The custom injection molding process starts with a conceptualized design and ends with a uniquely manufactured product.
If your product needs to be aesthetically pleasing or ergonomically friendly, injection molding techniques like insert molding or overmolding might be used to achieve those needs.
It might be difficult to figure out which process is best for your custom plastic part. Here’s a break down of the insert molding and overmolding processes.
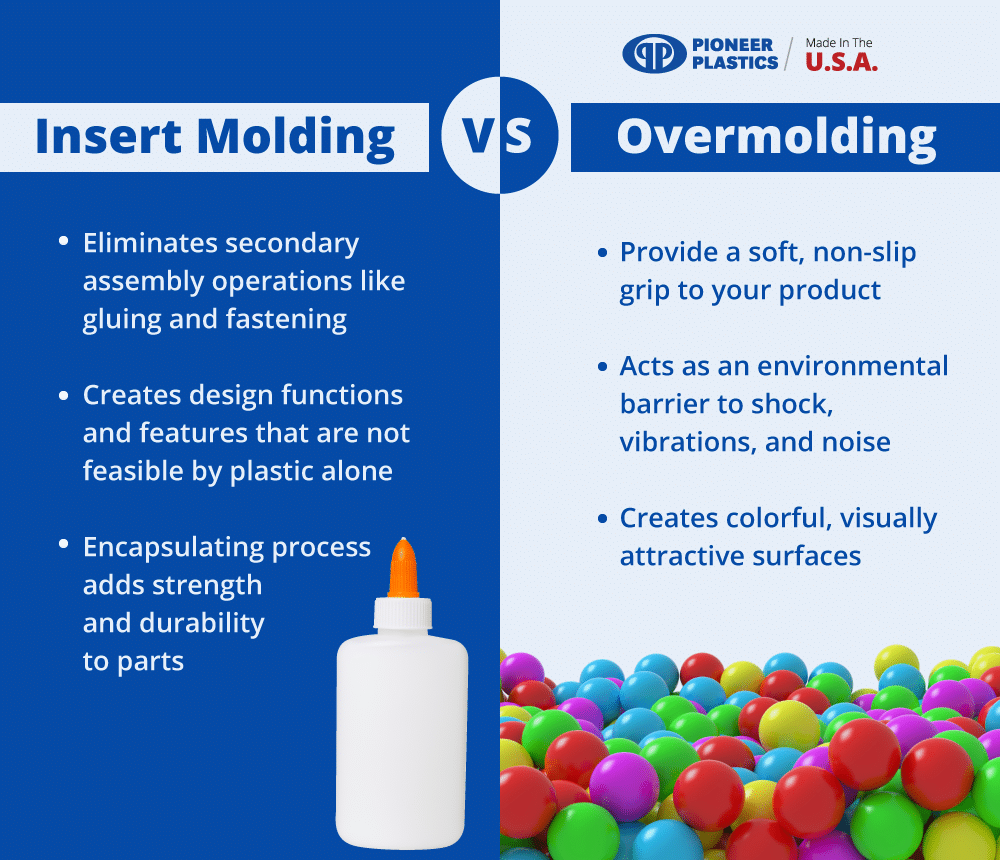
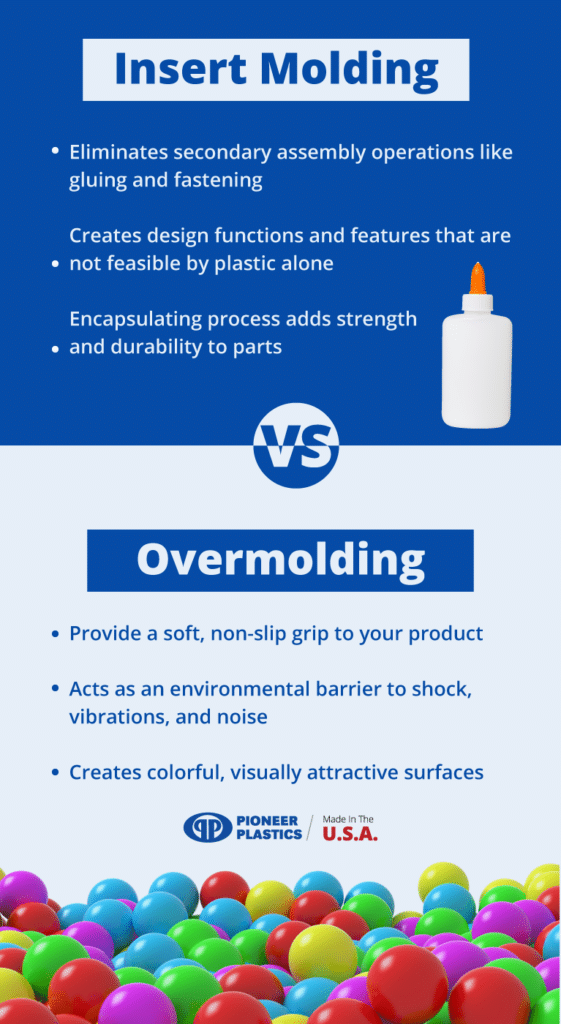
Insert Molding
Insert molding is a process where a rigid plastic resin is injected over another material, typically metal. The metal piece is placed in a tool for the plastic to be injected around. Encapsulating the insert with plastic creates a single molded piece that’s typically stronger than one created by assembling separate pieces together.
