Plastic components come in all shapes and sizes. While these parts might vary in terms of design or function, one very common need is the addition of color.
Numerous coloring methods have been developed over the years to create colorful plastic parts for a variety of industries—from industrial applications to the production of everyday household items.
In this blog post, we’ll delve deep into the fascinating process of coloring plastics. We’ll explore the factors that steer the selection of coloring methods, and how the color method can impact the final product’s properties.
In the end, you will have gained a comprehensive understanding of how custom plastic part companies use some of these methods to deliver high-quality, colored plastic parts.
So let’s get started on this colorful journey from raw material to finished product.
Color Psychology—The Impact of Color on the Final Product
Color can have a psychological impact on consumers. Different colors can help distinguish a product, align it with a brand’s identity, or even indicate a particular flavor or scent in the case of consumer goods, such as food packaging or cosmetics.
Certain colors can also evoke specific emotions or associations. For example, green is often associated with sustainability and nature, while blue can evoke feelings of trust and reliability. Therefore, understanding color psychology can be instrumental in shaping consumer perception and behavior.
This psychology is why color can significantly influence the aesthetic appeal of a product. It’s often the first thing consumers notice and can influence their initial perception, making it an essential element of product design.
For a couple of examples, a bright and vibrant color may be preferred for children’s toys to attract their attention, while subdued tones might be chosen for household items to blend well with home interiors or exteriors.
Aside from marketing and aesthetics, color in plastic products can also serve functional roles. For instance, colors can be used to denote different types or grades of a product, making identification easier. In safety equipment, bright, noticeable colors like red or yellow are often used to grab attention and signal caution.
The Role of Coloring in the Injection Molding Process
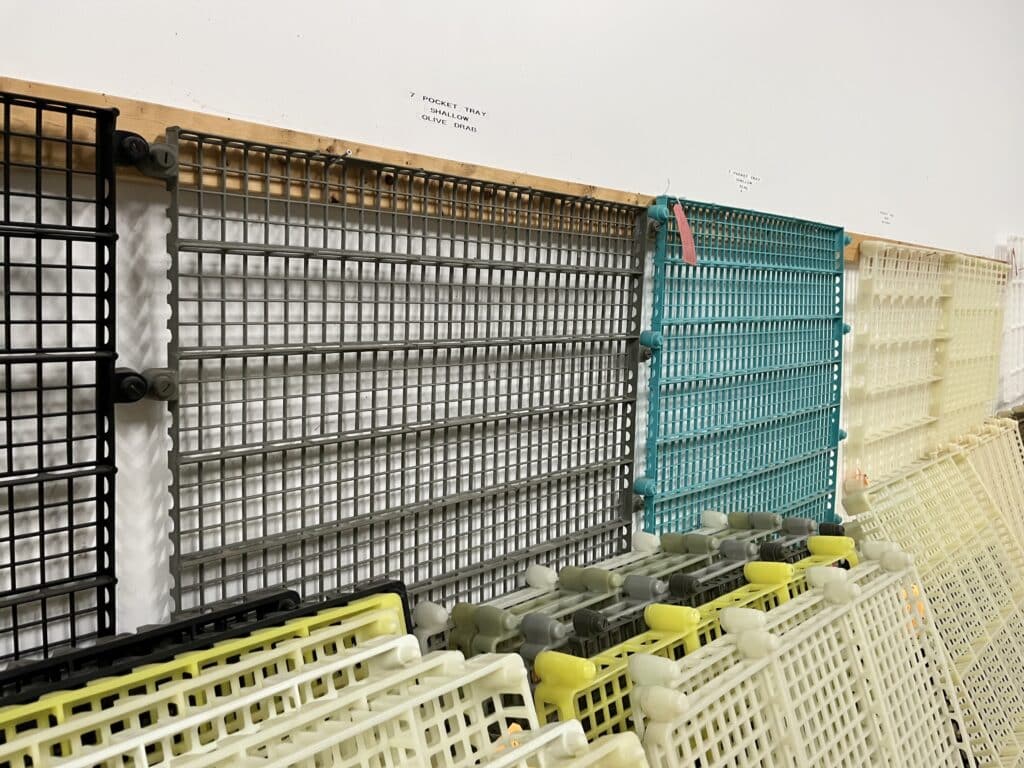
Plastic coloring is a crucial process in the manufacturing of plastic parts and products.
