When designing your custom plastic part, it’s crucial to consider what the part’s fit and function will be.
First and foremost, the function of the product will affect the fit and form of the part in almost every case. So as you draw out your design, make sure you’re cognizant of its fundamental usage.
The Design & Discovery Process
What special properties need to be included to make your part stand out as more functional than potentially competing products?
Ask yourself these function-related questions:
- What is the minimum required strength required for your product to perform successfully?
- What is your product’s intended longevity?
- Does your product need to be created with impact resistance in mind?
These, among many other product-specific questions, should be answered before you worry about the style of your custom plastic part.
Answering these questions provides you with a better understanding of what type of resin should be used to manufacture your part.
Determining Your Product’s Fit
Now that you understand exactly what your part needs to do, you’ll need to figure out what it will look like, how it will feel, and how it will interact with other elements within the product’s environment.
The goal is to strive for optimal performance.
In this context, “Fit” refers to how a custom plastic part mates to another part or occupies a specified amount of cubic inches within a box or on a shelf. *
For Example:
- How a container lid mates to its container
- How the plastic housing envelopes a motor
- How the product occupies shelf space at Walmart
Some Tips for Perfecting Your Product’s Fit
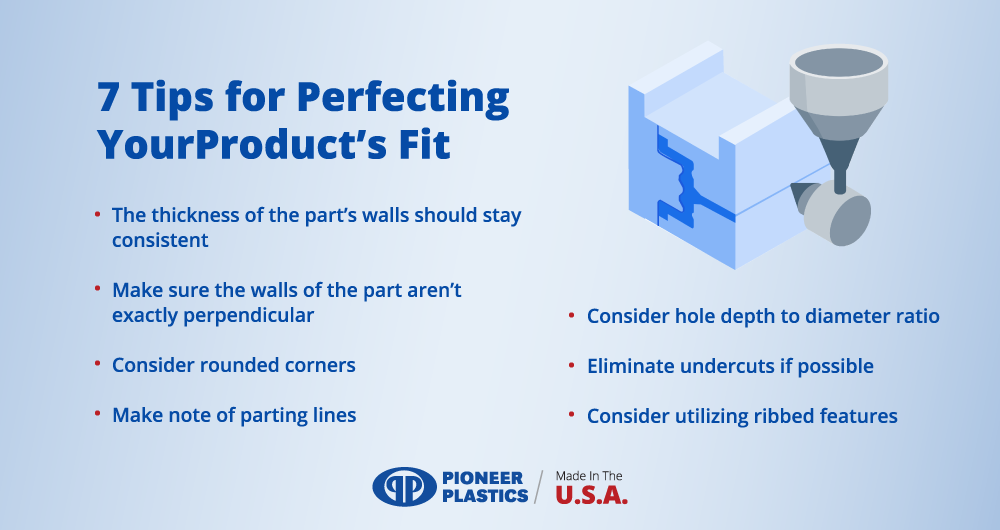
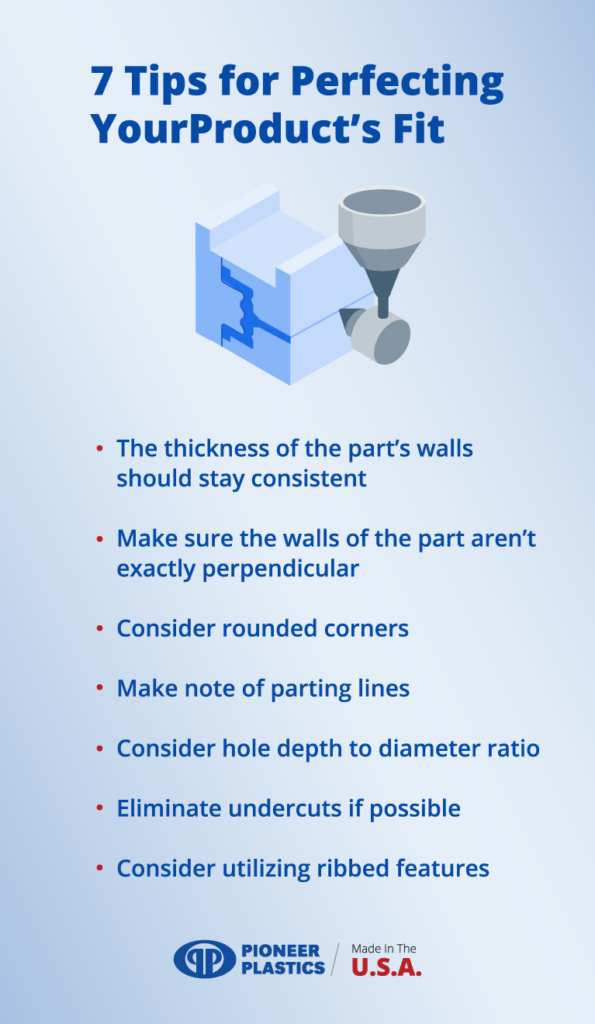
The thickness of the part’s walls should stay consistent whenever possible.
