In today’s fast-paced product development landscape, quickly transforming ideas into reality is crucial for innovation. Prototype injection molding and production-scale injection molding are essential for designing, testing, and manufacturing plastic parts, though they serve different purposes.
This guide explores the distinct roles of both methods, highlighting their applications, benefits, and advancements. Understanding these differences can help businesses, collectors, and vendors streamline decision-making, reduce costs, and enhance product outcomes as industry standards evolve.
Introduction to Injection Molding: Prototype vs. Production
Injection molding is a versatile manufacturing method that creates plastic parts by injecting molten material into a mold. It is crucial to produce exact prototypes before finalizing the design before building the injection mold for both prototypes and end-use products.
Prototype injection molding aids in testing and refining designs, while mass production molding focuses on efficiency, consistency, and scalability. Understanding these distinct roles is essential for reducing costs, improving product quality, and accelerating time to market.
Overview of Prototype Injection Molding
Prototype injection molding methods are essential in the early stages of product development, providing an efficient way to test designs and refine concepts before committing to full-scale production. This approach focuses on creating molds and parts quickly, enabling engineers and designers to validate their ideas, address potential design flaws, and make necessary adjustments. This minimizes risks and ensures a smoother transition to production.
Key Advantages of Prototype Injection Molding
- Faster Iterations: Enables rapid production and quick testing of design changes.
- Effective Design Validation: Creates tangible models for thorough testing of a product’s form, fit, and function.
- Cost Efficiency at the Initial Stage: Utilizes lower tooling expenses, making it budget-friendly compared to production molds.
Common Uses for Prototyping
Injection molding for prototypes is widely employed in scenarios where design precision and early testing are critical:
- Design and Function Testing: Assess product functionality and make improvements before mass production.
- Market Feedback and Analysis: Gather consumer feedback or demonstrate products at trade shows with early physical models.
- Pre-Production Validation: Test performance under real-world conditions to ensure the product meets practical requirements.
By enabling rapid experimentation, feedback, and improvement, prototype injection molding serves as the foundation for successful product development, helping businesses save time, reduce costs, and increase confidence in their final designs.
Overview of Production Injection Molding
Mass production injection molding techniques are the cornerstone of large-scale manufacturing, designed to produce high volumes of identical parts with high levels of consistency and precision. This method employs durable molds crafted from robust materials, such as hardened steel, specifically engineered to withstand prolonged use and mass production.
Unlike prototyping, where the priority lies in testing and refining ideas, production injection molding focuses on efficiency and scalability. It ensures that every piece meets the same high standards, making it ideal for industries that demand reliability, reproducibility, and cost-effective output.
Key Benefits of Production Injection Molding
- High-Volume Efficiency: Handles thousands—or even millions—of parts without compromising quality.
- Consistent Quality Assurance: Optimized for precision, ensuring uniformity across every unit.
- Economies of Scale: Long-term cost efficiency makes it a prudent investment for large quantities.
Common Applications of Production Injection Molding
Mass production injection molding techniques are well-suited for various industries and applications, including:
- Mass Production of Consumer Goods: This includes household products, packaging, and electronics components often produced in bulk.
- Automotive and Industrial Parts: Engine components, dashboards, and other high-strength parts benefit from durable production molds.
- End-Use Products: Products like toys and medical devices meet rigorous quality standards.
- Long-Term Manufacturing Runs: Ideal for designs replicated for years without significant modifications.
By offering high levels of consistency, cost-efficiency over time, and scalability, production injection molding is the solution of choice for transforming proven designs into everyday essentials.
