In the intricate dance of form and function that characterizes plastic injection molding, hot stamping emerges as a pivotal step, where aesthetic appeal meets durability. It’s a process that, while not as widely known as the molding itself, plays a crucial role in elevating the final product from merely functional to visually engaging. This blog post will delve into the fascinating world of hot stamping, unveiling its definition, application, and the significant advantages it brings to the production of custom plastic parts.
As we navigate through this exploration, you’ll discover how hot stamping operates on the principles of heat, pressure, and dwell time to transform the mundane into the magnificent. Pioneer Plastics stands at the forefront of this technique, harnessing its potential to enhance both the aesthetic and functional qualities of their proprietary products and custom solutions.
Whether you’re a manufacturing engineer, a product designer, a business owner, or are simply curious about the intricacies of plastic part creation, this post promises to shed light on the hot stamping process and its integral role in the art of plastic injection molding.
Understanding Hot Stamping in Plastic Injection Molding
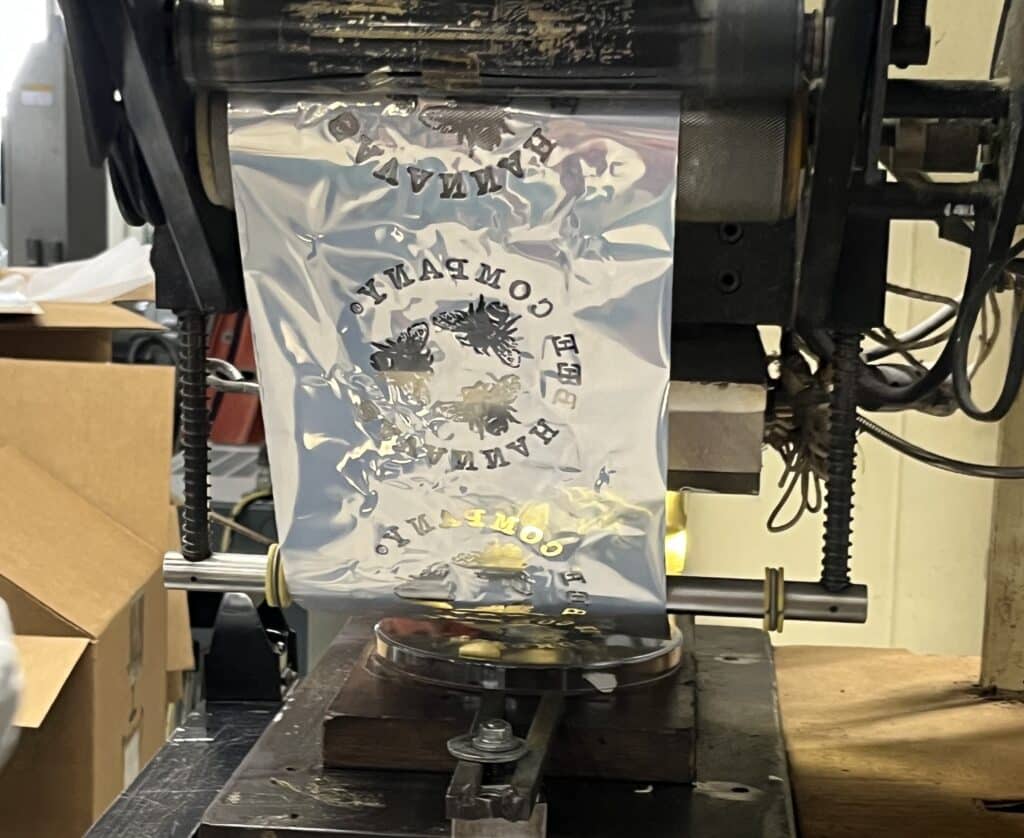
Hot stamping is a post-molding process that involves the application of pre-printed graphics, and metallic or pigmented foils onto the surface of plastic parts. It is typically employed to add decorative elements or functional markings to injection molded components.
The process is distinct from the molding itself and is performed after the parts have been molded and cooled.
