Achieving defect-free, high-performing plastic products requires precision and dedication at every production stage. In plastic injection molding, quality control is essential for ensuring that every part meets strict design and performance standards. By implementing thorough quality control measures from material selection to final packaging, manufacturers can reduce errors, minimize waste, and deliver exceptional products.
Pioneer Plastics, with over 60 years of industry expertise, underscores a strong commitment to quality assurance through meticulous procedures that aim to ensure high-performance outcomes. Their comprehensive quality control processes contribute to the production of custom plastic parts and a broad range of superior products for diverse industries.
In this article, we explore the four critical stages of quality control in plastic injection molding and explain how these processes lead to exceptional results for manufacturers, clients, and end-users alike.
Understanding the Plastic Injection Molding Process
Plastic injection molding is a precise manufacturing technique that converts raw plastic resin into finished parts. This process begins by heating the resin until it melts, then injecting it into a mold cavity. As the material cools and solidifies inside the mold cavity, it takes on the desired shape before being ejected as a final part.
Key factors, such as mold design, material properties, machine settings, and environmental conditions, impact the final product’s quality. Even minor variations in temperature or pressure can cause defects like poor surface finishes or dimensional inaccuracies. To counter these potential problems, manufacturers implement systematic quality control measures that catch and prevent issues early in the process.
Reputable manufacturers view quality assurance as a proactive practice that refines the process, reduces waste, and ensures durability and performance. For example, Pioneer Plastics has aligned its procedures with advanced manufacturing practices that support high-quality outcomes throughout production.
