In today’s rapidly evolving manufacturing landscape, staying ahead of the curve is essential. For engineers, designers, and manufacturers in the plastic injection molding industry, leveraging advanced technologies like Computer-Aided Design (CAD) modeling is no longer a luxury—it’s a necessity.
CAD modeling has revolutionized product design processes, enhancing efficiency, precision, and innovation. This article delves into the world of CAD modeling, exploring its types, evolution, applications, and transformative impact on product design, particularly in plastics and injection molding.
What is CAD Modeling?
Computer-Aided Design (CAD) modeling refers to the use of computer systems to assist in the creation, modification, analysis, or optimization of a design. CAD models are digital representations of physical objects, enabling designers to visualize and manipulate them in a virtual environment. In the context of modern product design and manufacturing, CAD modeling plays a pivotal role by enhancing visualization, improving accuracy, reducing errors, and streamlining the design process.
In the plastic injection molding industry, CAD modeling is crucial. It allows for the precise design of molds and plastic parts, facilitating innovation in custom plastic part design. By simulating the injection molding process, CAD modeling helps identify potential issues before production, saving time and resources.
Types of CAD Modeling
Understanding the different types of CAD modeling is crucial for selecting the appropriate tools and techniques for specific design needs. Here are the primary types of CAD modeling:
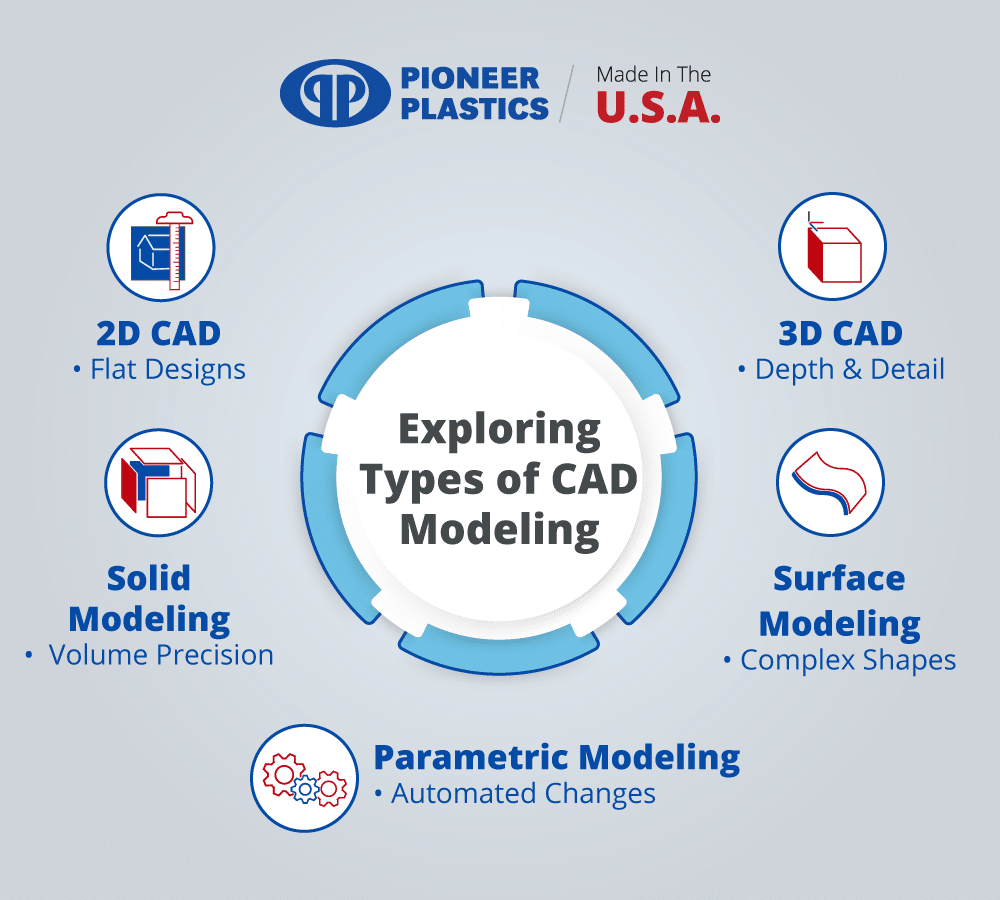
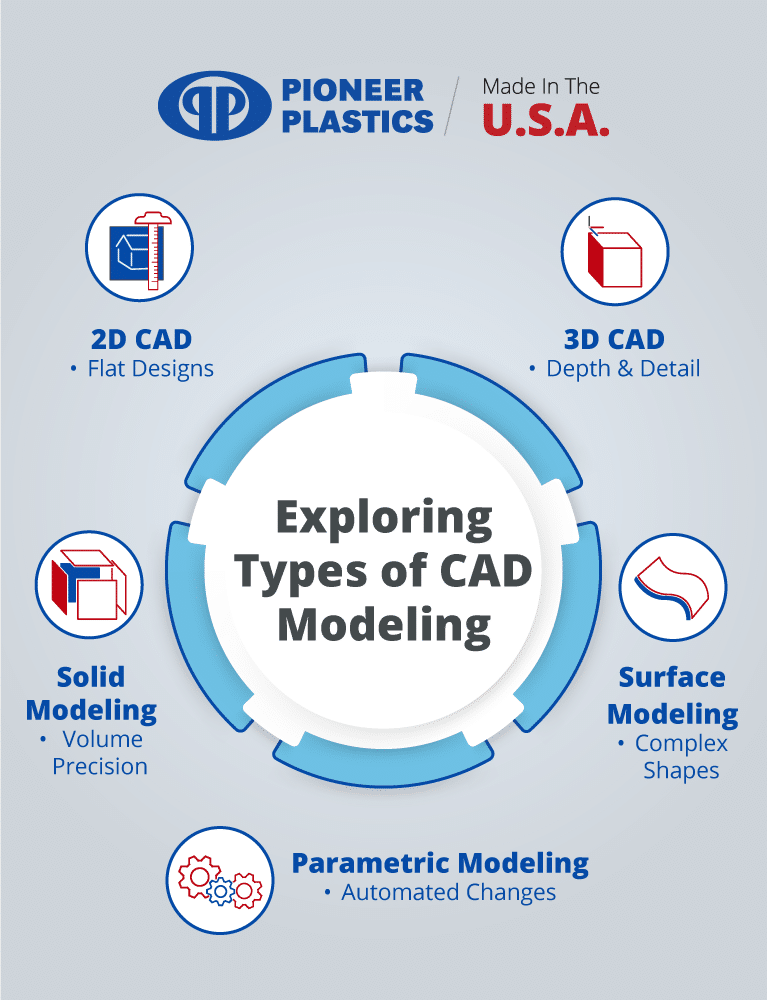
2D CAD: Basic Drawing and Design Applications
2D CAD involves creating flat drawings of products, which serve as the foundation for initial design sketches of plastic products. This type is ideal for:
- Drafting basic outlines and plans
- Designing simple components with minimal complexity
- Preparing schematic diagrams and technical drawings
Although 2D CAD lacks the depth of 3D modeling, it remains valuable for quick sketches and preliminary designs in plastic product development.
3D CAD: Advanced Modeling for Detailed Product Design
3D CAD takes design to the next level by adding depth to the traditional two dimensions. It enhances precision and visualization, allowing designers to:
- Create detailed models with complex geometries
- Visualize products from any angle
- Simulate real-world performance and interactions
In the injection molding sector, 3D CAD is vital for designing intricate parts and assemblies, ensuring that every detail aligns with manufacturing capabilities.
