When it comes to custom injection molding, the process of ejecting the finished part from the mold is just as crucial as the actual molding process itself. Proper part removal ensures the integrity of the molded part while minimizing production time and cost.
In this blog, we will focus on one of the essential methods used for part removal – the stripper plate. We will explore what a stripper plate is, how it works, and why it is a popular choice in custom injection molding.
Custom Injection Molding and its Applications
Injection molding is a versatile manufacturing process used to produce a wide range of plastic parts and components. It involves injecting molten plastic material into a mold cavity, where it cools and solidifies to form the desired shape.
This process is ideal for creating high-volume production of identical parts with complex geometries, tight tolerances, and excellent surface finish.
Injection molding has found applications in various industries, including automotive, medical, consumer goods, packaging, electronics, and more. From small and intricate components like gears and connectors to larger parts such as automotive dashboards and appliance housings, injection molding enables the production of a vast array of plastic products used in our everyday lives.
The Process of Creating a Plastic Part Through Custom Injection Molding
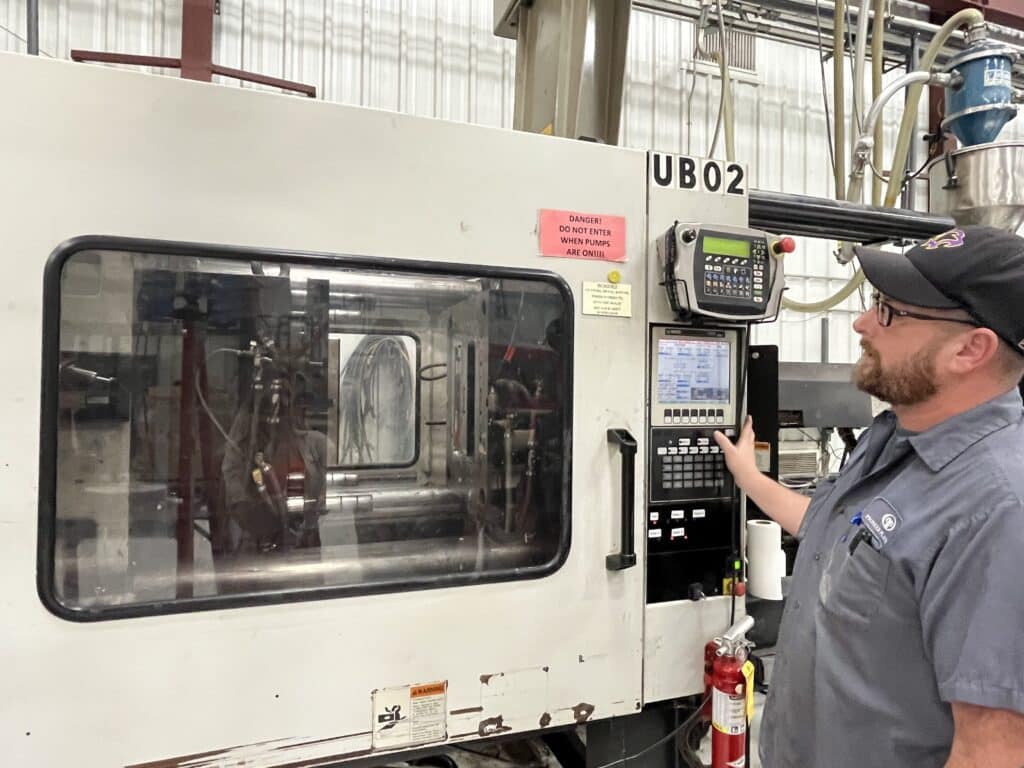
In custom injection molding, the process of creating a plastic part involves several steps, with the injection molding machine playing a crucial role in each phase. Here’s a step-by-step breakdown of how a plastic part is produced using the machine:
Mold Preparation
The first step is preparing the mold for the injection molding process. The mold consists of two halves – the cavity and core – which define the shape and features of the final part. The mold is clamped securely in the injection molding machine’s clamping unit.