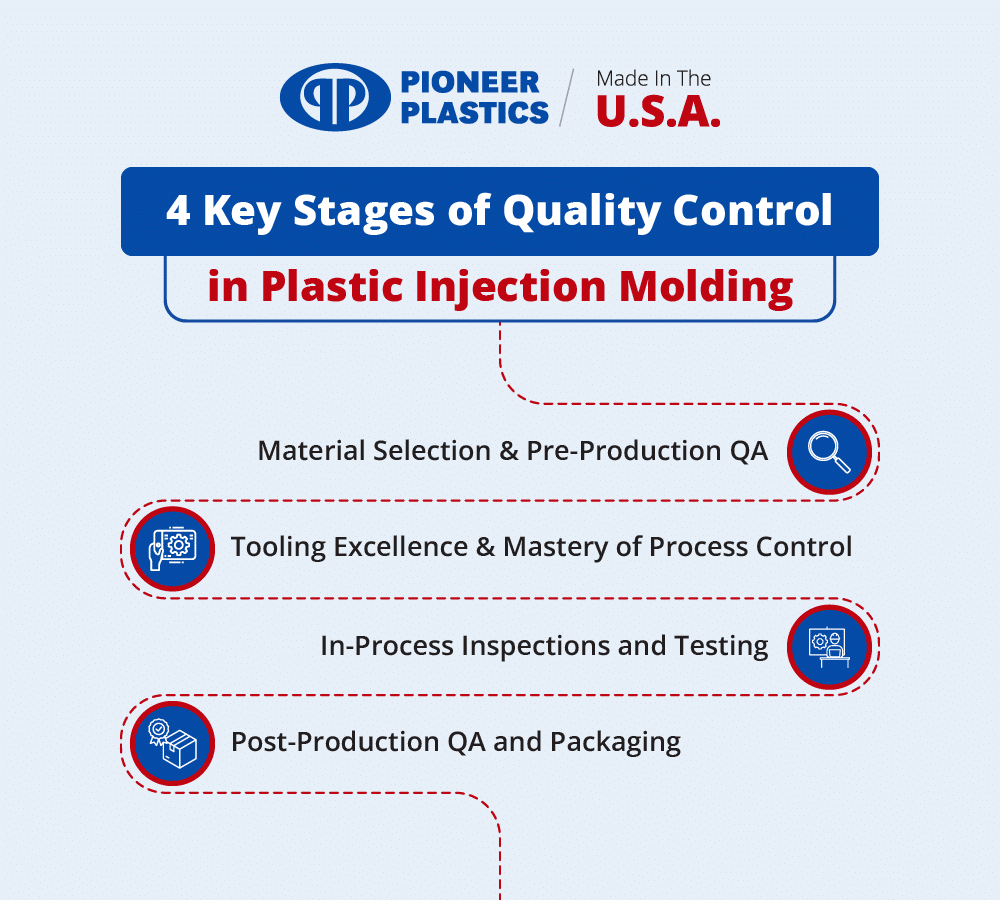
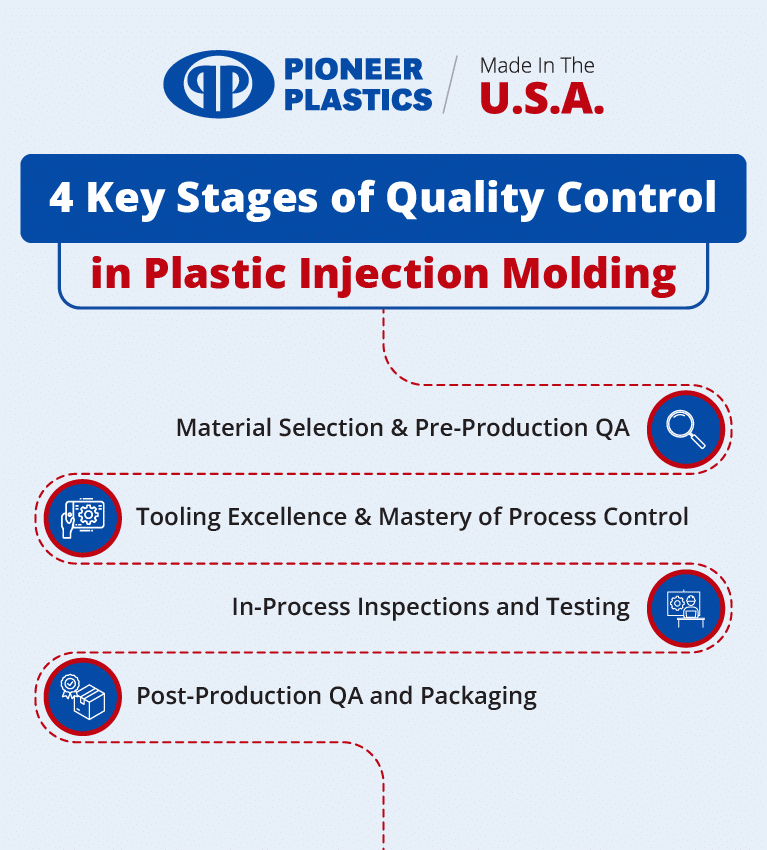
Stage 1: Material Selection & Pre-Production Quality Assurance
Why Material Selection Matters
The production of high-quality plastic parts begins with selecting the right raw materials, as material selection determines the functional and aesthetic properties of the final product. The chosen polymer must be durable, strong, and resistant to environmental conditions. For example, products used outdoors require materials that can withstand UV exposure and temperature extremes, while food-grade items must meet stringent safety standards.
Consistency in raw materials is also crucial. Metrics like the melt flow index—a measure of how easily a plastic melts—help manufacturers evaluate material performance. Procuring materials from reliable suppliers and performing rigorous tests ensures that the polymer remains uncontaminated and performs as expected.
At Pioneer Plastics, a strong emphasis is placed on the selection of high-quality, engineering-grade plastics as part of their production approach. Whether producing custom components or display cases, this careful material selection supports product reliability and longevity.
Pre-Production Testing and Inspections
Before production begins, comprehensive testing verifies that the raw materials meet design specifications. Pre-production tests, such as tensile strength assessments and thermal degradation analyses—including procedures like checking the melt flow index—help detect potential issues early.
Beyond raw material testing, the pre-production phase involves prototype and mold evaluations. At Pioneer Plastics, engineers conduct visual and dimensional inspections through prototype and mold evaluations to identify any inconsistencies in shape or color. This phase often includes direct collaboration with clients to ensure that custom requirements and proprietary materials are accurately integrated.
Addressing potential issues during pre-production lays a strong foundation for producing durable and flawless plastic parts.
