Understanding the nuances of custom injection molding can be a daunting task, especially when it comes to deciding between single-cavity, multi-cavity, and family molds.
This blog post aims to demystify these concepts, providing a comprehensive insight into their applications, advantages, and disadvantages.
By tapping into the expertise of Pioneer Plastics, a trusted name in the injection molding industry, we’ll help you navigate your manufacturing needs with confidence and precision.
Whether you’re a business in the food industry, the collectibles market, a household item manufacturer, or simply exploring your options in injection molding, this guide is tailored to empower you with the knowledge and guidance required for making an informed decision.
Understanding Injection Mold Cavities
Injection mold cavities play a pivotal role in the process of injection molding. They are the hollow spaces within the mold that give shape to the injected plastic, creating the final product.
So what are the main differences between single-cavity, multi-cavity, and family molds? The primary difference lies in the number and variety of parts they can produce in a single cycle. Single-cavity molds create one component at a time, multi-cavity molds produce multiple identical parts, and family molds manufacture different parts of a product simultaneously.
The choice of cavity type significantly impacts the efficiency, cost, and quality of the manufacturing process. Let’s explore the 3 primarily three types of mold cavities:
- A single-cavity mold, as the name suggests, has one cavity and produces one unit per cycle.
- Multi-cavity molds, on the other hand, have multiple identical cavities and can produce several units at a go. These molds can contain up to 128 cavities and are typically multiples of 2. The most common cavity tools are 2, 4, 8, 16, 32, and 64 with 128 cavities being very rare.
- Family molds are a unique type of mold with cavities for multiple parts that often go together.
Each of these mold types carries its own set of benefits and drawbacks, making them suitable for different applications. To make the right choice, it’s important to understand these mold types in more detail.
Single Cavity Molds
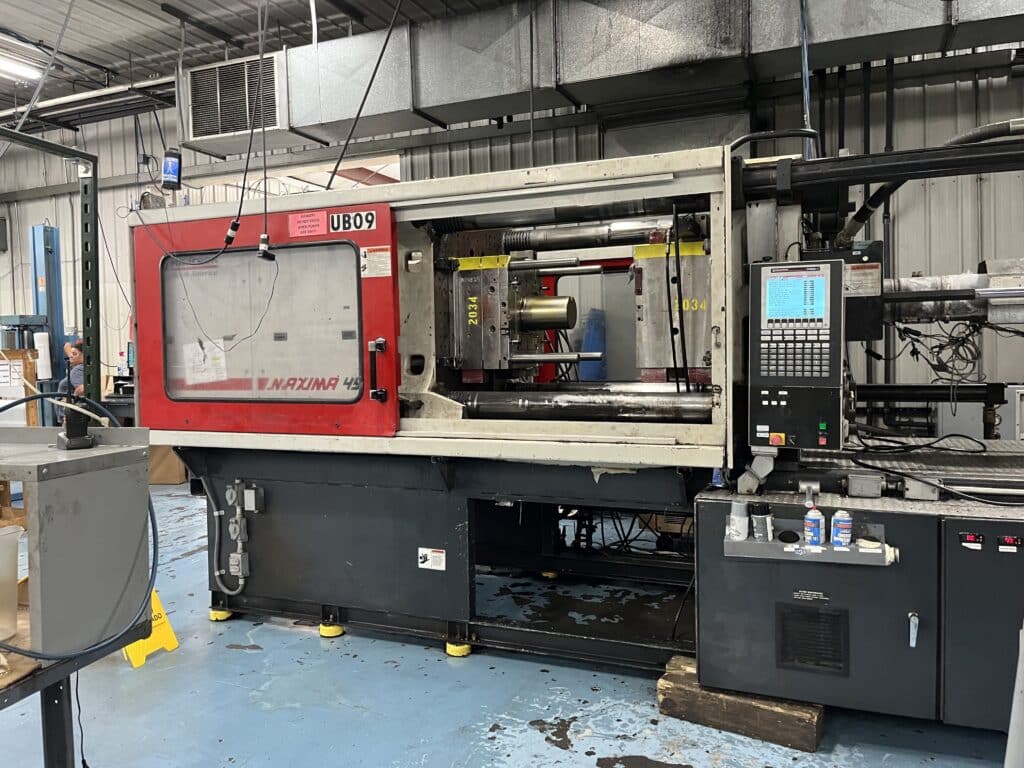
Single cavity molds are a type of injection mold that produces one plastic part per cycle. This type is ideal for producing high-quality, complex parts and for short production runs (low volume). It’s also great for manufacturing large or complex parts as it allows for a greater focus on the quality and precision of each individual item.
