367 million metric tons of plastic were produced in 2020 — a million metric tons less than the record high of 2019. From bottles and toys to automotive parts and surgical supplies, the unique material properties of plastic have given it an important place in our everyday lives.
Types of Plastic Molding
But how do plastic parts factories manufacture plastic parts, and which method best suits your project?
Although the compounds and molecular structure of plastics vary significantly, the techniques used to form these items are relatively simple.
Injection Molding
By far the most versatile plastic molding process, injection molding enables the manufacturing of plastic parts with the most complex geometry. The first step in the process is to design a custom mold according to the shape of the desired finished product. This type of mold is usually made with steel, due to its high melting point and chemical stability.
Once the mold is created, it is put into an injection molding machine. Plastic granules are melted and injected into it. The molten plastic is pressed to ensure uniformity and a proper fit within the mold. Once the molten plastic has been adequately pressed into the mold, it is allowed to cool until it sets. The final product is ejected from the mold — typically by a set pins or air to blow it off — and can be finished according to spec.
There are many different types of presses available for use, and they are rated according to how much force (measured in tonnage) they can deliver. A few parameters to consider when selecting a press are: required force, material flow index (MFI), clamping requirements, and safety factor — among others.
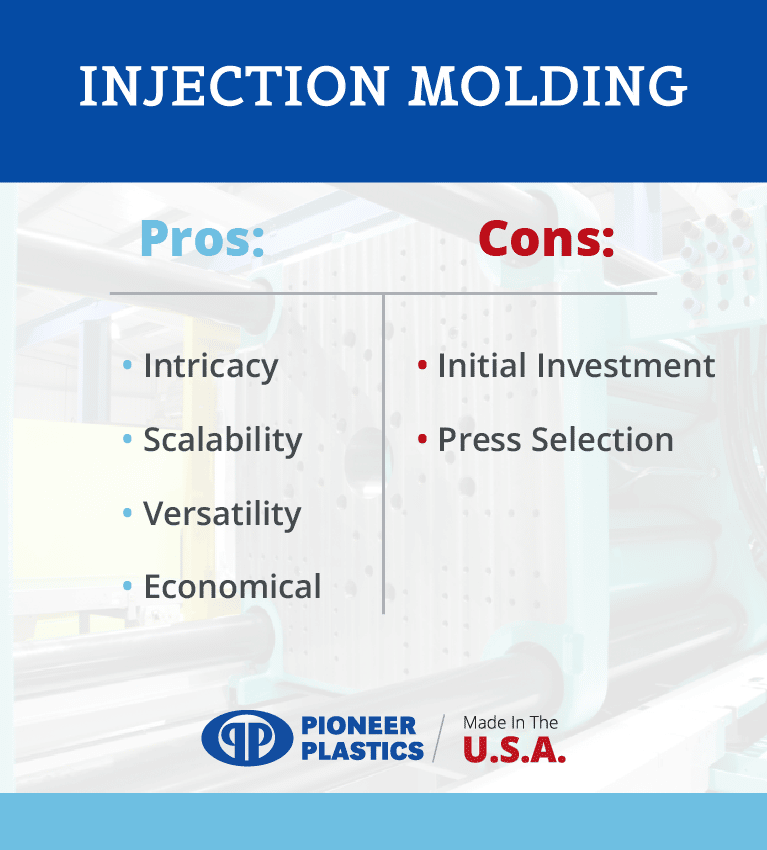
Pros
There are several advantages to injection molding over other plastic molding production methods, like:
- Intricacy. From holes and pegs to precision curvature, some plastic parts possess many details. Forming a mold in the exact part geometry ensures that each feature is accounted for, enabling the manufacture of some of the most intricate plastic parts.
- Scalability. Whether it’s a stable grid for your livestock barn flooring or a display case for your championship ring, injection molding enables manufacturers to make plastic products of any size.
- Versatility. By allowing additional compounds to be added into the granule mix, the injection molding process enables designers and engineers to get the exact properties they’re looking for. Colorants, resin type, and finishes are just a few customizations available in the manufacturing of your injection-molded product.
- Economy. On a cost-per-part basis, injection molding is a very economical means of manufacturing your product.
Cons
Despite its many advantages, some drawbacks of injection molding do exist, namely:
- Initial investment. Injection molding first requires a mold in the shape of the desired part, the cost of which can vary based upon material, size, and level of detail. This is usually only a one time investment, but can present a barrier to getting started.
- Press selection. Less a disadvantage than a parameter to consider, many different types of presses exist, so choosing the right one for your plastic part will take some consideration.
Overall, injection molding offers comparatively few drawbacks relative to the many benefits of this highly efficient manufacturing method. No wonder it’s the most common plastic manufacturing method!
