3D printing is revolutionizing manufacturing by offering unmatched versatility and creative freedom. When paired with the established efficiency and precision of injection molding, businesses can benefit from improved production workflows, potential cost reductions, and enhanced quality. This integrated approach blends the speed and flexibility of rapid design refinement with the high-volume reliability of injection molding. The result is a dynamic and agile process—one that enables quick prototypes, small-batch production, and ultimately, a smooth transition into large-scale manufacturing.
Innovation is the heartbeat of modern production. Whether you’re testing early designs or perfecting product details, 3D printing facilitates rapid iterations at lower costs and risks. Injection molding, known for its precision and scalability, builds on these iterative benefits. Together, these complementary methods shape a streamlined workflow—from initial concept to market-ready product—that empowers businesses to stay ahead of trends, reduce supply chain disruptions, and respond promptly to customer demands.
At Pioneer Plastics, we leverage over 60 years of injection molding expertise alongside state-of-the-art in-house 3D printing. Our integrated process covers rapid prototyping, custom small runs, and seamless transitions into full-scale production. Below, we’ll explore the synergy between 3D printing and injection molding, their distinct benefits, and how Pioneer Plastics stands ready to help transform your ideas into exceptional products.
Exploring the Synergy between 3D Printing and Injection Molding
In today’s fast-evolving manufacturing landscape, the demand for efficiency, flexibility, and innovation is on the rise. By pairing 3D printing with traditional injection molding, companies gain the best of both worlds: the agility of quick prototyping and the robust capacity required for mass production. This innovative union slices development timelines, minimizes upfront costs, and enhances final product quality—crucial for industries such as consumer goods, collectibles, and packaging.