Plastic Material Preparation
Plastic pellets or granules are poured into the machine’s hopper, which feeds the material into the injection unit. The plastic material is typically in solid form at room temperature and needs to be heated and melted before injection.
Injection Phase
The plastic material is then fed into a heated barrel, where a rotating screw carries it forward along the barrel. The screw’s friction and heating elements within the barrel melt the plastic. Once the material reaches the desired temperature and consistency, the injection unit pushes it forward, injecting it into the mold cavity through a nozzle and into the sprue or gate.
Cooling and Solidification
After the molten plastic material fills the mold cavity, the cooling process begins. The mold’s cooling channels and lines, often accompanied by coolants such as water or oil, help dissipate heat and accelerate the solidification of the plastic. This ensures that the part takes on its final shape and maintains its integrity.
Part Ejection
Once the plastic has solidified, the mold is opened using the clamping unit of the injection molding machine. An ejection system, such as ejector pins or a stripper plate, is employed to remove the part from the mold. This process is carefully designed to avoid damaging the part or the mold.
Part Finishing
Depending on the requirements of the final part, additional finishing operations may be necessary. This can include trimming excess material or performing secondary processes such as painting, printing, or assembly.
Throughout the entire process, the injection molding machine’s control panel plays a crucial role. Operators monitor and adjust various parameters such as temperature, pressure, injection speed, and cooling time to fine-tune the process and achieve the desired part quality and consistency.
By precisely controlling the injection molding machine, manufacturers can produce high-quality plastic parts with complex geometries, tight tolerances, and excellent surface finishes. This makes custom injection molding a preferred method for mass production of plastic components in various industries.
Removing The Molded Part from the Mold—3 Common Ejection Methods
There are three commonly used options for part ejection – air ejection, ejector pins, and stripper plates. Each of these methods offers unique advantages and features, providing manufacturers with flexible solutions to meet their specific needs.
Air Ejection
Air ejection is a widely used method in injection molding, especially for smaller parts or those with intricate features. Compressed air is introduced into the mold cavity, creating a pressure differential that pushes the part away from the mold surface. While effective for simple parts, air ejection may not be suitable for larger or more complex parts, as the air can sometimes damage or distort delicate features.
Ejector Pins
Ejector pins are another common method used to remove parts from the mold. These pins are strategically placed around the mold and are activated after the plastic has cooled and solidified. They extend into the mold cavity, pushing the part out by applying force on its backside. Ejector pins are effective for most part geometries and can be customized to fit specific mold designs. However, they do leave small witness marks or ejector pin marks on the part, which may require additional finishing.
Stripper Plate
The third method for part removal in custom injection molding is the use of a stripper plate. A stripper plate is a mechanism located within the mold, specifically designed to slide or lift the part off the core. It consists of a plate or set of plates that are mounted on a separate plate within the mold, parallel to the parting line.
The stripper plate is typically actuated by hydraulic cylinders or mechanical mechanisms, enabling it to move in a controlled manner. The plate uses a combination of mechanical force and precision to strip the part away from the core while ensuring its integrity and minimizing any potential damage or distortion.
Key Advantages of Using A Stripper Plate for Part Ejection
Stripper plates provide numerous advantages that make them a preferred choice in many molding applications. From ensuring excellent surface finish to protecting delicate parts, stripper plates offer unique benefits that contribute to the overall quality and productivity of the injection molding process.
- Versatility – Stripper plates are suitable for a wide range of part sizes and shapes. They work well with both simple and complex geometries, regardless of the presence of undercuts or recesses.
- Surface Finish – Stripper plates provide excellent part surface finish since they eliminate the need for ejector pin marks. This reduces the need for secondary finishing operations, saving both time and cost in the production process.