Stage 2: Tooling Excellence & Mastery of Process Control
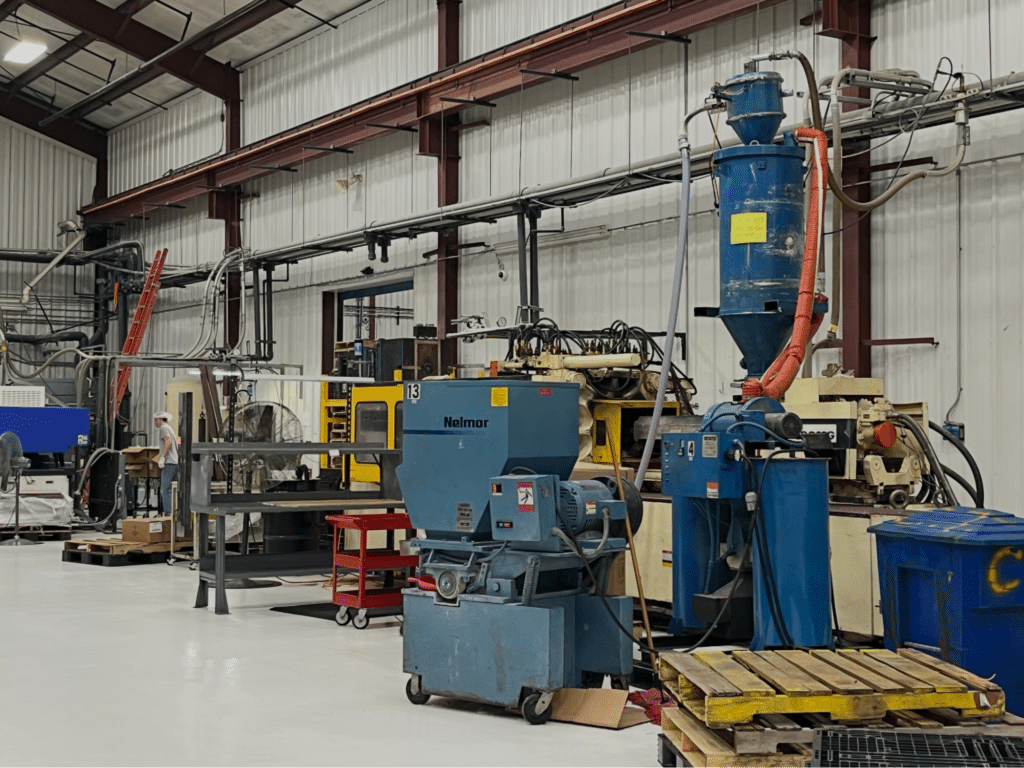
Precision in Tooling: The Foundation for Quality
The production of high-quality plastic products begins with creating precise molds. High-quality tooling is critical because it directly influences the dimensions and performance of the final product. A well-crafted mold minimizes issues such as warping, surface imperfections, or dimensional inconsistencies.
Tool building involves careful engineering to optimize material flow, cooling efficiency, and dimensional accuracy. Even a small error in mold design can lead to defects. Recognizing this, Pioneer Plastics handles tooling operations in-house, allowing rapid adjustments. If modifications in mold design or geometry are needed, changes can be implemented quickly, reducing delays and ensuring efficient production.
Mastering Process Control in Injection Molding
After the tooling is set, strict control over the injection molding process is essential. This process depends on several key variables—temperature, pressure, injection speed, and cooling time—all of which must be precisely regulated. Any deviation can result in issues such as sink marks, short shots, or flashing.
Advanced monitoring systems track these variables in real time. For instance, if a sensor detects a slight variation in cavity pressure, operators can adjust the injection pressure to correct the deviation. This blend of sophisticated technology and skilled management helps ensure that every part adheres to exact specifications.
Effective quality control is achieved when precision tooling and rigorous process monitoring work together seamlessly. A well-designed mold reduces production challenges, while diligent process control—governed by methodologies outlined in process control—helps maintain consistency from the first cycle onward. This integration minimizes waste, cuts production costs, and shortens lead times—benefits valued by both manufacturers and customers.
At Pioneer Plastics, the close integration of tool management and process control ensures that each custom plastic part meets high standards throughout production.
