In industries reliant on plastic components, the success of a project often hinges on the efficiency and precision of the manufacturing process. At the heart of this is strategic mold relocation—a critical step that involves relocating molds from one production facility to another. Whether driven by strategic realignment, capacity expansion, reshoring, or quality improvement, a well-managed transfer ensures smooth operations, consistent product quality, and maintained efficiency.
However, a mishandled transfer can lead to delays, production inefficiencies, and compromised product quality.
This article provides a comprehensive guide to the tool transfer process, outlining best practices, key considerations, and how Pioneer Plastics, with over 40 years of expertise, supports successful transfers.
Understanding Tool Transfer: What It Is and Why It Matters
Production tool transitions involve relocating a mold, along with its documentation and components, from one injection molding company to another. This process allows companies to adapt to changing needs, political issues (i.e. tariffs), reduce costs, or partner with specialized manufacturers. Given the significant investment in injection molds, ensuring a controlled transition is essential to maintain product consistency and quality.
A carefully executed transfer minimizes risks by safeguarding mold integrity and aligning production processes with the new facility’s standards. It also opens the door to improved lead times and access to advanced production techniques. In some cases, the transfer can serve as an opportunity to upgrade molds or incorporate new design features that can enhance overall production performance.
Beyond the immediate logistics, understanding the nuances of production tool transitions can help businesses future-proof their manufacturing processes. When performed correctly, it can extend the life of existing tools, optimize production cycles, and even reduce long-term operational costs.
Factors to Consider Before Starting a Tool Transfer
A successful mold transfer requires thoughtful preparation. Key considerations include:
Assess the Mold’s Condition
Conduct a comprehensive evaluation of the mold to identify any wear, damage, or inconsistencies. A pre-transfer assessment prevents unexpected maintenance and ensures optimal performance once production resumes. This step also offers a chance to plan any necessary refurbishments or upgrades that might enhance tool longevity. Pioneer Plastics is willing to do the assessment and handle any mold repairs to ensure efficient production.
Confirm Compatibility with the New Facility
Verify that the mold is compatible with the new facility’s equipment. Differences in press sizes, cooling systems, and auxiliary equipment may require modifications such as updated fittings or adjusted gate systems. In situations where compatibility issues are identified early, minor adjustments can often be made before the mold is moved, reducing the risk of production delays.
Plan for Production Timelines and Logistics
Develop a clear timeline to coordinate disassembly, transportation, installation, and setup. Planning for key steps like testing and validation minimizes production downtime. Consideration should also be given to seasonal production peaks so that the mold transfer can be scheduled during periods of lower production demand.
Gather Documentation and Historical Data
Assemble records including cycle times, material specifications, processing parameters, and maintenance logs. Comprehensive documentation enables the new partner to replicate successful outcomes and troubleshoot effectively. This historical data is invaluable for understanding the nuances of the current production process and maintaining product consistency post-transfer.
Clarify Intellectual Property and Ownership Terms
Address any IP or contractual concerns before the transfer to avoid legal disputes or delays. This is particularly important when transferring molds that have been subject to proprietary manufacturing techniques or are part of a larger supply chain network.
By addressing these factors upfront, businesses can set a solid foundation for a smooth mold transfer project and minimize potential disruptions in the manufacturing workflow.