The basic technique of hot stamping requires the application of heat, pressure, and dwell time to transfer the design from the foil to the plastic part. A heated die is used to press the foil against the part’s surface, and under controlled temperature and pressure, the adhesive layer of the foil bonds with the plastic. Dwell time, or the duration for which the die is held against the part, is crucial for ensuring a complete and durable transfer.
The foil used in hot stamping consists of a thin layer of pigment or metallic material, with an adhesive backing that bonds to the plastic part’s surface.
These materials are designed to withstand the heat and pressure of the stamping process while providing a high-quality finish that adheres well to the plastic substrate. Hot stamping foils come in a variety of colors and finishes, allowing for a wide range of design possibilities.
The Applications of Hot Stamping in Plastic Parts Production
Hot stamping serves multiple purposes in the production of plastic parts, ranging from aesthetic enhancements to functional applications. Manufacturers utilize this technique to apply metallic finishes, simulate patterns, or create intricate custom designs on their products.
These decorative elements can transform the appearance of a plastic part, giving it a high-end look and feel that can be tailored to match specific design requirements.
In addition to the visual appeal, hot stamping is also employed for practical reasons. It is an effective method for imprinting labels, serial numbers, and warning labels onto plastic components.
The durability of the hot stamping process ensures that these markings remain legible over the product’s lifespan, which is crucial for safety, regulatory compliance, and inventory management. Industries such as automotive, electronics, and consumer goods frequently rely on hot stamping to deliver both the functional and decorative elements that define their products.
Benefits of Hot Stamping in the Plastic Injection Molding Process
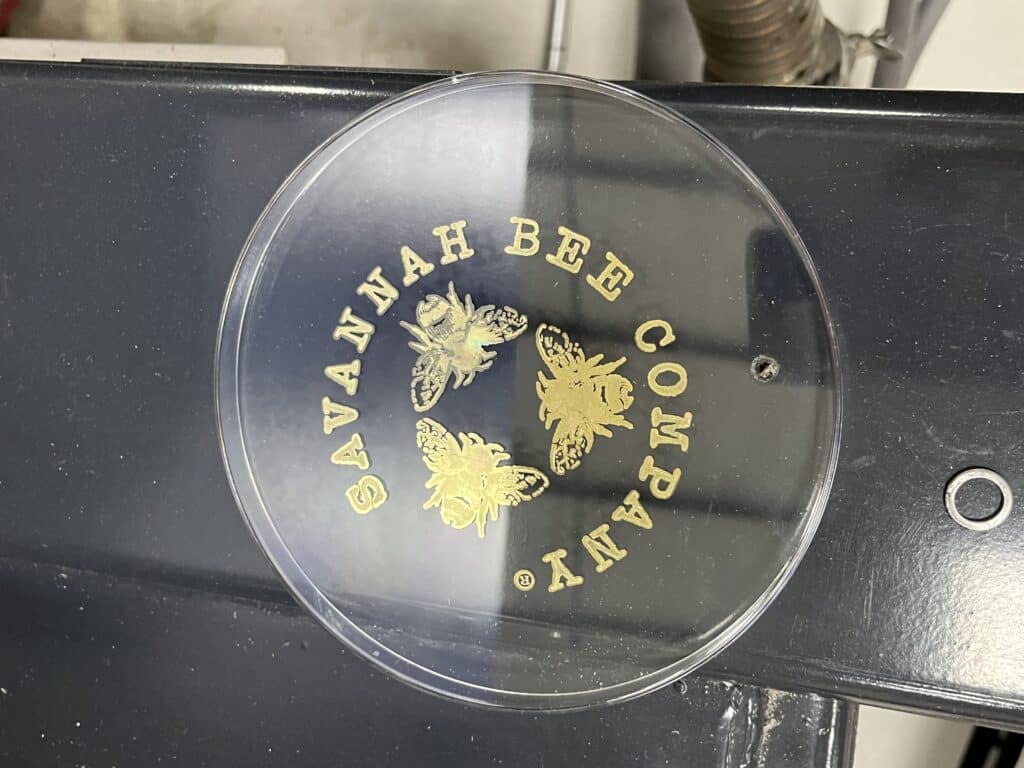
Hot stamping offers exceptional durability and longevity for decorations on plastic parts. Unlike other decorative techniques that may wear or fade over time, hot stamped images and patterns maintain their vibrancy and resist scratching, peeling, or fading. This resilience makes hot stamping an ideal choice for products that will be handled frequently or exposed to harsh conditions. However, hot stamping is not permanent—it will wear and fade over time depending on the handling and usage of the part.
