In the world of manufacturing, efficiency, cost-effectiveness, and quality are key. This is where hot runner systems in injection molding come into play, revolutionizing the creation of custom plastic parts.
Whether you’re a professional in the manufacturing field, a business owner, or simply curious about how everyday plastic items are made, this blog post will walk you through the fascinating process. We’ll explore the benefits, applications, and intricacies of hot runner systems, and demonstrate how Pioneer Plastics, a trusted industry leader, leverages this technology to deliver superior results.
Join us as we unveil the incredible world of injection molding and the crucial role of hot runner systems within it.
What Are Hot Runner Systems in Injection Molding?
Hot runner systems are a key component in the field of injection molding. These systems comprise heated components that keep the plastic in a molten state until it gets to the cavities of the mold.
These systems have revolutionized the injection molding process, offering numerous advantages over traditional cold runner systems which have runners that channel the molten plastic from the injection molding machine to the cavities of the mold.
Let’s dive more into hot runner systems and how they compare to their cold runner system counterparts.
Hot Runner Systems vs. Cold Runner Systems—What's the Difference?
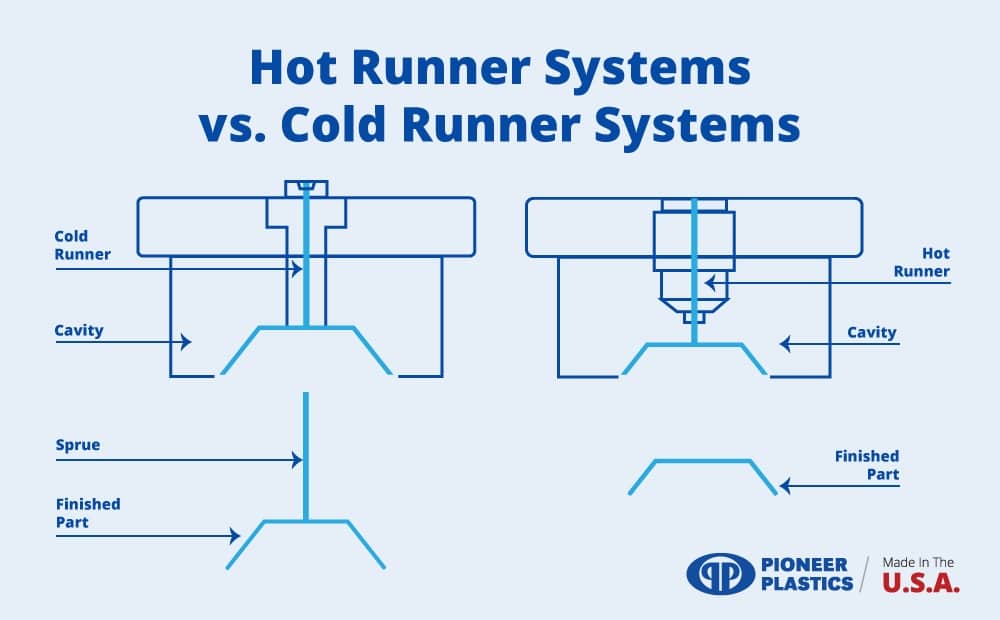
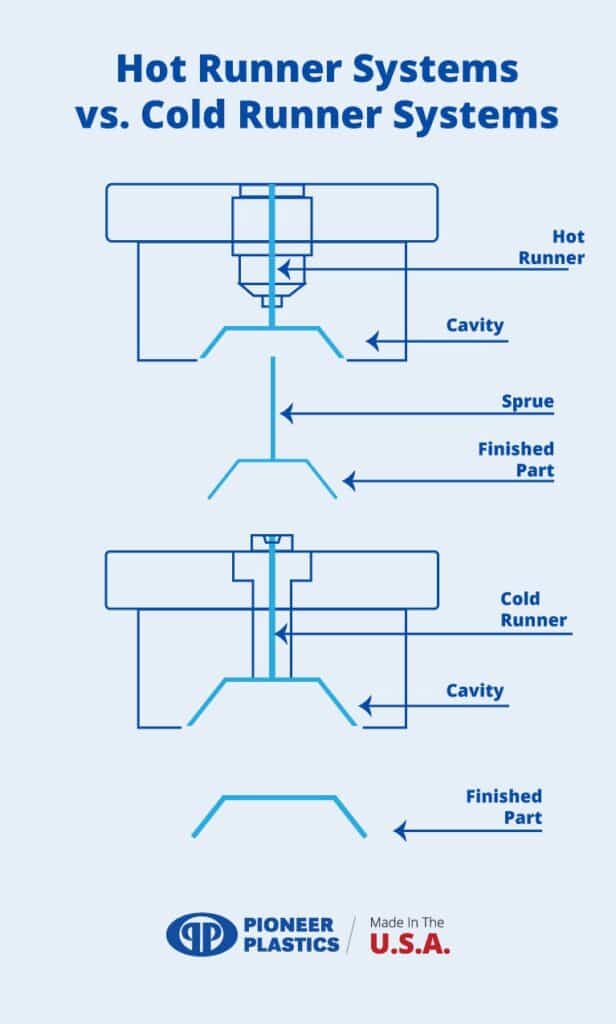
Hot runner systems have become an essential tool for many manufacturers across various industries. By leveraging this technology, businesses can enhance their production processes, deliver superior products, and stay ahead in the competitive manufacturing landscape.
So how are hot runner systems different from cold runner systems? The main difference lies in how they handle the plastic material during the injection molding process. In a hot runner system, the plastic is kept in a molten state throughout the entire process. This is achieved by using heated components, such as heated nozzles and manifold systems, to maintain the desired temperature of the plastic.
So how does this create an advantage over cold runner systems? Let’s explore the many benefits:
Complex Designs