Key Steps to Execute a Successful Tool Transfer
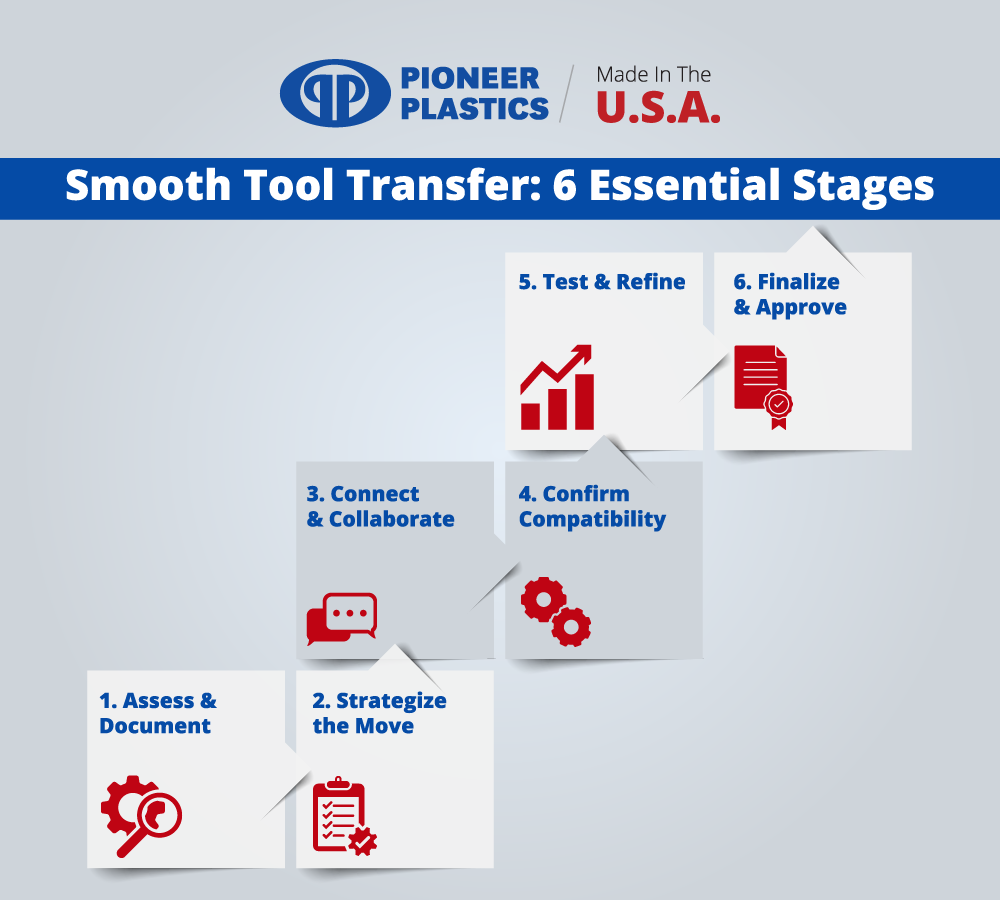
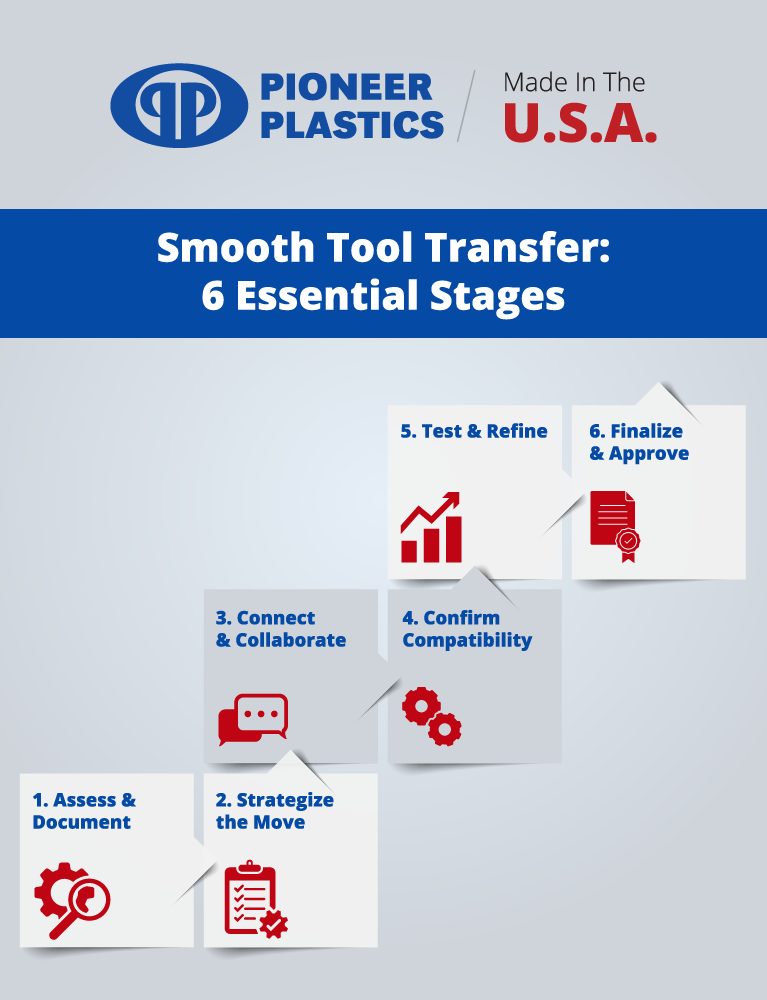
A meticulous and coordinated approach is essential for a successful tool transfer. Follow these steps:
Conduct a Detailed Tool Audit
Begin with an evaluation of the mold’s cavities, cores, parting lines, water lines, hydraulic fittings, and other critical components. Document maintenance history and update engineering files to provide the new partner with an accurate condition report. This audit ensures that no hidden issues are overlooked during the transition.