Detailed Comparison of Prototype vs Production Injection Molding
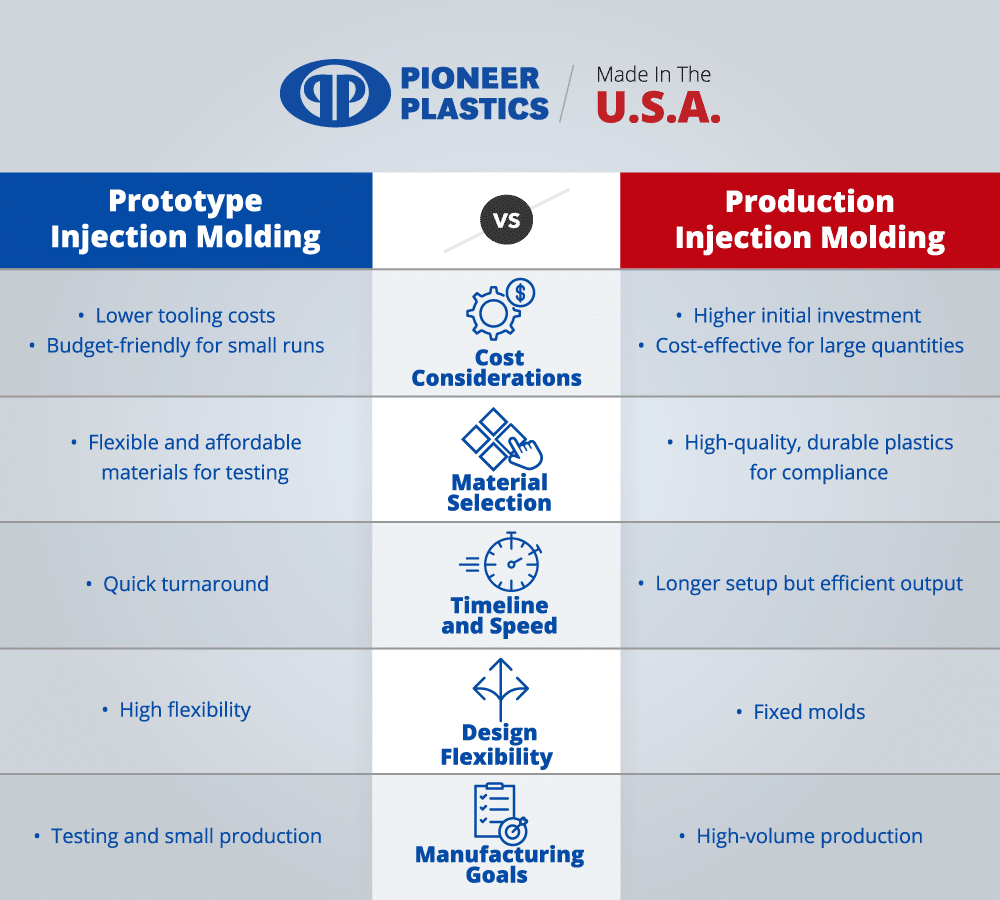
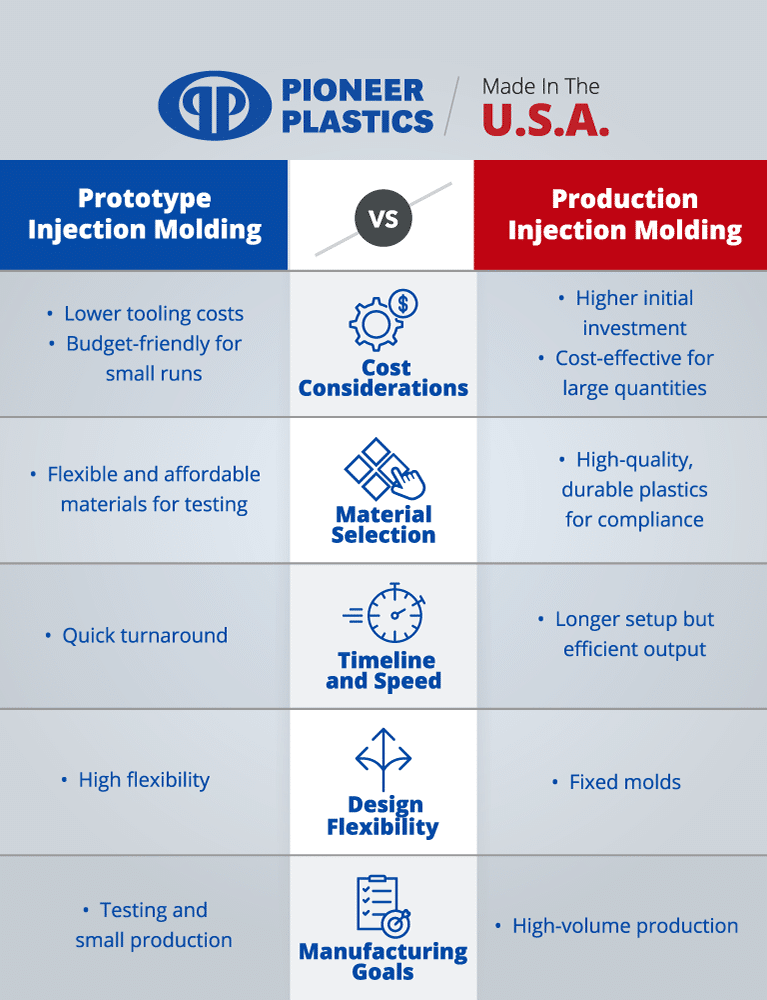
Choosing between prototyping and production injection molding requires understanding their differences in cost, materials, timelines, design adaptability, and manufacturing goals. Here’s a clear breakdown to help you make the right choice for your project.
Cost Considerations
Prototype Injection Molding
- Lower Tooling Expenses: Prototype molds are typically made from cost-efficient materials like aluminum, significantly reducing upfront costs.
- Budget-Friendly for Small Runs: Ideal for producing limited quantities during early development stages without substantial financial commitments.
Production Injection Molding
- Higher Initial Investment: Production molds are crafted from durable materials such as hardened steel. While initial expenses are higher, long-term benefits often justify the upfront cost.
- Cost Efficiency Over Time: Scalability and durability make production molds highly economical for manufacturing large quantities, reducing costs per unit.
Material Selection
Prototype Injection Molding
- Flexible Material Options: Test different materials and make adjustments to evaluate performance.
- Affordable Testing Materials: Uses less expensive materials, perfect for design validation and experimentation without inflating development costs.
Production Injection Molding
- High-Quality Durability: Relies on robust, production-grade plastics suited for end-use products.
- Regulatory Compliance: Materials meet strict quality and safety standards essential for industries like automotive, medical, and consumer goods.
Timeline and Speed
Prototype Injection Molding
- Quick Turnaround: Simplified designs and softer mold materials enable faster mold fabrication and shorter lead times.
- Faster Iterations: Allows rapid testing, revisions, and retooling during early development stages.
