Sustainability in injection molding is no longer a buzzword; a fundamental pillar of modern manufacturing. Driven by Environmental, Social, and Governance (ESG) goals and the need to address the industry’s environmental footprint—from high energy use to plastic waste—manufacturers are turning challenges into powerful opportunities. Adopting greener practices doesn’t just reduce environmental impact; it drives innovation, enhances efficiency, and delivers superior quality.
This guide explores the key strategies to transform your operations, covering everything from smart material selection and energy-efficient practices to lifecycle-focused design and strategic partnerships. Discover actionable insights to build a more sustainable—and competitive—business without compromising on performance.
The Four Pillars of Sustainable Injection Molding
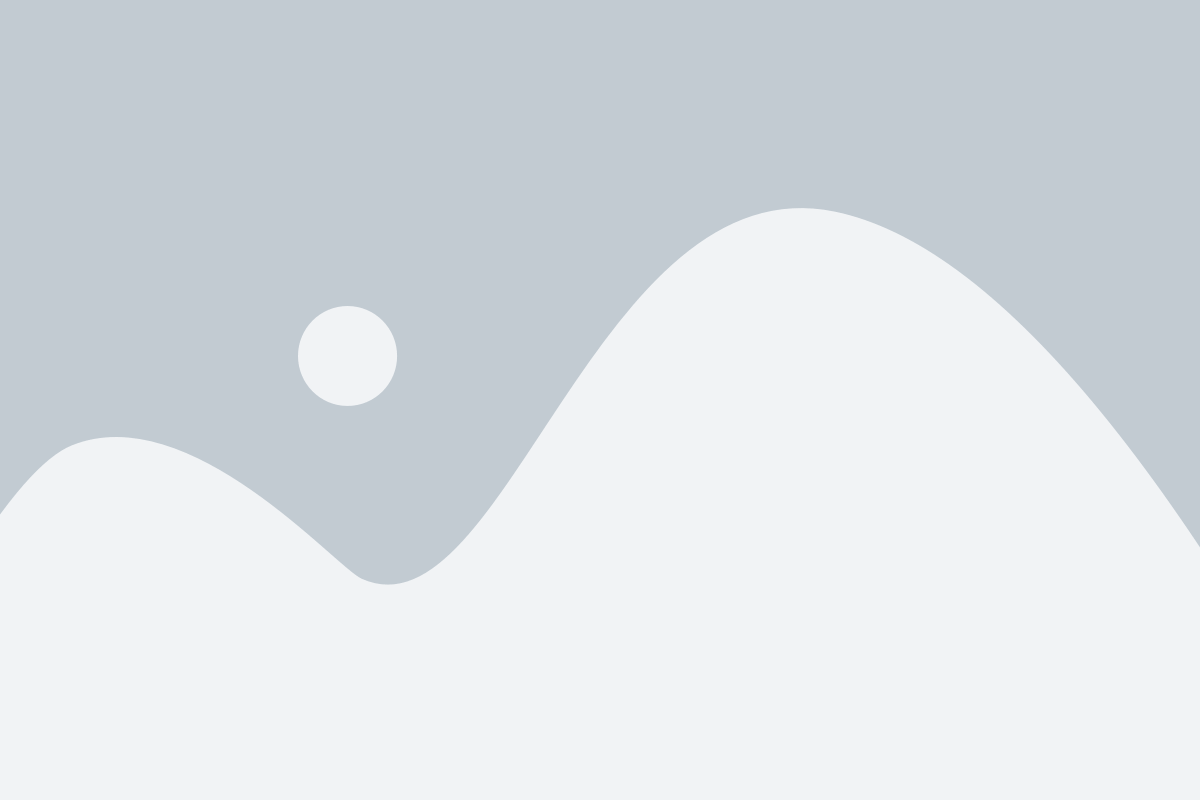
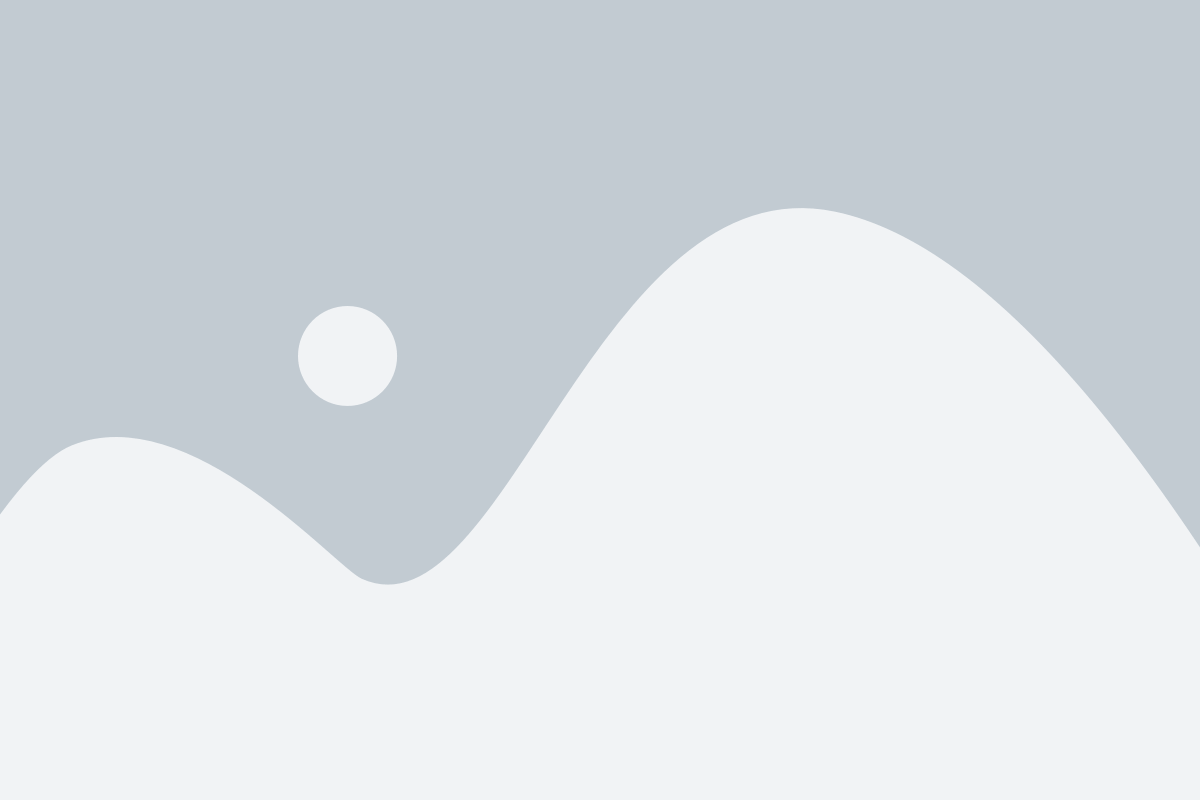
Achieving meaningful sustainability requires more than a single initiative; it demands a holistic approach built on a strong ESG framework. By focusing on four key pillars—Smart Material & Waste Management, Energy Efficiency & Carbon Reduction, Lifecycle-Centric Design, and Strategic Partnerships—manufacturers can create a comprehensive roadmap for more responsible and competitive production practices.
Pillar 1: Smart Material & Waste Management
Reducing plastic waste is a primary objective, demanding innovative thinking about both the materials used and the processes that handle them. This involves a two-pronged strategy: adopting environmentally friendly materials and implementing rigorous systems to minimize waste.
Transitioning to sustainable materials is a key step. Options include:
- Biodegradable Plastics: These are designed to break down under specific conditions, making them suitable for short-life applications.
- Bio-Based Polymers: Derived from renewable resources like corn or sugarcane, these polymers can help reduce dependence on fossil fuels.
- Recycled Engineering-Grade Plastics: Advances in recycling have enabled some high-performance resins to be produced from post-consumer waste while maintaining their quality standards.
While eco-friendly materials can sometimes come at a higher cost, manufacturers can address this by collaborating with suppliers on sustainable sourcing and investing in product redesign to optimize material use.
