Selecting a reliable custom injection molding partner goes far beyond a simple procurement decision—it lays the foundation for product success and business growth. Whether you are a large enterprise or an innovative entrepreneur, finding the right partner is critical. A top manufacturer not only produces high-quality parts but also becomes a strategic ally through tailored guidance, rapid turnarounds, and unwavering support.
The following sections outline the key traits that define a superior injection molding partner and provide practical insights to help you make an informed decision.
Importance of Choosing the Right Plastic Injection Manufacturer
Choosing the best injection molding manufacturer is essential for ensuring quality, efficiency, and reliability at every production stage. A subpar partner can lead to poor craftsmanship, delayed timelines, and miscommunications that may jeopardize your project.
In contrast, a top-tier manufacturer offers expert advice on material selection and design optimization. They streamline processes and foster long-term relationships that transform production challenges into opportunities. This careful selection not only saves time and reduces costs but also ensures your product stands out in a competitive market.
Expertise and Industry Experience
A manufacturer’s deep industry experience is a cornerstone of reliability. With exposure to diverse sectors, seasoned professionals are well-equipped to handle complex projects and swiftly resolve design challenges. They apply advanced methods to minimize waste and boost efficiency, ensuring even the most intricate components benefit from precision engineering.
This accumulated knowledge means that potential issues are often anticipated before production begins, resulting in fewer delays and a higher degree of predictable quality. As a result, experienced manufacturers innovate continually, delivering solutions that meet exacting customer requirements.
Versatility in Services Provided
A leading injection molding manufacturer offers a comprehensive suite of services that guide your project from concept to completion. This versatility ensures that you have everything needed under one roof, fostering synergy across different stages of development. From design refinement to prototype development, and full-scale production, they manage the entire workflow seamlessly. With the ability to adapt quickly to design changes and fabricate custom molds in-house, they not only control quality more effectively but also significantly reduce lead times and costs.
- Custom Injection Molding: Refine designs for optimal manufacturability, select high-performance materials for enhanced durability, and develop prototypes that set the stage for mass production.
- Tool Building Capabilities: Design and fabricate custom molds in-house while quickly adapting to design changes, reducing turnaround times.
- Engineering Support: Provide technical insights to review and refine product designs. Proactive engineering support ensures parts meet stringent strength and functionality standards.
By centralizing these capabilities, top manufacturers simplify communication, reduce lead times, and enhance overall operational continuity.
Advanced Manufacturing Capabilities and Technology
Staying at the forefront of technology is crucial in today’s competitive market. Top manufacturers use modern design and simulation tools—such as plastic injection molding software—to perfect product designs and predict material behavior. Meanwhile, automation and rigorous quality control systems improve consistency while reducing human error. Sensors and immediate feedback mechanisms help detect deviations early, preventing costly rework.
These advancements not only boost accuracy and efficiency but also lower production costs, giving your business a distinct competitive edge. Manufacturers embracing such innovations are better equipped to integrate sustainable practices, ensuring every component meets functional and environmental standards.
High Standards of Quality Assurance
Quality assurance is at the heart of successful injection molding. Rigorous checks and precision measurement tools help ensure every product meets exact standards. By selecting high-grade materials and adhering to standardized processes, manufacturers minimize variability and reduce waste.
This systematic approach builds trust, reinforcing that products will perform reliably throughout their lifecycle. Consistent quality is vital for establishing long-term partnerships and a reputation for excellence.
Adaptability and Customization Capabilities
In a fast-changing market, flexibility is essential. Top manufacturers efficiently manage everything from low-volume prototypes to high-volume production runs. They adapt quickly to design modifications, material changes, or evolving project requirements, ensuring your product remains on track despite unexpected challenges.
Whether your project demands a specialized finish or an unconventional design, an adaptable manufacturer will provide custom solutions aligned with your specific goals. For instance, some manufacturers, such as Pioneer Plastics’ wide range of products, have successfully created custom solutions for various markets including collectibles, household containers, and display cases. This versatility not only supports product uniqueness but also fosters innovation during product iterations, creating a collaborative partnership that meets or exceeds expectations.