Production Injection Molding
- Longer Setup Time: Complex mold designs and hardened materials make production molds more time-intensive to create.
- Steady Output: Once the mold is ready, the process efficiently produces large quantities without interruptions.
Design Flexibility and Customization
Prototype Injection Molding
- High Flexibility During Development: Molds are easier to modify, perfect for frequent design changes or extensive testing.
- Supports Complex Customization: Encourages innovative and experimental designs that evolve throughout development.
Production Injection Molding
- Fixed for Consistency: Once finalized, production molds are optimized for repeatability, reducing flexibility in future modifications.
- Precision and Uniformity: Consistently replicates the approved design with exact specifications and minimal deviations.
Manufacturing Goals and Output
Prototype Injection Molding
- Focus on Testing and Refinement: Creates preliminary parts for assessing function, form, and fit while identifying potential issues.
- Small Batch Production: Limited to producing prototypes or early-stage components for validation and market testing.
Production Injection Molding
- High-Volume Manufacturing: Tailored for large-scale production runs, ensuring consistent quality across thousands—or millions—of parts.
- End-Use Reliability: Supports finished-product manufacturing for consumer, industrial, or medical markets where durability and precision are paramount.
Choosing the Right Fit
The decision between prototype and production injection molding depends on your project’s specific needs. For early-stage development, prototype molding offers flexibility, fast iterations, and cost-efficiency, making it ideal for design refinement. On the other hand, production molding excels when scalability, durability, and large-volume consistency are priorities.
