Insert molding is an injection manufacturing process that integrates multiple materials into a single, cohesive component. It works by placing a preformed insert—often made of metal, ceramic, or another durable material—into a mold cavity before injecting molten plastic around it. This technique fuses the materials together, creating a robust, unified part that leverages the distinct properties of each element.
This approach is widely adopted across the automotive, medical, and electronics industries because it enables innovative and highly functional designs. By directly embedding features like threaded fasteners, electrical connectors, or structural reinforcements into plastic parts, insert molding eliminates the need for costly secondary assembly. The result is a more efficient and cost-effective production workflow that yields stronger, lighter, and more reliable components for both short-run and large-scale manufacturing.
What Distinguishes Insert Molding from Other Techniques
Insert molding stands out by embedding preformed components into the molding process, yielding benefits not typically found in other methods. In standard plastic injection methods, molten plastic fills a mold cavity to create an individual component; insert molding goes a step further by securing an insert within the mold. This integration provides immediate functionality and removes the need for glues, adhesives, or additional fasteners.
Unlike overmolding—which usually involves adding a secondary layer of resin for aesthetic or tactile benefits—insert molding incorporates non-plastic materials directly into the structure. This can enhance various functionalities, such as electrical conductivity, mechanical reinforcement, and wear resistance. Many industries seeking robust, cost-effective solutions to simplify assembly processes regard insert molding as a highly effective technique. Its ability to bolster part strength and design flexibility makes insert molding relevant for companies demanding both precision and high-volume scalability.
Step-by-Step Overview of the Insert Molding Process
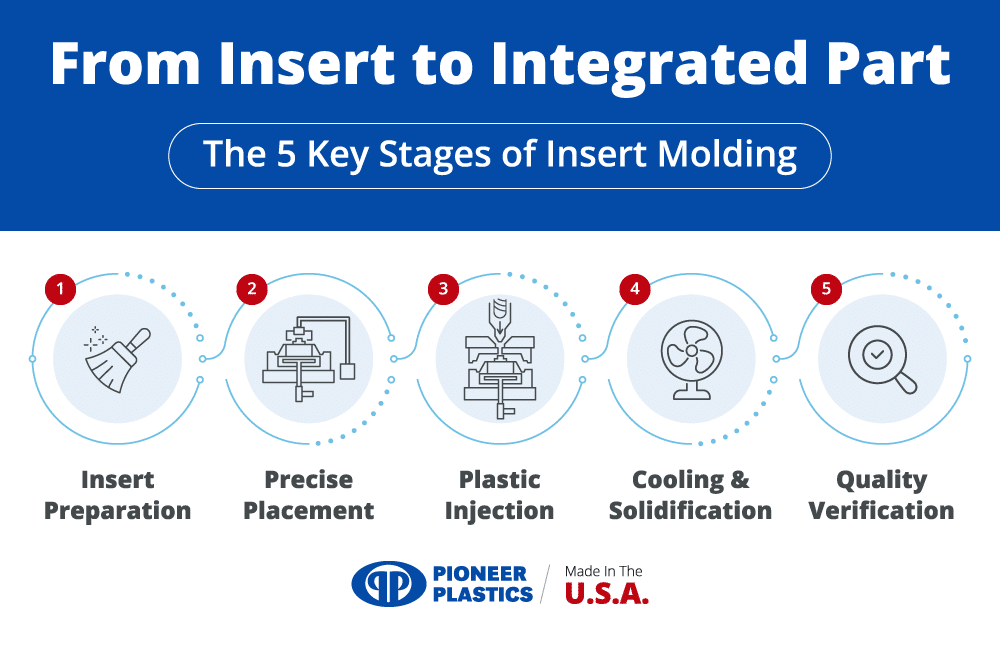
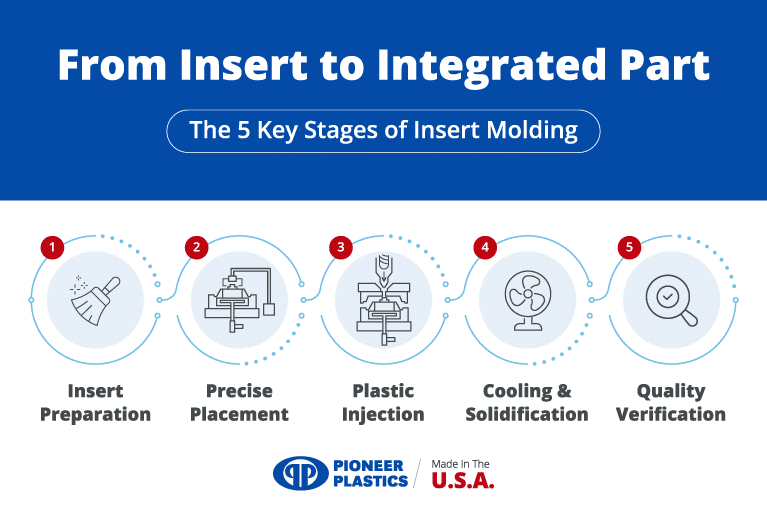
Insert molding expands on basic injection methods by introducing additional, carefully managed steps:
1. Preparation of the Insert
Inserts must be cleaned and, depending on requirements, preheated to reduce thermal shock when contacting hot plastic. This preparation promotes a strong bond and helps prevent defects like cracks, warping, or voids. A thorough surface inspection removes contaminants that might compromise product integrity.