This procedure involves incorporating color into plastic materials, often to enhance their aesthetic appeal and marketability.
The choice of a coloring method is influenced by various factors. These include the type of plastic material being used, the desired color intensity, the production volume, and the specific application of the product.
For instance, food packaging requires the use of food-safe coloring methods, while outdoor applications may demand colorants with high UV resistance. Understanding these factors can help manufacturers select the most suitable coloring method for their particular needs.
The Impact of Color on Plastic Properties
The addition of colorants to plastics can have a direct impact on the final product’s physical properties, quality and even its performance. Some factors to consider include:
- Mechanical Properties: The choice of colorant and coloring method can affect the mechanical properties of the plastic, such as tensile strength, impact resistance, and flexibility. It is essential to select colorants that do not compromise the structural integrity of the plastic.
- Heat Resistance: Certain colorants can reduce the heat resistance of the plastic, making it more susceptible to deformation at higher temperatures. This is especially important for plastic parts that will be exposed to extreme temperatures.
- Chemical Resistance: The addition of colorants can also affect the chemical resistance of the plastic, making it more or less susceptible to discoloration or other damage when exposed to certain chemicals.
- UV Resistance: Certain colorants offer excellent UV resistance, making them suitable for outdoor applications.
- Colorfastness: The choice of colorant and color method can also affect the colorfastness of the plastic, or its ability to resist fading or discoloration over time. This is critical for products that are exposed to harsh environmental conditions or long-term use.
The coloring method used can have a direct impact on the final product’s physical properties, quality and even its performance.
10 Methods of Coloring Plastics
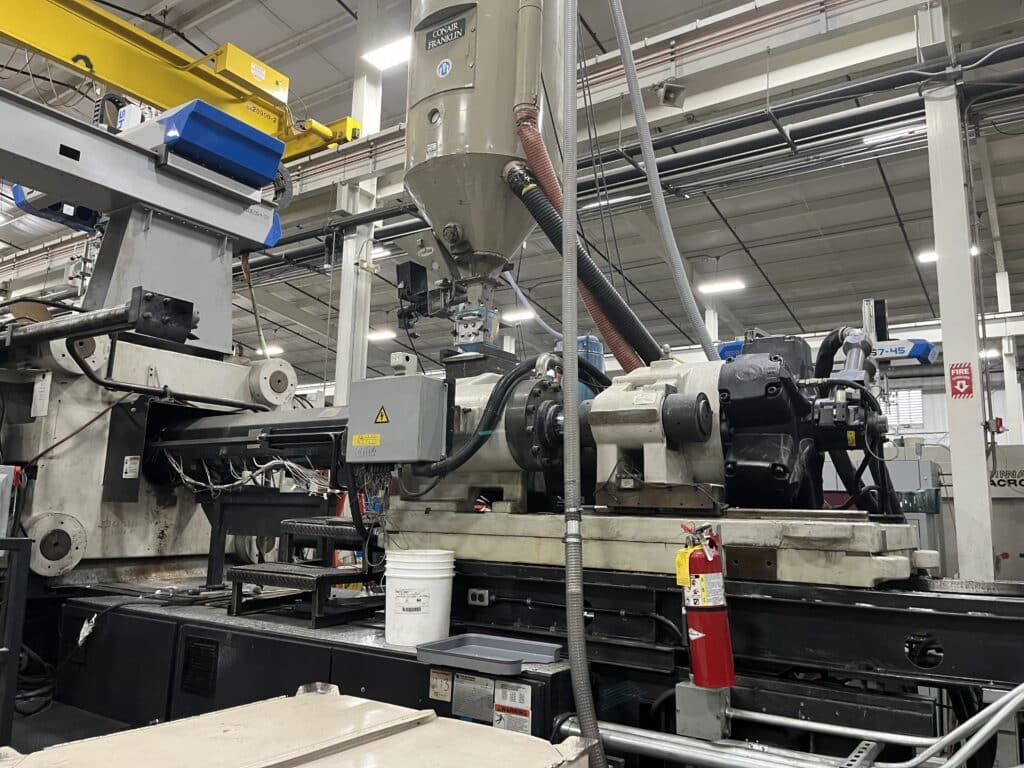
The coloring of plastics can be achieved through several methods, each with its unique benefits and considerations. During injection molding, the plastic granules and colorant can be either premixed as a homogeneous blend or pre-molded with color matching technology where colors are matched to exact specifications.