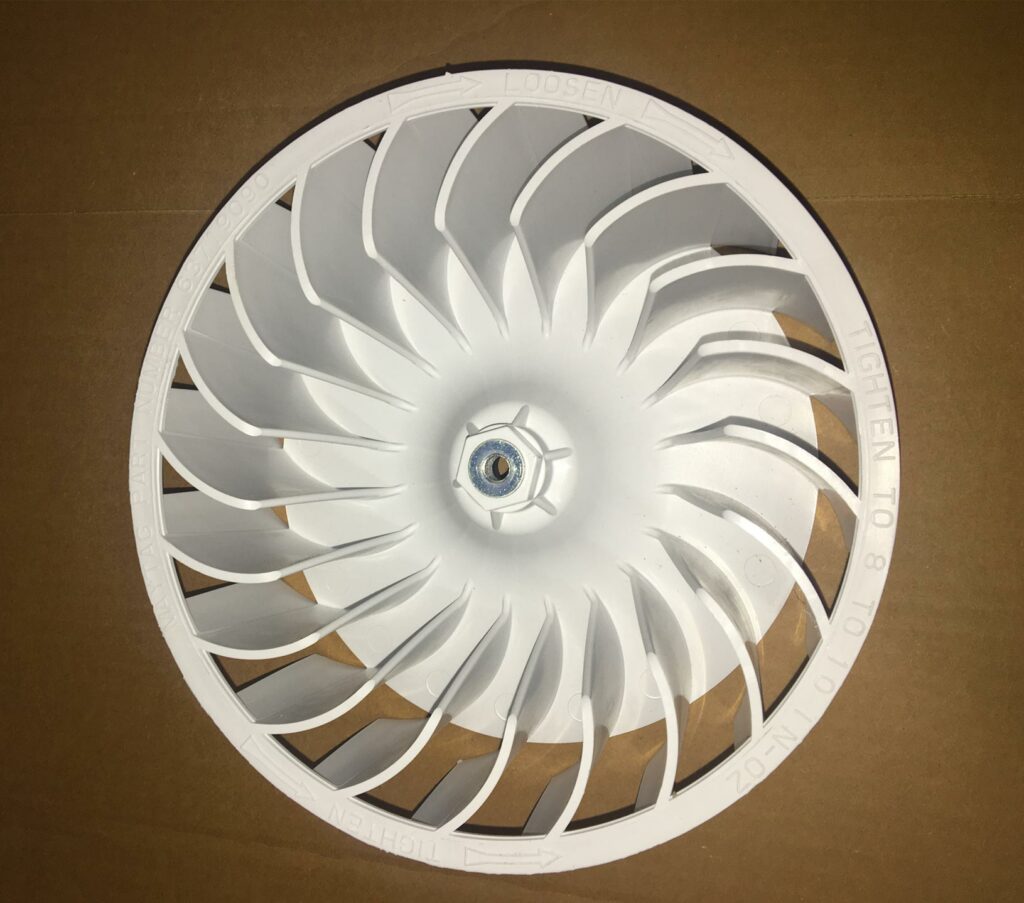
This process is most commonly used for custom-machined metal parts like threaded fasteners and electrical parts. There is no chemical bonding between metal inserts and plastic, so the insert and resin components must be designed for mechanical bonding.
Insert molding is controllable and allows better encapsulation than other methods used to mold plastic around metal parts. Molded inserts eliminate the need for a secondary insert installation process, making it more time-and-cost-efficient.
Benefits of Insert Molding:
- Eliminates secondary assembly operations like gluing and fastening.
- Creates design functions and features that are not feasible by plastic alone.
- The encapsulating process can add strength and durability to parts.
Overmolding
Overmolding is the process of adding an additional layer of resin to the existing plastic part. This process adds characteristics that a single piece of plastic can’t provide.
