In today’s rapidly evolving market, plastic injection molding innovations are significantly contributing to sustainability and efficiency. The plastic injection molding industry is undergoing a transformative era, propelled by advancements and a steadfast commitment to sustainable practices.
Plastic injection molding is a manufacturing process for producing parts by injecting molten material into a mold. It allows for the creation of complex and high-precision components used in various industries. Sustainable practices, such as using biodegradable and recycled materials, reduce environmental impact and lower production costs, meeting the growing consumer demand for eco-friendly products.
As manufacturers strive to meet the demands of the market, innovations in plastic injection molding technology are reshaping processes, enhancing efficiency, and reducing environmental impact.
Key Trends Shaping Plastic Injection Molding
The landscape of plastic injection molding is continually evolving, influenced by trends aimed at enhancing sustainability, precision, and automation. Automation increases production speed, ensures higher precision and consistency, reduces human error, and optimizes resource utilization, leading to enhanced overall efficiency and cost savings. These transformative trends not only improve manufacturing efficiency but also align with the global push towards environmentally responsible practices.
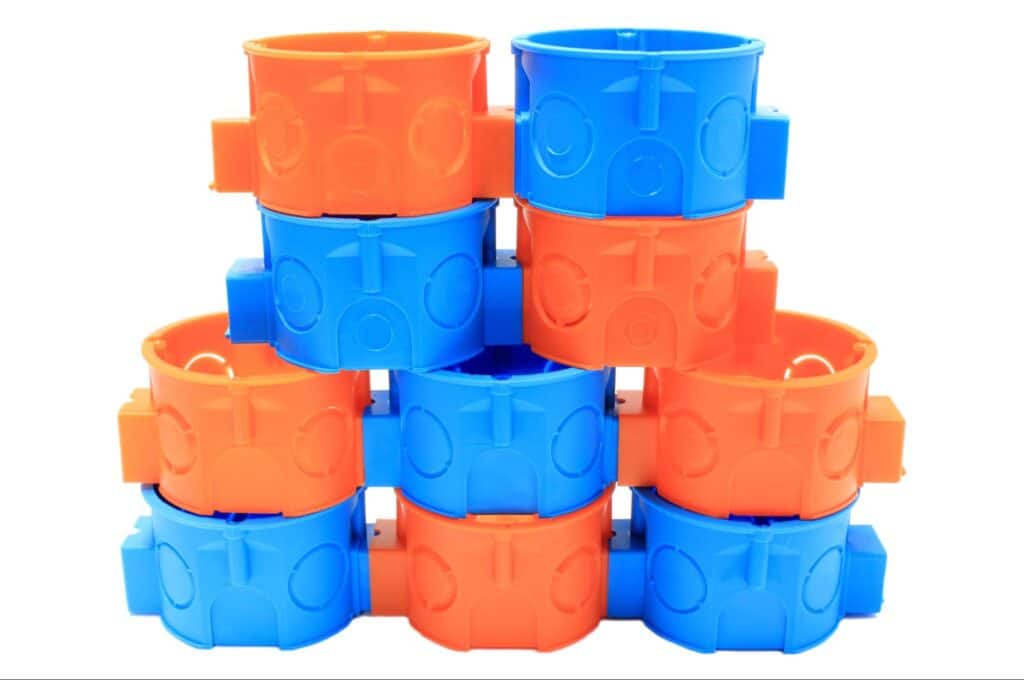
1. Sustainable Plastic Injection Molding Practices
Sustainability is a pivotal focus in modern plastic injection molding products. Manufacturers are adopting eco-friendly materials and processes to minimize their environmental footprint.
- Reducing Environmental Impact and Carbon Footprint: Manufacturers are increasingly adopting renewable energy sources, such as solar and wind, to reduce their carbon footprint. Energy-efficient equipment and lighting also contribute to sustainability efforts, reducing costs and emissions.
