“Made in USA” manufacturing signifies far more than a simple label—it represents a commitment to quality, local economic growth, and ethical production practices. At its core, it refers to goods primarily produced within the United States, where domestic facilities oversee critical aspects of product design, assembly, and labor.
For many, this designation is often associated with superior craftsmanship and dependability, reflecting values such as accountability, sustainability, and community investment. This perception underscores a commitment to high product quality and ethical practices, allowing businesses to differentiate themselves in competitive markets.
In today’s globalized economy, where products often cross multiple borders, reliance on overseas manufacturing has become commonplace. However, recent years have seen signs of a resurgence in American manufacturing, influenced by factors such as rising overseas labor costs, a growing consumer preference for responsibly sourced goods, and concerns over supply chain vulnerabilities. This shift underscores the importance of domestic production in delivering reliable solutions that align with modern consumer values.
“Made in USA” now spans a diverse range of industries—from food packaging and medical devices to custom injection molding products and collector-focused items. For businesses aiming to stand out, relying on American manufacturing highlights a dedication to high product quality and ethical practices.
The demand for domestically produced goods continues to grow. Consumers, increasingly conscious of their purchasing decisions, seek options promising shorter supply chains, more sustainable manufacturing, and higher ethical standards. Many buyers also associate U.S.-made goods with responsible production, positioning “Made in USA” as both an economic and values-based decision.
Throughout this article, we will explore the many benefits of purchasing products manufactured in America—advantages that go beyond reliability and into broader contributions for local economies and overall customer satisfaction.
The Historical and Economic Importance of “Made in USA” Products
Historically, during the 20th century, the “Made in USA” label was seen as a symbol of reliability and high standards, helping to build consumer trust domestically and abroad. American manufacturing has long been a significant driver of economic growth and innovation, powering advancements across automotive, aerospace, consumer goods, and advanced materials.
From early assembly line innovations in automotive plants to cutting-edge breakthroughs in materials engineering, U.S. factories have influenced global progress. For decades, “Made in USA” became synonymous with sturdy craftsmanship and dependable performance. This strong manufacturing base supported job creation for millions of Americans, strengthening local communities through stable wages and growth opportunities.
Despite challenges brought on by globalization and offshoring, local production is regaining momentum in part due to rising overseas labor costs and renewed awareness of supply chain vulnerabilities. Meanwhile, policymakers and industry leaders continue to explore ways to encourage domestic production and restore manufacturing activity.
Choosing American-made products contributes to local economic vitality and community development. The money spent on these goods circulates within regional economies, boosting employment and supporting small businesses. Whether through direct wages or secondary effects such as expanded retail and service opportunities, domestic manufacturing fosters a positive cycle of local growth and innovation. This economic benefit underscores why the nation’s manufacturing heritage remains critical to the broader U.S. economy.
Quality Assurance in American-Made Manufacturing
One hallmark of American manufacturing is a focus on thorough quality assurance. Stringent regulations promote product safety and environmental responsibility. These standards, alongside the use of advanced technologies, instill confidence that goods built on U.S. soil will meet industry-specific benchmarks. Businesses leveraging these advantages often reference specialized tools and software to maintain strict oversight of manufacturing quality.
Injection molding is an example of how U.S. factories pursue precision and reliability. Many domestic injection molding specialists invest in top-tier machinery and engineering-grade materials, ensuring that even complex or niche plastic components meet exact specifications. These producers place a premium on accountability, incorporating robust quality control measures throughout the production cycle so that any issues can be addressed swiftly.
Proximity further boosts this commitment to excellence. Closer geographic links between customers and production facilities shorten response times. If problems occur, teams can investigate and correct them immediately, avoiding long shipping delays or communication hurdles. On-site collaboration is more feasible, enabling rapid prototype adjustments and specialized refinements, which can be difficult to accomplish smoothly when working with overseas plants.
Finally, many American manufacturers employ seasoned craftspeople and legacy expertise that differentiates their work. Whether it’s a specialized plastic part or a more common household item, U.S. companies often operate with a blend of high-tech processes and personal care. That combination of advanced production protocols, strict regulatory frameworks, and skilled workmanship fortifies the reputation of domestic goods as trustworthy, durable, and consistent.
Supporting Local Job Creation and Economic Growth
One of the most powerful impacts of domestic manufacturing is job creation. American factories offer roles in production, engineering, logistics, and quality assurance, providing stable employment in many communities. While these positions contribute to economic stability, the specific levels of wages and their impact on financial security can vary by industry and location. Moreover, the economic ripple effect is substantial: manufacturing workers and their firms support local suppliers, restaurants, and other area businesses.