By evaluating factors such as project goals, budget, timeline, and production requirements, businesses can confidently select the injection molding process that best aligns with their objectives. Both methods are complementary, often functioning together to ensure a smooth transition from innovative ideas to market-ready products.
Advancements in Prototype and Production Injection Molding
The field of injection molding is evolving rapidly with innovative technologies and practices that enhance both prototype and production processes. These advancements are redefining how businesses approach product development and manufacturing, offering increased efficiency, sustainability, and precision.
Breakthroughs in Rapid Prototyping Technologies
- 3D Printing Integration: Combining 3D printing with injection molding has revolutionized prototyping, enabling faster tool production and greater design complexity. This hybrid approach reduces lead times, allowing quicker turnaround of functional prototypes.
- AI-Powered Simulation Tools: Advanced digital simulations predict mold performance, material flow, and potential design issues before physical production begins. This reduces errors, streamlines development, and optimizes outcomes for every prototype.
Emerging Material Innovations
- High-Strength Polymers: High-strength polymers provide enhanced durability and improved performance for both prototyping and production applications. These polymers are suited to demanding industries like automotive and medical manufacturing.
- Eco-Friendly Alternatives: The shift toward sustainability has increased interest in biodegradable and recyclable plastics. These materials minimize environmental impact and align with growing consumer demand for greener products.
Advancements in Automation and Smart Manufacturing
- Robotics and AI Integration: Automated systems improve speed, precision, and safety in injection molding. Robots can perform tasks such as part removal, quality inspection, and mold adjustments with minimal intervention.
- Real-Time Monitoring via Internet of Things (IoT): Smart manufacturing systems equipped with IoT technology allow for real-time monitoring and adjustments, ensuring optimal production conditions while reducing waste and downtime.
Trends in Sustainability
- Energy-Efficient Machinery: Manufacturers are adopting energy-saving injection molding machines that reduce power consumption without compromising performance. These advancements result in significant cost savings over time.
- Circular Economy Practices: Companies focus on closed-loop systems, reusing materials from discarded parts and implementing processes that support sustainable manufacturing cycles.
As these advancements reshape the landscape of injection molding, businesses can benefit from faster prototyping, improved production efficiency, and a commitment to sustainability. Staying ahead of these trends allows for more innovative and cost-effective manufacturing while meeting evolving market and environmental demands.
How to Choose Between Prototype and Production Injection Molding
Determining the right injection molding approach for your project requires careful evaluation of several key factors. Both prototype and production injection molding excel in different scenarios, so choosing the right process depends on your goals, budget, timeline, and production needs. Here’s a guide to help you make the best decision.
Assessing Project Goals
- Prototype Injection Molding: Ideal for early-stage development, allowing efficient testing and refinement of ideas. It enables design validation, addresses functionality issues, and makes improvements before committing to full-scale manufacturing.
- Production Injection Molding: The logical choice for finalized designs ready for market. It ensures efficient large-volume output with consistent quality for mass production.
Evaluating Budget Constraints
- Prototype Injection Molding: Offers a lower-cost entry point, making it budget-friendly for preliminary design validation or small runs. The use of cost-effective materials and simplified molds helps minimize upfront expenses.
- Production Injection Molding: While the initial investment is higher due to durable mold materials like hardened steel, this method becomes more cost-efficient as production volumes scale. It is ideal for long-term projects where economies of scale come into play.
Considering Time Requirements
- Prototype Injection Molding: With quick turnaround and faster iterations, prototyping is perfect for projects requiring rapid adjustments or a fast market introduction. Development cycles are shorter, enabling prompt testing and modifications.
- Production Injection Molding: Setting up production molds requires a longer setup time due to their complexity and focus on precision. However, once the process begins, it delivers steady, high-volume manufacturing efficiently.
Determining Production Volume Needs
- Prototype Injection Molding: Best suited for low-volume production, such as creating sample parts, test versions, or early-stage designs. This method is invaluable for refining ideas before committing to larger-scale operations.
- Production Injection Molding: Designed for high-volume manufacturing, this approach reliably produces thousands or millions of identical parts. It’s the go-to solution when scalability and consistency are essential for your business.
