Are you struggling with getting plastic replacement parts from your supplier? Short run plastic production could be the game-changer you’ve been searching for. By embracing this innovative approach, you can boost your manufacturing efficiency, reduce costs, and respond swiftly to market demands. Let’s explore how smart short run plastic production can transform your appliance business.
Understanding Short Run Plastic Production for Appliance Manufacturers
In the competitive world of appliance manufacturing, staying agile is essential. Short run plastic production refers to the manufacturing of small quantities of plastic parts, typically ranging from a few hundred to a few thousand units. This method is particularly beneficial when you need flexibility, quick turnarounds, and high-quality outputs without the commitment of large-scale production.
The Relevance to Your Appliance Business
As an appliance manufacturer, you may often face challenges like managing inventory, dealing with design changes, and meeting fluctuating market demands. Short run plastic production allows you to produce the exact number of plastic replacement parts you need, minimizing waste and reducing storage costs.
Common manufacturing hurdles that short run production can help with includes:
- Inventory Overload: Keeping a large stockpile of every possible replacement part ties up capital and storage space.
- Design Evolution: Appliances frequently undergo updates, rendering old parts obsolete.
- Unpredictable Demand: It’s challenging to forecast precisely how many replacement parts will be needed at any given time.
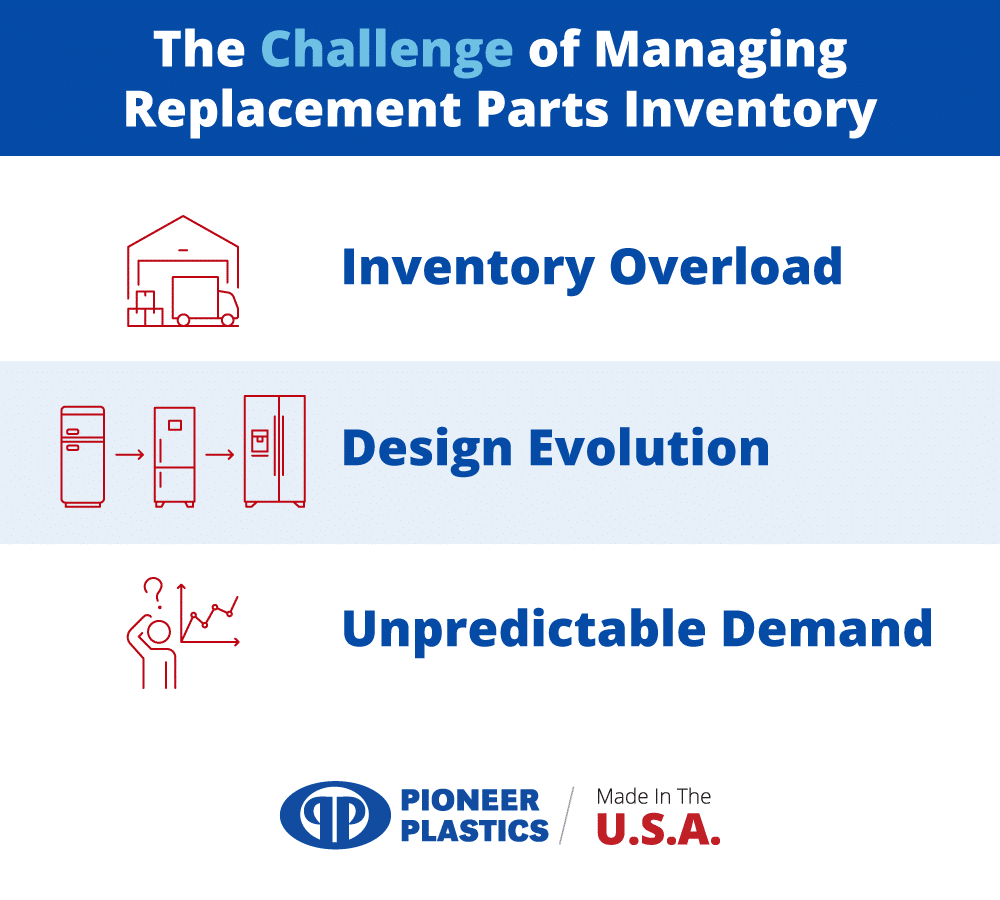
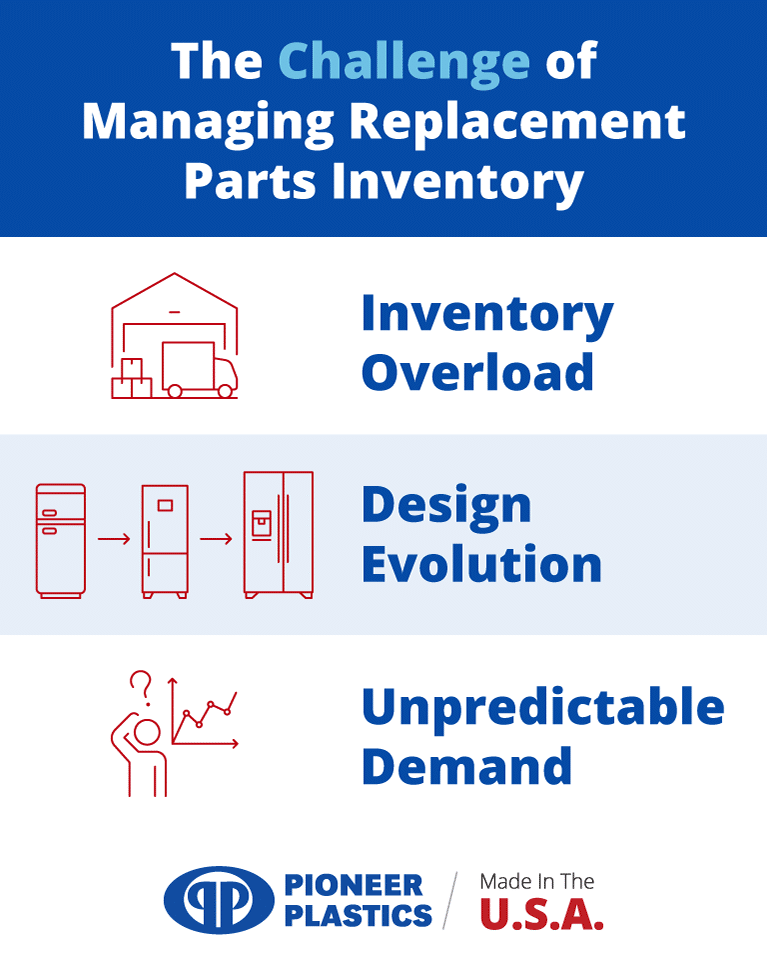
By adopting short run plastic production, you can navigate these issues with ease, ensuring you have the right parts at the right time.
Pioneer Plastics excels in the short run injection molding process by providing seamless retrieval, rapid mold changes, and expert mold management. Their advanced mold retrieval system ensures that all molds are easily accessible, minimizing downtime and maximizing productivity.
Quick mold changes are facilitated through state-of-the-art equipment and efficient protocols, allowing for swift transitions and reducing overall manufacturing lead times. Additionally, their team of experienced professionals manages the molds meticulously, ensuring optimal performance and longevity. These capabilities collectively make Pioneer Plastics a leader in short run injection molding, helping manufacturers stay agile and responsive to market needs.
The Benefits of Short Run Plastic Injection Molding
Short run plastic injection molding offers a multitude of advantages for your manufacturing process.
Rapid Turnaround Times
Time is money in the appliance industry. With short run production, lead times are significantly reduced. You can move to finished product swiftly, allowing you to meet tight deadlines and respond to urgent replacement part needs. Our streamlined operations enable quick mold changes and setup adjustments. This efficiency is crucial for short run plastic production, allowing you to pivot as needed.