Financial contributions from manufacturing jobs multiply within surrounding regions. Employees spend income locally, funding everything from groceries to entertainment, generating a cycle of economic self-reliance and growth. In addition, manufacturers form partnerships with domestic shipping providers, technology services, and other vendors—further enriching the community. Concentrated areas of industrial activity can evolve into specialized manufacturing hubs, as explored by thought leadership on how U.S. manufacturing influences the future.
American manufacturers benefit from collaborations with regional educational institutions, from technical programs to universities. These efforts supply skilled workers versed in toolmaking, engineering, and machine operation. By offering training and professional development, manufacturing companies retain talent and continue fueling local economic initiatives.
Dixon, Kentucky, serves as an example of a community benefiting from diverse manufacturing services that help maintain stable job opportunities and support local salaries. By supporting U.S.-based industries, consumers and businesses alike invest in the scaffolding of local and national economies, helping entire communities thrive.
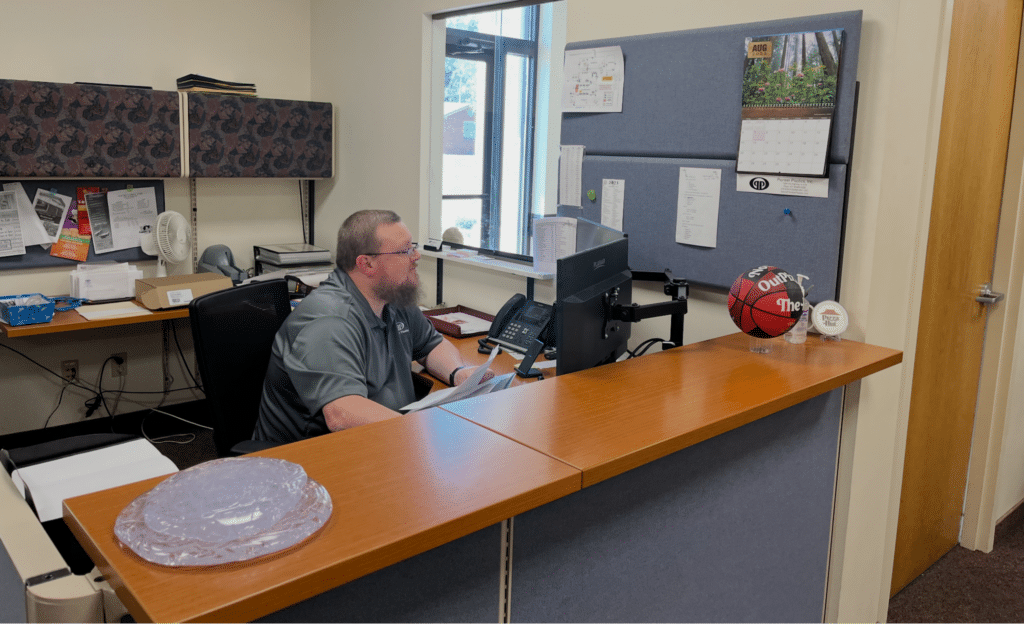
Advancing Ethical Manufacturing Practices
Ethical manufacturing involves treating workers fairly, minimizing environmental harm, and maintaining accountability throughout production. In the United States, manufacturers operate under labor laws designed to protect employee rights, promote fair wages, and sustain workplace safety. Although compliance can vary, these guidelines promote transparency and ethical practices, though their effectiveness compared to international standards can depend on specific regulations and contexts.
Purchasing “Made in USA” products often reassures buyers that these products come from regulated environments. Such environments typically mandate ethical labor policies and uphold community and environmental standards. Many U.S. manufacturers also emphasize equitable opportunities, providing pathways for skill advancement and investing in worker well-being.
In a marketplace where customers carefully weigh the social and ethical impacts of their purchasing decisions, a transparent and socially responsible supply chain can be a potent differentiator. For businesses, ethical manufacturing helps build deeper trust with customers who value social responsibility. For individual buyers, it ensures their purchases align with personal ideals of sustainability, fairness, and community well-being.
Environmental Benefits of Domestic Manufacturing
Environmental responsibility is a further component of ethical production. Strict regulations on emissions, waste disposal, and resource management help protect natural ecosystems. Factories may adopt methods like recycling production waste or improving energy efficiency to lessen their ecological footprint. Going beyond compliance, an increasing number of manufacturers proactively pursue sustainable initiatives.
Compared to extended global supply chains, domestic manufacturing typically helps reduce carbon footprints. Producing and distributing goods locally cuts down on fuel-intensive overseas shipping, lowering overall greenhouse gas emissions. Reduced transit also shortens lead times, an added benefit for businesses seeking timely product turnarounds.