Let’s take a closer look at some of the methods used for coloring plastics:
1) Pre-colored Resin
This is a ready-to-use colorant option. This method eliminates the need for additional coloring steps and reduces production time, but it is typically the highest cost method as pre-colored resin is generally the most expensive. This is generally a method used for higher volume projects (hundreds of thousands of pounds).
2) Masterbatching
Masterbatching is a process where concentrated colorants are mixed with a carrier resin, creating a “masterbatch” that is then blended with the base resin.
This method is lauded for its versatility across various plastic types and its capacity to generate vibrant, uniform color.
3) Solvent Dyeing
Conversely, Solvent Dyeing involves dissolving dyes in a carrier solvent, which is applied to the plastic.
This method is particularly suitable for achieving translucent or transparent hues and is commonly used for coloring clear plastics such as polystyrene or acrylic.
4) Dry Pigment Blending
In this method, dry pigments are directly mixed with the plastic resin before processing. It is a simple and economical method, suitable for small-scale production or when a wide range of colors is required. However, achieving consistent color dispersion can be challenging, and it may require additional processing steps. This method isn’t used as often today as it is very messy.
5) Salt and Pepper Mixing
The raw material coloring method with cube blends, also known as “Salt and Pepper” mixing combines dry masterbatch and a natural polymer. This involves blending the colorant and plastic resin granules before the molding process and is normally used when there is no metering equipment available at the press.
Although this method might result in color variations in the final product, it proves cost-effective for large production runs, but does leave room for color variations.
6) Color Feeder
This method involves using a separate machine to continuously feed color pellets into the injection molding machine. This ensures consistent and uniform color throughout the production run, with minimal manual intervention.
This method is typically best suited for large production runs and offers a cost-effective solution for coloring plastics. It is considered the most common and ideal method for coloring plastics.
7) Hand Mixing
This method involves adding small amounts of colorant directly into the plastic material using a manual process.
This method is also very common and is usually most suitable for small production runs and is relatively easy to implement. However, it can be labor-intensive and not may not always yield consistent results.
8) Color Compounding
Color compounding involves mixing colorants with plastic resin to create a colored compound. This method offers flexibility in achieving specific color shades and properties. It is commonly used for engineering plastics or specialty applications where precise color control is required.
9) Liquid Coloring
Liquid coloring involves the use of liquid colorants, which are typically pre-mixed with the base resin or added directly to the molding machine. This method offers excellent color dispersion, cost-effectiveness, and ease of use. It is commonly used for small to medium production runs.
10) Coating or Painting
In some cases, plastics can be colored through coating or painting processes. This method is often used when intricate designs or special effects are desired. Coating or painting can provide a wide range of colors and finishes, but it can add to the overall cost and may require additional processing steps.
Overall, the choice of coloring method and its precise implementation can create significant differences in an end product. For example, using a masterbatching method ensures a more uniform distribution of color, while solvent dyeing might provide a range of vibrant color choices.
It is important to note that the choice of coloring method should be determined in collaboration with the custom injection molding company you choose to work with, taking into consideration factors such as the desired color, product requirements, and production volume.
If coloring is not done correctly, it can lead to issues like uneven color distribution, poor colorfastness, or even a change in the physical properties of the plastic. Choosing an injection molding company that has a wealth of experience and knowledge on which color methods work best is key to having a high-quality result.
