Choosing the right source for your plastic products plays a critical role in determining your business’s overall efficiency and success. Industries such as manufacturing, packaging, and collectibles rely heavily on plastic components, making the decision between domestic and overseas sourcing pivotal. This choice influences product quality, sustainability, costs, and supply chain efficiency.
In today’s market, where shipping costs are rising and supply chains face frequent disruptions, many businesses are shifting toward domestic sourcing to improve reliability and mitigate risks. This article examines the essential factors—quality, sustainability, logistics, and costs—that shape sourcing decisions. By comparing domestic and overseas sources and considering emerging trends, you can decide on the best strategy to meet your organization’s evolving needs.
The Sourcing Showdown: Domestic vs. Overseas at a Glance
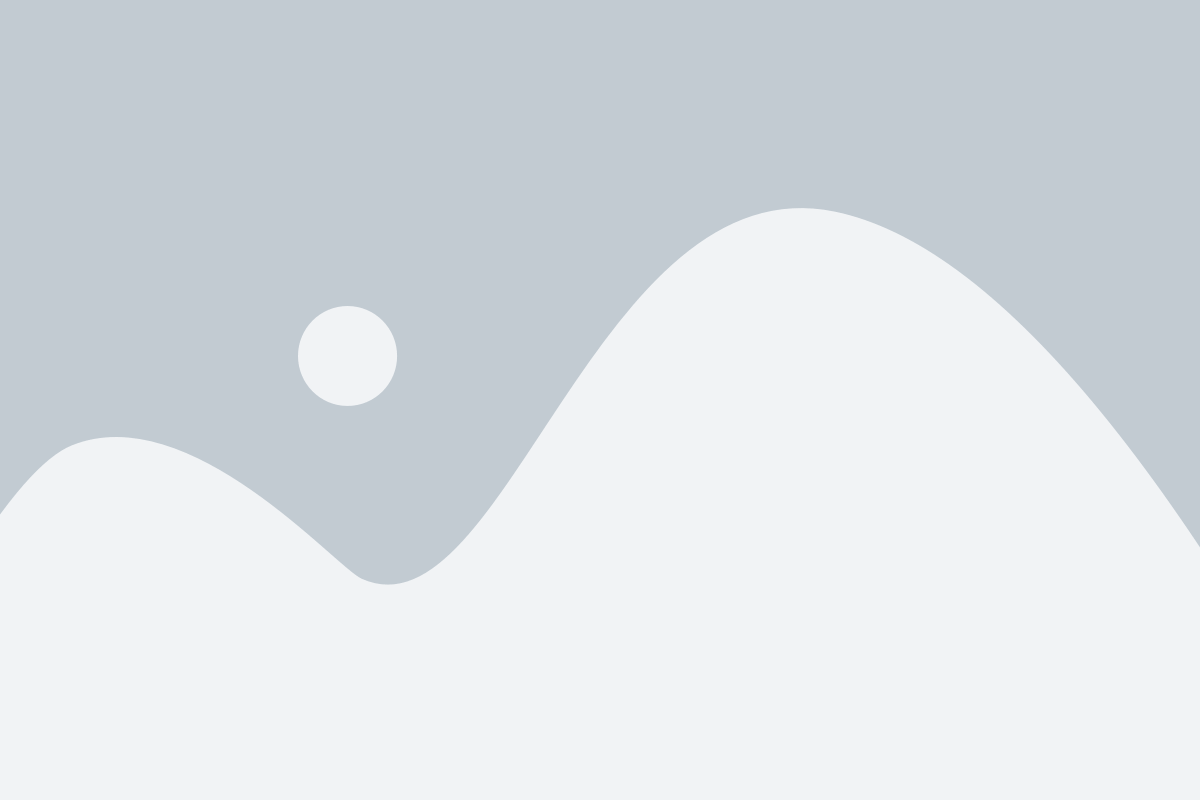
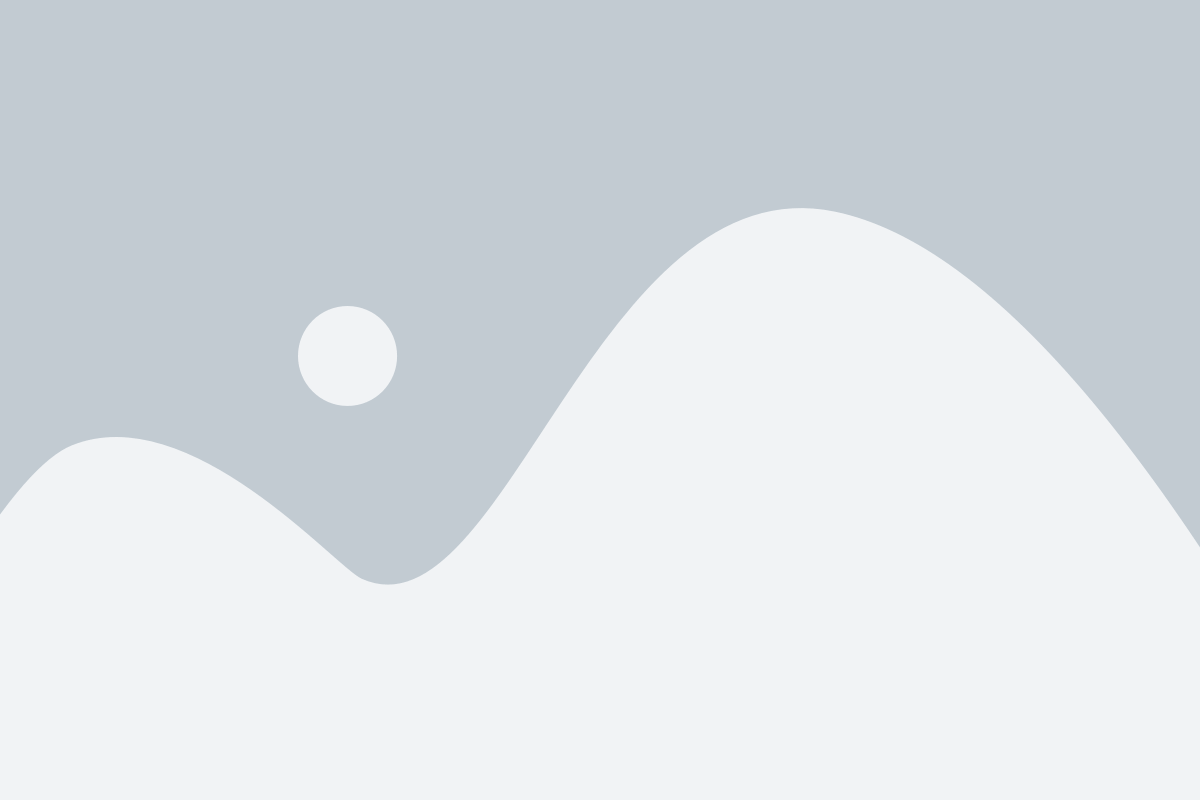
When deciding between domestic or overseas sourcing, several factors affect product quality, operational efficiency, sustainability, and costs. A detailed look at these key considerations reveals the distinct trade-offs of each approach, helping you determine which strategy best aligns with your business priorities.
Quality
Domestic: Domestic sourcing offers superior quality assurance. U.S.-based suppliers are mandated to meet strict regulatory standards through FDA-enforced Quality System regulations. Many also voluntarily pursue ISO 13485 certification to align their processes with international quality management expectations. This combination of mandatory and voluntary measures, coupled with geographic proximity, facilitates closer collaboration during product development, allows for regular on-site inspections, and enables the quick resolution of any issues, significantly lowering the risk of defects and production delays.
Overseas: Quality levels from international sources can vary significantly. Limited direct oversight and long distances hinder on-site checks and swift defect resolution, which may result in inconsistent quality outcomes. To mitigate this, businesses often need to invest in additional audits, third-party inspections, and more rigorous quality control measures to ensure products meet required standards.
Sustainability
Domestic: Local sourcing helps reduce carbon footprints. The minimized shipping distances inherent in local production lower fuel usage and associated emissions, contributing to a greener supply chain. Furthermore, numerous U.S. manufacturers are actively incorporating eco-friendly practices and materials, such as adopting energy-efficient processes and using bio-based or recycled plastics to meet growing consumer and regulatory demands.