High-Quality Aesthetic
The process of hot stamping also yields high-quality aesthetic results, capable of reproducing intricate details with precision. It allows for the addition of metallic finishes, wood grains, and complex custom designs that are difficult to achieve through other means. The visual appeal and fine detail provided by hot stamping can greatly enhance the overall appearance of the finished product.
Cost-Effective
Moreover, hot stamping is cost-effective for medium to high volume production runs. The initial setup costs are offset by the low running costs and quick processing times, which reduces the overall cost per part when spread across large quantities.
Environmentally Friendly
Additionally, as an environmentally friendly alternative to painting and coating processes, hot stamping eliminates the need for solvents and results in less waste, making it an attractive option for businesses looking to reduce their environmental impact.
The Integration of Hot Stamping with Injection Molding
Hot stamping is typically introduced as a secondary process once the plastic injection molding cycle is completed. This ensures that the base part is fully formed and has the structural integrity necessary to withstand the subsequent hot stamping procedure. The integration of hot stamping into the production line is carefully managed to maintain efficiency and quality control, with a seamless transition from molding to decoration.
Before a plastic part undergoes hot stamping, it requires preparation to ensure the best adhesion and finish. This involves cleaning the surface to remove any contaminants and verifying the part’s dimensions to align with the stamping design.
The plastic part’s material and design may also necessitate specific surface treatments or primers to optimize the adhesion of the foil or pre-printed heat transfer during the hot stamping process.
Customization through hot stamping offers a variety of design options, allowing for the incorporation of intricate patterns, text, and images that can significantly enhance the visual appeal and functionality of the final product.
How Hot Stamping Contributes to Product Differentiation
Hot stamping plays a pivotal role in product branding and identity by allowing manufacturers to apply precise and custom designs onto plastic parts. This process not only enhances the visual appeal but also serves as a method for brand recognition, enabling a product to stand out on the shelves or in the marketplace.
The crisp, clean lines and vibrant colors achieved through hot stamping can make logos, brand names, and other design elements pop, which is critical in creating an immediate visual impact and fostering brand loyalty.
The perceived value of products is often elevated by the premium finishes that hot stamping can achieve, such as metallic sheens, textured surfaces, and intricate patterns.
These embellishments can transform a standard plastic component into a luxury item, which in turn can justify a higher price point and position the product in a different market segment. By utilizing hot stamping, companies can effectively differentiate their products, offering a competitive edge that attracts consumer attention and preference.