Create a Comprehensive Transfer Plan
Develop a step-by-step strategy that outlines disassembly procedures, packaging requirements, shipping logistics, and responsibilities at both facilities. Include contingencies for potential delays or damage during transit. Consulting skilled toolmakers on integrated tooling solutions can offer ideas for streamlining these procedures. A detailed plan should incorporate timelines for each task and assign accountability to ensure nothing is missed.
Ensure Open Communication Among Stakeholders
Establish clear communication channels between the existing and new partners. Share documentation such as CAD files, maintenance logs, and processing parameters. This alignment helps set expectations and promptly resolve issues during the transfer. Regular meetings, both prior to and during the transition, can foster transparency and collaborative problem-solving.
Validate Tool Compatibility
Before the transfer, confirm that the mold meets the new facility’s specifications. Address any modifications needed for proper integration with the machinery and support systems. Compatibility checks reduce setup delays and ensure seamless production.
Perform Testing and Trial Runs
After installation, conduct trial runs to verify that the mold produces parts meeting quality standards. Evaluate aspects such as dimensional accuracy, surface finish, and cycle times. Continue test runs until consistent, high-quality results are achieved. This phase is crucial for identifying any lingering adjustments that must be addressed before full-scale production resumes.
Document and Sign Off on Final Approval
Once testing confirms performance standards, update all relevant documentation and secure formal approval from engineering and quality control teams. This final sign-off ensures that the mold is ready for volume production and mitigates any risks associated with rushed transitions.
Challenges in Tool Transfer and How to Overcome Them
Even with careful planning, tool transfers can face challenges that must be managed proactively:
Physical Damage and Incompatibility
Molds are heavy and intricate, making them vulnerable to damage during transit. Partnering with experienced logistics providers and conducting pre- and post-shipment inspections can reduce the risk of damage or compatibility issues. Advanced cushioning and custom crating solutions often provide additional protection during the move.
Incomplete Documentation
Missing records can slow down the setup process. Ensure all available documentation is gathered beforehand, and work with existing partners to fill gaps in records to aid in rapid tuning at the new facility. Developing a digital repository for such documentation can facilitate easy sharing and future transfers.
Production Downtime
Disruptions can impact schedules and revenue. Mitigate downtime by planning transfers during non-peak periods, building buffer stocks, and establishing contingency plans for unforeseen delays. Allocating additional resources during the initial weeks of production at the new facility can help overlap timelines and reduce impact.
Material or Process Variations
Switching partners may introduce differences in materials or processing techniques. Run compatibility tests and adjust molding parameters as needed to prevent quality issues like warping or dimensional errors. Regular cross-checks with material suppliers and process engineers can minimize these variations effectively.
Regulatory and Compliance Issues
Ensure that the new facility meets all industry-specific standards. Sharing relevant documentation and performing additional audits can avoid compliance gaps during the transfer. Engaging with third-party inspectors or certification agencies may sometimes be necessary to validate compliance before production resumes.
By anticipating these challenges and implementing targeted strategies, businesses can significantly reduce risks and ensure a seamless mold transfer.
Choosing the Right Partner for Tool Transfer and Beyond
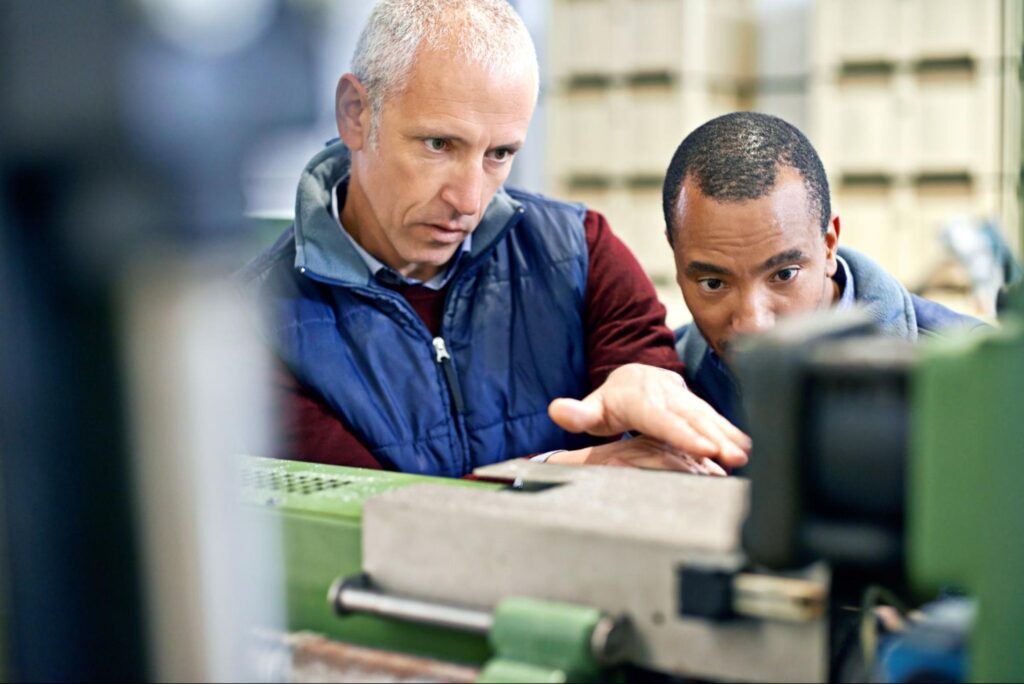
Selecting an experienced injection molding partner is critical. When evaluating potential partners, consider the following factors:
Expertise in Tool Transfer and Custom Injection Molding
Look for a track record of managing successful transfers. A partner with a deep understanding of logistics, compatibility checks, and process validation will streamline the transition and ensure high-quality production. Their experience should also extend to handling unique challenges across different production volumes and product types.