Pioneer Plastics' Approach to Plastic Coloring
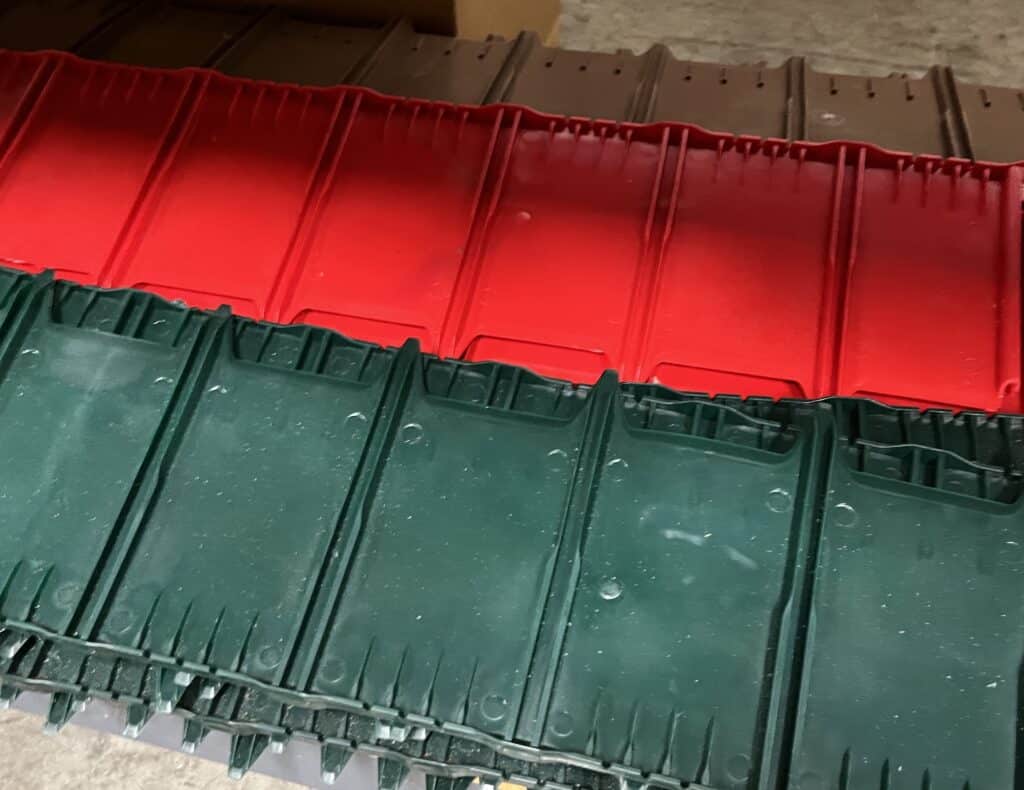
Pioneer Plastics leverages hand mixing and color feeder methods to achieve the desired hue and quality for each plastic component they produce. On occasion we also purchase pre-colored batches of resin depending on the scenario.
The choice of which method to use is influenced by factors such as the type of plastic, the product’s intended use, and the desired color intensity.
Quality control is key in our coloring process. Every batch of colored plastic undergoes rigorous testing to ensure color consistency and adherence to specifications. Pioneer Plastics utilizes advanced color-matching technology, ensuring that every plastic part matches the exact color requested by the client.
Apart from visual appeal, there is also a focus on the product’s performance. We ensure that the coloring process does not compromise the structural integrity of the plastic or its suitability for its intended use.
This balance of aesthetic and functional considerations exemplifies the expertise and attention to detail that Pioneer Plastics brings to every project.
Choose Pioneer Plastics for Your Colored Plastic Parts
As we have explored, the process of coloring plastics is a complex and nuanced one with a significant impact on the final product’s appeal, functionality, and overall performance.
At Pioneer Plastics, we have over 35 years of experience in the production and manufacturing of a wide variety of color-injected plastic components. Our longevity in the industry speaks volumes about our commitment to quality, customer satisfaction, and continual innovation.
We have a deep understanding of the plastic coloring process and leverage this expertise to provide high-quality colored plastic parts to our valued customers.
We are known for our rigorous quality control measures to create precise and consistent color in the plastic parts we create.
Contact Pioneer Plastics today to discuss your custom plastic part needs.