2. Mold Setup and Insert Placement
Inserts are accurately positioned within the mold cavity using specialized fixtures or automated systems. Proper alignment ensures even plastic flow around the insert and a robust bond. Precision tooling and registration techniques help minimize misalignment, which is especially critical in large production runs.
3. Injection of Molten Plastic
Molten plastic is then injected under controlled pressure to encapsulate the insert fully. The mold’s design ensures uniform flow and stable pressure, preventing issues such as insert damage, flow hesitation, or distortion. Sensor monitoring helps regulate temperature and pressure for optimal consistency.
4. Cooling and Solidification
Cooling channels within the mold facilitate quick and uniform cooling, preserving dimensional accuracy and limiting the risk of warping. Once the plastic solidifies, the part is ejected as an integrated assembly. Proper cooling management is crucial to prevent residual stresses that may reduce performance over time.
5. Quality Assurance and Inspection
Quality checks confirm that the insert is securely bonded and that the final component meets all dimensions and specifications. Depending on the application, testing might include destructive or non-destructive methods to verify adhesion, alignment, and functionality. Early detection of abnormalities helps reduce waste and maintain quality.
Core Considerations for a Successful Project
To harness the full potential of insert molding, designers and engineers must navigate two critical areas: selecting the right materials and mastering the unique challenges of the process. Getting these right is the key to creating durable, high-performance components.
Material Selection and Compatibility
Choosing the right materials is the foundation of a successful insert molding project. The goal is to create a strong, permanent bond between the insert and the surrounding plastic resin. This requires careful consideration of both materials’ properties.
Common Material Pairings
- Metals with Engineering-Grade Plastics: Durable inserts like stainless steel or brass are often molded with robust plastics like polycarbonate or nylon to create parts with exceptional strength and wear resistance
- Ceramics for High-Temperature Applications: Ceramic inserts are ideal for components requiring superior electrical insulation or abrasion resistance in demanding thermal environments.
- Specialized Polymers: In some cases, a second, reinforced polymer can be used as an insert to optimize specific traits like chemical resistance, flexibility, or reduced weight.
- Key Factors to Evaluate: When selecting materials, it’s essential to consider the part’s final application, including its load-bearing requirements, necessary chemical resistance, and thermal stability.
Overcoming Key Process Challenges
While powerful, insert molding presents unique technical challenges that require proactive solutions to ensure quality and consistency.
- Thermal Expansion Differences
- Challenge: One of the most common issues is the varying expansion and contraction rates between the insert material and the molten plastic. This can lead to warping, cracks, or a weak bond.
- Solution: Preheating inserts before molding and designing the mold to account for differential expansion can effectively mitigate these thermal stresses.
- Precise Insert Placement
- Challenge: The placement of the insert within the mold must be exact. Even minor misalignments can compromise the part’s structural integrity, function, or appearance.
- Solution: Using automated placement systems (like robotics) and custom-designed fixtures ensures repeatable accuracy, which is critical for high-volume production.
- Strict Quality Control
- Challenge: Because insert-molded parts are often used in critical applications, they must meet exacting standards.
- Solution: Implementing thorough quality control is non-negotiable. Advanced tools such as machine vision systems and automated measurement solutions allow manufacturers to inspect each part, detect flaws early, and maintain a high degree of consistency.