In-House Tooling and Engineering Capabilities
Partners with internal tool and engineering teams can address issues swiftly, reducing reliance on external vendors. This in-house expertise is vital for timely adjustments and repairs during the transfer process. The ability to provide on-the-spot engineering support can greatly accelerate the ramp-up to full production.
Flexibility, Scalability, and Quality Focus
Choose a partner that can accommodate varying production volumes and maintains robust quality control systems. Transparent communication and ongoing support throughout the process are essential. Additionally, the partner should be proactive in suggesting improvements that not only resolve immediate challenges but also enhance future production efficiency.
Pioneer Plastics stands out with over 40 years of experience, comprehensive in-house capabilities, and a strong industry reputation for precision and reliability. Their balanced approach to innovation and quality ensures that every tool transfer is smooth and tailored to the client’s needs.
Steps to Prepare for a Smooth Production Transition
Preparing internally to get a quote and to prepare for a tool transfer minimizes downtime and maintains quality. Key steps include:
Gather and Organize Documentation
Collect all relevant engineering files, CAD models, maintenance logs, and production records. Detailed documentation enables the new partner to quickly understand your mold’s history and specifications, facilitating a faster operational start.
Assess Production Needs and Build Buffer Stock
Evaluate your production schedule to anticipate any disruptions. Build a buffer stock of molded parts to meet customer demand during the transition. This proactive measure can prevent supply chain interruptions and ensure customer satisfaction. In cases involving food or beverage packaging, consult FDA guidelines for food-grade plastics for compliance considerations.
Define Performance Expectations
Set clear performance goals for the mold in its new environment. Outline key metrics such as tolerances, cycle times, and material properties to ensure the new setup replicates your quality standards. Clearly defined objectives help in monitoring success during trial runs and production ramp-up.
Create a Detailed Transition Timeline
Develop a timeline with milestones for disassembly, transportation, setup, testing, and final approval. Build in extra time for any necessary adjustments to keep the process on track. This structured timeline acts as a roadmap for all stakeholders, ensuring that every phase of the transition is well-coordinated.
Plan for Post-Transfer Testing
Coordinate with your new partner to schedule trial runs and validate mold performance. A rigorous testing phase is critical to catch any issues before full-scale production begins. Regular feedback sessions during this phase help fine-tune operations, ensuring that any discrepancies are addressed promptly.
Advanced Considerations for Optimizing Your Tool Transfer Process
For companies aiming to push the boundaries of efficiency, advanced planning methods and technology integration are key. Consider these additional strategies:
Embrace Digital Tooling and Simulation
Modern digital simulation tools allow engineers to virtually test a mold’s performance before it reaches the new facility. By incorporating digital twin technology, companies can simulate changes in processing parameters and predict potential issues in a risk-free environment.
Implement Robust Quality Control Measures
Beyond pre-transfer audits, integrating continuous quality monitoring systems during and after tool transfer adds an extra layer of assurance. Real-time data collection can alert operators to any deviations, enabling immediate corrective actions.
Strengthen Team Collaboration with Integrated Software
Invest in collaborative project management software designed for manufacturing. These systems can help synchronize tasks between different teams, track progress, and ensure that every member is informed of updates or issues in real time. Such collaboration minimizes miscommunication and enhances overall efficiency throughout the transfer process.