Regulations play a crucial role: U.S. manufacturers must meet federal and state environmental standards. These guidelines require responsible waste disposal, proper chemical handling, and verified emissions controls. As a result, many facilities pursue energy-efficient strategies, invest in greener technology, or implement recycling initiatives to reduce landfill contributions.
Many American producers continuously adopt eco-friendly innovations to reduce environmental impact further. Examples include switching to renewable energy sources, using recycled plastics or biodegradable materials, and employing modern equipment that cuts down on energy consumption. These efforts allow manufacturers to limit carbon emissions while still maintaining high-volume or specialized production.
Shorter supply chains also invite simpler packaging solutions and localized distribution options, thereby shrinking waste streams. Taken together, these combined efforts demonstrate that choosing U.S.-made products can help address ecological concerns at a regional level while contributing to global sustainability goals.
The Advantage of Shorter Lead Times and Better Customer Service
Modern markets reward responsiveness, speed, and flexibility. Domestic manufacturing provides shorter lead times that help businesses bring products to market quickly or adjust to shifting consumer demands. Rather than navigating lengthy import procedures, local manufacturers deliver finished goods through faster shipping methods, reducing potential holdups.
In the United States, direct interactions between client teams and production engineers are often easier to coordinate. Face-to-face visits can expedite prototype reviews, design changes, or product tweaks. Operating in the same or similar time zones cuts communication lag, protecting businesses from the logistical gridlock that sometimes accompanies overseas collaborations.
Domestic manufacturing also handles production volume changes more fluidly. Facilities can pivot between short-run and large-scale orders without complex new agreements or burdensome shipping constraints. This adaptive model benefits clients with seasonal demands or those uncertain about how quickly a product might scale. Moreover, real-time collaboration fosters transparent problem-solving if design issues come up.
Since local producers operate under the same legal and business framework, they often offer more direct accountability. If something goes wrong, it’s straightforward to rectify the issue by scheduling a call or even an on-site meeting. This close feedback loop bolsters customer satisfaction and prevents small setbacks from escalating.
Delivering High-Quality Proprietary and Custom Plastic Products
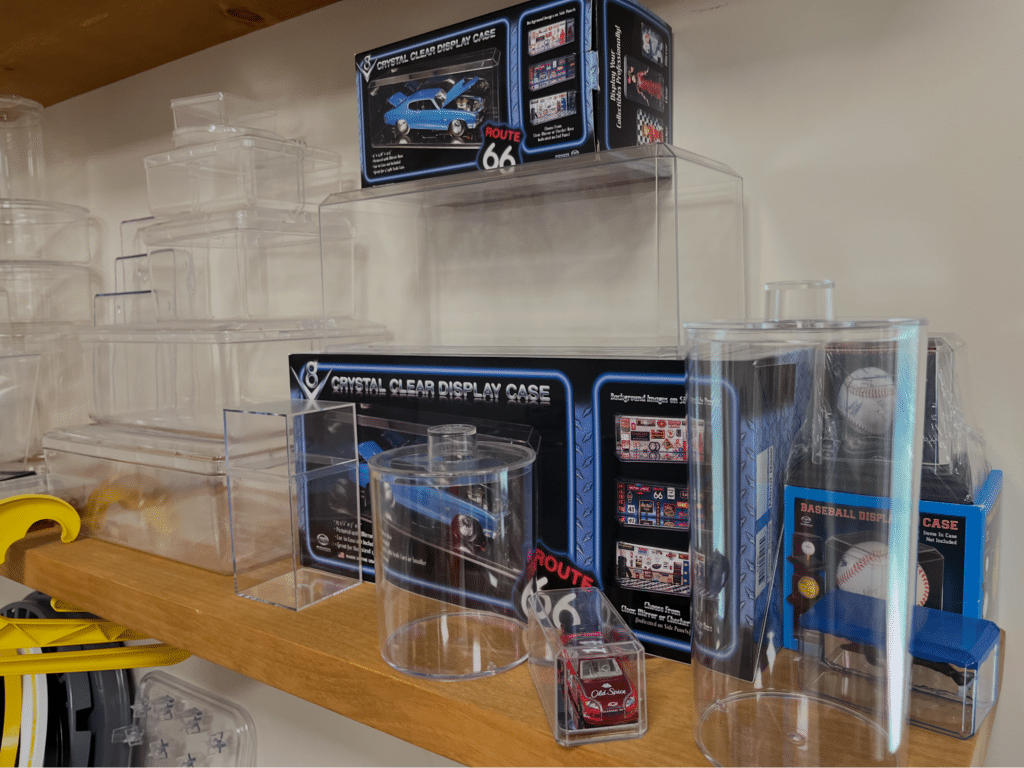
When it comes to producing proprietary or specialized plastic goods, American manufacturing provides a unique edge. Operating out of local plants allows manufacturers to oversee each phase of product creation, from concept to final inspection. Access to specialized engineering-grade materials and refined manufacturing methods further ensures items can be tailored precisely to a client’s needs.