Integrating Prototyping into the Process
In many cases, the most effective strategy combines both prototyping and production processes. Starting with injection molding for prototypes allows for early-stage testing and refinement, reducing risks and ensuring the final design meets all requirements. Once a design is validated, transitioning to mass production injection molding becomes a seamless step for large-scale manufacturing.
The benefits of this dual approach include:
- Minimized Risk: Identifying and resolving issues before investing in production molds prevents costly mistakes.
- Optimized Costs: Testing with prototype molds eliminates unnecessary expenditures, while production molds reduce cost per unit over time.
- Enhanced Quality: Refined prototypes ensure that the final output meets customer expectations and market demands.
Example Scenarios
- Launching New Products: Begin with prototypes to test functionality, collect consumer feedback, or showcase concepts to stakeholders. Once the design is validated, use production molds for scaling.
- Expanding High-Demand Manufacturing: Transition to production injection molding when products require larger volumes to meet growing market demands, ensuring scalability and durability for end-use items.
By considering your project’s unique requirements and applying the appropriate process—or blending the two—you can achieve the perfect balance of flexibility, cost-efficiency, and scalability.
The Role of Custom Injection Molding in Bridging the Gap
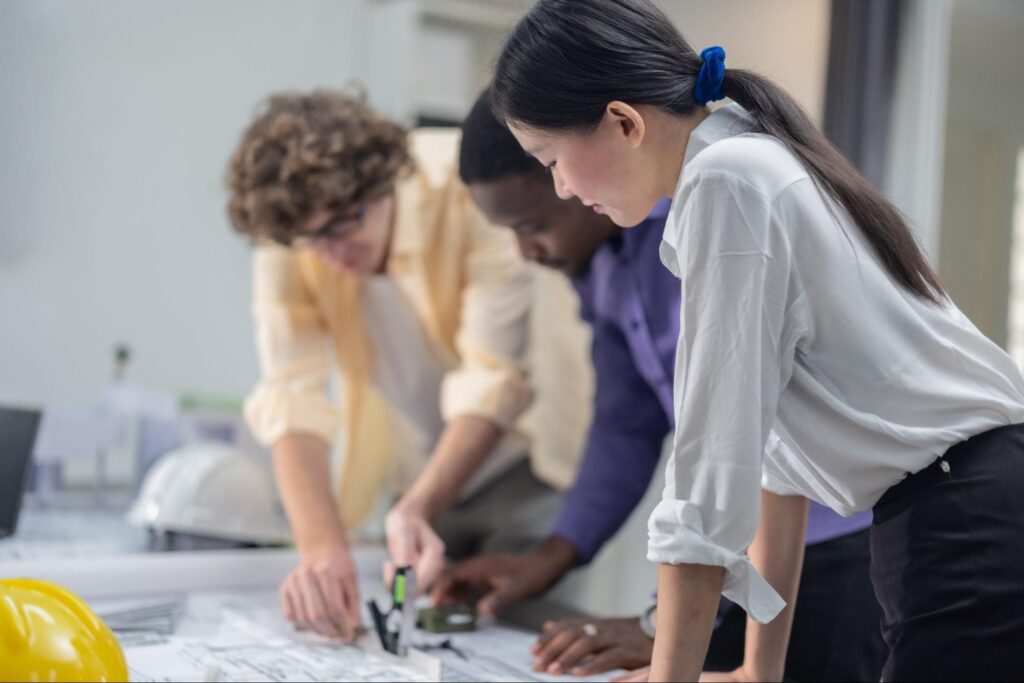
Custom injection molding solutions serve as the crucial link between prototyping and full-scale production, offering tailored services that address each project’s unique demands. By combining the best aspects of prototype and production processes, custom injection molding ensures products are developed and manufactured with high levels of consistency, precision, flexibility, and efficiency.
Meeting Unique Customer Requirements
Custom injection molding allows businesses to translate their specific needs into highly specialized solutions:
- Tailored Designs: Molds are created to match exact specifications, ensuring products meet functional and aesthetic expectations.