- Introduction of Biodegradable and Recycled Materials: Manufacturers are increasingly incorporating biodegradable and recycled materials into their products. Biodegradable plastics are made from natural, renewable resources, such as corn starch, and decompose naturally, reducing environmental pollution. Additionally, recycled plastics minimize the use of raw materials and reduce the overall carbon footprint associated with plastic production.
- Energy-Efficient Manufacturing Processes: Investing in all-electric plastic injection molding machines enhances precision and reduces power consumption significantly, leading to upwards of a 50% reduction compared to older hydraulic systems. To implement these energy-efficient systems, manufacturers should assess their current machinery, consult with energy efficiency experts, and gradually transition to newer, more sustainable technologies.
2. Precision Plastic Injection Molding Technology
Innovations in precision plastic injection molding enable manufacturers to create complex, high-quality components while minimizing waste and costs. These advancements also improve product design, functionality, and longevity.
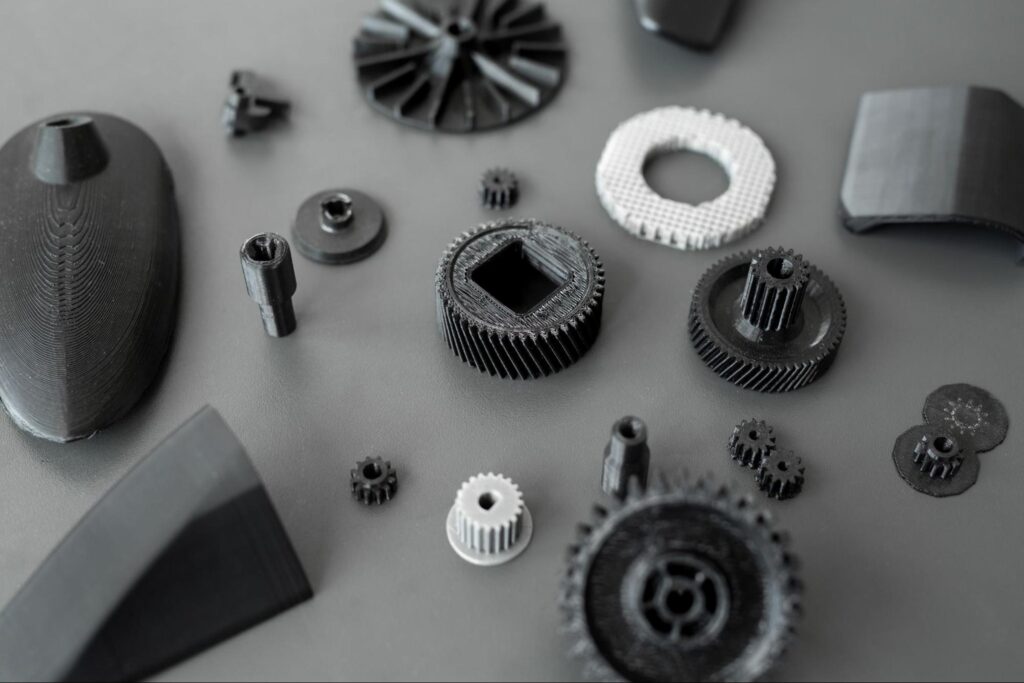
- Enhanced Mold Design and Tooling Processes: Advanced 3D printing techniques and computer-aided mold design technologies allow for greater precision in mold creation, reducing errors and enhancing product quality. These advancements also enable manufacturers to create intricate and highly detailed components that were not possible previously.
- Improvements in Quality Control: Advanced quality control and inspection processes, such as automated optical inspection systems, enable manufacturers to identify and rectify defects in real-time. These systems use high-resolution cameras and advanced algorithms to identify defects and anomalies, ensuring consistently high-quality products.
3. Automation and Smart Manufacturing in Plastic Injection Molding
Automation and smart manufacturing systems are revolutionizing plastic injection molding, enhancing production speed, accuracy, and efficiency.
