Businesses relying on overseas plastic manufacturing are facing a storm of uncertainty. International trade disputes, fluctuating import tariffs, and unpredictable shipping delays can cripple budgets and disrupt operations. What once seemed like a cost-effective solution is now fraught with hidden expenses and logistical nightmares, leaving companies searching for a more reliable alternative.
Many are finding the answer right here at home. By shifting production to a domestic injection molding partner, businesses can insulate themselves from international trade volatility, achieve greater cost stability, and streamline their entire supply chain.
The Strategic Shift to Domestic Manufacturing
Choosing a U.S.-based manufacturer is more than just a logistical preference; it’s a strategic decision that offers clear, compounding advantages.
- Cost Stability and Predictability: Domestic production helps you avoid the sudden price hikes caused by international tariffs and currency fluctuations. This allows for more accurate budgeting and long-term financial planning. While no company is immune to global raw material price shifts, eliminating the layer of tariff-related volatility provides a significant competitive edge.
- Supply Chain Reliability: Extended shipping times, port congestion, and customs delays become a non-issue. With a domestic partner, lead times shrink from weeks or months to a matter of days. This agility allows for faster response times to market demands and dramatically reduces the risk of stockouts.
- Uncompromising Quality Assurance: U.S. manufacturing operates under stringent quality control standards. Having production on home soil means a hands-on approach to quality, ensuring every part is built to last and meets exact specifications. Problems can be identified and solved in real-time, not an ocean away.
