Just like the design of the part, the mold design & manufacturing process is important to the integrity and function of the part. If not executed properly, the injection molding process can cause cosmetic injection molding defects and form injection molding defects, sometimes compromising the safety and performance of the product. With that in mind, be sure that your plastic injection molding partner takes the proper precautions with your product so that none of these types of injection molding defects occur.
Here is a list of common injection molding defects and how to avoid them:
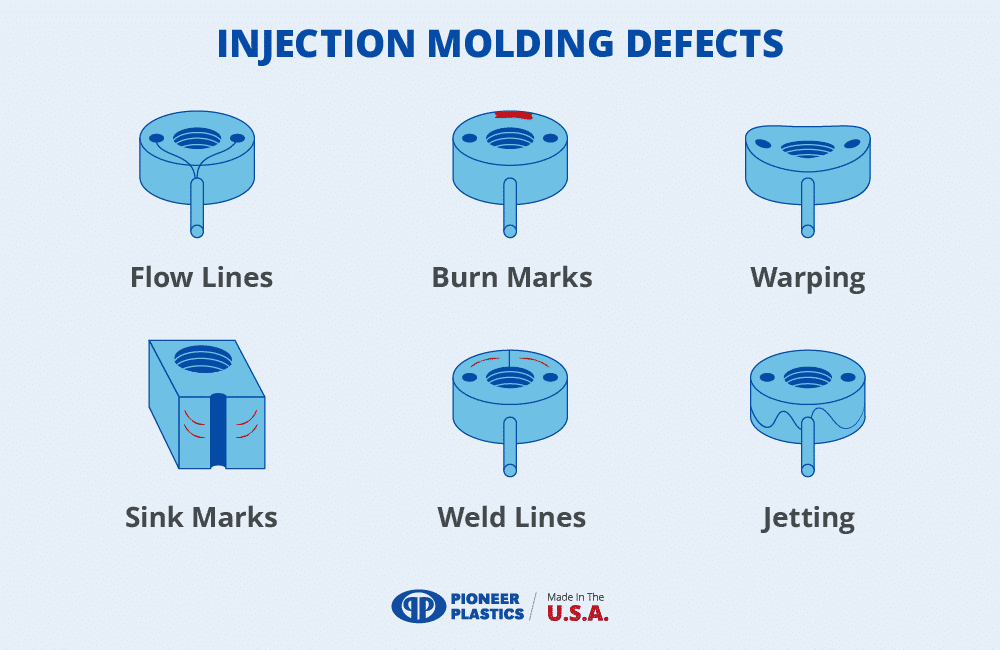
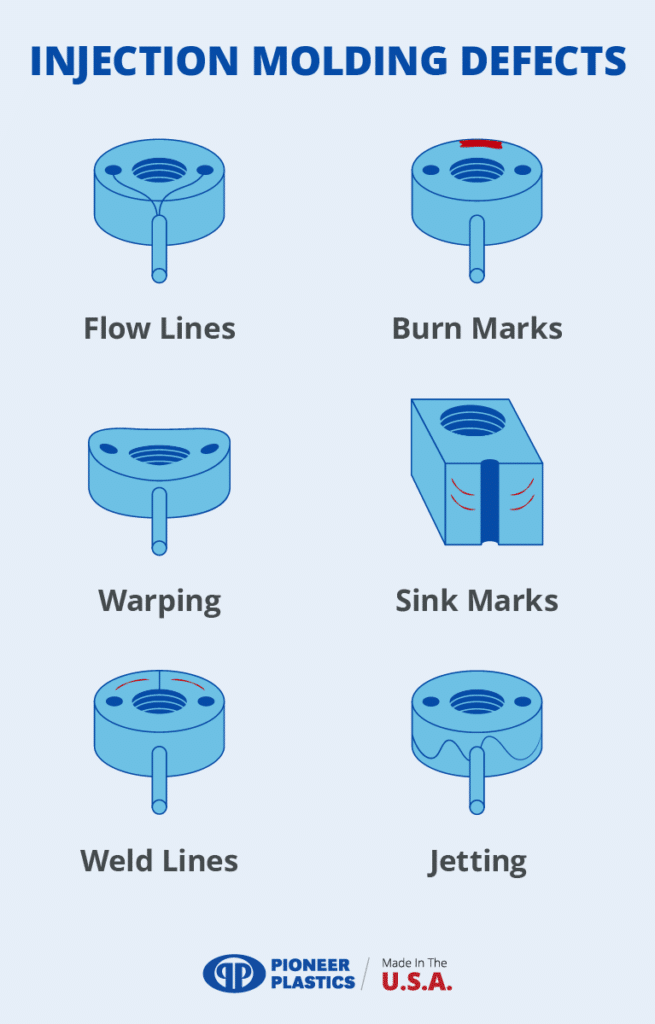
Flow Lines
Flow lines (sometimes called flow marks) are lines commonly caused by a variation in the cooling speed of the molten plastic as it flows through the mold. They often appear in a wavy pattern and might be a slightly different color than the rest of the piece. Flow lines don’t typically impact the integrity of the piece, but they can be unsightly and unacceptable in certain products (like high-end frames for glasses).