Responsiveness and Customer-Centric Approach
A customer-first mindset paired with effective communication is crucial for a successful manufacturing partnership. Reliable manufacturers keep you informed with regular updates and ensure access to support channels that swiftly address your concerns.
Transparent and proactive communication builds trust and long-term loyalty. Real-time adjustments, based on ongoing dialogue, further ensure each stage of production aligns with your vision. This approach reduces friction, provides peace of mind, and ultimately leads to higher-quality outcomes.
Manufactured in the USA: Why It Matters

Partnering with the U.S.-based injection molding manufacturer can offer certain advantages. Many domestic companies have dedicated quality practices and adhere to local regulatory requirements, and being in the same time zone or cultural context can facilitate communication; however, the specific benefits—such as lead times and logistics reliability—can vary from one manufacturer to another. It is important to evaluate each partner on a case-by-case basis.
Proven Track Record and Client Satisfaction
A strong history of client satisfaction is a powerful indicator of a manufacturer’s capability. Reputable partners showcase positive testimonials and a diverse portfolio that spans multiple industries and specialized sectors. Long-standing collaborations and repeat business underscore their commitment to excellence.
Reviewing success stories provides confidence that your project will receive careful attention. Established manufacturers back their reputation with documented achievements, demonstrating a consistent ability to deliver products tailored to client needs.
Environmental Responsibility and Sustainability
Modern consumers and businesses increasingly value sustainability. Leading manufacturers respond by implementing eco-friendly practices—optimizing material usage, reducing waste, and employing energy-efficient production processes. Adopting greener manufacturing processes can reduce operational costs and help meet environment-friendly regulations.
While these efforts can also help companies meet evolving environmental expectations, they primarily underscore a commitment to both quality production and environmental stewardship. By merging sustainability with high-quality production, manufacturers position themselves as innovators in both fields. This commitment strengthens relationships with eco-conscious clients and contributes to broader environmental goals.
Future Trends in Injection Molding
The injection molding industry continues to evolve as more manufacturers embrace digital transformation. Advanced technologies that connect manufacturing processes—such as real-time monitoring and data analysis—enable organizations to refine production parameters and predict maintenance needs seamlessly.
Innovations in materials also play a critical role. The emergence of new polymers, including more eco-friendly bioplastics, sparks changes in design and manufacturing. The synergy between design teams and production personnel will become increasingly vital as these tools and materials mature, pushing the industry toward greater efficiency and creativity.
Navigating Industry Challenges: Collaboration and Continuous Improvement
Market variables like fluctuating raw material costs, evolving regulations, and increasing demands for customization require agile responses. Manufacturers that invest in process improvements and advanced training programs can better handle these pressures.
Collaboration between manufacturer and client is especially valuable here. Open feedback channels and iterative designs ensure efficient adaptation to changing conditions. By aligning technical expertise with flexible management practices, manufacturers can innovate quickly and mitigate risks, keeping production on schedule even in uncertain market conditions.
Selecting the Right Partner: Practical Tips
Choosing the right injection molding partner requires a combination of strategic evaluation and due diligence. As you explore potential manufacturers, ensure they align with your business goals and values, positioning them as an extension of your team rather than just a vendor. Additionally, assessing their innovative capabilities and commitment to continuous improvement will provide insights into their ability to adapt to future challenges. These considerations not only impact production efficiency but also influence the overall success and sustainability of your projects.
