Reshoring manufacturing—moving production back to the United States—has emerged as a crucial strategy for reducing operational vulnerabilities, enhancing product quality, and meeting the demand for American-made goods. Global disruptions in recent years have prompted manufacturers to reconsider the stability and advantages of domestic production. Beyond cost considerations, reshoring also helps businesses secure supply chain control, shrink time-to-market, and meet consumer expectations for transparency.
This article explores the key benefits of reshoring manufacturing, including job creation, quality improvements, and supply chain resilience. We’ll also address common challenges, such as workforce training and the initial expenses needed to modernize infrastructure. Whether you aim to safeguard your operations, deliver top-notch products, or support local communities, reshoring provides a transformative path to long-term success.
Key Advantages of Reshoring Manufacturing to the United States
Reshoring manufacturing offers strategic benefits that go far beyond simple price comparisons. By bringing production stateside, companies can ensure quality, strengthen operations, and fulfill growing consumer expectations for reliable, US-made products. Below are some of the most compelling advantages.
Boosting Local Job Creation
Reshoring bolsters local communities by generating employment across skill levels, fueling sustained regional growth:
- Skilled Job Opportunities: Domestic manufacturing expands roles in engineering, tool building, and advanced machinery, enhancing the local talent pool. For instance, engineering services benefit directly from such growth.
- Entry-Level Positions: Return of assembly, packaging, and quality control roles offers stable wages for workers with limited previous experience.
Beyond contributing to workforce development, reshoring can lead to revitalized local economies by increasing consumer spending power and encouraging further business investment.
Mitigating Supply Chain Risks
Relying on manufacturing overseas often exposes companies to geopolitical tensions, trade barriers, and logistical slowdowns. Reshoring relieves these vulnerabilities by simplifying and localizing production:
- Reduced Shipping Complexities: While shorter routes can minimize transportation costs and reduce exposure to port delays, the actual impact varies based on operational and environmental factors.
- Lower Global Disruption Exposure: Domestic operations lessen the impact of international trade conflicts and regulatory upheavals.
- Smarter Coordination: Proximity fosters better collaboration between product design, production, and quality assurance teams.
By relocating manufacturing closer to home, companies enjoy greater stability, responsiveness, and control throughout the production process.
Enhancing Quality Control and Reliability
When your manufacturing is domestic, you have tighter oversight and can ensure meticulous quality monitoring:
- Robust Regulatory Standards: US-based operations comply with strict manufacturing regulations, improving safety and reliability.
- Faster Design Modifications: Adapt or refine products more swiftly without the time lags tied to overseas communication.
- Protection of Intellectual Property: Producing closer to headquarters mitigates IP theft and reduces the risk of counterfeiting.
Proactive quality management can lower defect rates and boost brand credibility, creating trust among consumers that expect American-made excellence.
Achieving Cost Competitiveness
Though labor costs may be higher in the US, hidden expenses can accompany outsourcing abroad. Reshoring uncovers savings and efficiencies that could tip the balance:
- Avoiding Hidden Costs: Domestic production helps companies sidestep additional fees like import duties.
- Reduced Error Rates: Close monitoring puts a lid on product defects, minimizing costly returns or remakes.
- Stable Financial Forecasting: For many businesses, US-based expenses remain relatively predictable, reducing the likelihood of unexpected fluctuations; however, this predictability may not extend to all income levels or in times of economic upheaval.
Weighing the total cost of ownership—logistics, quality, and potential geopolitical shifts—shows how reshoring can align cost and sustainability for many manufacturers.
