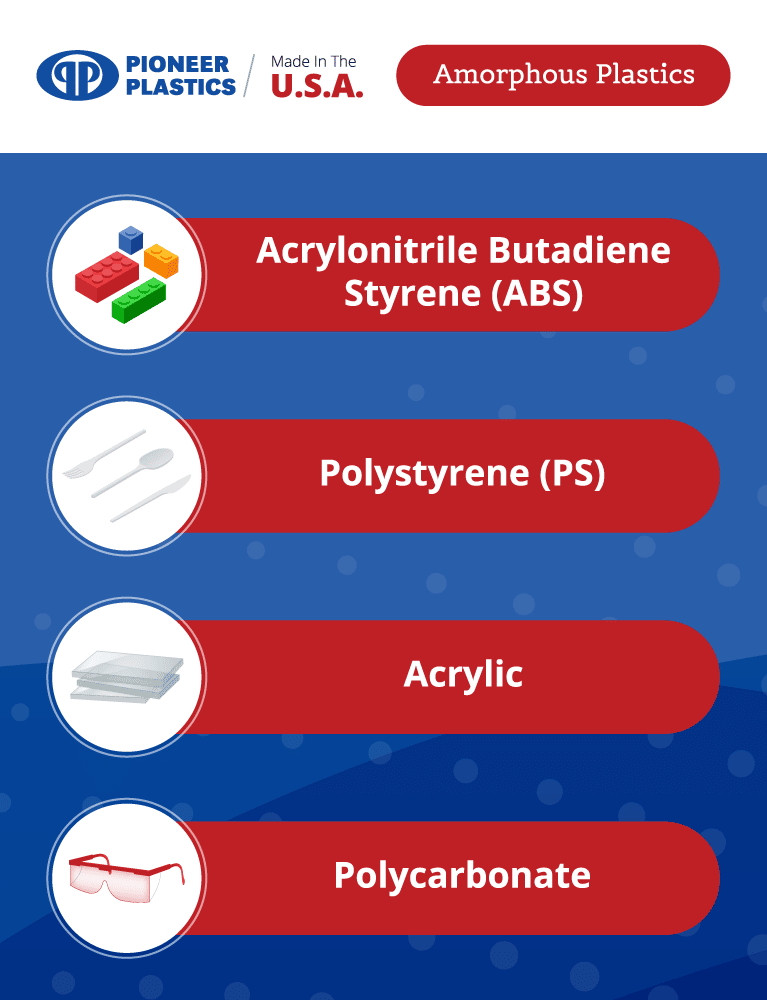
These include:
- Acrylonitrile Butadiene Styrene (ABS): Impact-resistant and rigid, used in Legos and some cars.
- Polystyrene (PS): Rigid and economical, used in plastic cutlery and CD cases.
- Acrylic: Transparent and shatter-resistant, used to replace glass in windows.
- Polycarbonate: Heat-resistant and durable, used in eyewear and car exteriors.
The molds used in injection molding are just as important as the plastic. There are two major types of molds: two-plate and three-plate molds.
Two-plate molds are the more straightforward variety. The mold consists of two halves, one of which has the injector. The plates come together to form the complete mold and then pull apart to eject the object. They’re excellent for low-complexity parts and items that must be durable, but they can lack precision.
Three-plate molds include a third plate sandwiched between the two used in a two-plate mold. This additional plate allows the machine to create delicate components by adjusting the location where plastic is injected. They’re great for high-complexity parts, but that extra complexity can lead to lower durability.
How Injection Molding Is Used
Plastic injection molding is used in just about every industry that uses plastic in any way. It’s one of the backbones of modern manufacturing. Here’s how injection molding is used in some of the biggest industries in the world.