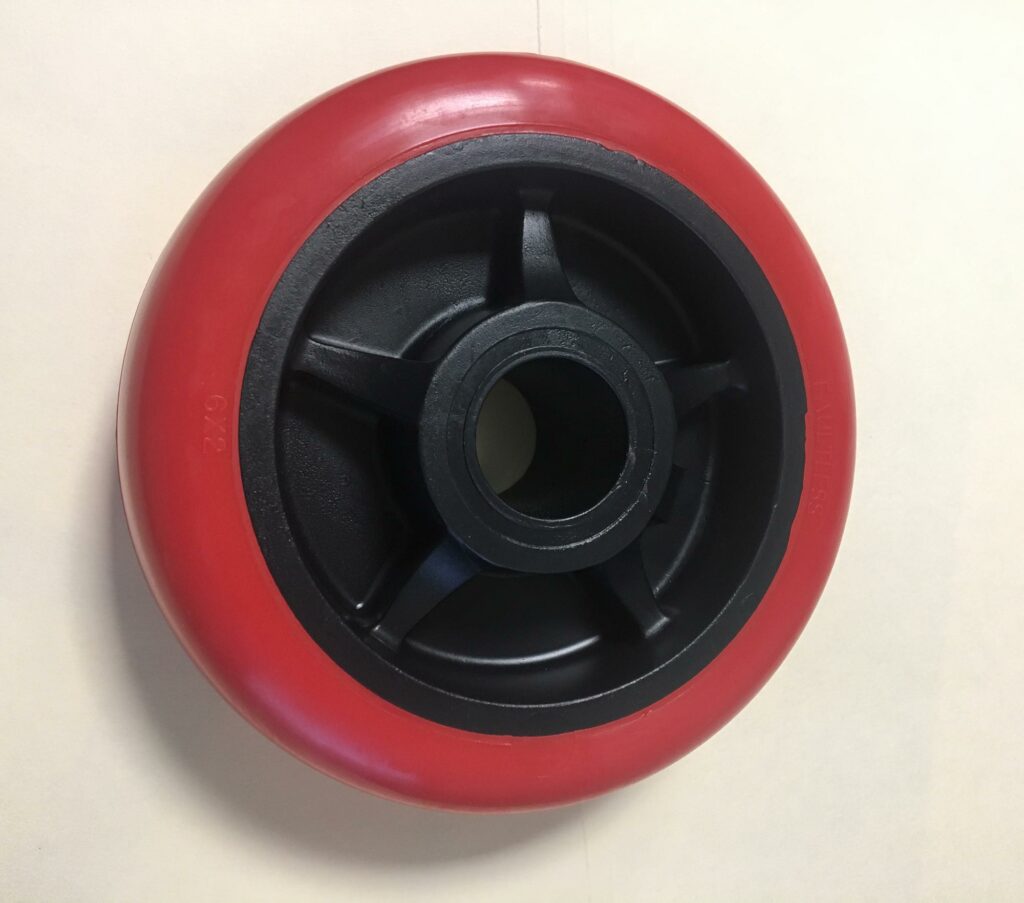
One common reason to use this technique is to add a soft, functional, ergonomic layer of rubber-like material (typically a thermoplastic elastomer) over a hard surface. This improves the grip of a hand-held item.
One example of this is toothbrushes. Toothbrushes are often made from a hard plastic center with a soft plastic grip around the handle.
Another use for over-molding is to change or enhance the appearance of a part by overmolding material of a different color or finish.
There are two primary methods of overmolding:
- Two-shot molding uses a single production mold.
- Pick-n-place molding uses two production molds where an entire batch of parts are molded. Then, they are manually placed into a second mold where the overmold resin is injected to produce the completed parts.
Thousands of possible combinations exist for over-molded material. Resins have to be adhesive and compatible with each other in order for the process to work.
If the goal of using overmolding is to enhance grip or increase cushioning in your product, make sure your injection molding company knows those goals. Factors like cushioning, flexibility, and friction will play into the type of resins that are used in the product.
Benefits of Overmolding:
- It can provide a soft, non-slip grip to your product.
- It acts as an environmental barrier to shock, vibrations, and noise.
- It creates colorful, visually attractive surfaces.
- It reduces the number of secondary steps and costs associated with them, in turn reducing the complexity of assembly.
- It can provide adhesion between different materials and eliminate the need to assemble different materials by hand.
Why Choose Pioneer Plastics?
We specialize in all aspects of the process- from concept to consumer. We can design, build, produce, and distribute your part. From insert molding to overmolding and so much more, we can help you produce your custom plastic part.
Contact us today to get a quote for the production of your part.