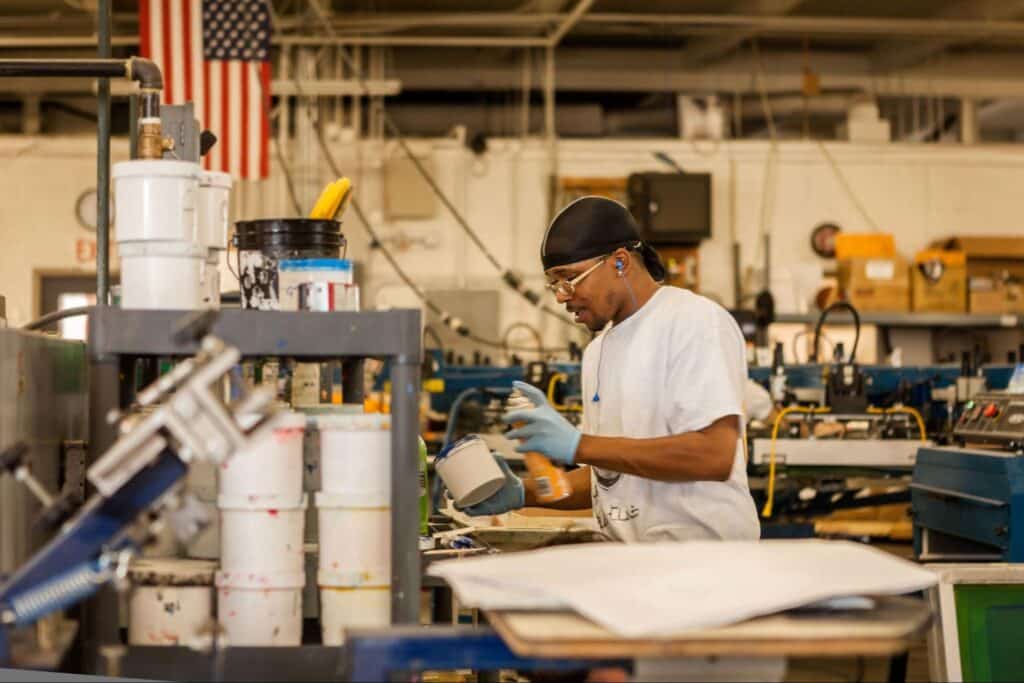
Strengthening Local Economies Through Reshoring Manufacturing
Reshoring is more than a corporate strategy; it’s a potent engine for local economic growth. By revitalizing manufacturing operations at home, businesses invigorate the broader community, supporting both regional industries and public services.
Stimulating Local Businesses and Industries
Reshoring often triggers increased demand for regional suppliers, raw materials, and creative partnerships:
- Boosting Ancillary Services: Domestic production spurs growth in machining, packaging, and transportation within the same locale.
- Encouraging Collaboration: Close proximity encourages manufacturers to collaborate, exchange ideas, and innovate collectively.
Driving Innovation and Workforce Development
To keep pace with advanced manufacturing methods, companies collaborate with educational institutions to nurture talent:
- Tailored Training Programs: Aligning with community colleges and trade schools helps cultivate a specialized, skilled workforce.
- Structured Apprenticeships: Business-sponsored apprenticeships allow hands-on learning for emerging engineers and technicians.
- Diversity in Hiring: Broadening recruitment assists in filling critical roles while promoting inclusive opportunities.
Empowering Community Transformation
Reshoring’s broader societal contributions include higher tax revenues for infrastructure, enhanced community services, and general economic uplift. As manufacturing rebounds, communities reclaim their proud industrial heritage, forging a resilient future less reliant on global volatility.
Pioneer Plastics: A Reshoring Success Story
A prime illustration of reshoring’s potential can be found in Pioneer Plastics, based in Dixon, KY. With over 40 years of industry experience, Pioneer Plastics exemplifies how domestic manufacturing creates both customer and community value:
- Decades of US Production: Their long-standing commitment to manufacturing in the United States ensures local job creation and supports economic vitality.
- Rapid Lead Times: Pioneer Plastics’ in-house tool building and engineering services expedite design modifications and ensure quicker time-to-market, a hallmark benefit of reshoring.
- Wide-Ranging Capabilities: From custom injection molding to proprietary products like collectible display cases and clear containers, they cater to short-run and long-run production demands.
- High-Quality Assurance: Maintaining every step of production in the US helps Pioneer Plastics oversee quality control and product consistency more effectively than if outsourced abroad.
Equally important, Pioneer Plastics has forged strong partnerships with local suppliers and educational institutions, fostering skill development and career growth for community members. By training new professionals in engineering-grade plastics and offering production services under one roof, they streamline the path from concept to completion. These collaborative efforts not only boost the company’s capacity but also reinforce the local workforce, showcasing how reshoring can drive sustained development and industry leadership.