Rapid turnaround times in short run production for the appliance industry are achieved through molds that are designed and prototyped or 3D printed, and then utilized over and over. Lean manufacturing principles and responsive supply chain management further streamline production, while automated quality control ensures swift validation of parts. These combined strategies allow companies to move quickly to finished product, meeting tight deadlines and responding promptly to urgent replacement part needs.
Reduced Inventory Costs
By manufacturing only what you require, you cut down on excess inventory and associated storage costs. This lean approach also reduces the risk of holding obsolete or unsold parts.
Unmatched Flexibility
At Pioneer Plastics, we understand that delays can be costly. That’s why we’ve optimized our processes to offer rapid turnaround times without compromising quality.
Handling Complex Projects with Ease
No project is too complex for us. We employ state-of-the-art equipment and technology and a skilled team to manage:
- Multiple Short Runs: Handling various projects simultaneously.
- Urgent Requests: Adjusting schedules to meet tight deadlines.
- Custom Requirements: Tailoring solutions to your specific needs.
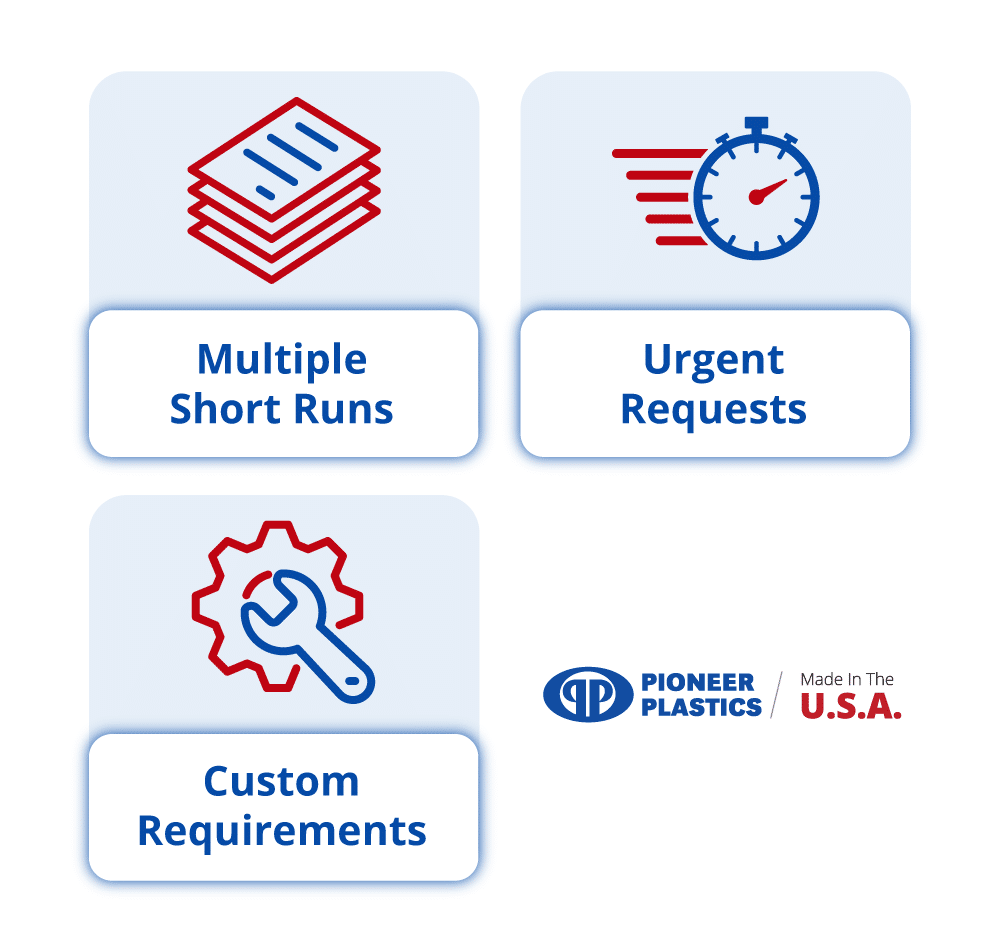
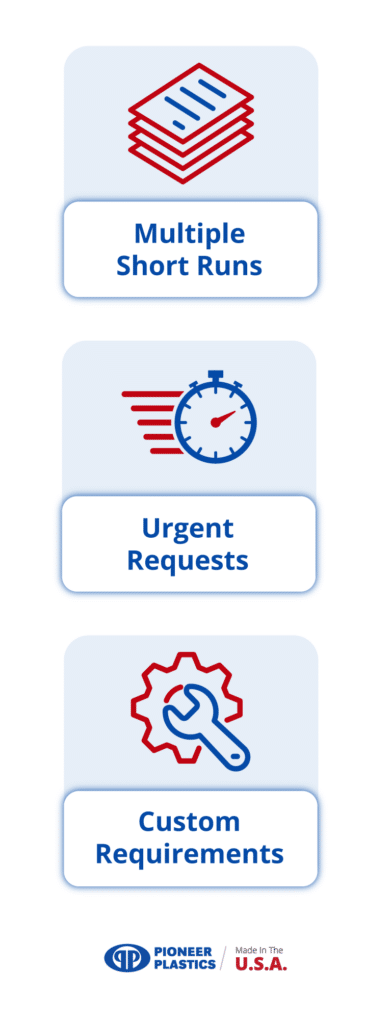
Custom Solutions for Diverse Appliance Needs
We cater to a wide range of appliance manufacturers, providing custom solutions that align with your unique requirements. We produce plastic replacement parts for washing machines, refrigerators, ovens, dishwashers, industrial machinery, and more. Replacement parts may include:
- Housing Components: Durable casings and enclosures.
- Functional Elements: Gears, clips, handles, and more.
- Aesthetic Features: Knobs, buttons, and panels with customizable designs.
Whether you manufacture kitchen appliances, HVAC systems, or industrial equipment, we have the expertise to deliver the parts you need.