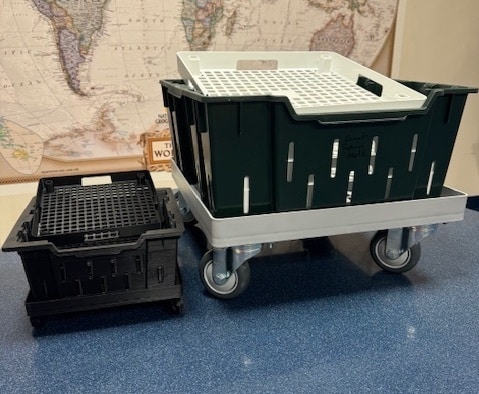
The image above features an example of how Pioneer Plastics used 3D CAD and a 3D printer to create a smaller model of a product (left) before creating the final (right).
Solid Modeling: Creating Accurate Part Geometries
Solid modeling focuses on representing the volume of the object, not just its surfaces. This approach is beneficial for:
- Ensuring dimensional accuracy
- Performing interference and collision detection
- Facilitating prototype development in plastics
By providing a complete representation of the object, solid modeling allows for comprehensive analysis and testing before production.
Surface Modeling: Designing Complex Surface Structures
Surface modeling involves manipulating the exterior surfaces of a model, which is essential for:
- Designing visually appealing plastic products
- Creating complex shapes and curves
- Refining ergonomic features
This type is particularly useful when the visual appearance and surface quality are paramount, such as in consumer products and automotive components through surface modeling.
Parametric Modeling: Automating Design Changes
Parametric modeling involves creating relationships between different parts of the model, allowing for automatic updates when a change is made. This is valuable for:
- Design changes that affect multiple parts
- Creating configurations and variations of a model
- Generating complex geometries based on specific parameters
By automating design changes, parametric modeling significantly reduces the time and effort needed to modify designs, making it a valuable tool in modern manufacturing.
Evolution of CAD Modeling
The journey of CAD modeling began in the mid-20th century and has seen remarkable advancements since then.
Brief History and Milestones in CAD Development
- 1950s-1960s: Early developments with systems like Sketchpad laid the groundwork for interactive graphics.
- 1982: Introduction of AutoCAD revolutionized access to CAD tools across industries.
- 1990s-2000s: Transition to 3D modeling and advancements in solid and parametric modeling techniques.
Transition from Manual Drafting to Digital Modeling
The shift from manual drafting to digital models brought significant benefits:
- Increased Efficiency: Designs could be created and modified faster.
- Improved Accuracy: Reduced human errors associated with manual drawings.
- Enhanced Collaboration: Digital files could be easily shared and reviewed.
Significant Advancements in CAD Technologies
Modern CAD systems now integrate:
- Cloud Computing: Allowing remote access and collaboration through cloud computing.
- Artificial Intelligence: Enabling generative design and optimization with artificial intelligence.
- Virtual and Augmented Reality: Enhancing visualization and interaction with models via virtual reality (VR) and augmented reality (AR).
These advancements have not only improved the functionality of CAD software but have also made it more accessible and collaborative, driving innovation in product design.
Role of CAD in the Digital Transformation of Manufacturing Processes
CAD modeling is at the heart of the digital transformation in manufacturing, enabling:
- Integration with Computer-Aided Manufacturing (CAM) and Computer-Aided Engineering (CAE): Streamlining the transition from design to production.
- Simulation and Analysis: Testing designs under various conditions virtually.
- Customization and Personalization: Facilitating the production of tailored products efficiently.
This integration supports a more agile and responsive manufacturing environment, allowing companies like Pioneer Plastics to adapt quickly to changing market demands and technological advancements.