- Economic and Environmental Benefits: Sourcing and producing locally supports the American economy and sustains domestic jobs. Furthermore, reducing reliance on long-haul international shipping significantly lowers a company’s carbon footprint, aligning business goals with environmental responsibility.
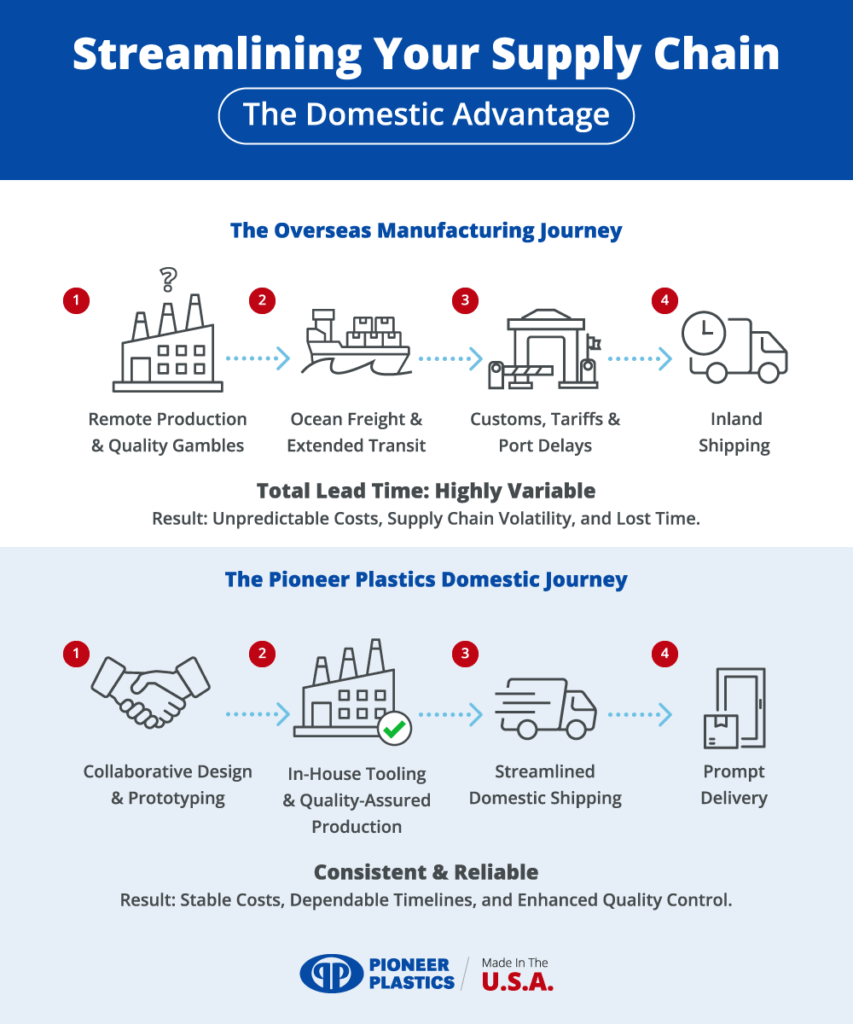
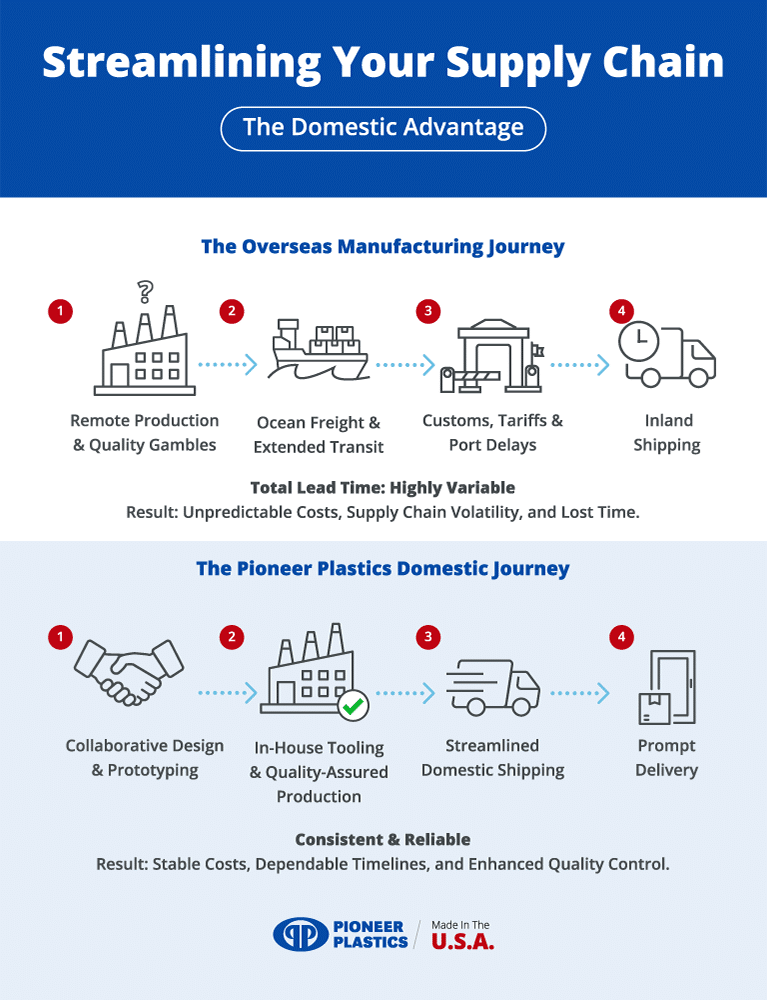
Pioneer Plastics: Your Domestic Manufacturing Partner
For over 40 years, Pioneer Plastics has been at the forefront of the domestic manufacturing movement. Operating entirely from our facility in Dixon, Kentucky, we provide the expertise and infrastructure businesses need to capitalize on the benefits of U.S.-based production. Our commitment is simple: deliver consistent quality, economic stability, and reliable service by keeping manufacturing local.
Addressing Common Concerns About Switching to Domestic Production
Making a change in your supply chain is a significant decision, and many businesses have valid questions. By addressing these common concerns head-on, you can see a clearer path to a more resilient manufacturing strategy.
Concern 1: “Isn’t the upfront cost of domestic manufacturing higher?”
While the per-unit price from an overseas supplier may seem lower at first glance, it rarely reflects the Total Cost of Ownership (TCO). This initial price tag doesn’t include escalating tariffs, exorbitant shipping fees, customs brokerage costs, and the financial impact of delays. Furthermore, hidden costs from poor quality—such as rework, returns, and damage to your brand’s reputation—can quickly erase any perceived savings. Domestic manufacturing with a partner like Pioneer Plastics offers a transparent price that encompasses quality and reliability, leading to a lower TCO and fewer surprise expenses.
Concern 2: “Is the transition process from an overseas supplier too complicated?”