Rotational Molding
Despite all the uses of injection molding, there are some plastic parts where a different manufacturing method is required. One such scenario is when a press cannot be used to fill the molten plastic within the mold. This is often the case with large, hollow, one-piece parts, such as containers, tanks, bladders, etc.
In applications like these, rotational molding is an excellent alternative. Here the plastic pellets are injected into a mold as before, but instead of being pressed to fill the cavity, they are rotated (or shaken) to deliver an even coating within the mold. Also known as rotomolding, this production method relies on the principle of centrifugal force to distribute the plastic uniformly.
Just as press selection is a key component of injection molding, determining the proper rotational speed is crucial in rotomolding design. Typical rotational molding occurs at relatively slow rates, with average speeds ranging from 2 to 20 RPM. Too slow, and the molten plastic may not experience enough centrifugal force to be moved. Too fast, and it may not coat the mold evenly.
Other parameters to consider are operating temperature, MPI, and wall thickness.
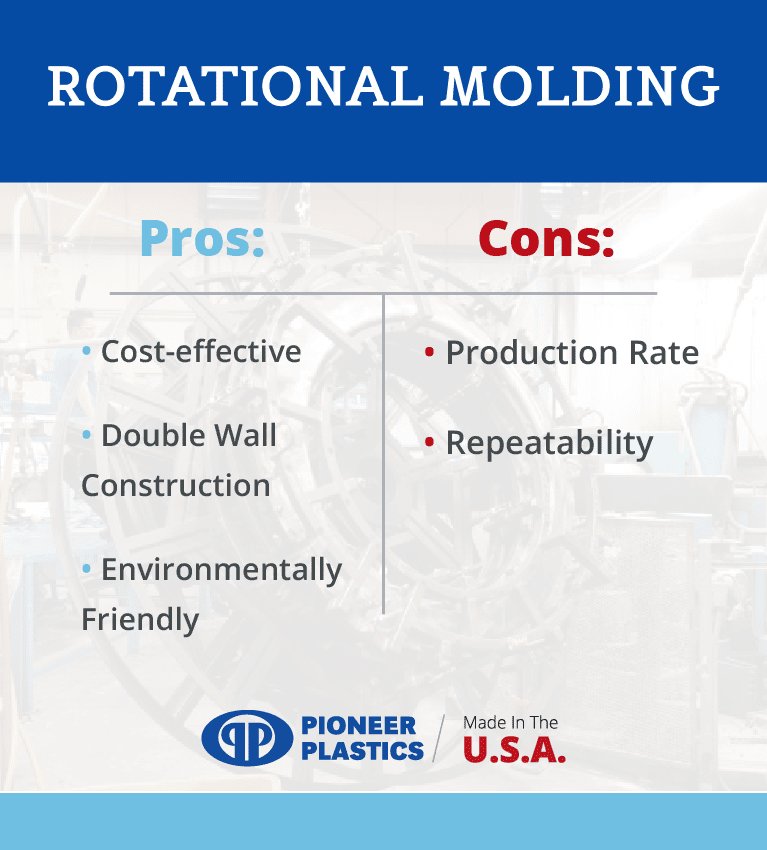
Pros
Some of the primary benefits offered by rotational molding include:
- Cost-effective. For one-piece, hollow parts ill-suited to other manufacturing processes, rotational molding is a very economical means of production. The process is relatively simple, and is a cost-effective way to produce detailed hollow parts.
- Double-wall construction. Rotomolding is especially useful in products with a double wall in their design. Helpful in applications where insulation is a must, little more than a multi-layered cavity is required to realize this type of design.
- Environmentally friendly. Minimal material loss occurs throughout the rotomolding process, and the little excess that is wasted can often be reused. This makes it a relatively efficient method, and gives it a lower carbon footprint.
Cons
No manufacturing process is perfect, and rotomolding is not without its flaws. A few weaknesses are:
- Production rate. The low RPM at which rotational molding takes place means that fewer parts can be made per hour. Longer production times can reduce productivity, and potentially lead to profit loss.
- Repeatability. Rotomolded products often require little tooling and are often finished with softer materials like aluminum, but what tooling is done can take its toll. Softer tools wear out faster and must be replaced more frequently, adding one more cost to the process.
These drawbacks should be considered within the product design process, but they don’t take away from the fact that rotational molding is still a very effective way of making certain plastic parts.
Blow Molding
Another very common manufacturing method is blow molding. Useful for manufacturing hollow parts like bottles or jugs, blow molding involves the expulsion of air into a heated plastic mass or tube until it is forced up against the walls of a mold and reaches the desired geometry. The mass or tube is known as a parison, and the entire process is very similar to blown glass production.