The use of a hot runner system allows for more complex and intricate designs, as there are no restrictions imposed by the presence of runners. Additionally, some hot runner systems will do two shot molding enabling the injection of multiple materials or colors simultaneously, without the risk of cross-contamination. This versatility opens up a wide range of possibilities for manufacturers, allowing them to create multi-component parts or products with intricate designs and color patterns.
Part Quality
Using a hot runner system also helps to prevent material degradation and ensures optimal part quality. By closely monitoring and controlling the temperature of the plastic, hot runner systems can produce parts with superior surface finish and dimensional accuracy for a clean and finished product.
Material Savings
In cold runner systems, these runners solidify along with the plastic, resulting in material waste that needs to be trimmed or regrinded. In contrast, hot runner systems ensure a smoother flow of plastic, without the need for runners. This not only reduces waste but also speeds up the production cycle.
By reducing material waste, manufacturers can optimize their material usage and reduce overall costs. This also results in environmental benefits. By eliminating plastic waste, they contribute to a more sustainable production process. This aspect is particularly crucial in today’s manufacturing landscape, where businesses are under increasing pressure to minimize their environmental footprint.
Efficiency
The absence of runners and sprues in hot runner systems results in faster production cycles. With no waiting time for the plastic to cool and solidify, manufacturers can produce parts at a higher rate, increasing overall productivity.
Cost Savings
A common misconception about injection molding is that it is an expensive process. However, as we’ve discussed, by reducing waste, speeding up production, and minimizing the need for labor-intensive processes such as trimming and regrinding, hot runner systems can lead to substantial savings for the customer.
The upfront cost of these systems might be higher than their cold runner counterparts for the company who owns the mold however, the actual per-unit cost of production is lower—making the production cost for their customers lower as well. This is especially true for high-volume production runs due to the high efficiency and repeatability of the process.