Equally important is managing waste during production. Many manufacturers now incorporate regrind—recovered plastic scraps—back into their processes through a closed-loop system that treats every scrap as a resource, substantially cutting the volume of materials heading to landfills. Furthermore, implementing lean manufacturing practices and accurate production forecasting can reduce the surplus caused by overproduction. Tools like rapid prototyping also allow for testing and refining designs before committing to full-scale production, minimizing errors and material waste.
Pillar 2: Energy Efficiency & Carbon Reduction
Reducing energy consumption is critical to lowering the overall environmental impact and carbon footprint of injection molding. This can be achieved through several key strategies:
- Upgrading to Modern Equipment: Equipment designed with energy efficiency in mind can dramatically reduce consumption. Many modern systems integrate features such as variable-speed motors, all-electric or hybrid solutions, and automated systems that have documented improvements in performance and efficiency.
- Implementing Lean Manufacturing Practices: Lean manufacturing eliminates waste by streamlining operations. Reducing machine downtime, optimizing material handling, and standardizing workflows all cut energy use and enhance production efficiency, which leads to significant cost savings.
- Using Energy Monitoring Systems: Real-time energy monitoring systems provide invaluable insights into consumption patterns. These systems help identify inefficiencies, enabling targeted improvements and data-driven decisions that reduce overall energy usage.
- Optimizing Production Environments: Simple adjustments to the production environment—such as employing efficient temperature controls, upgrading to LED lighting, and performing regular, proactive maintenance—also contribute significantly to energy conservation.
Pillar 3: Design for the Entire Lifecycle
Thoughtful, eco-conscious design is crucial for sustainability, as early decisions can significantly reduce waste and improve recyclability down the line. A lifecycle assessment (LCA), which evaluates a product’s environmental impact from raw material extraction through to disposal, is an essential tool to guide these design choices. The key principles of this approach include:
- Minimizing Raw Material Usage: Efficient design techniques, such as reducing wall thickness, consolidating parts, and simplifying geometries, can lower material consumption and energy requirements while still maintaining key performance properties.
- Designing for Modularity and Repairability: Creating products that are easy to disassemble facilitates repair and recycling. This extends the product’s useful life and reduces the amount of waste sent to landfills.
- Focusing on Recyclable Materials: Selecting materials that align with existing, accessible recycling systems is critical. This ensures that products can be successfully reclaimed at their end-of-life, supporting circular economy initiatives.
By integrating end-of-life considerations like take-back programs and ease of disassembly from the very beginning, sustainability is woven into every stage of a product’s lifecycle.
Pillar 4: Strategic & Collaborative Partnerships
No single company can achieve its sustainability goals in isolation. Collaboration is essential for advancing sustainable practices across the industry. Strategic partnerships with raw material suppliers, research institutions, and environmental organizations can help accelerate waste reduction and foster innovation. The benefits of this collective approach are clear:
- Advancing Recycling Technologies: Joint efforts can lead to crucial improvements in recycling processes and the development of new infrastructure.
- Sourcing Sustainable Materials: Strong partnerships can help secure a continuous and reliable supply of eco-friendly resources.
- Sharing Best Practices: Open collaboration encourages the exchange of insights and expertise, promoting the industry-wide adoption of the most effective sustainability measures.
By leveraging collective resources and expertise, companies can more effectively overcome challenges and drive the entire industry toward a more sustainable future.
How Pioneer Plastics Puts Sustainability into Practice
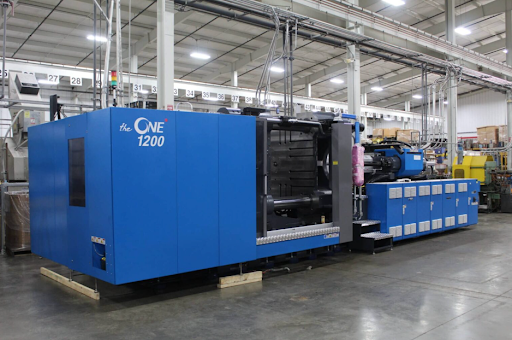
Pioneer Plastics demonstrates a commitment to sustainable practices in its injection molding operations. For example:
Employing Recycling Initiatives
Pioneer Plastics has implemented initiatives aimed at reducing waste, including efforts to recycle production scrap materials. These measures are part of a broader strategy to reduce reliance on virgin plastics while minimizing waste.