Overseas: While some international manufacturers are making strides in greener processes, long-distance shipping inherently increases a product’s carbon footprint. Additionally, less stringent or varying environmental standards in some regions can lead to manufacturing practices that may not fully align with a company’s environmental or ethical values.
Logistics, Lead Times, and Communication
Domestic: Domestic suppliers offer significantly faster shipping and reduced lead times—an essential advantage for businesses operating under stringent deadlines or maintaining just-in-time inventory systems. Logistics are simplified with fewer customs delays. This is further enhanced by seamless communication, as closer proximity and shared time zones enable immediate and more effective coordination on design modifications, production adjustments, and problem-solving, reducing the risk of costly miscommunications.
Overseas: International sourcing typically involves longer shipping times, complicated customs procedures, and unpredictable delays that can disrupt inventory and production schedules. Communication can be hindered by language differences, varying business cultures, and significant time zone discrepancies, which can slow down important discussions and lead to misunderstandings that affect product development and quality.
Costs and Economies of Scale
Domestic: Although labor and production costs in the U.S. tend to be higher on a per-unit basis, these may be offset by reduced shipping expenses, fewer quality-related rework costs, and more efficient inventory management due to shorter lead times. When all factors are considered in a total cost of ownership model, these offsets can help narrow the overall cost differences.
Overseas: Lower wages and raw material prices can yield lower per-unit production costs, which remains an attractive factor. Furthermore, large-scale manufacturing capabilities in some regions offer significant economies of scale, making this route appealing for high-volume production runs. However, businesses must account for hidden and volatile costs such as tariffs, customs fees, fluctuating freight charges, and expenses from quality rework, which can diminish or even eliminate the anticipated savings.
Risks, Accountability, and Specialization
Domestic: Local sourcing minimizes risks stemming from geopolitical disruptions, political instability, and sudden tariff changes. It also offers enhanced transparency and accountability, as strict U.S. regulatory measures enforce high standards in labor, environmental, and safety protocols, providing greater operational oversight and a faster, more agile response to shifts in market demand.
Overseas: International sourcing presents risks including economic fluctuations and unforeseen alterations in trade policies. However, certain overseas regions specialize in specific plastic production methods and may offer access to advanced technology, specialized expertise, and highly automated production lines that can boost overall efficiency for certain products.
Community & Economic Impact
Domestic: Opting for domestic sourcing directly supports local job creation and strengthens regional manufacturing communities. Products manufactured in the USA often carry a strong appeal for consumers who are increasingly interested in quality, ethical production practices, and supporting the national economy.
Industry Trends in Plastic Sourcing
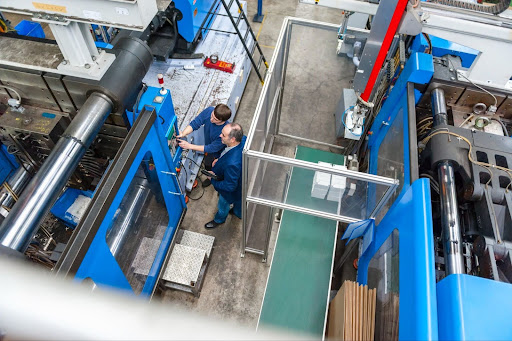
The landscape of plastic sourcing is expected to evolve further, driven by new regulations, consumer demands, and technological advancements. Below are some trends shaping the way organizations source plastic materials:
Increasing Demand for Sustainable Materials
Eco-friendly plastics—such as those made from bio-based raw materials and advanced chemical recycling—are emerging as popular alternatives. U.S. manufacturers are actively incorporating these materials, helping reduce environmental impact.
Growth of Nearshoring and Reshoring
Amid trade uncertainties and recent supply chain disruptions, many companies are bringing production closer to home. Exploring the benefits of nearshoring offers faster market access and more predictable logistics, while reshoring supports local economies through job creation and improved oversight.