- Intelligent Automated Systems: Advanced robotics, automated conveyors, and pick-and-place systems automate the plastic injection molding process, reducing human intervention and errors. Automated systems also reduce cycle times, enabling manufacturers to produce more parts in less time.
- Smart Manufacturing Technologies: The use of sensors, data analytics, and machine learning enhances production processes, providing real-time monitoring and predictive maintenance. This leads to improved quality control, reduced downtime, and enhanced efficiency.
- Intuitive Human-Machine Interfaces (HMI): Intuitive HMIs allow for real-time monitoring, improving process control, and reducing errors. These interfaces also provide operators with real-time data, enabling them to make informed decisions, leading to enhanced efficiency and reduced risks.
- AI and Machine Learning: Artificial intelligence and machine learning technologies enable predictive maintenance, advanced quality control, and real-time data monitoring. These automated systems reduce downtime and costs associated with maintenance, leading to significant cost savings.
4. Advancements in Injection Molding Materials
The realm of injection molding materials is witnessing significant innovation, with advanced materials enhancing both performance and sustainability across various sectors. Here’s a closer look at these materials and their distinctive applications:
Advanced Materials in Injection Molding
- Carbon Fiber Composites:
- Properties: Incredibly strong yet lightweight, these composites are ideal for applications requiring high strength-to-weight ratios.
- Key Benefits: They contribute to improved fuel efficiency and reduced emissions by lowering the overall weight of vehicles.
- Advanced High-Strength Steels (AHSS):
- Properties: AHSS offers superior strength and durability, enabling manufacturers to reduce component weight without compromising performance.
- Key Benefits: Leveraging these materials leads to energy-efficient engineering solutions, particularly in automotive applications.
- Bio-based Plastics:
- Properties: These plastics, including polylactic acid (PLA), are derived from renewable resources like corn starch and are biodegradable.
- Key Benefits: They provide an eco-friendly alternative to traditional plastics and help reduce the carbon footprint.
- Recycled Plastics:
- Properties: Incorporating recycled plastics not only cuts down waste but also lower production costs.
- Key Benefits: They present an economical and environmentally conscious option for manufacturers, aligning with sustainability objectives.
Industry-Specific Applications
- Automotive Industry:
- Application: Carbon fiber composites and AHSS are pivotal in manufacturing lightweight yet strong vehicle parts.
- Impact: Helps enhance vehicle fuel efficiency and performance while adhering to stricter emission regulations.
- Electronics and Healthcare:
- Application: Precision molding of intricate components is critical for the performance of medical devices and electronics.
- Impact: Ensures reliability and meets high standards for biocompatibility and durability.
- Consumer Products:
- Application: Utilization of durable plastic components improves the functionality and longevity of everyday items.
- Impact: Boosts consumer satisfaction through enhanced product quality and lifespan.
- Industrial Uses:
- Application: Injection molding advancements contribute to the production of complex industrial components such as molds with uniform cooling.
- Impact: Optimizes thermal management and minimizes cycle times, thereby increasing manufacturing efficiency.
These advancements in materials are not only propelling the plastic injection molding industry forward but are also setting new standards in terms of sustainability, cost efficiency, and application-specific performance.
5. Rapid Prototyping and Agile Manufacturing Techniques
Rapid prototyping and agile manufacturing techniques are shaping the future of plastic injection molding. These agile practices allow manufacturers to quickly produce prototypes and iterate designs, reducing time to market and overall costs.