For custom plastic solutions, domestic experts blend engineering know-how with advanced injection molding tools. Businesses receive tight manufacturing tolerances, resulting in products that fulfill demanding specifications and overall reliability standards. The presence of in-house capabilities, such as tool development and mid-production refinements, helps ensure quick adjustments when requirements shift.
These advantages translate to robust performance whether you’re a hobbyist seeking a dependable diecast display case or a large-scale operation needing specialized parts for industrial applications. By working with engineers and production teams nearby, customers can efficiently finalize designs, confirm feasibility, and move smoothly to full-scale output.
As a result, domestic manufacturing channels combine straightforward communication, fast modifications, and a culture of accountability. This synergy is especially important for proprietary or custom plastic lines, where misalignment between a concept and its final form can be costly or time-consuming. Given their proximity and regulatory frameworks, American manufacturers strive to deliver exceptionally crafted, long-lasting products that meet or exceed customer expectations.
Customer Satisfaction Through American Manufacturing Standards
Choosing American-made plastic products often equates to purchasing goods that align with high standards for quality, consistency, and reliability. Domestic manufacturing plants tend to employ systematic quality control measures to ensure durability, function, and design precision. Clients can count on tight compliance with project specifications and rapid course corrections when necessary.
Another key factor is accessible communication. Domestic collaboration largely avoids the time zone and language barriers that can complicate international contracts. This simplicity increases transparency and allows stakeholders to address minor or major design revisions right away. For businesses working on new product lines, being able to iterate promptly can be critical to a swift market launch.