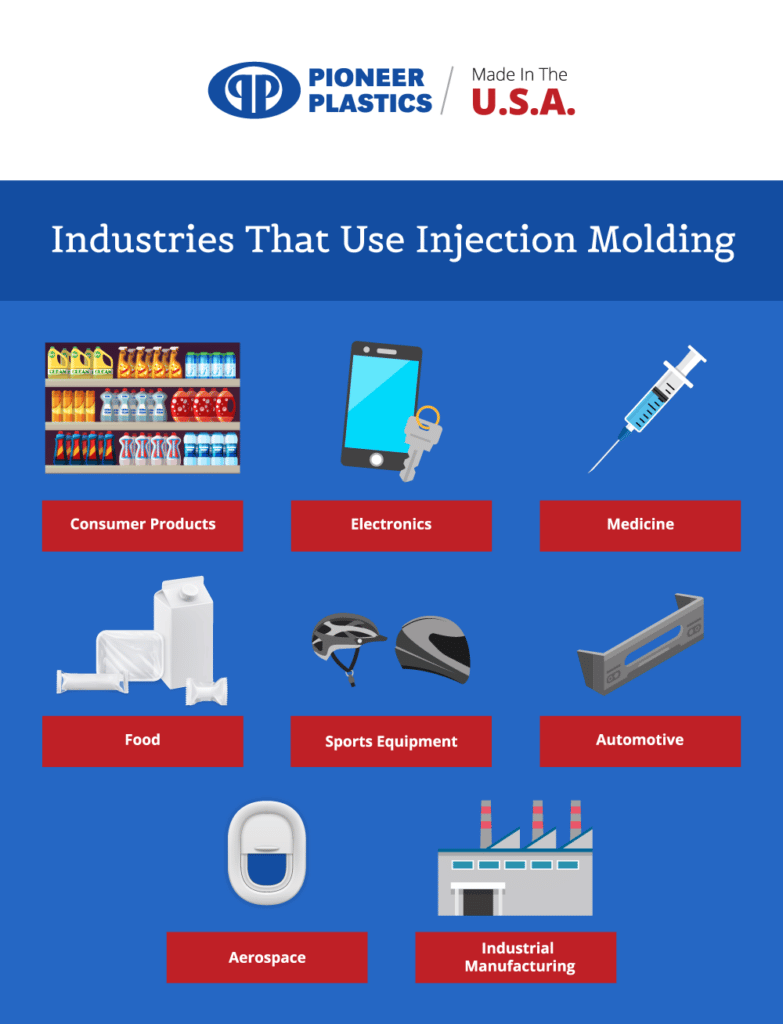
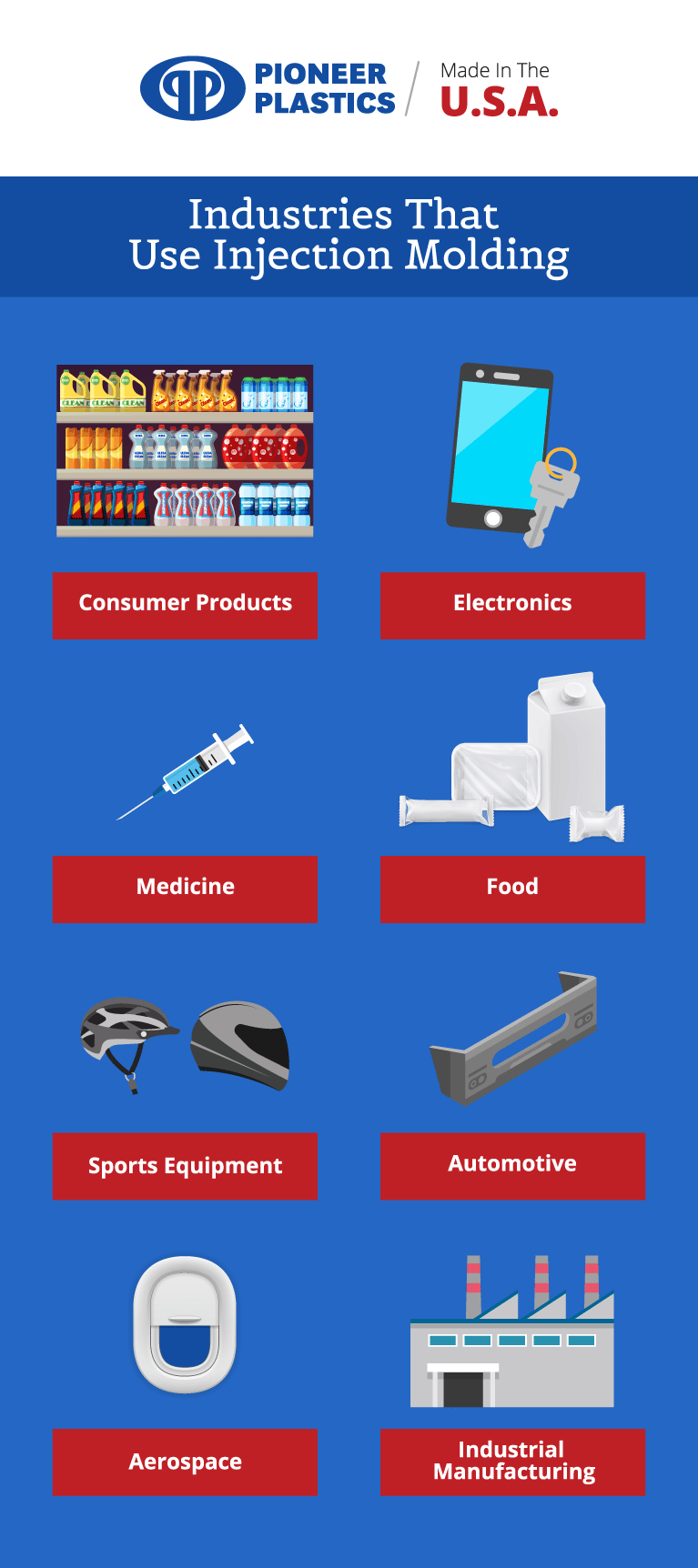
Consumer Products
Today one of the most common uses for injection molding remains in consumer products. Injection molding is a cost-effective way to produce durable objects people can use in their homes. It’s used to make everything from collectors’ boxes to appliance parts to packaging items. In fact, plastic injection molding is one of the reasons why there are so many convenient, affordable products on the market today.
Electronics
Plastic plays a vital role in electronics. It’s a lightweight material that doesn’t conduct electricity. Many electronic devices need to be portable. They also need to keep users safe by avoiding shorts and other electrical problems. These devices come in such a variety of shapes and sizes that companies need to have the ability to quickly produce unique housings.
The easiest way to accomplish this is through custom injection molding. A mold can be created to fit any collection of circuits and wires in the shape that makes sense for the product. It can be designed to include specific ports, button cut-outs, screens, and anything else the device may need. That’s why injection molding is used to produce everything from car key remotes to phones.
Medicine
The medical world requires materials that offer precision and safety in equal measure. It also needs tools and components that are cost-effective to allow as many people as possible to receive treatment. Historically, metal and glass were common in medical facilities, but today’s medical professionals need more flexibility from their daily tools.
Injection molding meets that need. Plastic injection molding can turn out medical-grade parts at significantly less expense than metal equivalents. Certain modern plastics can stand up to the heat of autoclaves, which allows them to be safely used in sterile environments. These plastics can be injection molded into everything from surgical tools to components in devices like x-ray and MRI machines.
Injection molding is also vital to life sciences applications. Custom injection molding can help create prostheses, hearing aids, and other life-altering and life-saving devices that patients will use daily. The objects can be produced with a mold that’s specifically based on the patient’s body. The result is a uniquely close fit, making these aids as comfortable as possible.