Applications of Hot Runner Systems in Various Industries
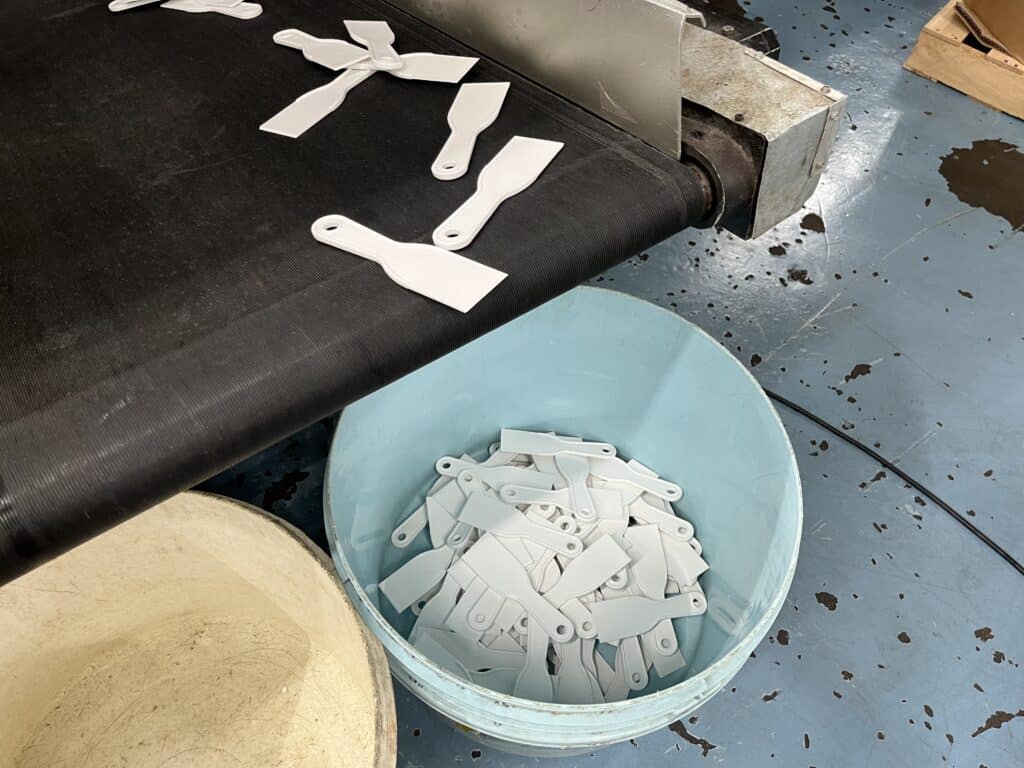
Hot runner systems have a wide array of applications across numerous industries. Their versatility and efficiency make them a preferred choice for various manufacturing processes. Some common examples include:
- Automotive Industry: Hot runner systems are used to produce intricate parts for automotive interiors. The elimination of runners in hot runner systems allows for the creation of complex and intricate designs, making them ideal for automotive parts that require precision and attention to detail for parts such as dashboard components, door panels, and instrument clusters.
- Packaging Industry: Hot runner systems are utilized to manufacture plastic containers, bottles, and packaging materials. Their ability to produce clean and uniform parts with high surface finish makes them well-suited for packaging applications. The system’s ability to handle complex molds and produce high-quality results makes it ideal for creating detailed and delicate pieces.
- Medical Industry: Hot runner systems play a vital role in the production of medical devices and components. The precise control over temperature and material flow ensures the creation of high-quality, sterile, and safe medical products such as parts for medical devices, syringes, vials and surgical instruments.
- Consumer Goods Industry: These systems are used to create a wide range of consumer goods, including plastic parts for household appliances and electronics or simple plastic home tools such as a putty knife. The ability to produce intricate designs, multi-component parts, and vibrant color patterns makes them a popular choice for consumer product manufacturers.
- Food Industry: Hot runner systems are integral to creating sturdy, safe, and aesthetically pleasing plastic packaging. They help in the production of items like food-grade containers, bottle caps, and other types of packaging. These systems also ensure uniformity and precision, which are key in maintaining the quality and safety standards in this sector.