Issues that arise mid-production are also easier to fix. U.S.-based factories often handle mold and tool adjustments on-site, streamlining troubleshooting efforts and limiting delays. This agility becomes invaluable for businesses on tight deadlines, as well as for collectors seeking timely access to new storage or display solutions.
Moreover, domestic manufacturers can handle variable project sizes—from extensive orders of proprietary inventory to limited runs of custom parts. By offering a variety of scalable options, these providers meet the diverse needs of corporate customers and individual collectors alike. Whether the final product is a polished presentation piece or a functional industrial component, consistent manufacturing standards remain a shared goal.
Why “Made in USA” Is the Right Choice for Custom Plastic Solutions
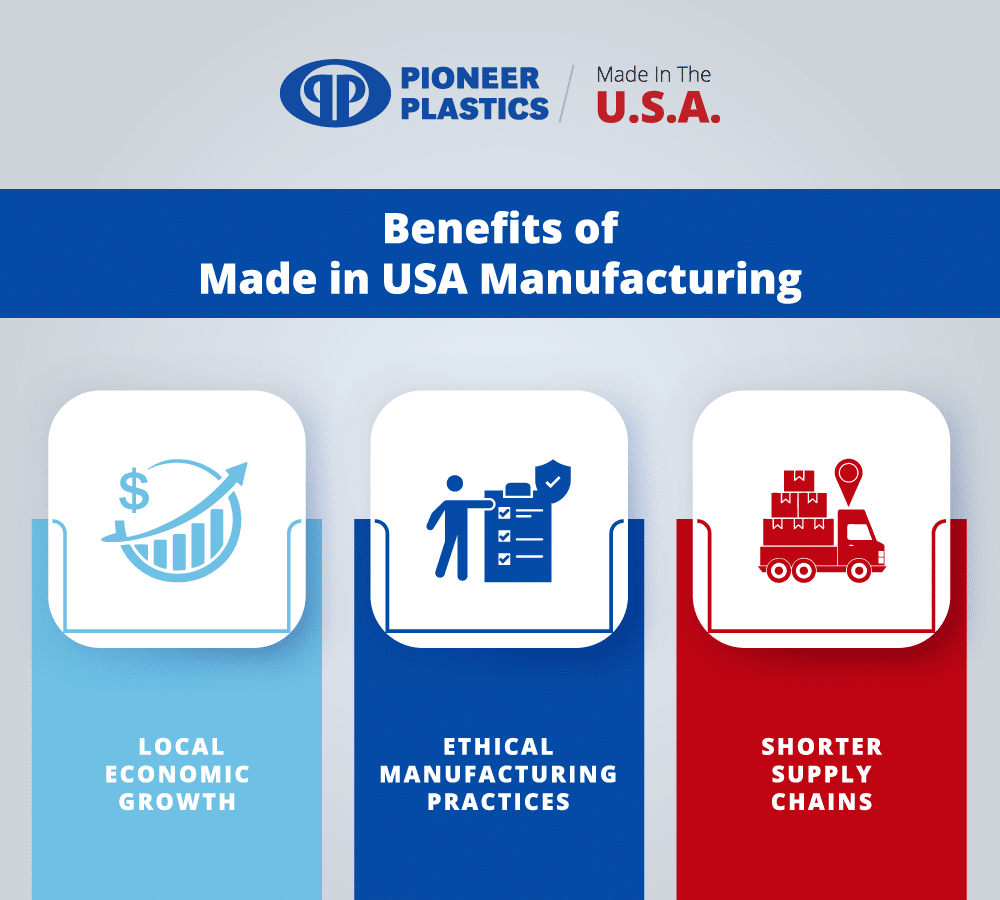
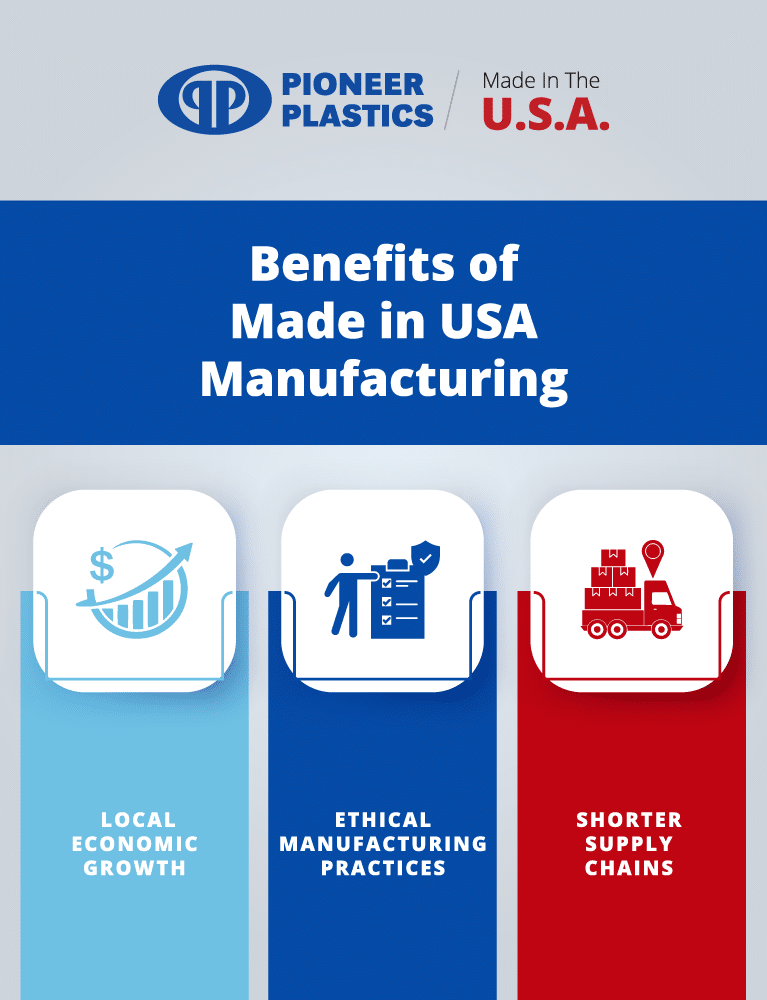
“Made in USA” manufacturing embodies quality craftsmanship, quick turnaround, ethical standards, and community-driven support. This holistic approach does more than produce great products—it spurs economic growth, advances sustainable practices, and fosters close collaboration.
Choosing “Made in USA” for custom plastic solutions offers numerous advantages, including reliable supply chains, faster fulfillment, and enhanced communication due to proximity. U.S. manufacturers adhere to strict ethical and environmental standards, ensuring fair labor practices and responsible operations, which appeals to businesses and consumers prioritizing sustainability. This choice not only fosters local economic growth by supporting jobs and regional development but also enables closer collaboration for detailed customization and innovation, resulting in high-quality, dependable products.
Backed by over 60 years of industry experience, Pioneer Plastics exemplifies these qualities through in-house tool building, custom injection molding, custom plastic parts, 3D printing, and engineering services. By integrating design, engineering, prototyping, and production under one roof, they deliver the consistency and clarity you require.
To learn more or discuss your specific needs, we invite you to contact a trusted American manufacturer today and discover the lasting advantages of Made in USA manufacturing.