Inconsistencies in the wall thickness can cause the plastic to warp. When the plastic cools, it cools from the outside inward which can cause the outside walls to be pulled inward (called sinks), internal stress, or internal voids.
Make sure the walls of the part aren’t exactly perpendicular
This wall feature is called a draft angle. It allows the part to come out of the mold smoothly. We recommend a draft angle of between 2 and 5 degrees.
Consider Rounded corners
Rounded corners allow material to flow through the part more efficiently. This also reduces stress on the material during the cooling process, in turn reducing its tendency to crack, bow, warp, or have fragile corners.
Make note of parting lines
A parting line is a line where the two halves of the mold meet. This can create a thin blemish around the part depending on how it was designed. If you need a sharp edge on your part, you can reduce blemishes incorporating that edge in the parting line.
Consider hole depth to diameter ratio
Most plastics companies recommend the hole depth-to-diameter ratio to stay under two. There are two types of holes:
– Through Holes
– Blind Holes
Unlike through holes, blind holes don’t protrude through the part. The pins that are used to make these blind holes shouldn’t be too long, because the heat and pressure can potentially warp the insertion area.
Eliminate undercuts if possible
To save money, it would be wise to avoid using undercuts. Undercuts will almost always result in a more expensive part, due to a more complex mold design and typically more process time is needed to create them.
An undercut is any protrusion or indentation that houses any non-standard mating part of the plastic. (For example: A T-shaped connector)
Consider utilizing ribbed features
If you want to strengthen the molded part without adding additional wall thickness, ribbing is a great way to accomplish this. Taller ribs can lead to issues like warping and bending. But if your piece has subtle and simple ribbing, it should serve the function well.
Perfecting Fit & Function: The Case Studies
Panera Bread
Panera Bread brought a prototype of their newest food tray into Pioneer Plastics.
The complicated design prohibited proper stacking and was not nearly as user-friendly as it could have been. Sometimes a fancy appearance can have costly results.
After extensive testing with Pioneer’s new ergonomic design, we ended up solving the stacking issue while saving them $50,000 on mold cost!
The Inventor
An inventor brought in his custom plastic part that incorporated varied wall thicknesses. He didn’t understand that this inconsistency would cause shrinking and warping, hindering the product’s ability to be placed upright.
After redesigning the product to have consistent wall thickness throughout the whole piece, it streamlined and improved the whole injection molding process.
This redesign strengthened his invention and promoted product longevity, which was crucial since his goal was to get this product on retail shelves.