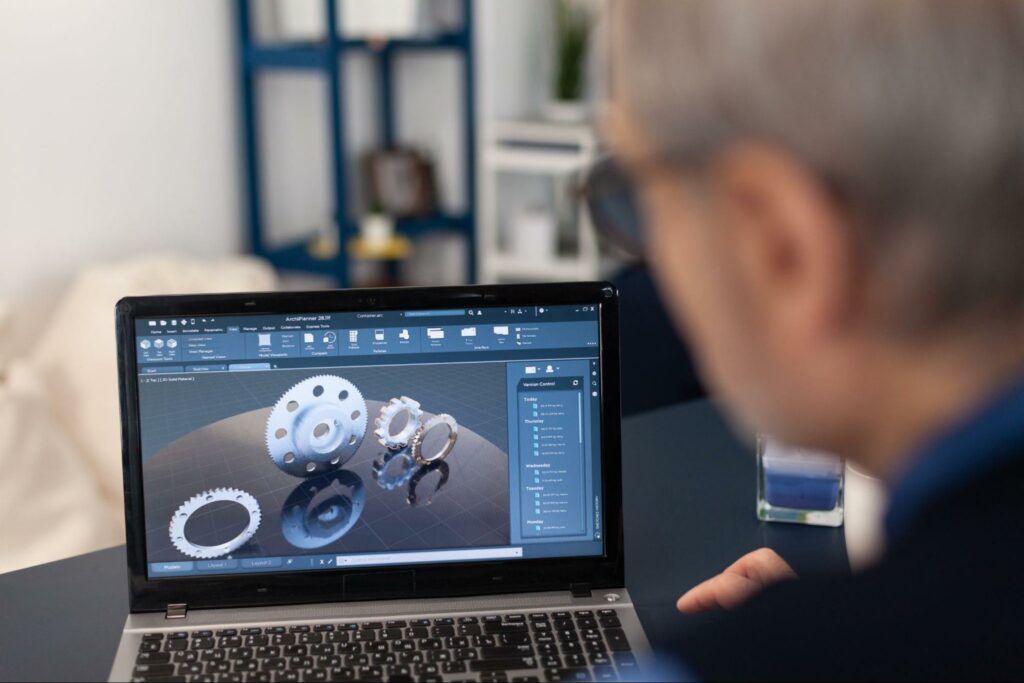
Applications of CAD Modeling in Various Industries
CAD modeling is a versatile tool that has revolutionized several sectors, providing precision, innovation, and efficiency. Here’s how it is applied across different industries:
Automotive Industry: Precision and Customization
- Design and Engineering: CAD models are used for designing complex engine components and safety systems. This improves not just performance, but safety as well.
- Aerodynamic Simulation: CAD modeling allows engineers to simulate and test the aerodynamic efficiency of vehicle designs.
- Personalization: The flexibility of CAD enables modular car designs, catering to custom preferences. Custom configurations can be visualized and refined before production.
Aerospace Industry: Innovation and Safety
- Lightweight Design: CAD tools help in optimizing materials for lightweight and fuel-efficient aircraft structures.
- Safety Testing: By simulating extreme environmental conditions, engineers can ensure structural integrity and safety.
- Breakthrough Designs: CAD fosters the creation of innovative aircraft layouts, pushing the boundaries of traditional design.
Architecture and Construction: Complex and Sustainable Designs
- Building Information Modeling (BIM): CAD integrates multiple facets of building design, from structural engineering to mechanical systems.
- Visualization and Walkthroughs: Realistic 3D renderings and virtual tours are made possible, enhancing design presentation.
- Environmental Analysis: Enables architects to evaluate the energy efficiency and sustainability of new construction projects.
Electronics Industry: Innovation in Miniaturization and Design
- Circuit Board Design: CAD is essential for designing compact, efficient circuit boards used in modern electronics.
- Thermal Management: Simulates heat dissipation to ensure electronic components run efficiently without overheating.
- Ergonomics in Design: CAD facilitates the creation of user-friendly technological devices with optimal physical interfaces.
Plastics and Injection Molding: Precision and Efficiency
- Mold Design: Companies like Pioneer Plastics use CAD to create precise injection molds tailored to specific product requirements.
- Material Efficiency: CAD modeling helps optimize plastic part design to reduce waste and enhance quality.
- Complex Product Development: CAD empowers designers to conceptualize and execute intricate and innovative plastic components that meet client specifications and market needs effectively.