Additionally, single cavity molds are a good choice for testing products. For example, if you think you can sell a large volume but don’t have the budget for a multi cavity mold, a single cavity mold will give you product to test before you build a larger cavity mold. If this test goes well, you can build the same thing. This test also helps you learn if modifications are necessary, and at a lower cost than if you were using a large cavity mold.
However, single-cavity molds may not be the most efficient option for all production needs.
While they ensure high-quality parts, their one-part-per-cycle nature means slower production rates, which can lead to higher costs, especially for large-scale manufacturing projects.
Despite these potential drawbacks, single cavity molds are the perfect choice for projects that prioritize quality over quantity. An example of an ideal application for single cavity molds would be high-quality cases to store collectible items in.
With fewer cavities, production can be more focused on detail and fit. It also enables greater control over the entire process to ensure quality is consistent.
Multi-Cavity Molds
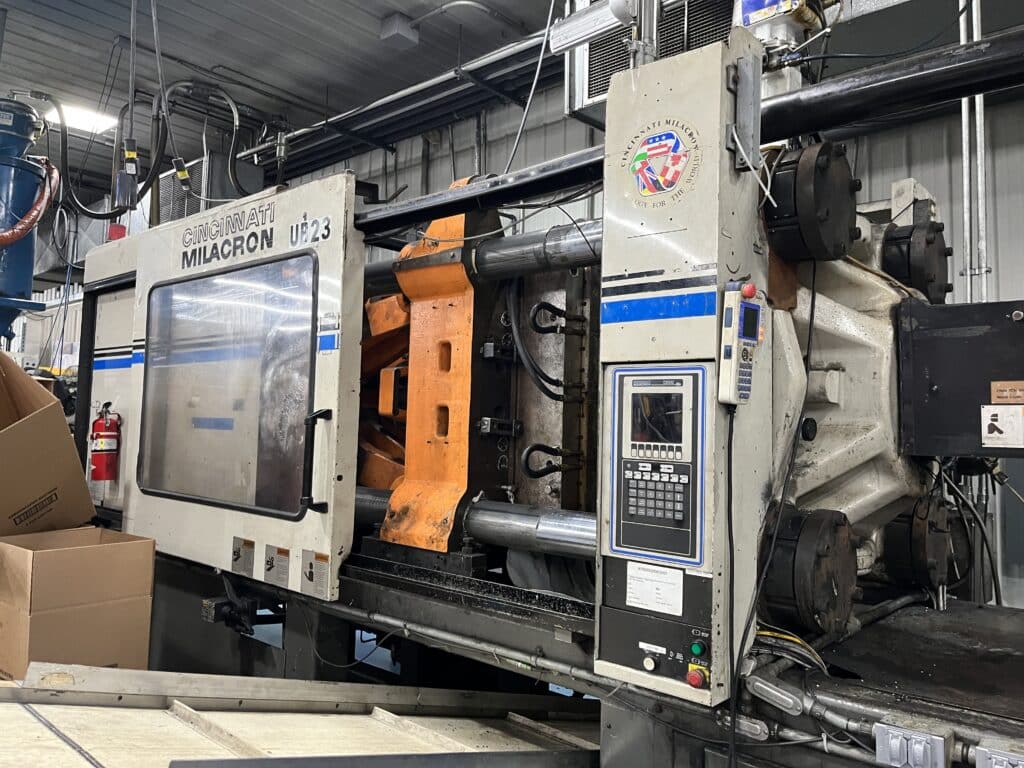
Multi-cavity molds are a type of injection mold design where multiple identical cavities are incorporated into a single mold.
This setup allows the simultaneous production of multiple identical parts in a single cycle, increasing manufacturing efficiency and reducing production time. Since multi-cavity molds have multiple cavities that create identical parts in one cycle they can be more efficient in terms of production speed and cost per part. It’s an excellent choice for mass production where high volumes of identical parts are required.
However, multi-cavity molds come with their own set of challenges. The initial cost is higher due to the complexity of creating multiple identical cavities.
Maintaining uniformity across all the cavities can also be demanding, both in terms of precision during mold creation and maintaining consistent processing conditions during production. Any variation could lead to inconsistent parts, which might require further processing or even result in scrap.
Multi-cavity molds shine in scenarios where there is a need for high-volume production of uniform parts.