Ensuring Sustainability and Environmental Responsibility
Reshoring can also contribute to environmental benefits by reducing transportation emissions and potentially improving adherence to eco-friendly manufacturing practices:
Reducing Carbon Emissions and Energy Consumption
Producing goods closer to consumption points can help decrease transportation emissions and fossil fuel consumption:
- Less Long-Distance Freight: Shorter routes can lead to measurable cuts in carbon emissions.
- Streamlined Logistics: Shorter distances encourage more efficient, localized transportation networks.
Supporting Sustainable Manufacturing Practices
Stricter US environmental standards can encourage greener manufacturing methods:
- Responsible Materials: Partnering with domestic, ethically focused suppliers reduces harm from unregulated resource extraction.
- Adoption of Green Processes: Local facilities are more likely to meet or exceed federal and state emissions guidelines.
Aligning with Consumer Demand for Eco-Conscious Products
A “Made in the USA” label resonates with buyers who value sustainability. It signals minimized shipping footprints, reliable labor standards, and better opportunities for companies to document their production processes in real time. However, the actual environmental benefits depend on the specific practices and regulatory standards implemented at the reshored facilities.
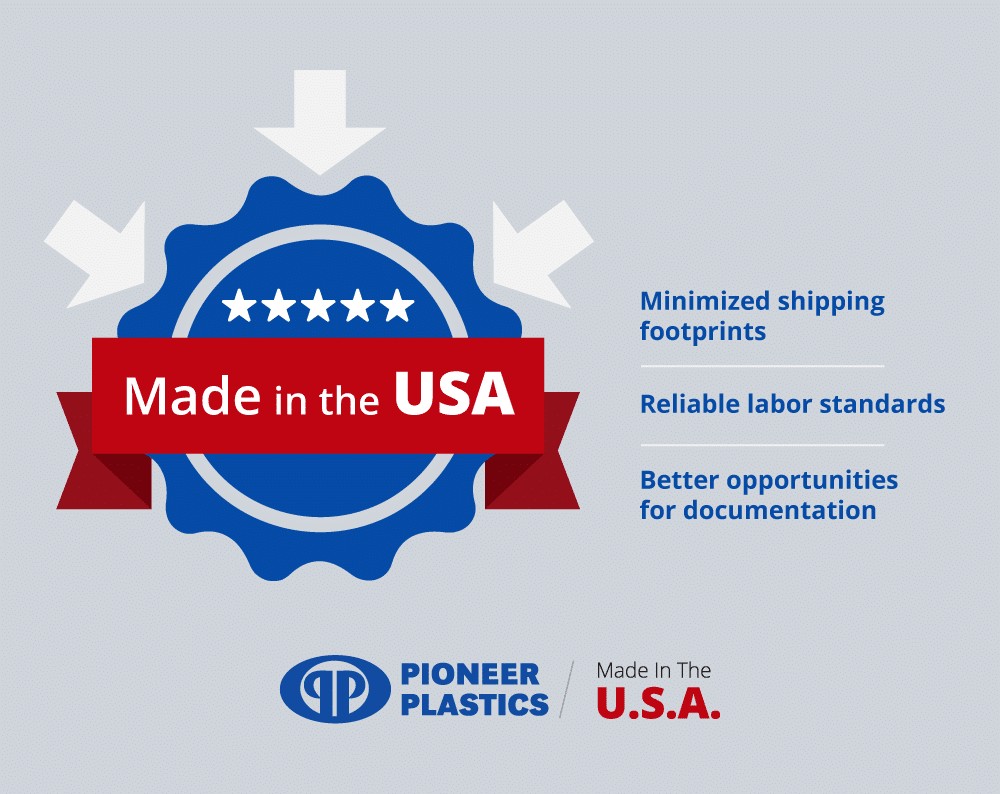
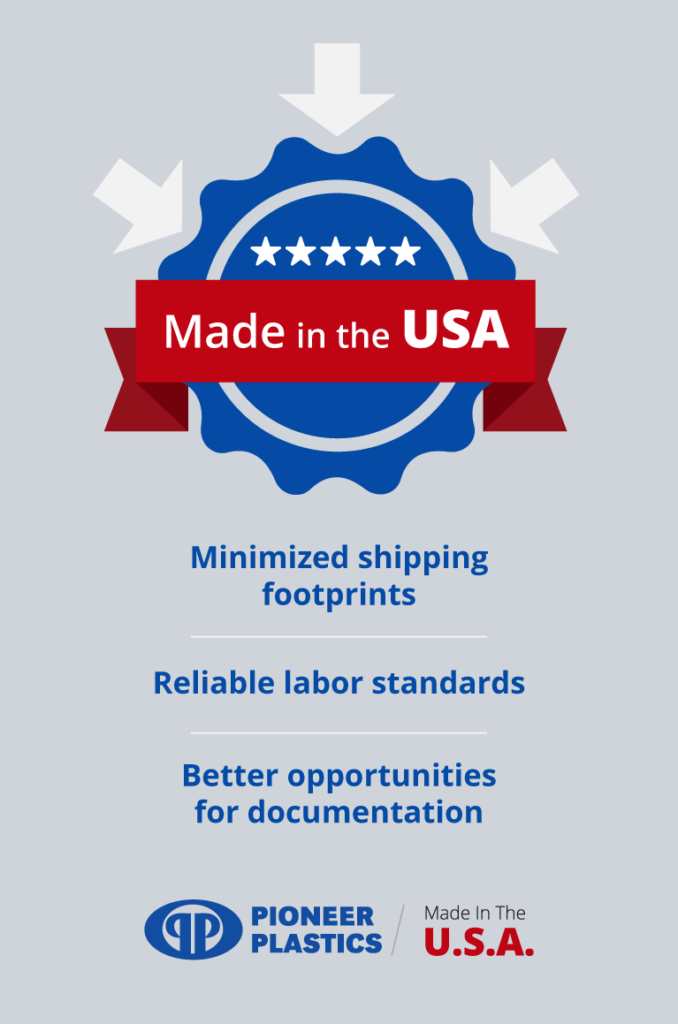
Overcoming Challenges in Reshoring
Despite its advantages, reshoring brings certain hurdles—particularly in labor costs and infrastructure investment. Yet, proactive measures can transform these challenges into growth opportunities.