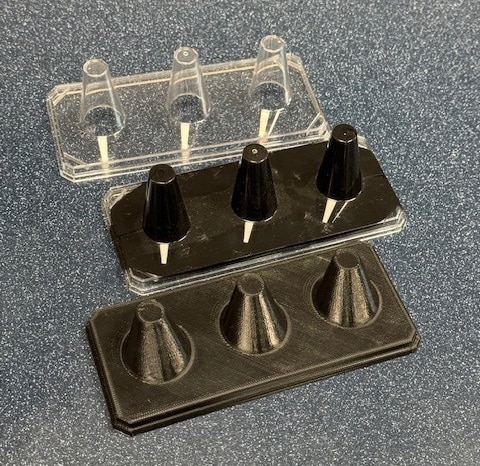
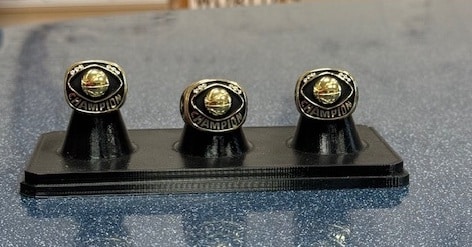
The images above shows how Pioneer Plastics utilized CAD modeling and a 3D printer to create different sizing variations of a ring display case to determine the final model.
CAD modeling continues to play a critical role in these industries, driving innovation, improving efficiency, and enabling the creation of complex structures and products. By leveraging advanced techniques and integrations, companies can significantly enhance their design processes and product offerings.
CAD Modeling Tools and Software
Selecting the right CAD software is essential for maximizing efficiency and achieving design goals.
Popular CAD Software Used in the Industry
- AutoCAD: Versatile for 2D and 3D designs across industries.
- SolidWorks: Favored for mechanical design and parametric modeling.
- CATIA: Used extensively in the aerospace and automotive sectors.
- Fusion 360: A cloud-based platform combining CAD, CAM, and CAE capabilities.
Features and Capabilities of Leading CAD Tools
- 2D and 3D Modeling: From basic sketches to complex assemblies.
- Simulation and Analysis: Testing designs under virtual conditions.
- Collaboration Tools: Enabling team-based design and feedback.
- Generative Design: Utilizing AI to explore optimized design possibilities.
- Integration with CAM and CAE: Seamlessly linking design with manufacturing and engineering analysis.
Software Leveraged by Pioneer Plastics for Product Design
Pioneer Plastics utilizes advanced CAD software to:
- Prototype Development: Rapidly creating designs and testing models.
- Engineering Analysis: Ensuring designs meet all specifications and standards.
- Custom Injection Molding: Designing precise molds for efficient production.
Our selection of CAD tools allows us to maintain a high level of accuracy and efficiency in our design processes. By incorporating tools like Cimatron Technologies software, we can seamlessly transition from conceptual designs to detailed engineering models, ensuring that every product we develop is optimized for performance and manufacturability.
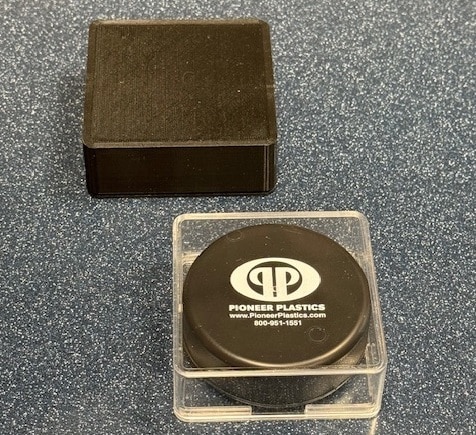
The image above features an example of how Pioneer Plastics uses their CAD software and 3D printer to create a test case (back) to determine the best size for the final model (front).
Integration of CAD with Other Digital Technologies
- Computer-Aided Manufacturing (CAM): Linking designs directly to manufacturing equipment.
- Computer-Aided Engineering (CAE): Providing advanced analysis and simulation capabilities.
- Data Management Systems: Organizing and tracking design revisions and documentation.
This integration not only streamlines the design-to-production workflow but also enhances our ability to innovate and respond to complex design challenges efficiently.