By proactively managing these material and process complexities, companies can successfully reap the full benefits of insert molding without compromising on quality or efficiency.
Applications & Advantages Across Industries
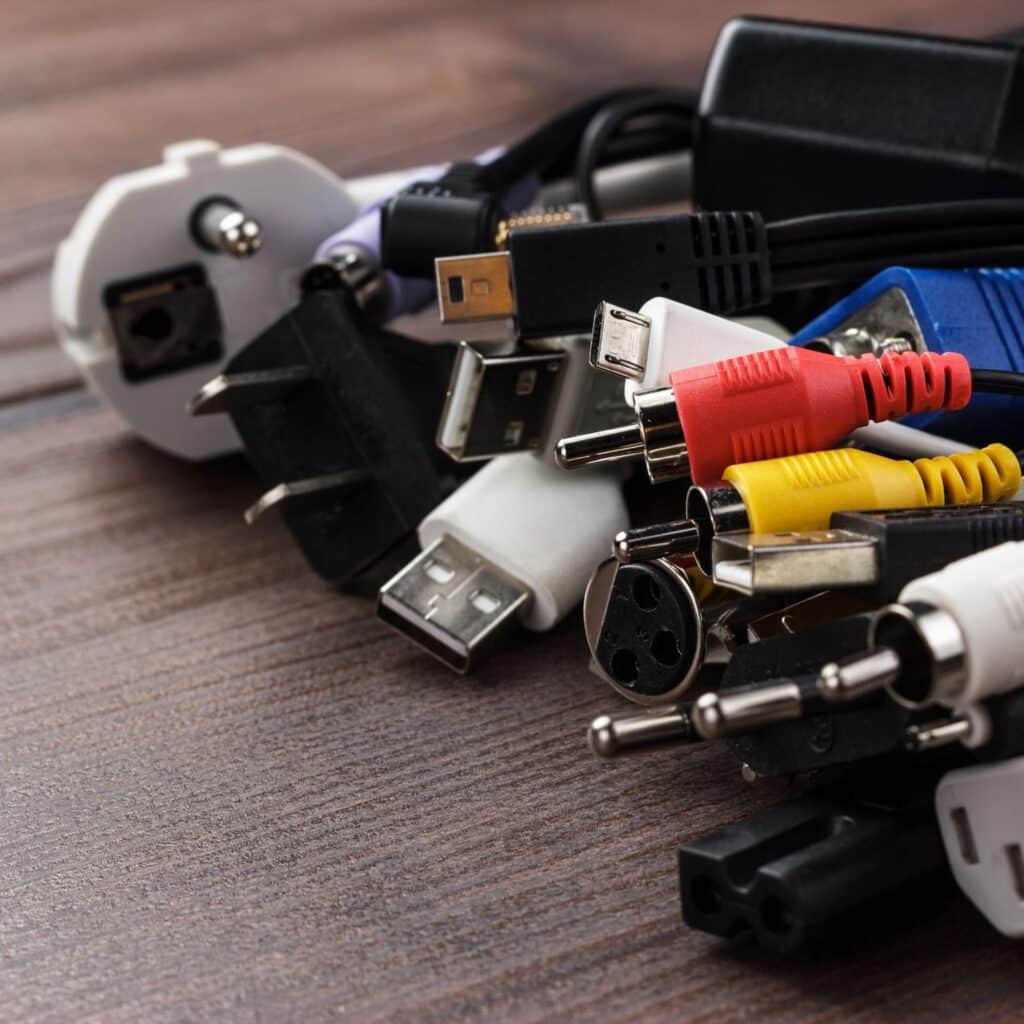
Insert molding creates stronger, more versatile components by seamlessly combining materials in a single production step. This capability delivers significant advantages across numerous sectors, from automotive and medical to electronics and consumer goods.
Automotive
Insert molding is essential for producing durable and reliable automotive components like knobs, threaded fasteners, and electrical housings. By embedding metal inserts into plastic parts, manufacturers create components that can withstand constant mechanical stress and high temperatures under the hood. This process enhances strength and durability while enabling weight reduction, a critical goal in modern vehicle design. The consolidation of parts also leads to significant cost efficiency by eliminating secondary assembly steps.