Managing Higher Upfront Costs
Domestic production may entail immediate financial demands for wages, modernization, and automation. Strategic measures can offset these investments:
- Leveraging Advanced Technology: Automation tools streamline workflows and compensate for higher labor costs.
- Adopting Lean Manufacturing Practices: Methodical waste reduction cuts unnecessary overhead and optimizes daily operations.
- Tapping Incentives: Various state and federal programs offer grants or tax breaks to encourage US-based production.
Over time, fewer shipping disruptions, lower defect rates, and closer quality control can deliver long-term returns that make reshoring financially sound.
Bridging the Workforce Skills Gap
A shortage of skilled labor in certain areas may curtail manufacturing’s growth potential. Businesses can work with local educational entities to maintain a robust talent pipeline:
- Technical Collaborations: Partner with tech schools or colleges to develop skill-specific curriculum.
- Apprenticeship Programs: Allow hands-on learning, bridging theoretical knowledge and real-world manufacturing demands.
- Recruiting Diverse Candidates: Inclusive hiring strategies help recruit from untapped talent pools, alleviating chronic skill shortages.
Embracing Automation and Technological Advancements
To compete with global efficiencies, domestic manufacturers can harness state-of-the-art equipment:
- Robotics and AI Integration: Speed processes, cut down on errors, and lift overall productivity without inflating labor costs.
- Continuous Modernization: Regularly upgrading machinery supports precision, reliability, and heightened production volumes.