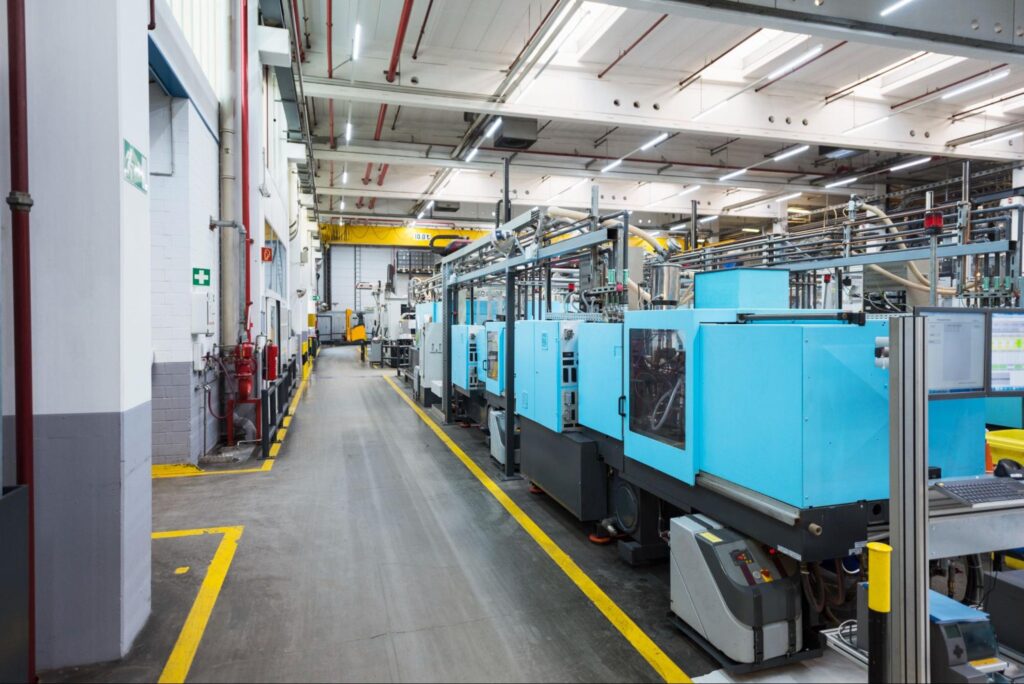
- Additive Manufacturing: 3D printing allows for the rapid production of prototypes, reducing lead times and costs associated with traditional mold-making processes.
- Iterative Design Processes: With agile manufacturing, manufacturers can quickly modify and test designs, leading to more efficient and cost-effective production.
- Lean Manufacturing Principles: Lean manufacturing principles, such as just-in-time production and waste reduction, promote efficiency and cost savings.