How CAD Modeling Transforms Product Design in Plastics
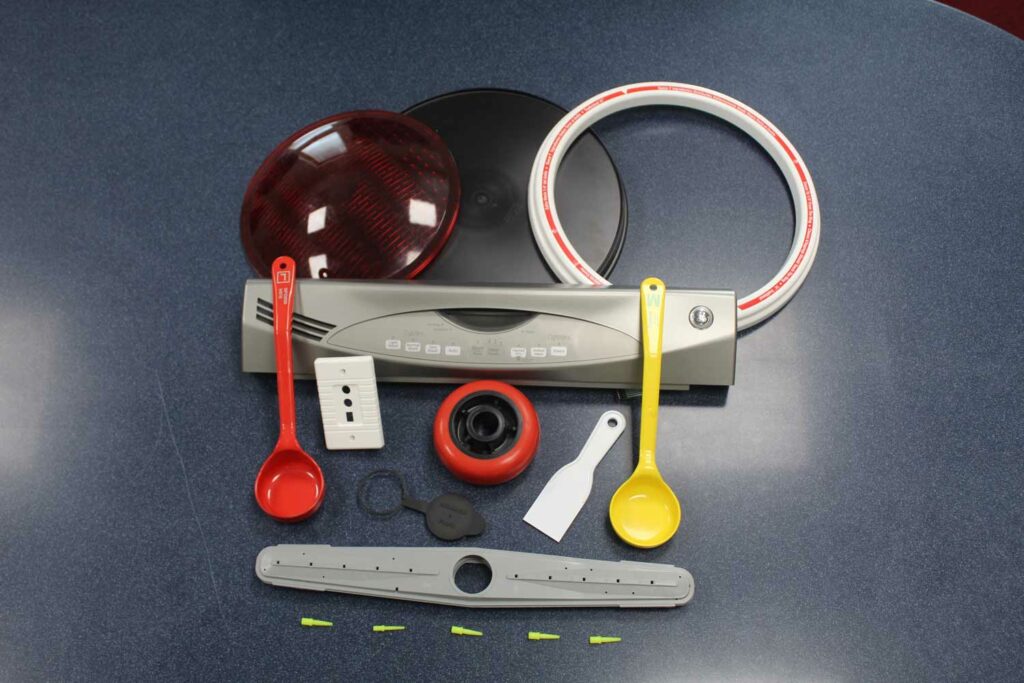
Computer-Aided Design (CAD) modeling significantly enhances product design in the plastics industry, offering numerous advantages that streamline processes and improve outcomes.
Improved Design Accuracy and Reduction of Errors
CAD modeling introduces a high level of precision in the design process. By using exact measurements and tolerances, CAD tools significantly reduce the risk of errors. For example, in the creation of molds for injection molding, precise CAD models ensure that every detail is captured accurately, which is crucial for maintaining quality and consistency across numerous production runs. Moreover, CAD software allows for standardized models, which promote uniformity and quality assurance throughout the product design cycle. Early detection of potential issues in CAD simulations can prevent costly mistakes in the manufacturing stage, effectively minimizing waste and ensuring higher quality outcomes.
Efficient Prototype Development and Rapid Iteration
The capabilities of CAD modeling facilitate rapid prototyping, allowing designs to move swiftly from concept to reality. This efficiency is especially beneficial for industries where quick iterations based on feedback can make a significant difference in meeting project timelines and client expectations. The flexibility of CAD systems enables engineers to easily modify designs, which, coupled with virtual testing environments, reduces the need for multiple physical prototypes. The result is substantial cost savings and a faster design-to-production timeline, allowing businesses to adapt swiftly to changes and innovate continuously.
Customization Capabilities for Unique Product Specifications
One of the standout features of CAD modeling is its ability to support customization. By leveraging advanced CAD techniques, designers can create tailored solutions that meet specific client needs and preferences. The software’s capacity to handle intricate and complex geometries allows for the production of designs that were previously challenging or impossible to achieve with traditional methods. This adaptability ensures that products not only meet but exceed client expectations, showcasing the industry’s ability to cater to a diverse range of specifications and market demands.