When evaluating potential manufacturing partners, consider these actionable tips:
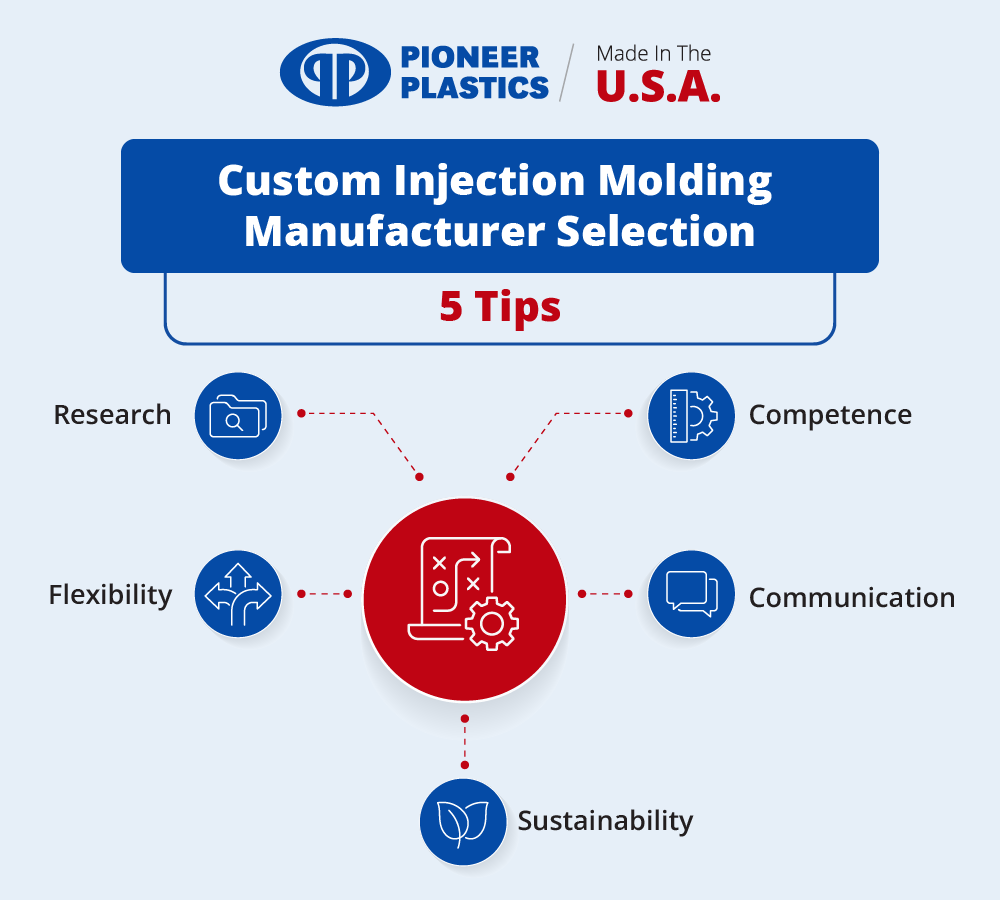
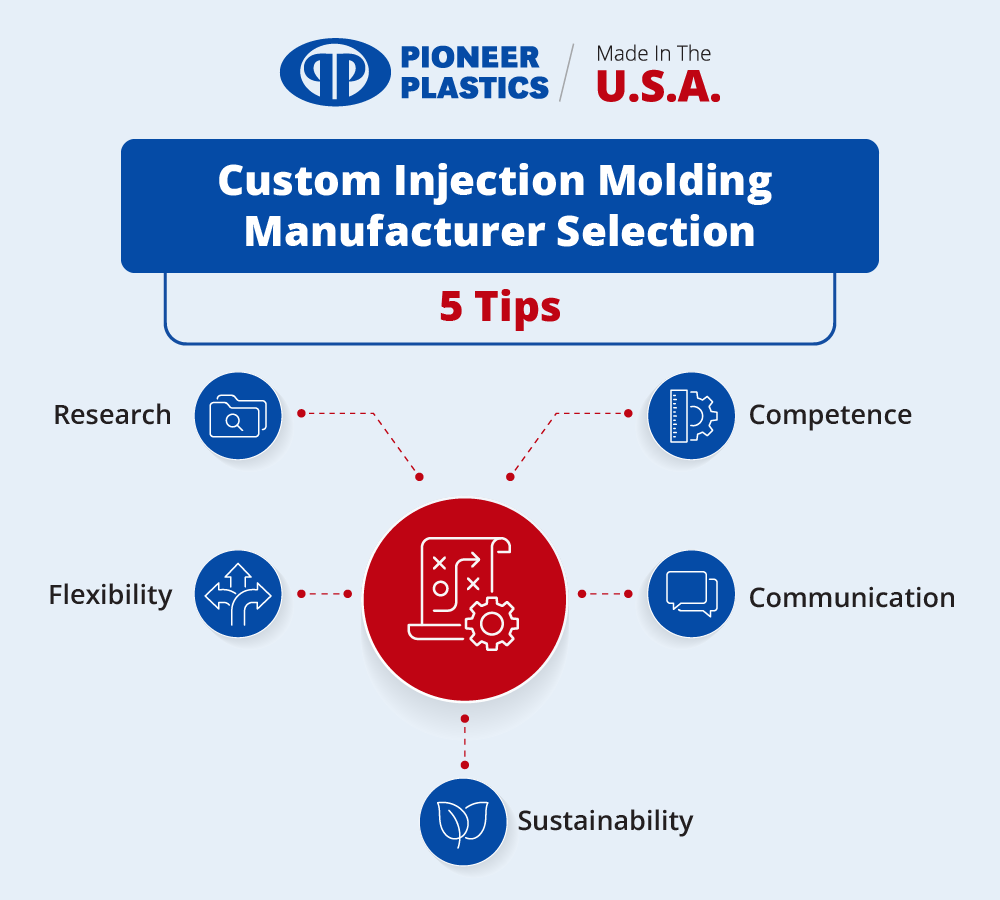
- Conduct thorough research: Look at portfolios, certifications, and testimonials to gauge strengths in quality control and technology.
- Assess technical competence: Ask about their manufacturing technologies and engineering support to confirm they can handle your project’s complexities.
- Gauge flexibility and scalability: Verify their ability to accommodate shifting production volumes and custom orders—key for long-term success.
- Prioritize clear communication: Opt for a partner that provides regular updates and transparent discussions to keep projects on track.
- Evaluate sustainability practices: Seek companies active in eco-friendly methods and ethical standards, which can reduce costs and enhance brand reputation.
By following these tips, companies can ensure they select a partner that not only fulfills their present requirements but also sets the stage for future success. A well-chosen injection molding manufacturer can bring unmatched expertise, innovative solutions, and a commitment to quality that align with your strategic objectives. Building a relationship with a manufacturer who understands your market and possesses a track record of reliability is invaluable. As trends in technology and sustainability continue to shape the industry, the right partner will be integral in navigating this evolving landscape effectively.
Continuous Improvement and Long-Term Partnership
A reliable injection molding partner is committed to ongoing improvement. They regularly assess and refine production techniques, integrating advanced technology and best practices. This dedication to continuous learning elevates the partnership’s strategic value, ensuring consistently high manufacturing outcomes.
Long-term collaborations are built on shared progress. As the market evolves, so do production methods and material science. An enduring partnership leverages this evolution, positioning both parties at the forefront of innovation.
Industry Outlook and Future Collaboration
Looking forward, the injection molding industry is poised for dynamic growth and innovation propelled by next-generation manufacturing techniques. As sustainability continues to shape business decisions, manufacturers and clients will benefit from more efficient processes and resilient supply chains.
By embracing modern materials and cultivating close collaboration, organizations can better respond to market fluctuations. The result is a foundation of trust that supports sustained innovation for all parties involved.
Building Strategic Alliances for Future Success
Choosing the right custom injection molding manufacturer extends beyond simply acquiring parts—it’s about forming a partnership that drives innovation and long-term success. Essential traits include deep technical expertise, a comprehensive range of services, advanced technology, rigorous quality systems, and a flexible, customer-focused approach. Additionally, partnering with a U.S.-based injection molding manufacturer may offer benefits such as familiarity with local regulations and streamlined communication, though the specific advantages will vary by company.
Evaluate your options carefully, and consider how a trusted injection molding partner can transform your projects. Take the next step toward precision and success by reaching out to a manufacturer that shares your passion for excellence and is ready to bring your vision to life. Contact Pioneer Plastics today