Impacts of Innovation on Manufacturers and Consumers
The latest innovations in plastic injection molding have profound effects on both manufacturers and consumers, driving growth and enhancing user experiences.
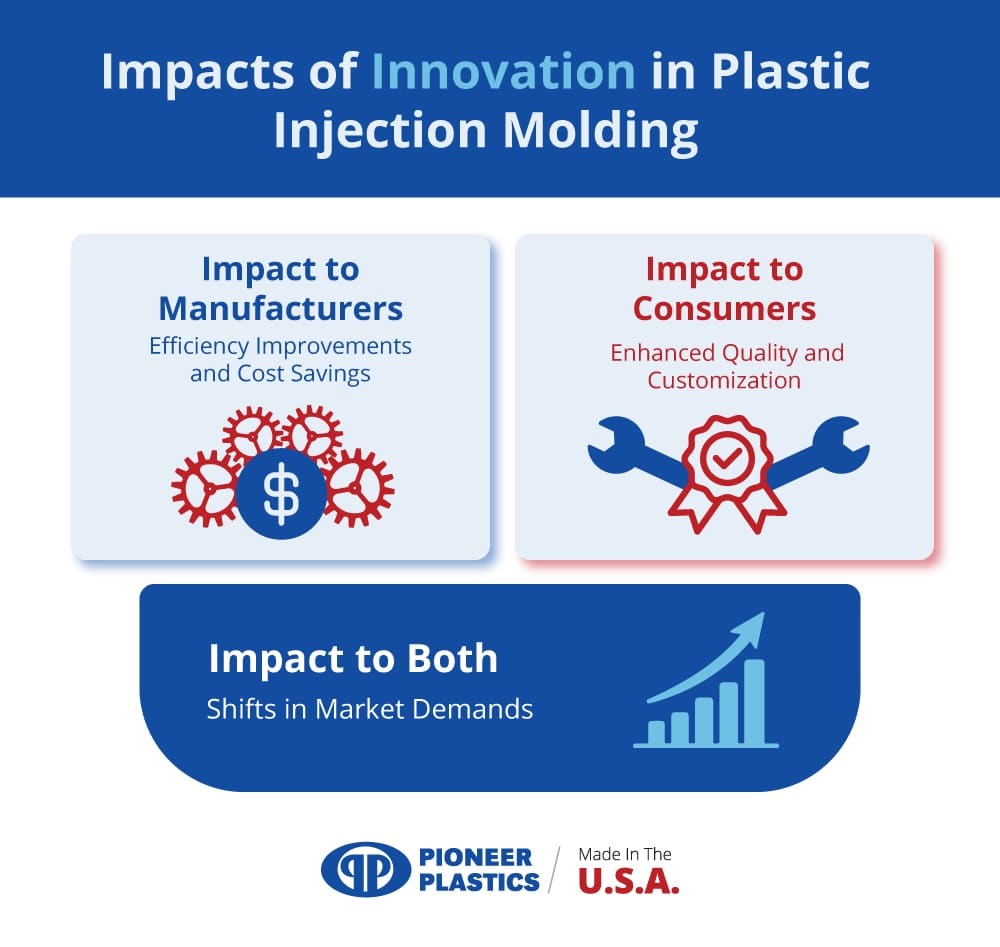
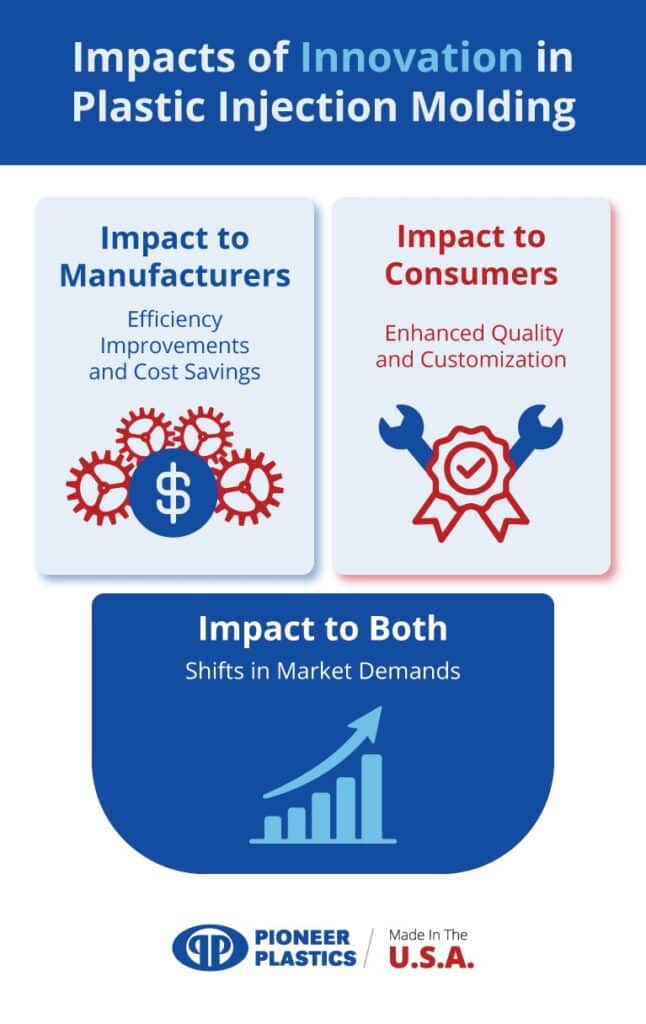
- Efficiency Improvements and Cost Savings for Manufacturers: Advanced technologies streamline production processes, reducing cycle times and material waste. This leads to significant cost savings and the ability to take on more complex projects without compromising quality.