Leverage Expert Consultations and Continuous Improvement Programs
Engage industry experts periodically to review transition strategies. Their insights can uncover areas for improvement and optimize workflows. Additionally, establish a continuous improvement program that gathers feedback from every tool transfer to refine and standardize processes for future operations.
Integrating Advanced Technologies in Tool Transfer
Embracing advanced technology is not only about digital simulations; it is also about integrating the latest machinery and automation. New robotic systems for mold handling and disassembly can reduce human error and accelerate the transfer process. Automation in quality control, using visual inspection systems or advanced sensors, ensures that transferred molds meet strict quality standards before production restarts.
Cutting-edge technology enables a more predictable and customized tool transfer experience. For instance, integrating AI-driven analytics can help predict potential issues during the transfer, from timing delays to process variations. These proactive insights allow companies to implement contingency measures in advance, ensuring minimal disruption and optimal production performance. Aligning such processes with recognized quality standards, such as ISO 9001 certification importance in manufacturing, can further bolster reliability.
Monitoring and Continuous Improvement in the Production Process
The tool transfer process does not end once the mold is installed; ongoing monitoring is essential. Establish key performance indicators (KPIs) that track production quality, downtime, and efficiency immediately after the transfer. Regular review meetings with the production team can uncover insights that lead to further optimization. Implementing measures recommended by EPA guidelines on sustainable manufacturing can also help maintain eco-friendly practices alongside operational improvements.
Continuous improvement efforts, including periodic audits and adjustments, help maintain high standards over time. Leveraging feedback from trial runs and early production cycles ensures that any unexpected issues can be quickly resolved, setting up the production line for long-term success.
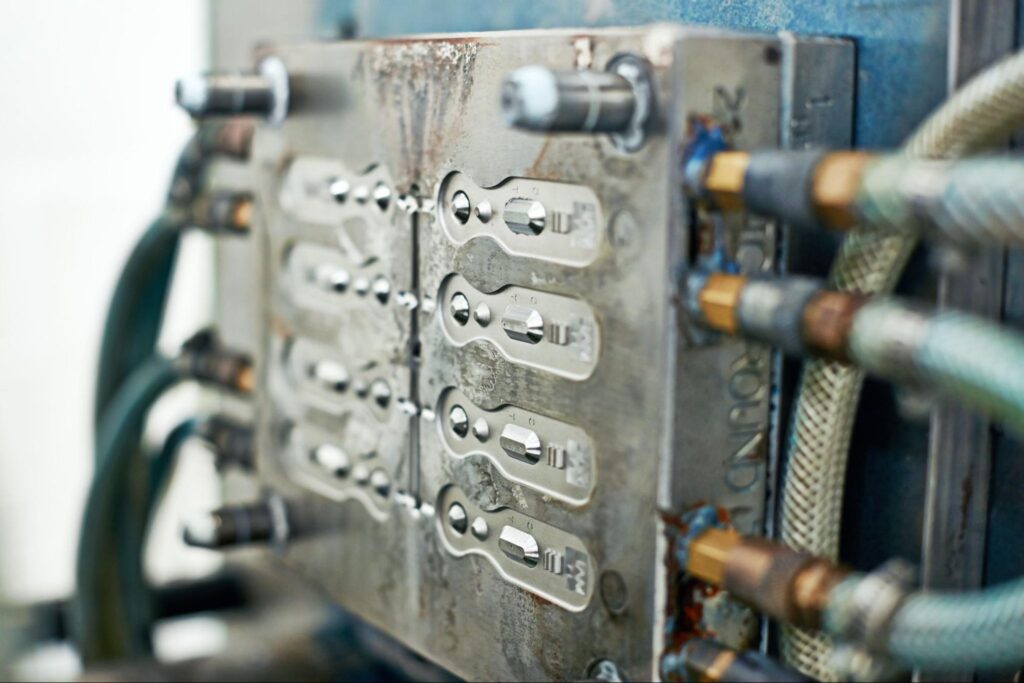
Ensuring Successful Outcomes with Careful Tool Transfer Strategies
Successfully transferring injection molding tools requires thorough planning, attention to detail, and collaboration with the right partner. A well-managed transfer improves production quality, streamlines operations, and sets the stage for long-term success. From evaluating the mold’s condition to coordinating logistics and integrating advanced technologies, every step is critical to a seamless transition.
Pioneer Plastics, with its 40+ years of expertise, comprehensive in-house capabilities, and robust tool management and development capabilities, simplifies the process and minimizes downtime. Their focused approach ensures that your production remains consistent and efficient during complex transitions. If you’re ready to move forward with a tool transfer or have questions about injection molding services, contact us to get started.