Finding the Right Injection Molding Company
Selecting a reputable custom injection molding company to produce your parts is pivotal for businesses looking to balance quality and budget. Such suppliers use machines that have been tested and maintained to a high standard, ensuring their performance and longevity.
When looking for a supplier, it’s essential to consider their reputation in the industry, their customer service process, and if they are an overall fit for your needs.
An ideal supplier will be able to provide comprehensive information about their services and be proactive in addressing your questions, providing insights, and suggesting solutions for your production goals.
Pioneer Plastics: A Trustworthy U.S. Custom Injection Molding Company
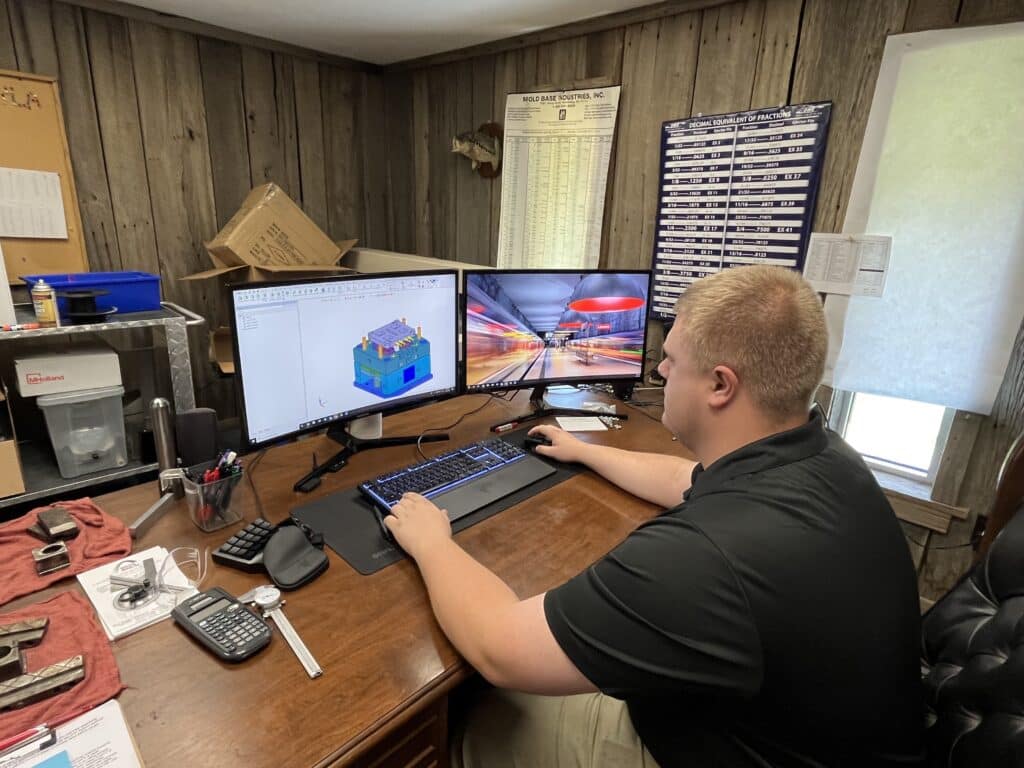
Pioneer Plastics has established an eminent reputation in the injection molding industry. With a rich history rooted in quality, innovation, and customer satisfaction, we’ve emerged as a trusted name not just locally, but on a national level.
Our commitment to exceeding customer expectations is at the heart of everything we do. We understand the importance of delivering reliable, high-quality products on time, every time. This uncompromising standard has earned us the loyalty and respect of a wide range of clients.
One of our key strengths is our proficiency in using hot runner systems in injection molding. This expertise enables us to create plastic parts that meet precise specifications, ensuring that each product we manufacture aligns perfectly with our client’s needs. Whether you’re a seasoned professional in the manufacturing industry or a newcomer seeking guidance, Pioneer Plastics is equipped to provide solutions that cater to your specific requirements.