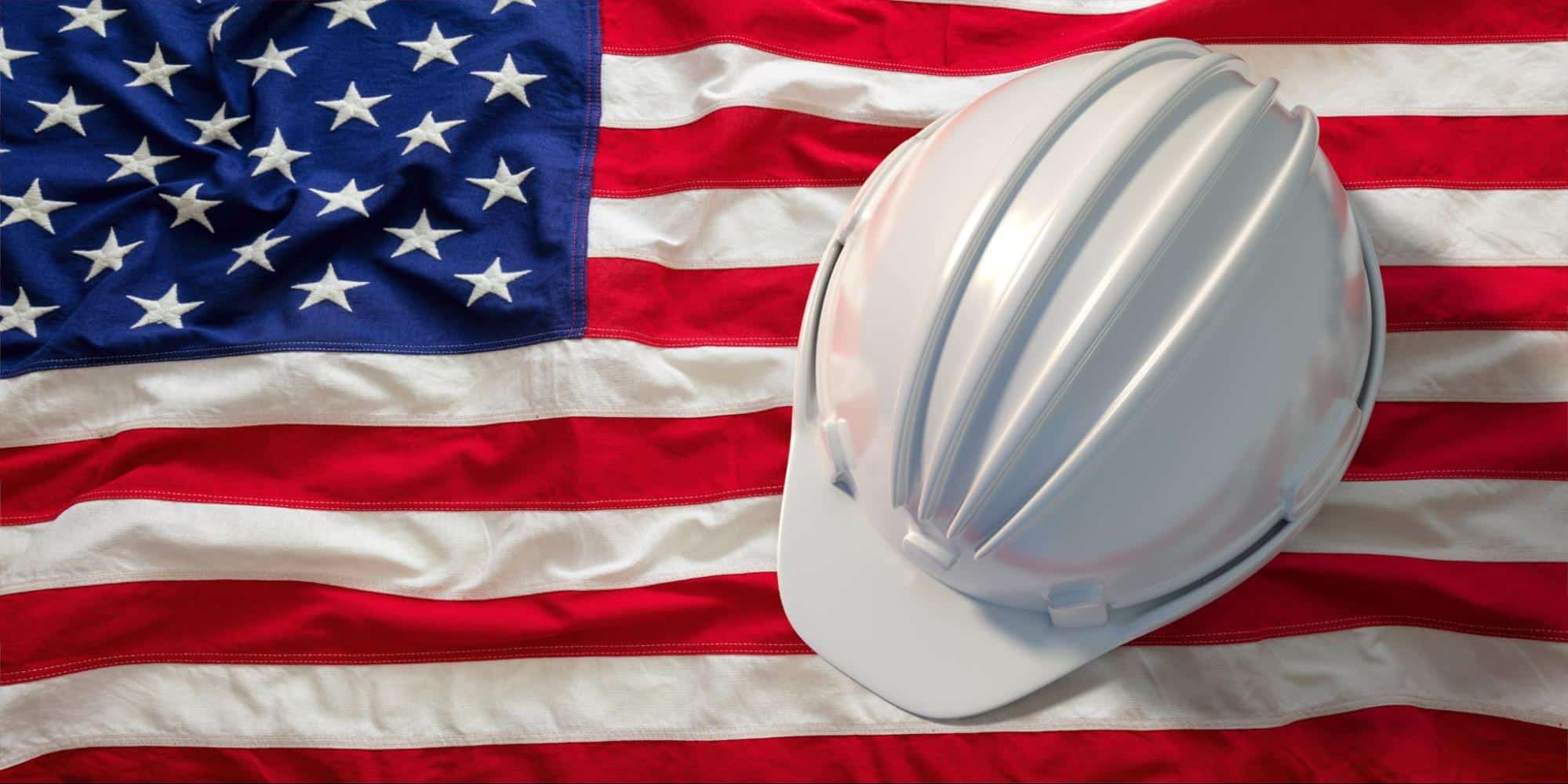
The Advantages of Reshoring Manufacturing
Reshoring manufacturing empowers businesses to minimize supply chain disruptions, improve product quality, and bring production closer to end users eager for transparency. Beyond mere cost comparison, it creates a resilient operational framework, enabling brands to remain competitive amid rapidly shifting markets.
Examining the hidden costs of offshoring—such as shipping delays, international trade barriers, and additional coordination complexities—makes a compelling case for relocating operations back home. Reshoring meets consumer demands for US-made reliability and supports the broader American economy, enabling businesses to flourish internally while benefiting local communities.
For companies looking to secure supply chain stability and deliver top-tier American products, reshoring stands as a powerful solution. By partnering with a seasoned domestic manufacturer equipped for custom injection molding and tool building, organizations can optimize production and capitalize on a thriving “Made in the USA” market.
Ready to start your journey? Contact us now to discover how reshoring can accelerate growth and reshape your manufacturing strategy.