Pioneer Plastics: Your Partner in Short Run Plastic Production
With over 40 years of industry experience, Pioneer Plastics is uniquely positioned to help you capitalize on short run plastic production.
Expertise in Custom Injection Molding
We transform your concepts into market-ready products through our custom injection molding services. Our mold management capabilities allow us to be a strategic partner whether it’s managing the tool development or managing your existing mold.
Providing Engineering Services and Product Design Guidance
Our experts provide invaluable guidance throughout the product design process. We work with high-quality plastics ensuring your parts are durable and reliable.
Commitment to Quality You Can Trust
Quality isn’t just a buzzword for us—it’s a promise. We adhere to ISO 9001:2015 certification standards, implementing rigorous quality control measures to guarantee that every product meets your exact specifications.
Unparalleled Customer Service
At Pioneer Plastics, your success is our success. We provide personalized service, ensuring we understand your needs and exceed your expectations. Our team prioritizes open communication through regular updates, feedback loops and a consultative approach.
The Benefits of Experience
With decades of experience, we offer:
- Expert Guidance: Assisting you from concept to completion.
- Quality Assurance: Delivering products that meet rigorous quality standards.
- Operational Efficiency: Streamlining processes to save you time and money.
Unlock Success with Short Run Plastic Production
Don’t let outdated production methods hold you back. Short run plastic production offers you a smart, efficient way to meet your manufacturing needs. By partnering with Pioneer Plastics, you gain access to unparalleled expertise, quality, and customer service.
Take control of your manufacturing process today. Contact Pioneer Plastics to discover how our smart short run plastic production solutions can boost your appliance business to new heights.