Stage 3: In-Process Inspections and Testing
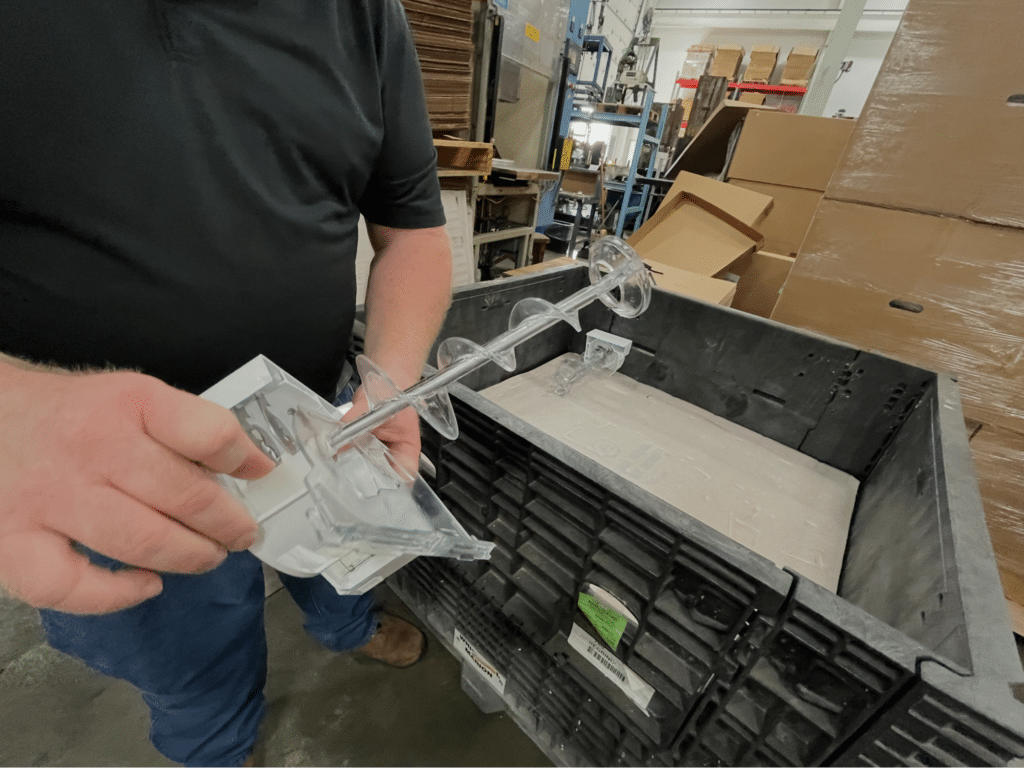
Quality control throughout production is a continuous, proactive effort. In-process inspections are essential for identifying and correcting deviations as they occur.
Real-Time Monitoring for Proactive Quality Assurance
Real-time monitoring systems are central to effective quality control. Automated vision systems, dimensional analysis tools, and material flow sensors continuously capture production data. For example, if a sensor detects a minor variation in part thickness, adjustments to injection pressure can be made promptly to correct the issue.
Regular visual inspections also play an important role. Imaging technology detects aesthetic issues such as flow marks or burns early on, prompting technicians to pause the production line and investigate further. This prompt intervention reduces widespread defects and minimizes material waste.
Ensuring Consistency in Every Run
Maintaining consistency is crucial—especially during high-volume production. Minor variations in color, shape, or texture can compromise overall quality. In projects where intricate details matter, an unwavering commitment to precision is essential.
At Pioneer Plastics, rigorous in-process inspections guided by advanced monitoring tools and expert oversight help guarantee that every product—whether from a large-scale run or a custom project—meets high-quality standards.
Stage 4: Post-Production Quality Assurance and Packaging
Final Inspections: The Last Line of Defense
Post-production quality assurance confirms that every product meets the required standards before reaching the customer. Rigorous final inspections include checks of dimensions, structural integrity, and overall performance. Products may also undergo functional tests and visual assessments for surface quality.
For specialized products—such as components for food or medical use—these inspections help ensure compliance with stringent regulatory standards. Pioneer Plastics carries out comprehensive evaluations to guarantee that each product fulfills customer requirements.
Packaging: Protecting and Presenting with Excellence
Packaging serves a dual role in quality control by protecting the product during transportation and by presenting it professionally. Secure packaging prevents damage during transit and storage while enhancing market appeal. Delicate items may require additional protective measures, such as cushioning or custom inserts.
Pioneer Plastics places a strong emphasis on robust packaging solutions. Each product is carefully inspected before shipment, ensuring it arrives in pristine condition. This attention to detail reinforces the high standards maintained throughout their production process.
Benefits of Comprehensive Quality Control
Incorporating comprehensive quality control in plastic injection molding processes not only strengthens a company’s reputation but also positively impacts the bottom line by enabling efficient utilization of resources. By focusing on the smallest details, manufacturers can consistently deliver exceptional products that meet or exceed industry standards. This methodical approach creates a competitive edge, positioning companies to seamlessly expand into new markets and offer more innovative solutions to their clients.