Because both are used in the making of hollow plastic parts, blow molding and rotational molding are often compared when selecting a manufacturing method. The two are very different, though, as both the method and application vary significantly. Here are the pros and cons of each:
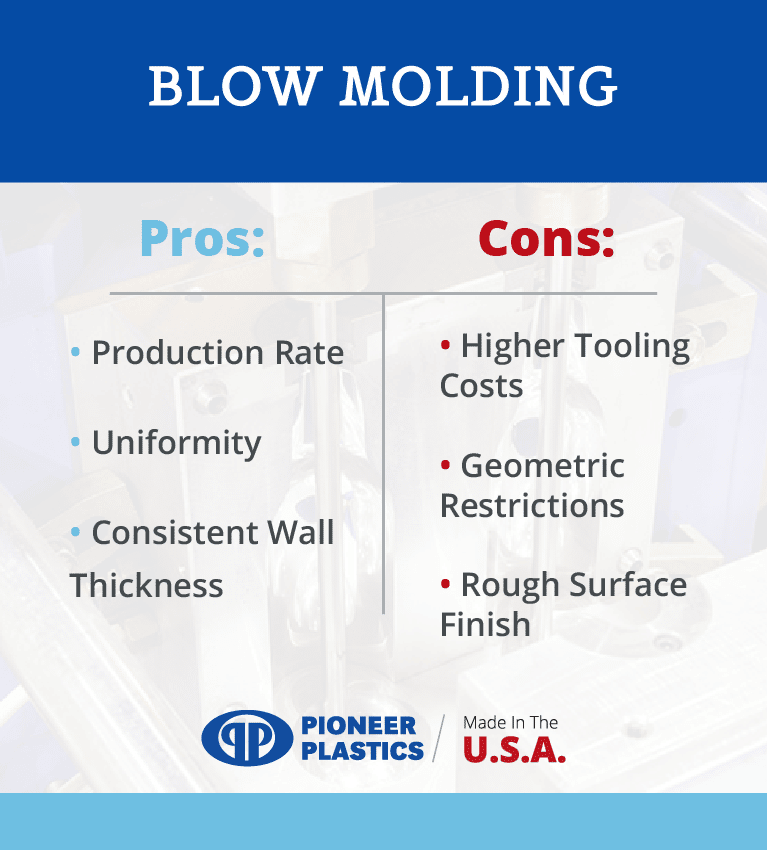
Pros
- Production rate. Replacing slower rotation rates with faster air injection, the time it takes to make a piece via blow molding is significantly less than that of rotomolding. That means significantly more parts can be made, to the effect of 20,000–30,000 parts per year, compared to 2,000–4,000 from a single rotational mold.
- Uniformity. Most commonly used in the realization of a simple design, blow molding is more frequently used for parts with a uniform geometry, where little detail is involved.
- Consistent wall thickness. While rotomolding is best for parts with varying wall thicknesses, blow molding is more frequently used for products featuring a single wall thickness, especially for thin-walled products like bottles or cups.
Cons
Although an excellent choice for quickly producing uniform, thin-walled products, blow molding is not the best choice for every project. Some of the disadvantages of blow molding are:
- Higher tooling costs. Blow molding requires machinery to pinch or cut off its final blown product, and those are more expensive than simpler rotomolding tools. Because of that, blow molding tooling costs can be 6–10 times higher than rotomolding costs.
- Geometric restrictions. Blow molding is effective in manufacturing simple part shapes, but it does not lend itself well to more complex geometries; those may need to be made with rotomolding.
- Rougher surface finish. Blow molding can produce pronounced parting lines and a rougher surface finish — traits that may not always be desirable.
Overall, blow molding is very suitable for the mass production of simple, inexpensive parts. However, its much higher tooling costs and rougher exteriors should be taken into account.
Pioneer Plastics: On the Frontier of Plastic Molding Production
There are many factors to consider when selecting the manufacturing process that will make your product come to life. Injection molding is an efficient, customizable way to produce the most complex product geometries, but design parameters, like material selection, must be considered carefully.
For hollow parts where a part would fail, rotational molding allows for detailed features with minimal machining, but production rates can be slower, and the softer tools used may need to be replaced more often. Blow molding is highly effective for rapidly manufacturing simple, cost-effective designs, but the tooling costs are much higher — and still other methods like extrusion and compression molding are available.
At Pioneer Plastics, our designers and engineers have extensive experience molding plastic parts. We understand the manufacturing process, and can help you select the most efficient way to build your product. Contact us today, and we’ll turn your plastic design into a reality.