Streamlining with In-House Tool Building
An in-house tool and die shop allows for rapid design iterations, reducing the number of trial runs and associated material waste. This process helps align production more closely with design needs, contributing to more efficient operations.
Advancing Sustainability Through Collaboration
Pioneer Plastics works closely with clients to select suitable eco-friendly materials and simplify product designs. By considering lifecycle impacts from concept through production, they support customers in reaching their environmental goals while maintaining quality.
The Future of Sustainable Manufacturing: Trends and Innovations
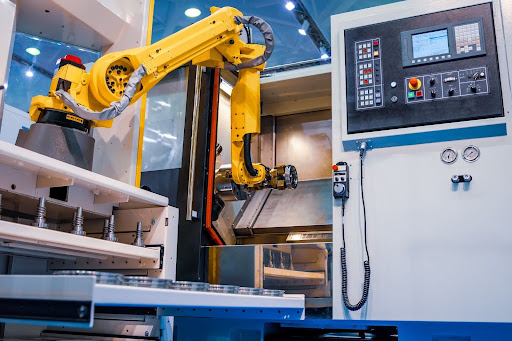
The journey toward sustainability is dynamic, driven by continuous innovation in technology, energy, and materials. While significant challenges remain, the injection molding industry is actively exploring and implementing forward-thinking solutions that promise a more efficient and responsible future.
The Rise of the Smart Factory: Automation and Data
The next frontier in sustainability is digital. Research and development continue into leveraging digital tools and automation to reduce waste and improve efficiency. Enhanced automation and smart sensor technology in modern equipment provide real-time production data, enabling precise process optimizations that were previously impossible. Furthermore, artificial intelligence is increasingly integrated into predictive maintenance systems, with documented benefits such as early fault detection and optimized maintenance scheduling that help prevent unplanned downtime and wasted resources. As the industry continues to explore ways to use these digital innovations, advancements in AI and data analytics are demonstrating real-world value and applications.
Powering Production with Renewable Energy
Integrating renewable energy sources into manufacturing processes is a vital step for advancing sustainability. By adopting solar, wind, or other renewable energy systems, companies can significantly reduce their reliance on fossil fuels and lower their carbon footprint. This strategic transition not only helps lower long-term production costs but also contributes to a cleaner, more resilient manufacturing ecosystem.
Innovating Past Hurdles: Advanced Materials and a Circular Economy
While challenges such as the higher cost of sustainable materials and current recycling limitations persist, these hurdles also inspire constant innovation. Research and development efforts continue to address these issues head-on. Companies are increasingly exploring advanced plastic formulations derived from agricultural waste or new biodegradable polymers that degrade more quickly. These solutions can help reduce long-term landfill burdens while maintaining critical performance characteristics. As these advanced technologies become more cost-effective and scalable, injection molding stands poised to grow as an even more sustainable manufacturing method across diverse industries.
A Culture of Improvement: Continuous Sustainability Monitoring
Technology alone is not enough; sustainable manufacturing requires a commitment to ongoing evaluation and improvement. Many companies are establishing dedicated teams to track the performance of eco-friendly initiatives, utilizing advanced data analytics and environmental performance indicators to continually refine their operations. This iterative, data-driven approach ensures compliance with evolving ESG standards and, more importantly, uncovers new opportunities to reduce waste, improve efficiency, and reinforce a culture of sustainability.
Your Competitive Edge: From Sustainable Practices to Market Success
As the injection molding industry adapts to growing environmental awareness and evolving ESG standards, adopting sustainable practices is increasingly essential. From reducing plastic waste and energy consumption to incorporating eco-friendly materials and thoughtful design practices, manufacturers can take meaningful steps toward a greener future.
Pioneer Plastics leverages decades of industry experience alongside a commitment to more sustainable practices. Whether you need guidance on eco-conscious design or custom injection molding solutions that incorporate recycled materials, Pioneer Plastics is prepared to help you enhance your environmental performance. Together, we can contribute to a more sustainable plastics industry—one innovative solution at a time. Contact Pioneer Plastics today to explore ways to reduce waste and improve sustainability in your operations.