Effective quality control in plastic injection molding offers multiple advantages:
- Reduced Waste & Cost Savings – Early detection of defects minimizes material waste and reduces rework costs, resulting in overall savings.
- Increased Product Reliability and Longevity – The combination of thoughtful material selection and precise manufacturing practices helps ensure consistently durable, high-performing products.
- Faster Time to Market – Streamlined quality control reduces production errors, shortening lead times and accelerating market delivery.
- Enhanced Customer Satisfaction – Delivering reliable, defect-free products builds trust and fosters long-term customer relationships.
- Scalability – A comprehensive quality control system enables manufacturers to effectively handle both high-volume and specialized orders without sacrificing quality.
These benefits streamline operations and ensure that every product meets the highest standards of excellence, supporting Pioneer Plastics’ reputation as a trusted industry partner.
Pioneer Plastics’ Commitment to Quality and Excellence
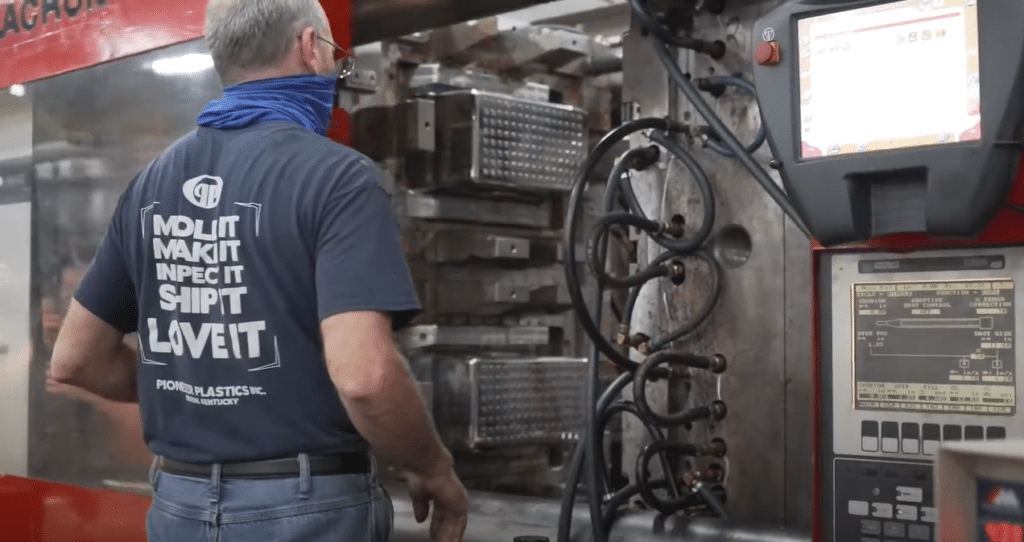
Quality is more than a promise—it is a core value embedded in every production step at Pioneer Plastics. With a fully integrated in-house manufacturing process, every phase from tool building to final packaging is closely monitored and regularly refined.
Employing a domestic “Made in USA” production model supports enhanced oversight across many production stages. This approach, combined with a focus on quality materials and advanced manufacturing practices, ensures robust control over the entire process. Whether crafting custom plastic components for industrial applications or designing refined display cases for collectors, Pioneer Plastics maintains rigorous standards that drive customer satisfaction across diverse industries.
Achieve Excellence with Pioneer Plastics’ Quality Control Practices
Achieving exceptional quality in plastic injection molding requires a strategic, comprehensive approach—from selecting high-standard materials and ensuring precision in tooling to applying thorough in-process inspections and meticulous post-production evaluations. These four critical stages form the backbone of a robust quality control system that guarantees every product meets high standards of durability, reliability, and performance.
Pioneer Plastics’ commitment to domestic production and advanced manufacturing practices underpins its focus on quality control throughout the process. Whether you need custom plastic parts for industrial applications, display cases for collectibles, or innovative injection molding solutions, Pioneer Plastics is dedicated to delivering excellence at every stage.
To learn how Pioneer Plastics can elevate the quality of your next project, contact Pioneer Plastics today and discover the benefits of partnering with a company that prioritizes quality control, precision engineering, and outstanding customer service.