Considering Hot Stamping for Your Plastic Injection Molded Parts? Choose Pioneer Plastics
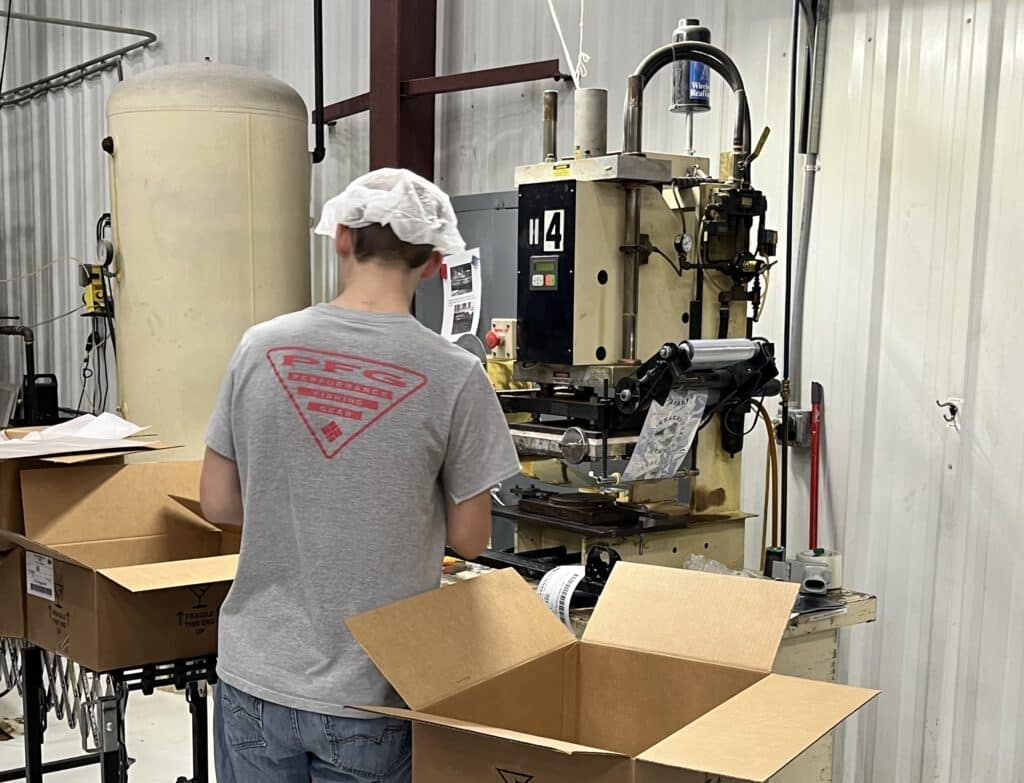
When choosing hot stamping for your plastic injection molded parts, it’s important to consider the specific requirements of your project. The design intricacies, color fidelity, and durability demands of the final product are key factors that will influence the suitability of hot stamping as a decorative and branding solution.
Additionally, the volume of production and the economic implications of incorporating hot stamping into your process must be assessed to ensure that the benefits align with your project’s budget and timeline.
An experienced custom injection molding company can guide you in the best options to achieve your desired end result.
Pioneer Plastics’ Expertise in Hot Stamping
Pioneer Plastics’ hot stamping capabilities are bolstered by state-of-the-art equipment designed to deliver precision and quality.
The company’s extensive experience with this technique allows for the execution of complex hot stamping projects that meet exacting standards. With a focus on consistency and excellence, Pioneer Plastics ensures that each hot stamped product reflects the high level of craftsmanship associated with their brand.
Through a portfolio of successful plastic part customization endeavors, Pioneer Plastics demonstrates its adeptness in enhancing the aesthetics and functionality of plastic parts. Pioneer Plastics’ commitment to innovation means they are continually refining their custom plastic parts and custom injection molding processes, including hot stamping, to meet the evolving needs of their diverse clientele.
Working with Pioneer Plastics to integrate hot stamping into your design begins with a thorough consultation to understand your needs and objectives.
Their team of experts will evaluate your design and provide recommendations on how hot stamping can enhance your parts, considering factors such as material compatibility and the complexity of the design.
Elevate the Ordinary to Extraordinary, One Press at a Time
As we’ve explored, hot stamping is not just a process; it’s an avenue for innovation and customization in plastic injection molding.
The technique’s ability to deliver both aesthetic appeal and functional value makes it a compelling choice for those who seek to elevate their plastic parts beyond the ordinary. With Pioneer Plastics’ extensive experience and state-of-the-art equipment, your project can harness the full potential of hot stamping to achieve remarkable results.
Let’s collaborate to infuse your products with the durability, precision, and beauty that hot stamping can provide. Together we can set a new standard for excellence in your industry.
Embrace the opportunity to distinguish your products with the unmistakable touch of class that hot stamping offers. Contact Pioneer Plastics now, and let’s discuss how we can integrate this transformative technique into your next plastic injection molding project.