Medical
In the medical field, precision and consistency are non-negotiable. Insert molding is used to securely embed metal components like surgical tips, needles, or specialized connectors within the plastic body of instrument handles and diagnostic equipment. This creates a single, seamless part that is easy to sterilize and meets strict FDA quality standards, ensuring both reliability and patient safety.
Electronics
Manufacturers use insert molding to embed conductive metal contacts, pins, and structural inserts directly into plastic enclosures and circuit housings. This provides robust protection for delicate internal components while ensuring reliable electrical connections. The design flexibility of this process allows for the creation of compact, multi-functional parts that are essential for today’s smaller and more powerful electronic devices.
Consumer Goods
From kitchen utensils with reinforced metal tips to phone cases with integrated stands, insert molding adds both functionality and durability to everyday products. This technique allows for innovative designs that would be impossible or too expensive to produce with traditional assembly. For example, display cases for diecast models can feature built-in metal adapters for secure mounting, creating a premium, high-value product.
Across all these industries, the ability to consolidate parts into a single molding cycle not only improves performance but also delivers significant environmental benefits by minimizing material waste and energy consumption from secondary assembly processes.
Environmental and Sustainability Considerations
Sustainability plays an increasingly important role in modern manufacturing. Insert molding contributes to eco-friendly strategies by merging components into a single mold cycle, thus reducing the need for separate assembly steps. The process optimizes material usage and power consumption, helping lower overall environmental impact.
Durable, long-lasting parts also reduce the need for frequent replacements, cutting down on resource consumption downstream. As corporate environmental standards grow stricter, adopting advanced manufacturing methods like insert molding aids producers in meeting both regulatory requirements and consumer expectations.
The Future of Insert Molding: Innovations and Trends
Technological advancements indicate a bright future for insert molding. Real-time process monitoring, advanced sensors, and machine learning algorithms help operators optimize molding parameters, predicting potential issues before they escalate. These features enable consistent part production, reduce downtime, and trim maintenance costs.
Additionally, combining additive manufacturing with insert molding presents new opportunities for customized or complex inserts. Engineers can create 3D-printed inserts with intricate internal structures, enhancing thermal management, weight reduction, or specialized functionality. Simulation software continues to mature, providing designers and production teams with sophisticated tools to visualize and refine insert molding efforts at early stages.
As companies seek to produce lighter, stronger, and more sustainable products, insert molding is poised to remain a key technique. Ongoing research into novel polymer blends and hybrid materials will further expand the range of feasible applications, making insert molding even more integral in meeting future market demands.
Choosing the Right Partner for a Successful Insert Molding Project
Selecting the right professional manufacturing partner is critical to a successful insert molding project. A competent partner will possess comprehensive capabilities in product design, prototyping, tooling, manufacturing, and quality control. Their expertise in selecting advanced materials and handling custom inserts is what ensures each product meets rigorous performance standards. An experienced partner simplifies the overall process by offering active communication and collaborative engineering support—effectively bridging the gap between concept and market-ready product.
With more than 40 years of expertise, Pioneer Plastics embodies this partnership approach. Our comprehensive capabilities—covering everything from in-house tool building and rapid prototyping to engineering-grade molding—streamline product development and ensure strict adherence to quality standards for industries ranging from automotive and medical to collectibles and household products.
When you partner with Pioneer Plastics, you gain access to a dedicated team that works closely with you to transform your ideas into impactful, market-ready products. Our problem-solving approach addresses potential challenges like material compatibility and dimensional tolerances early, resulting in optimized designs, reduced time-to-market, and minimized production costs. Whether your project demands small-scale prototyping or large-volume manufacturing, Pioneer Plastics stands ready to deliver high-quality, high-performance insert molding solutions.
Partnering for Success
The insert molding process offers a versatile way to produce high-performance, durable parts by integrating materials like metal, ceramic, or specialty plastics directly into injection-molded components. Companies benefit from reduced assembly costs, improved product longevity, and design flexibility ideal for diverse markets such as automotive, medical, and consumer goods.
To fully realize the potential of insert molding, businesses need precision, advanced materials, and engineering expertise—attributes that seasoned partners like Pioneer Plastics can provide. If you’re looking to simplify production and elevate your product designs, contact Pioneer Plastics to see how this innovative process can meet your requirements. For further guidance and personalized support, explore Pioneer Plastics’ custom injection molding services and discover how their solutions can bring your ideas to life.