- Enhanced Quality and Customization for Consumers: Consumers receive products that are not only higher in quality but also tailored to their specific needs. The precision and flexibility of modern plastic injection molding allow for customization that meets individual preferences and industry requirements.
- Shifts in Market Demands: As innovation drives product quality and sustainability, market demands evolve. Manufacturers are now expected to deliver environmentally friendly products without sacrificing performance, prompting a shift towards more responsible manufacturing practices.
These impacts collectively foster a more dynamic and responsive market, where both manufacturers and consumers benefit from the continuous advancements in plastic injection molding technology.
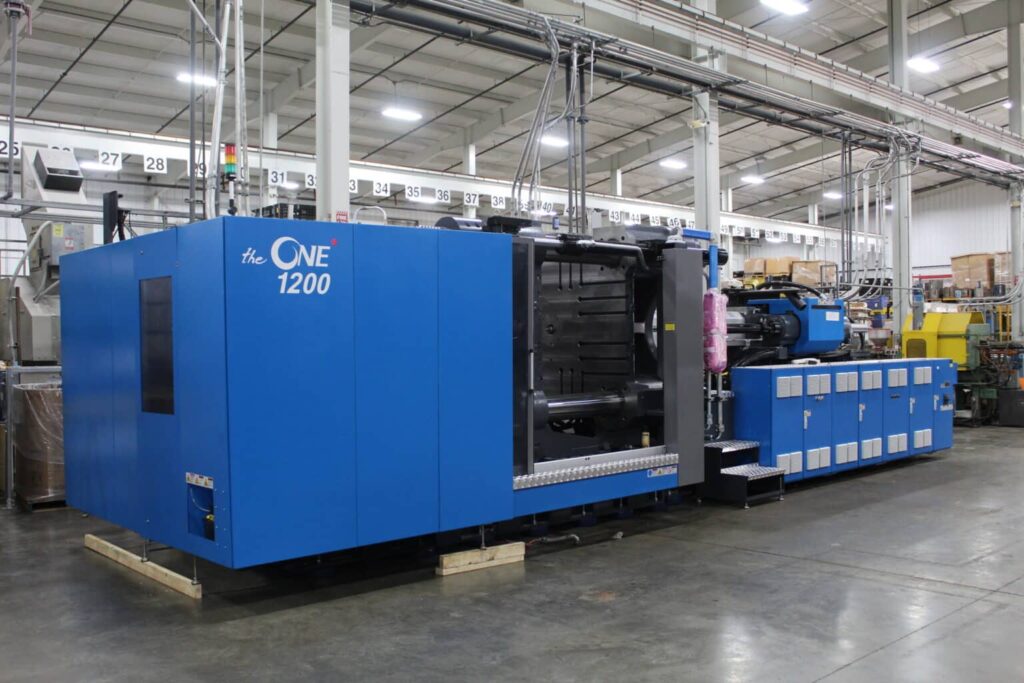
Embracing the Future: Sustainable Innovations and Efficiency in Plastic Injection Molding
The plastic injection molding industry is experiencing innovations revolutionizing manufacturing processes. By embracing things like sustainable practices, precision technologies, and smart systems, companies enhance efficiency and contribute positively to environmental sustainability. These groundbreaking advancements not only drive economic growth but also pave the way for a greener, healthier planet for future generations.
Pioneer Plastics exemplifies leadership in continuously evaluating, adopting, and implementing innovations within plastic injection molding. Pioneer Plastics employs state-of-the-art machinery and sustainable practices, including the use of recycled materials and energy-efficient molding systems, to produce high-quality custom plastic parts. Their comprehensive engineering services guide clients through the entire product development process, ensuring tailored solutions that exceed expectations.
Contact Pioneer Plastics to learn more about their advanced plastic injection molding capabilities and how they can help meet your specific needs while staying at the forefront of industry innovation.