How to Avoid Them:
Flow lines can be avoided by increasing the injection molding speed and pressure to ensure the material fills the mold before cooling. You can also try rounding the corners of the mold to increase wall thickness and keep flow rate consistent.
Burns
Burns can be caused by trapped air or overheated resin in the mold during injection molding. Excessive heat or increased plastic injection molding speeds can cause overheating, in turn causing the resin to burn. Burns can appear as black or brown colored spots on the edge or surface of the part.
How to Avoid Them:
To prevent burns, lower the melt temperature and mold temperature to prevent overheating, reduce the injection molding speed to limit the risk of an air trap, and shorten the mold cycle time so that trapped air and resin doesn’t have time to overheat.
Warping
Most commonly heard when referring to wood that has dried unevenly, warping is an injection molding defect that appears when different components of the plastic part shrink unevenly. During the cooling stage of the molding process, uneven shrinkage can put stress on parts causing bending or twisting. Most often, the cause of warpage is the cooling process happening too quickly.
How to Avoid It:
Warping can be prevented by ensuring the cooling process is long enough to prevent uneven stresses on the material and by lowering the temperature of the plastic material or mold.
Sinking
Sink marks are depressions on an otherwise flat surface of a part. These can occur when the inner part of the injection molding shrinks (or cools too slowly), pulling the outside inward before it has a chance to completely cool.
How to Avoid It:
Increase the wall thickness of the part to reduce the possibility of sink marks. Use ribs and gussets to add strength to the product and improve cooling of the part, reducing the likelihood of sink marks. Use injection molding simulation software to optimize the mold and cooling designs before production, promoting even temperature distribution. Adjust cooling times and conditions to improve cooling speed and uniformity.
Air Pockets
Air pockets are trapped air bubbles in the finished part. Air bubbles are commonly caused by inadequate pressure to force air out of the mold cavity. Larger air pockets can weaken the part.
How to Avoid Them:
To avoid air pockets in the mold, raise the injection molding pressure to force out trapped air pockets. Modify the part’s design by adding draft, fillets, or ribs to the part to ensure material flows well and to avoid dead spaces where air can get trapped. Ensure that the resin is dried adequately before molding to avoid moisture from being trapped and forming air pockets.
Weld Lines
A weld line is a result of weak material bonding. They appear on the surfaces of parts where the material has come back together after splitting into two or more directions in the mold. If the material bonding is weak, the overall strength of the part is lowered.
How to Avoid Them:
Weld lines can be avoided by increasing the material temperature to prevent uneven solidification and increasing injection speed and pressure to limit cooling before the mold is filled.
Jetting
Jetting is a injection molding defect that occurs in a molded part when the initial jet of molten material starts solidifying before the rest of the material fills the mold. Jetting looks like squiggly lines on the surface of the molded product.
How to Avoid It:
Jetting can be avoided by reducing injection pressure (to prevent rapid movement of the material into the mold) and increasing material and mold temperature (to keep the material from solidifying too early).
While there are many injection molding defects that can occur, partnering with an experienced custom injection molder like Pioneer Plastics should relieve your worries.
If you have an idea for a plastic product and would like to partner with a company that has been manufacturing them for over 35 years, contact us today!
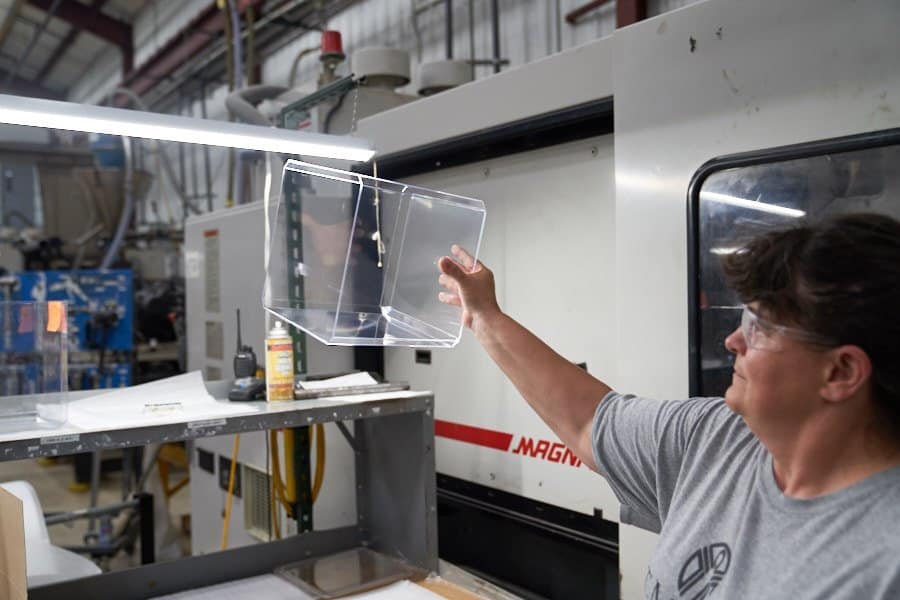