Industries such as consumer electronics, automotive, and food packaging often use these types of molds to meet their high demand and maintain consistent quality.
In these photos below see how an 8-cavity mold was used to create plastic pieces for landscape edging.

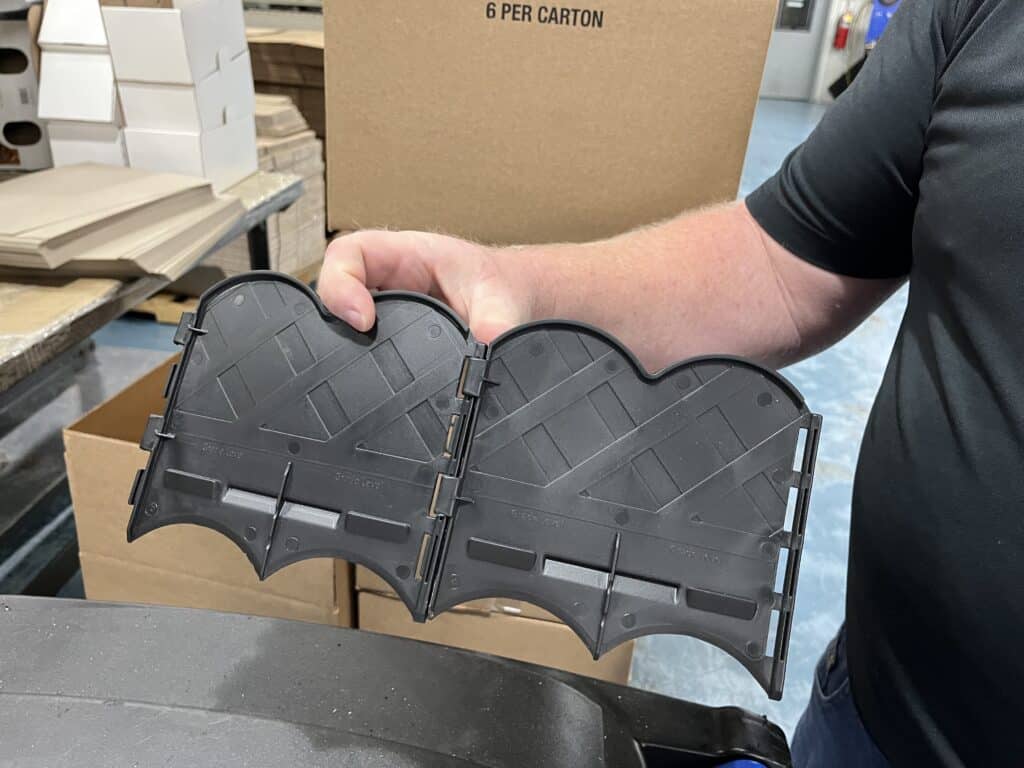
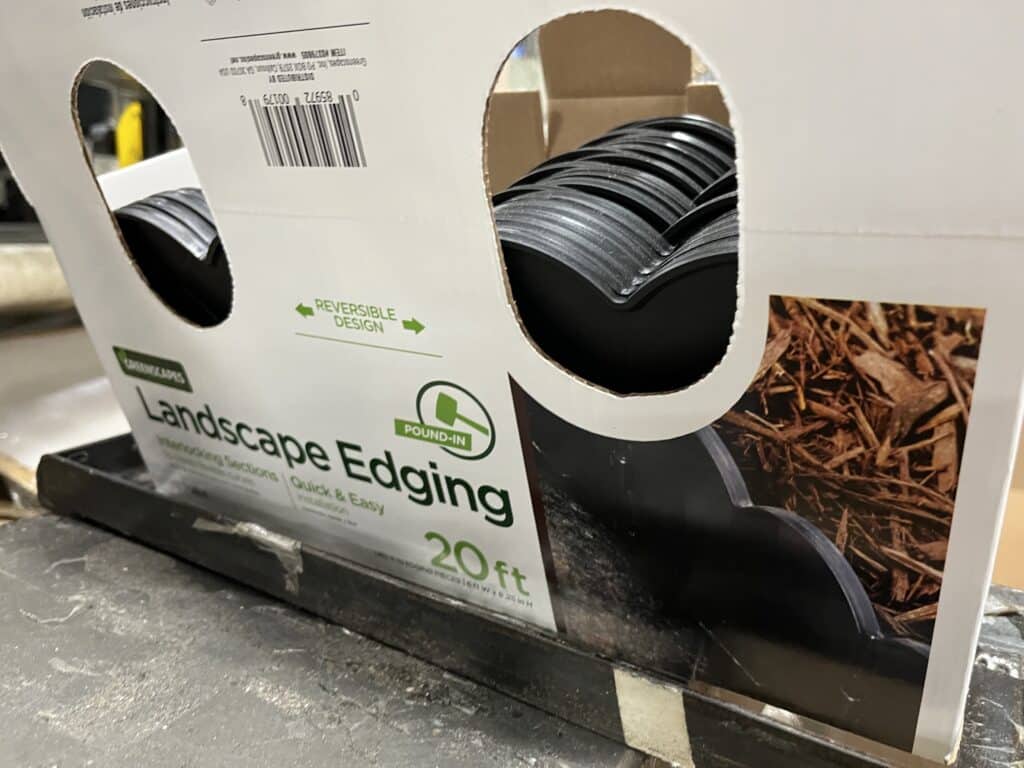
Notice how one 8-cavity mold seamlessly created these 8 pieces which are ready for assembly. But how does this all work? The diagram below shows how the material flowed through the 8-cavity mold to create this finished product.