Rising Automation and Digitization
Technological advances in robotics, automation, and digital supply chain management are enhancing production efficiency. These solutions enable domestic facilities to better compete with lower-cost international operations and streamline processes across multiple stages of production.
Expansion of Circular Economy Practices
Innovative recycling methods and waste-reduction initiatives are central to extending the lifecycle of materials used in plastic products. Embracing circular economy practices is becoming critical as regulatory and consumer demands for sustainability grow.
Impact of Changing Trade Policies
Evolving trade policies, including tariffs and adjustments in trade agreements, continue to influence sourcing strategies. Staying informed on such changes is vital to avoid unexpected costs and disruptions.
Understanding Pioneer Plastics’ Advantage in Domestic Sourcing
Partnering with a U.S.-based injection molding company like Pioneer Plastics offers a streamlined path from concept to realization. With decades of industry experience, Pioneer Plastics delivers custom solutions emphasizing quality, efficiency, and sustainability:
- Custom Injection Molding Solutions: They transform ideas into high-performance products, benefiting from shorter lead times.
- Advanced Engineering and Tool Building: Their in-house capabilities allow for rapid adjustments to design changes, mitigating delays and reducing costs.
- Stringent Quality Standards: By adhering to mandatory FDA requirements—and often supplementing with voluntary ISO 9001 certification—they maintain reliable product quality essential for sectors with rigorous safety demands.
- Commitment to Sustainability: Pioneer Plastics integrates eco-friendly practices, including the use of recycled materials and energy-efficient technologies.
- Flexible Production Capabilities: Their capacity supports everything from prototypes to large-scale production runs, accommodating diverse manufacturing needs.
Making Your Choice: Actionable Tips for Your Sourcing Strategy
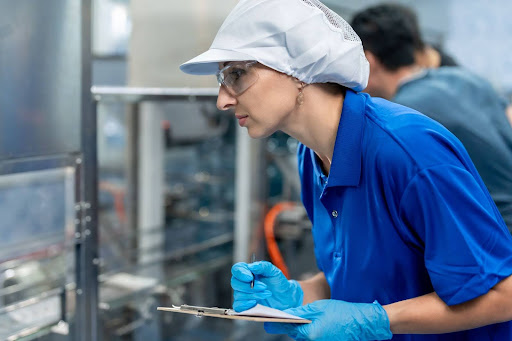
To optimize your sourcing strategy, consider the following tips:
- Align with Business Priorities: Identify whether cost, speed, quality, or sustainability is most critical for your operations to guide supplier selection.
- Review Logistics and Delivery Times: Assess how shipping timelines and potential disruptions could impact your supply chain. Domestic sourcing tends to offer shorter, more predictable delivery times.
- Assess Quality and Compliance Needs: For products that require strict regulatory compliance, domestic suppliers may offer more dependable quality. With overseas options, additional verification is often necessary.
- Evaluate Total Costs: Look beyond immediate production expenses to consider factors like shipping, tariffs, and potential rework costs. This holistic approach ensures a fair comparison of overall expenses.
- Prioritize Sustainability: Seek suppliers that practice eco-friendly production methods. This not only enhances your brand reputation but also aligns with growing regulatory and consumer expectations.
- Maintain Clear Communication: Whether domestic or overseas, ensure your supplier is committed to transparent and ongoing communication to minimize misunderstandings.
- Plan for Long-Term Growth: Regularly review and adjust your sourcing strategy to ensure it continues to meet your evolving business requirements over time.
Bringing Your Supply Chain Home: The Domestic Advantage
Deciding on the right source for your plastic products is critical for long-term operational success. Domestic sourcing offers advantages in quality, communication, and sustainability that help mitigate many of the risks associated with international production. Although overseas suppliers can sometimes offer cost benefits, hidden expenses and logistical challenges may significantly impact overall value.
For companies focused on rigorous quality standards, transparency, and sustainable practices, partnering with a trusted U.S.-based manufacturer can provide a reliable and efficient solution. Explore how domestic manufacturing expertise can drive efficiency and support your company’s long-term growth.
Contact Pioneer Plastics today to discover how their domestic, high-quality plastic products can propel your business forward.