Use of Virtual Reality and Augmented Reality in Enhancing CAD Design Visualizations
The integration of Virtual Reality (VR) and Augmented Reality (AR) with CAD modeling brings an additional layer of depth to the design process. These technologies enhance visualization by providing immersive environments where designers and stakeholders can explore spatial relationships and make informed decisions based on real-time interactions with the digital models. This capability not only enriches collaborative design reviews, allowing teams to work together regardless of their physical locations, but also accelerates the decision-making process, fostering more effective and efficient project management. This integration propels CAD modeling into a new realm of interactive design, aligning with modern needs for innovative and responsive product development.
Benefits of CAD Modeling in Injection Molding Design
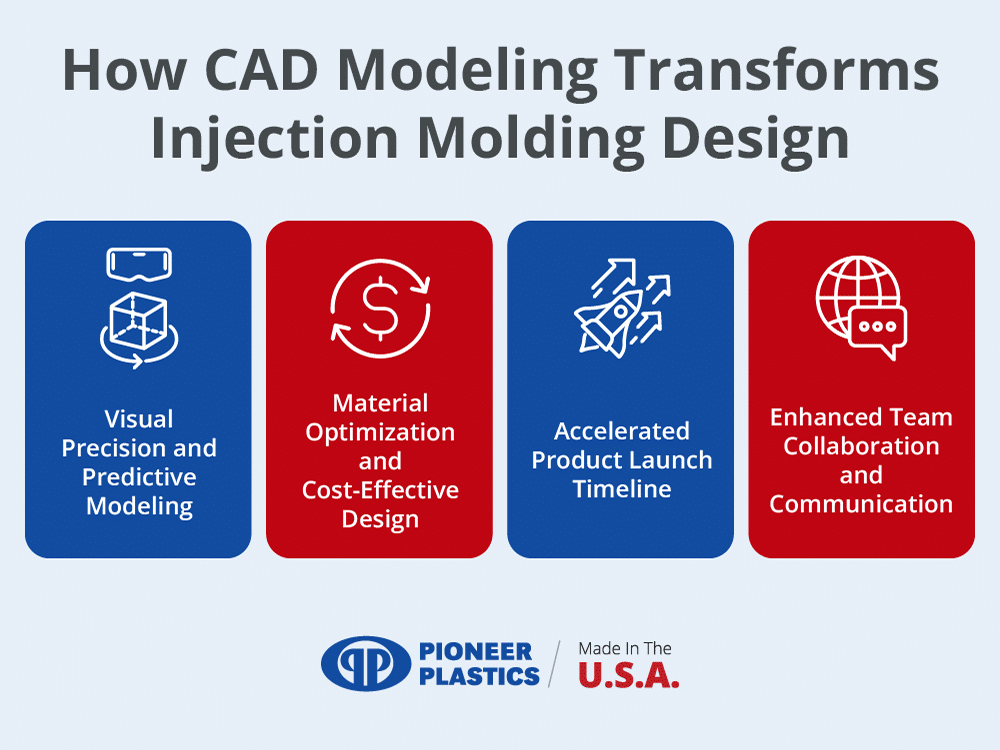
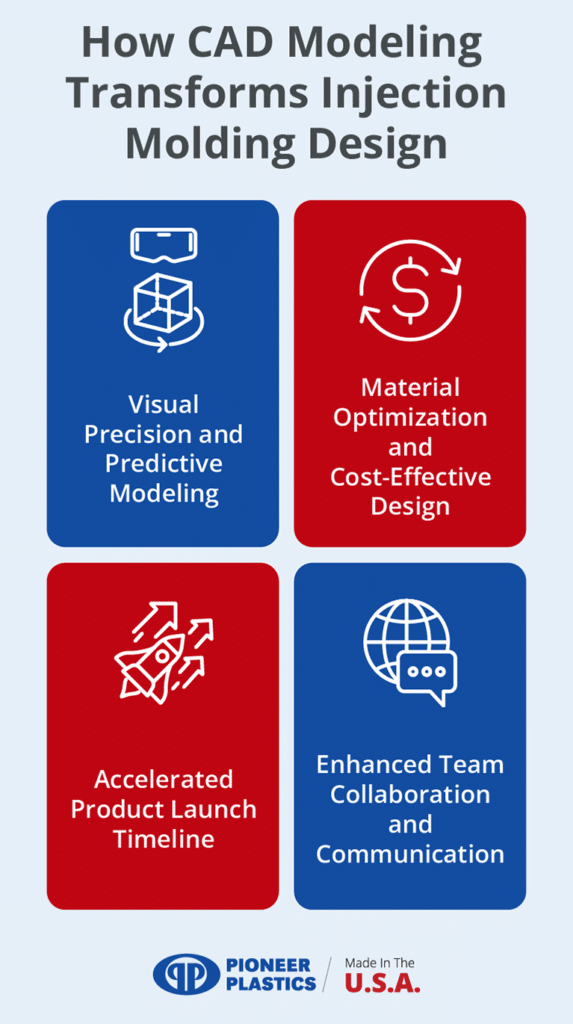
CAD modeling significantly enhances the injection molding process through:
Enhanced Visualization and Simulation Before Production
- Mold Flow Analysis: Predict how molten plastic will fill the mold.
- Warpage and Shrinkage Prediction: Adjust designs to compensate for material behavior.
- Material Selection: Simulate different materials to find the optimal choice.
Reduction of Material Waste and Cost Efficiency
- Optimized Runners and Gates: Design efficient paths for material flow.
- Thickness Uniformity: Ensure consistent wall thickness to reduce defects.
- Cycle Time Reduction: Optimize designs for faster production cycles.
Faster Time-to-Market for New Products
- Streamlined Design Process: Accelerate development stages from concept to production.
- Concurrent Engineering: Allow multiple teams to work on different aspects simultaneously.
- Quick Adjustments: Implement changes rapidly in response to market feedback.
Collaboration and Communication Improvements Between Teams
- Unified Design Platform: Share models easily among engineers, designers, and clients.