We understand that moving production can seem daunting. That’s why a full-service domestic partner is essential. Pioneer Plastics is equipped to make this transition as seamless as possible. Whether you need to transfer existing molds or develop entirely new tooling, our in-house engineering and tool-building teams manage the process from start to finish. We work with you as a strategic partner, handling the technical details so you can focus on your business without disruption.
Concern 3: “Can a U.S. manufacturer handle the scale and volume I need?”
This is a common misconception. Established U.S. manufacturers like Pioneer Plastics have invested heavily in modern technology, automation, and infrastructure to handle high-volume production runs efficiently. With over four decades of experience, we have developed robust processes to scale production to meet client demands without sacrificing quality or speed. Our domestic location also allows for greater flexibility, enabling us to adapt to both large-scale orders and more specialized, custom projects.
From Concept to Creation: Our In-House Capabilities in Action
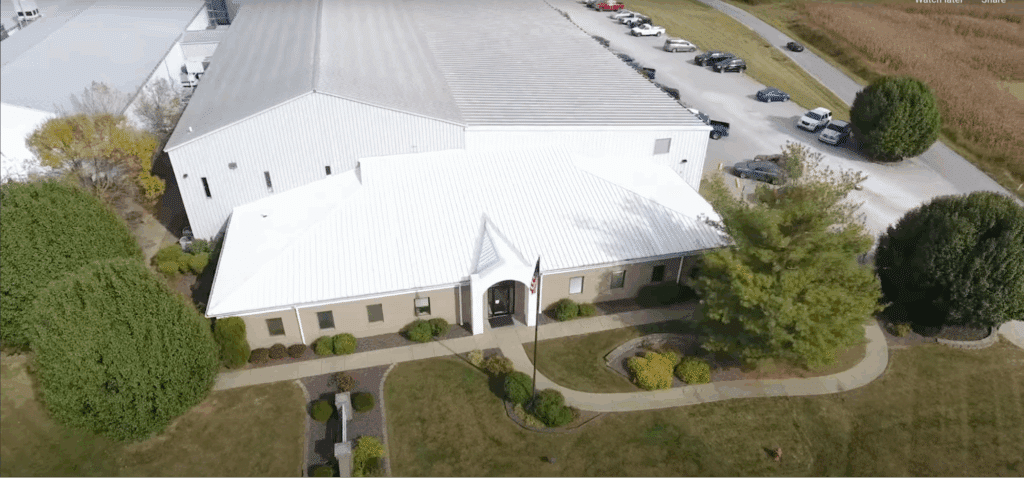
Pioneer Plastics offers a comprehensive, end-to-end manufacturing process under one roof. This integrated approach is the key to reducing lead times, maintaining strict quality control, and providing a stable cost framework for our clients.
- Custom Injection Molding: We collaborate closely with clients to transform ideas into finished products. Our custom injection molding process is designed to meet your specific requirements, streamlining development and minimizing the risks associated with overseas sourcing.
- Agile In-House Tool Building: With our own tool and die shop, we can create, modify, and maintain molds with exceptional speed and precision. This in-house capability allows us to adapt quickly to design changes and ensure every production run is optimized for quality and efficiency.
- Product Expertise as Proof: The result of our integrated process is a diverse range of high-quality products built to exact specifications. For example, our collectible display cases are not just simple containers; they are precision-engineered solutions designed to protect valuable items from dust and environmental damage. Likewise, our versatile clear plastic containers offer a perfect balance of durability and aesthetics for retail, organizational, or specialized storage needs. These products serve as a testament to the high standards achievable through dedicated domestic manufacturing.
Build a More Resilient Business
In an era of global uncertainty, shifting to domestic injection molding is more than a cost-saving measure—it’s a strategic move toward business resilience. Partnering with Pioneer Plastics provides a direct path to greater cost stability, superior quality assurance, and streamlined operational efficiency.
Whether you need durable display cases, innovative custom parts, or a comprehensive engineering solution, our decades of experience and commitment to U.S.-based manufacturing provide a strong foundation for your success.
Take the next step in strengthening your supply chain. Reach out to Pioneer Plastics today to discover how our domestic injection molding solutions can help you navigate the complexities of international trade and support American industry.