In the 8-cavity mold, the mold is balanced on all sides so that the material can flow evenly through the parts. Reference the diagram below. The circle in the center is where the material flows into the mold. The lines represent what’s called a “runner” and the large circles on the outside represent the parts. The arrows demonstrate how the material flows through the mold. Once the material flows through, it creates the part and the finished product is pushed out onto a conveyor belt where the parts can then be assembled and boxed up for shipping.
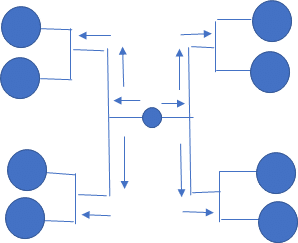
When considering whether to use a multi-cavity mold, factors such as production volume, part uniformity, and budget should be taken into account. An experienced custom injection molding company can help you to determine which type of mold is right for your product needs.
Family Molds
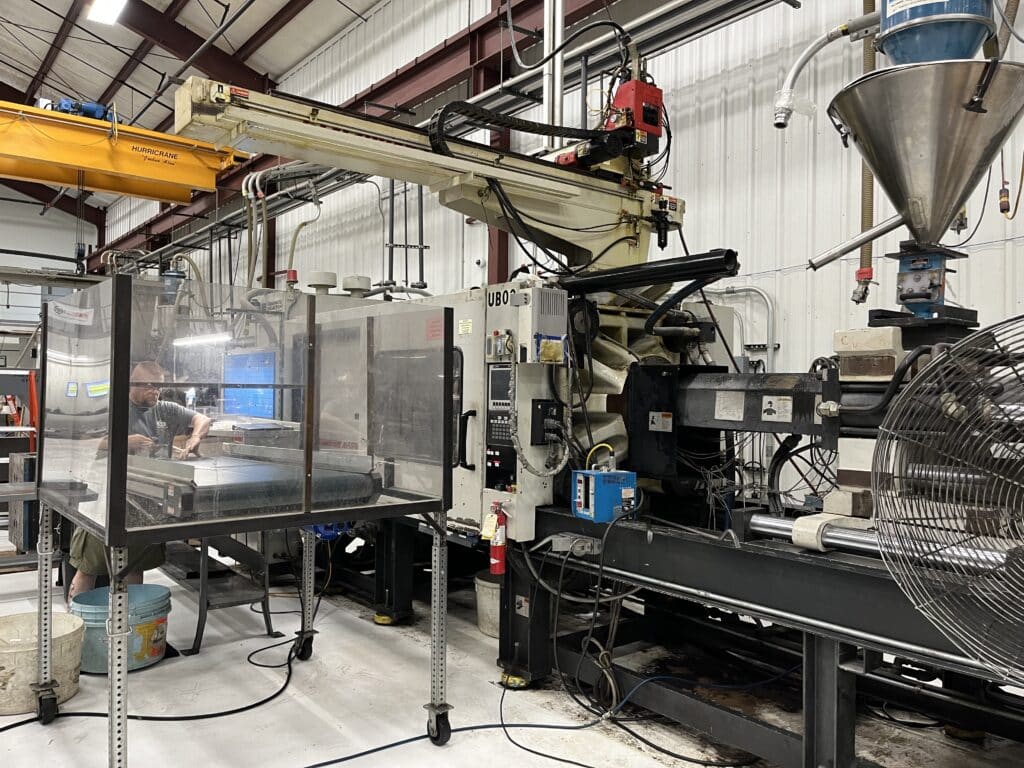
Family molds are unique in the realm of injection molding. They are essentially a combination of single and multi-cavity molds, producing different parts of an assembly during a single cycle.