- Part Protection – With a stripper plate, there is minimal direct contact between the part and the stripping mechanism, reducing the risk of damage or deformation to the part during removal. This makes the stripper plate an ideal choice for delicate or precision parts.
- Efficiency – The use of a stripper plate can significantly improve production efficiency. Its controlled and automated stripping process allows for faster cycle times, resulting in increased productivity and lower overall manufacturing costs.
Need Custom Injection Molding for Your Plastic Part?
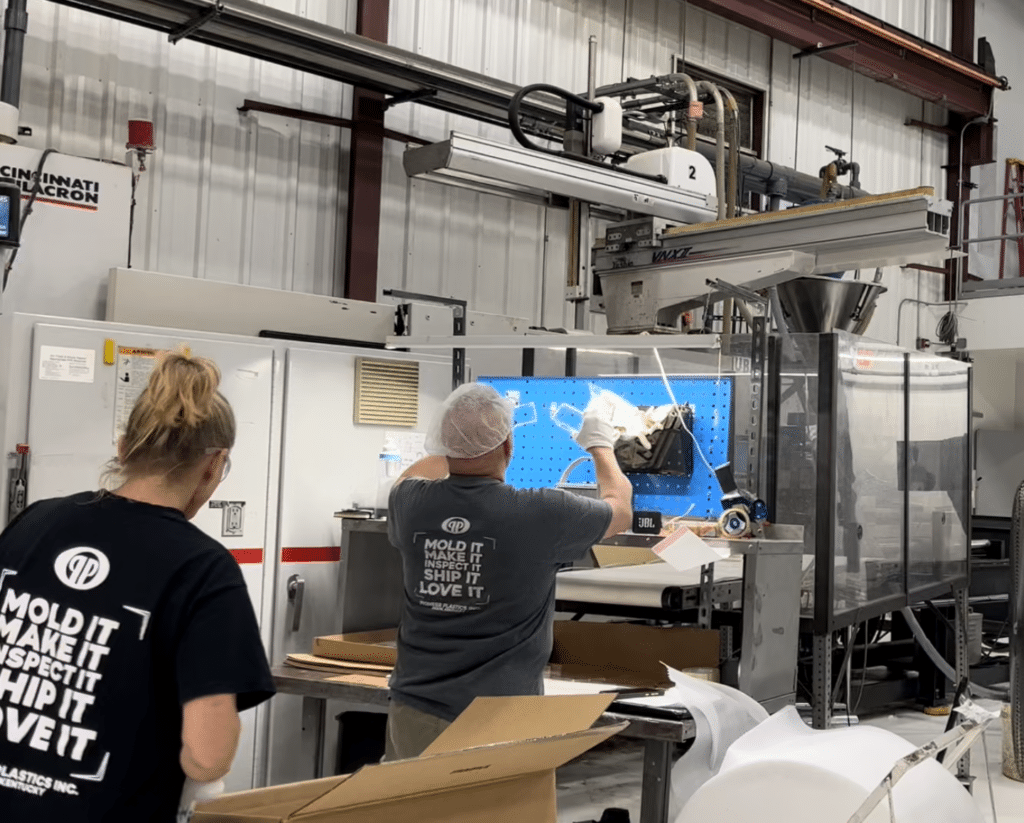
Injection molding is a highly versatile manufacturing process utilized to produce a wide range of plastic parts used in various industries. As technology and innovation continue to advance, injection molding continues to be a preferred method for cost-effective and efficient manufacturing of plastic components.
The method of part removal plays a vital role in ensuring successful production. While air ejection and ejector pins are commonly used options, the stripper plate offers distinct advantages, making it a preferred choice for many applications.
At Pioneer Plastics, we understand the importance of efficient part removal and employ various techniques, including the use of stripper plates, to ensure the highest quality molded parts for our customers. With our extensive expertise in custom injection molding, we provide tailored solutions that meet your specific requirements, while optimizing production efficiency.
Contact us to learn more about our custom injection molding services today.