Food
Food service, food storage, and food sellers all require non-reactive tools, containers, and parts to meet FDA hygiene and safety requirements. Furthermore, with the demand for disposable, portable food options, all food and beverage providers need to prioritize affordable single-use containers.
The many food-grade plastics available make plastic injection molding an excellent solution for these businesses. Any plastic considered food-grade is non-toxic and non-reactive, so it can safely store things people will put in their bodies. In combination with the flexibility of injection molding, these plastics can be used to create everything from take-out containers to food processing equipment to water bottles.
Sports Equipment
Sports involve pushing the human body to extremes. It’s vital that the equipment athletes use makes this safe. Sporting goods and athletic gear need to protect the user while remaining precisely within the sport’s regulations in question.
Injection molding is a great way to accomplish that. High-durability injection-molded plastic makes an excellent exterior for a football or bike helmet. It can also act as secure binding clips on snowboarding boots, grips on ski poles, and even the housing and pedals of an elliptical machine.
Automotive
As the automotive industry prioritizes fuel efficiency, it’s become essential to reduce weight in many parts of different vehicles. Anything that’s not required to be made of metal for structural or regulatory reasons is quickly being replaced with safer, durable plastic alternatives.
In the typical vehicle, many components are produced with injection molding techniques. Everything from tiny elements like individual lock buttons all the way to significant parts like the entire dashboard, bumpers, or even exterior door panels may be made with this technique. It offers precision, affordability, and quick production, making it the perfect solution for vehicle manufacturers producing millions of cars annually.
Aerospace
The aerospace industry, and the defense industry beyond it, uses injection molding in many different ways. Injection molding is the most precise way to produce lightweight, aerodynamic objects that fit the specific tolerances needed to keep planes in the air. Specific plastics are injection-molded to create objects like turbine blades, engine housings, windows, and pin maps.
Industrial Manufacturing
Injection molding products aren’t just the end of the process. Many manufacturers use injection-molded parts as steps to get finished products. An injection-molded pin map, for example, is used to shape carbon or glass fibers into the proper form for aerospace uses. Injection molding can also create components for industrial machines such as rollers, switches, and housings.
Pros and Cons of Injection Molding
Injection molding is a versatile, helpful method of producing plastic objects. It offers some significant benefits to companies seeking to create plastic things, that:
- Are affordable: Once a mold is built, injection molding is one of the most cost-effective methods of producing identical plastic objects. The cost is simply the operation of the machine and the plastic used within it.
- Have tight tolerance: Every single item that comes from a mold will be exactly the same. If you have precise tolerances you need to follow, as with electronics or automotive components, injection-molded objects will meet those requirements with far fewer defects.
- Require high volume: Molding a product is significantly faster than building or machining it in another manner. It’s as quick as injecting the plastic and waiting for it to solidify.
- Require flexible production: Injection molding works with a variety of plastics. You have the freedom to choose the perfect plastic and the right colors for your component without the need for expensive post-production changes.
No manufacturing technique is perfect for every situation, of course. There aren’t many drawbacks to injection molding, but they include:
- Cost of mold production: The up-front cost of injection molding is higher than some alternatives. This is because the mold itself needs to be built to fit your needs. However, if you’re producing a significant number of objects, this cost quickly pays for itself.
- Effort of changes: If you want to change anything about your product other than the color or material, you will need to create a new mold. This can take time and effort, just like the production of the original. Injection molding is best for products that do not change significantly until many have already been made.
If you need just a few of a product, or if you need your component to be made out of metal or another non-plastic material, then injection molding may not be for you. But if you need custom parts in large amounts, it’s a great idea to consider injection molding products
Start Your Injection Molding Journey Today
If you’re ready to make injection molding part of your business, you can start today. Pioneer Plastics can support you every step of the way with US-based production, in-house tooling and design experts, and convenient delivery options. Learn how Pioneer Plastics’ end-to-end custom injection molding services can help you create all the plastic parts and products you need.