How to Design Your Custom Plastic Part For the Shelves of Walmart and Other Retailers
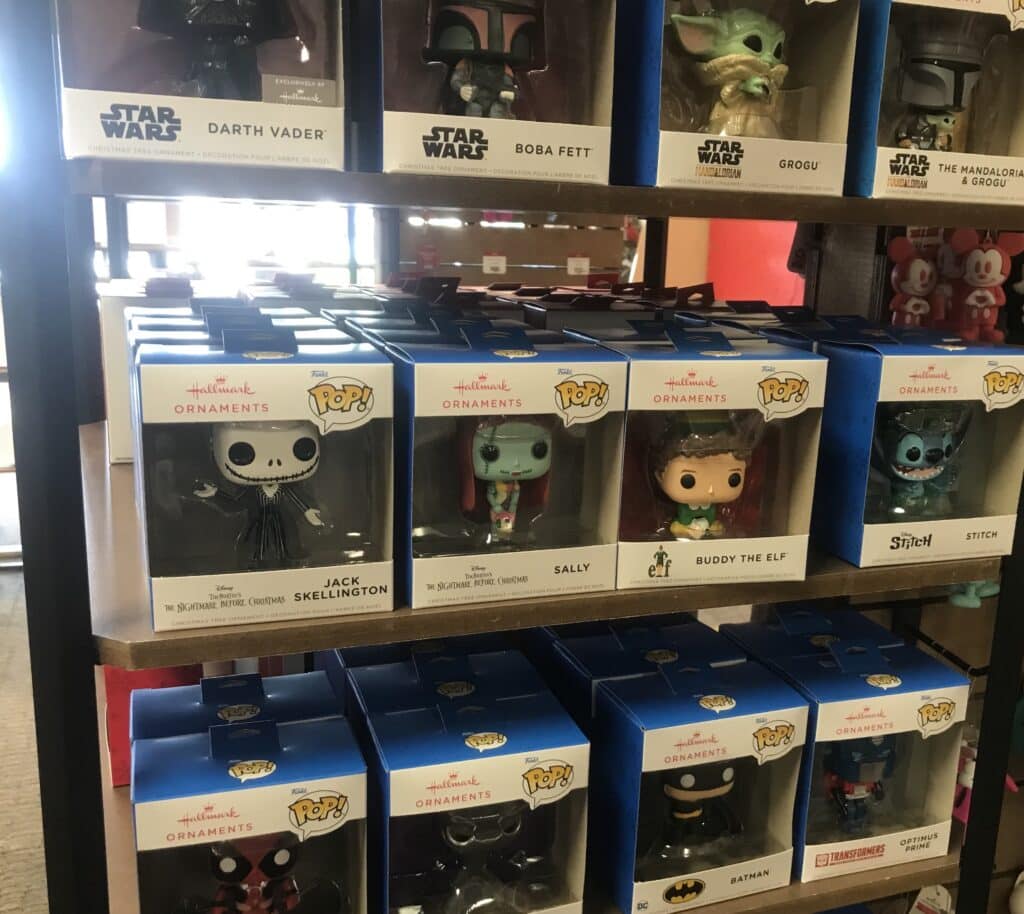
It’s all about the cubic inches.
Let’s say you own an ice cream company, and you’re hoping to modernize the ice cream container so that it increases user-friendliness and fits perfectly in the frozen section at Walmart.
You’ll need to design for a specific amount of shelf space.
It’s important to know that this shelf space allotted varies for each product type. For example, Walmart won’t accept a 10-gallon ice cream tub.
Your contact for any of these big box retailers will be able to provide you with the exact amount of cubic inches your product can occupy. Be careful, because if you don’t abide, they don’t have to stock your product.
Design Hint: You’ll need to understand the Supplier Standards, obtain a Universal Product Code (UPC), and you must carry Product Liability Insurance to sell your product in big box stores.
Also, you’ll need to notify your custom plastic part manufacturer that the retail market is your end goal!
Pioneer Plastics will be able to create exactly what you want with the custom injection molding process, but we might not be aware of the demographic you’re hoping to sell to unless you inform us.
Basically, you don’t want to spend thousands of dollars on a container that looks nice, functions well, but can’t be sold at any major retailer.
To ensure that your product is of high-quality and ready for manufacturing, be sure to design it with these practical tips in mind
Every custom plastic part is different. Some might need simple design tweaks, while others might need a complete overhaul. To get a quote on the production of your custom plastic part, contact Pioneer Plastics today!