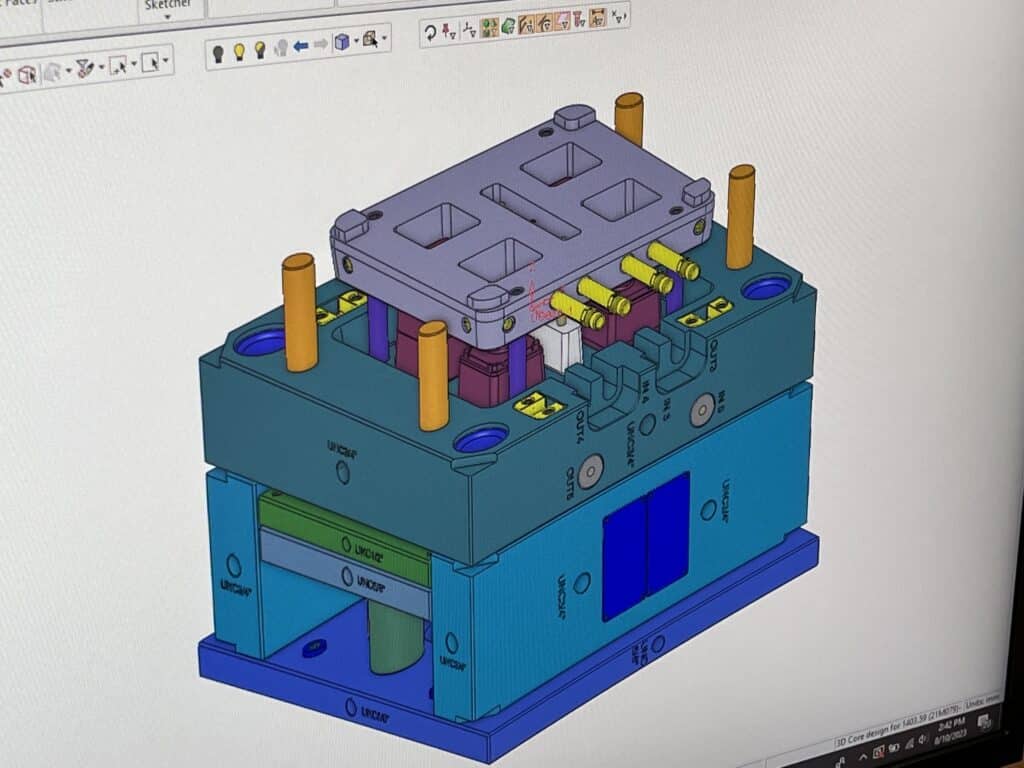
In addition to our expertise, we offer transparency and integrity. We believe in maintaining an open line of communication with our clients, providing regular updates and honest feedback. We’re not just your supplier; we’re your partner, dedicated to achieving your goals with you.
Get High-Quality, Custom-Made Plastic Parts with Pioneer Plastics
From reducing waste and improving part quality to streamlining production cycles and enabling intricate designs, hot runner systems have become a go-to solution for many manufacturers.
They play a pivotal role in enhancing productivity, reducing costs, and encouraging environmental sustainability.
At Pioneer Plastics, we pride ourselves on our expertise and our commitment to quality and customer satisfaction. Hot runner systems are at the core of our production capabilities, allowing us to create detailed, complex designs that meet our clients’ exact specifications. These systems facilitate the efficient production of a wide range of products.
Our expertise in utilizing hot runner systems extends beyond just technical knowledge. Pioneer Plastics’ team understands how to leverage the benefits of these systems to optimize production. By leveraging this technology, they can deliver superior results to their customers, meeting the highest standards of quality, efficiency, and cost-effectiveness.
If you’re interested in learning more about our injection molding services don’t hesitate to reach out to us. Let Pioneer Plastics be your partner in creating superior plastic products through innovative injection molding systems.