- Real-Time Updates: Keep all stakeholders informed of the latest changes.
- Documentation: Maintain clear records of design iterations and decisions.
Pioneer Plastics’ Expertise in Utilizing CAD for Superior Design and Manufacturing
Our team at Pioneer Plastics leverages CAD modeling to:
- Deliver high-quality, custom plastic parts that meet exact specifications.
- Provide expert guidance throughout the design process.
- Ensure efficient and cost-effective manufacturing solutions.
Insight into Sustainable Product Design and Material Savings
- Eco-Friendly Materials: Use CAD to plan for recyclable or biodegradable plastics.
- Design for Disassembly: Facilitate easier recycling and maintenance.
- Resource Optimization: Minimize material usage without compromising integrity.
Integrating sustainability within CAD modeling helps minimize environmental impact while enhancing product performance—a pivotal factor in modern design strategies.
By focusing on sustainable design practices, Pioneer Plastics not only reduces environmental impact but also enhances the economic viability of its products. CAD modeling plays a critical role in achieving these sustainability goals by enabling precise material calculations and efficient design strategies that conserve resources.
Harnessing CAD to Revolutionize Product Design
CAD modeling stands at the forefront of modern product design and manufacturing, especially in the plastic injection molding industry. Its ability to enhance accuracy, reduce errors, and streamline processes makes it an indispensable tool for engineers, designers, and manufacturers aiming to optimize their product design process.
At Pioneer Plastics, we harness the power of CAD modeling to transform ideas into tangible, high-quality products. Our expertise ensures that every design is optimized for performance, manufacturability, and sustainability.
Ready to take your product design to the next level? Contact Pioneer Plastics today to discover how our advanced CAD modeling services can bring your vision to life with precision and efficiency.