They consist of two or more parts for a product family or a series of related components, all contained within one mold. This setup allows for the simultaneous production of all components, eliminating the need to produce them separately in multiple molding cycles.
Despite their convenience, family molds are not without their drawbacks. The main challenge lies in ensuring uniform filling for all the parts, as they may vary in size, shape, or thickness.
Inadequate filling can result in quality issues with the final product. Additionally, in the event of a defect or damage, the entire mold needs to be shut down for repair, affecting the production of all parts.
On the positive side, family molds can lead to significant cost and time savings.
They reduce the number of molding cycles, decrease the amount of plastic waste, and require less energy. These molds are particularly suitable for products that need to be assembled post-molding, as they ensure that all components are available at the same time.
They also find extensive use in small-scale productions or when the parts are too small to justify the use of a multi-cavity mold. These molds are cost-effective for producing complex assemblies but have the challenge of ensuring all parts are of equal quality and precision.
Comparing Single Cavity, Multi-Cavity, and Family Molds
The choice depends on several factors, including the complexity of the part, the required production volume, the material used, and the available budget.
Volume of Production
For example, a company producing a high volume of simple parts may benefit from a multi-cavity mold, while a company needing a small number of complex parts might choose a single cavity mold.
Family molds can be an excellent choice if you are producing multiple different parts for an assembly.
Material Choice for Each Mold Type
While the material choice largely depends on the product specifications, some materials may be more suitable for specific mold types due to factors such as cooling rates and shrinkage. For example, if the material needs to be different for different parts of the family mold, a family mold really isn’t the bes choice.
It’s best to consult with your injection molding partner, such as Pioneer Plastics, to make an informed decision.
Switching Molds During the Process
Switching between mold types is possible, but it would require a new mold to be made, which can be costly and time-consuming. Therefore, it’s crucial to choose the right mold type at the beginning of the production process.
Pioneer Plastics: Your Trusted Injection Molding Partner
Pioneer Plastics stands as a beacon of expertise in the realm of injection molding. Harnessing decades of industry experience, we provide unparalleled insight into the intricate world of injection mold cavities.
We understand that navigating the nuances of single-cavity, multi-cavity, and family molds can be overwhelming, which is why we’re committed to supporting you every step of the way.
Our team of seasoned professionals possesses in-depth knowledge of these mold types, allowing us to provide timely and practical advice on selecting the ideal mold for your specific manufacturing needs.
We offer a comprehensive suite of services related to single-cavity, multi-cavity, and family molds, ensuring a one-stop solution for all your injection molding requirements.
From the initial consultation phase through to production and quality assurance, we strive to deliver an exceptional customer experience that is anchored on quality, efficiency, and excellent customer service.
Our vast experience and expertise allow us to provide injection molding solutions across a wide array of industries.
Our track record of successful delivery across diverse industries underscores our versatility and adaptability, making us your ideal family mold injection molding company, supplier, and manufacturer.
At Pioneer Plastics, we don’t just provide services; we build partnerships. We believe in fostering strong relationships with our clients, understanding their unique needs, and delivering solutions that not only meet but exceed their expectations.
So, if you’re searching for a trusted, reliable family mold manufacturer or a partner for your injection molding needs, look no further than Pioneer Plastics.
Making the Right Choice for Your Injection Molding Needs
Understanding the nuances between single-cavity, multi-cavity, and family molds is crucial to making an informed decision for your injection molding needs. It’s not just about the cost, but also the production volume, complexity of the part, and the material used.
Making the right choice can significantly impact the efficiency and success of your manufacturing process.
Pioneer Plastics is committed to assisting businesses and individuals in navigating these choices. We aim to help our clients find the optimal solution tailored to their specific needs, ensuring a smooth and efficient injection molding process.
With our expert knowledge and vast experience, we can guide you through the complexities of injection molding, from selecting the right mold type to addressing any issues that may arise during production.
If you’re unsure about which mold type to choose for your injection molding needs, get in touch with us at Pioneer Plastics. We’re more than happy to discuss your project requirements and provide you with the best possible solutions.
Remember, the success of your project is our primary concern, and we’re here to ensure you achieve it.