- Adaptability: Customization enables quick adjustments throughout the process, minimizing delays and optimizing outcomes.
Enhancing Product Development with Engineering Expertise
A key strength of custom injection molding is its ability to enhance the entire product development process:
- In-House Tool Building: Skilled tool-building capabilities allow for quick mold adjustments and refined designs, accelerating development timelines.
- Collaborative Engineering Support: Expert guidance on materials and structural design ensures products are built for durability, performance, and compliance with industry standards.
Providing Seamless Transitions Between Phases
Custom injection molding bridges the gap between early-stage prototyping and high-volume production by integrating the strengths of both approaches:
- Streamlining the Shift from Prototype to Production: Once a prototype is perfected, custom molds for large-scale manufacturing can be developed with minimal disruption.
- Consistency Across Phases: Custom molds ensure that the quality and specifications achieved during prototyping are seamlessly carried into production.
Partnering with an Experienced Injection Molding Provider
Choosing the right partner for custom injection molding makes all the difference. An experienced provider ensures:
- Expertise Spanning Prototyping and Production: Efficient navigation of both stages allows for a smooth and cost-effective transition from developmental concepts to market-ready products.
- Commitment to Quality: With extensive experience, the provider ensures consistency and precision across each production phase.
- End-to-End Flexibility: Whether it’s a short-run custom order or high-volume manufacturing, an experienced team adapts to the project’s unique scope with efficiency and skill.
By utilizing custom injection molding, businesses can innovate with confidence. This approach addresses specific requirements and ensures a smoother transition from design refinement during prototyping to efficient, large-scale production.
Why Pioneer Plastics Is Your Preferred Partner for Injection Molding
Pioneer Plastics offers a range of injection molding services, including mass production injection molding techniques, delivering custom solutions that cater to diverse industries and unique customer needs.
Decades of Expertise and Committed Excellence
With over 60 years of industry experience, Pioneer Plastics has honed the craft of transforming ideas into tangible products. The team’s extensive knowledge and commitment to excellence contribute to reliable partnerships in plastic manufacturing. From initial concept development to full-scale production, their expertise ensures seamless execution at every step.
Comprehensive Capabilities in Tool Building and Engineering
At Pioneer Plastics, more than just injection molding is offered; end-to-end support is provided to bring visions to life:
- Advanced Tool Building: In-house tool-building capabilities enable rapid mold adjustments and modifications, supporting efficiency and precision throughout the project.
- Advanced Engineering Support: Focusing on high-quality engineering-grade plastics, the team provides expert guidance on material selection and product design, ensuring parts meet durability, performance, and compliance standards.
Commitment to Rapid Prototyping and Quality Production
Pioneer Plastics understands the importance of speed and quality in modern manufacturing:
- Accelerated Prototyping: Specializing in quick-turnaround services, enabling businesses to bring concepts to life faster without compromising precision or performance.
- USA-Made Manufacturing Standards: Commitment to domestic production ensures high-quality standards while supporting the U.S. manufacturing sector.
Versatility to Accommodate Short-Run and Long-Run Projects
Whether a limited prototype run or high-volume production is needed, Pioneer Plastics is equipped to handle projects of all sizes:
- Scalability with Consistency: From small-batch custom orders to high-volume manufacturing, consistent quality and performance are delivered across all production volumes.
- Flexible Production Solutions: Ability to adapt to various customer requirements ensures each project is completed on time and to exact specifications.
Bridging Prototyping and Production for Optimal Results in Injection Molding
Understanding the differences between prototype and mass production injection molding is essential for successful product development. Prototyping facilitates rapid iteration and cost-effective design validation, while production molding focuses on efficiency and scalability for large volumes of end-use products. Leveraging both methods can help businesses remain competitive and innovative. By evaluating project goals, budgets, and timelines, the right approach can be selected to maximize efficiency and minimize risks.
At Pioneer Plastics, we provide expert guidance in navigating these choices. With decades of experience in custom injection molding and 3D printing, we offer tailored solutions to meet your needs. Contact us today to learn how our innovative services can bring your ideas to life from concept to production.