3D printing accelerates design experimentation, enabling faster tweaks in shape, size, and materials. Injection molding then scales these refined prototypes to large output. 3D printing complements rather than competes with injection molding. While injection molding still reigns for high-volume output, 3D printing excels in the product’s early stages by:
- Reducing design risks before expensive mold creation
- Enabling rapid, cost-effective iterations and custom configurations
- Allowing flexible, small-batch runs for concept validation
Research indicates that integrating additive manufacturing (AM) with injection molding can substantially streamline product development cycles by accelerating prototyping and critical design iterations, though exact reduction percentages vary with specific applications. These methods let designers explore complex geometries, verify functionality, and pinpoint refinements prior to committing to large-scale molding.
3 Common Uses for 3D Printing in the Injection Molding Industry
Integrating 3D printing yields invaluable opportunities to tackle manufacturing challenges. Below are three ways it amplifies efficiency and creativity:
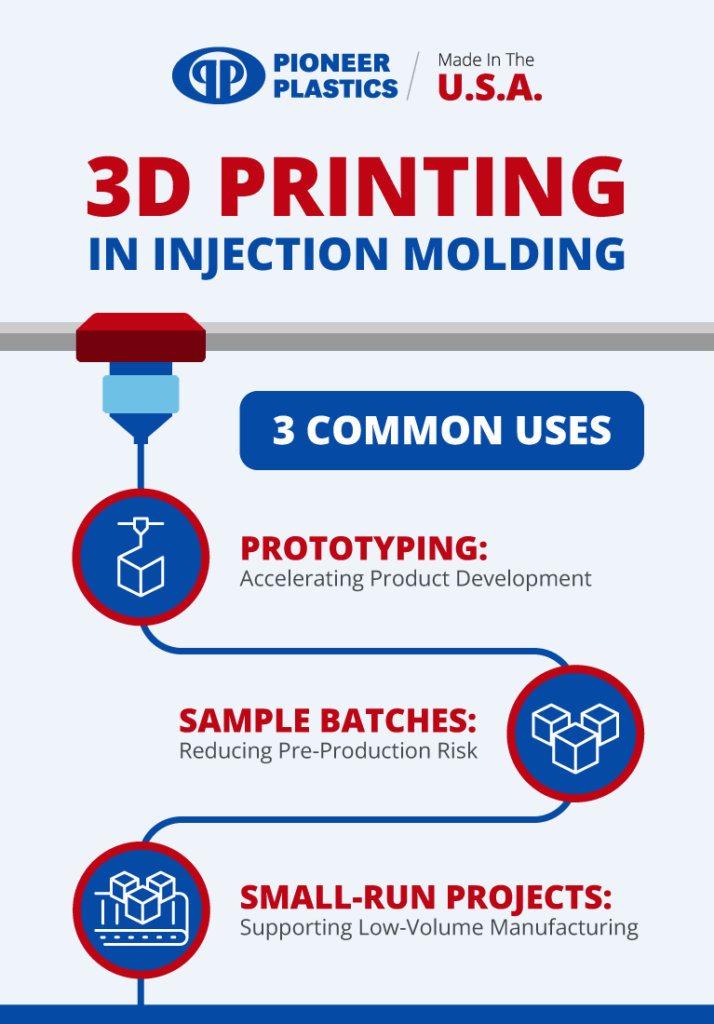
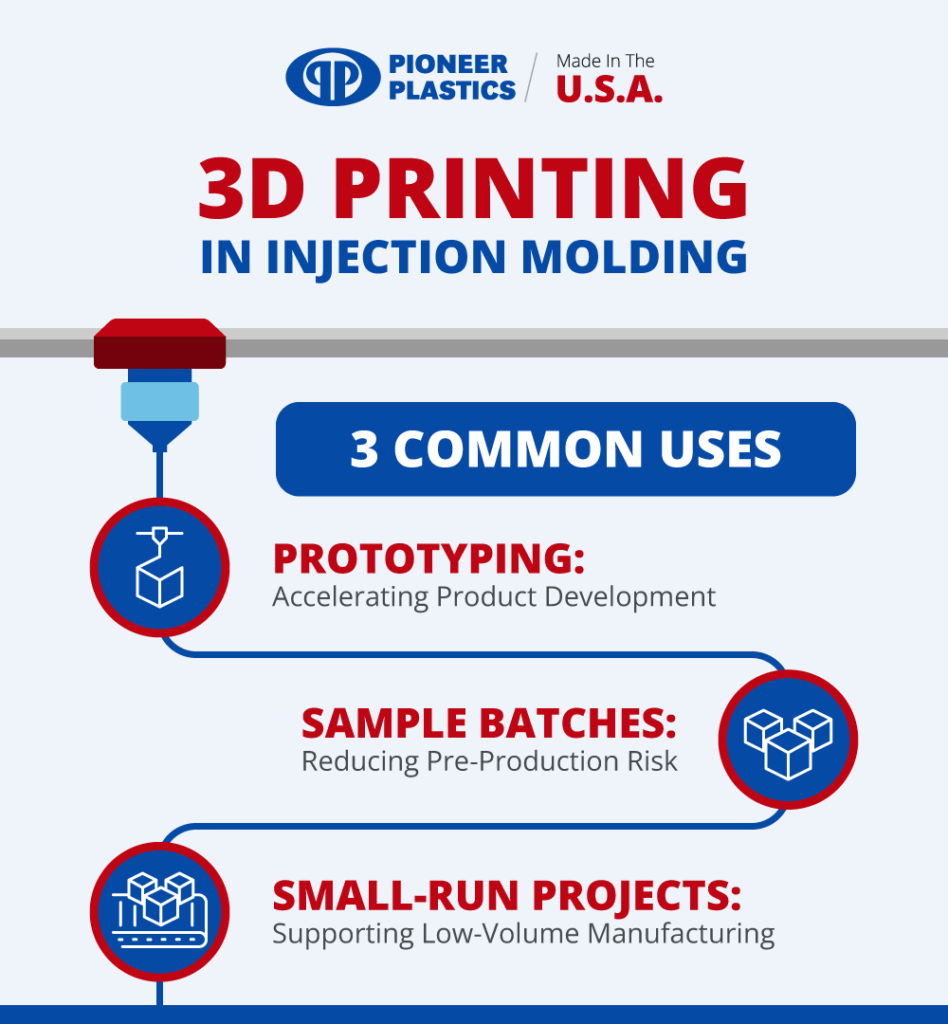
1. Prototyping: Accelerating Product Development
Prototyping with 3D printing revolutionizes how new products are tested. Benefits include:
- Rapid development of prototypes for design verification
- Frequent, cost-effective design modifications without significant time penalties
- Early evaluation of aesthetics, functionality, and overall user experience
For instance, a designer creating a custom collectible display case can 3D print a sample to gauge proportions and structural integrity. Quick iterations help refine the end product before injection molding begins.
2. Sample Batches: Reducing Pre-Production Risk
3D printing is ideal for limited sample batches that bridge the gap between prototyping and large-scale output. This approach:
- Validates core designs with minimal financial outlay
- Enables real-world testing to confirm performance and user satisfaction
- Identifies final enhancements before costly mold creation
Many companies rely on these small batch production strategies to test their products in real environments, avoiding the expense and risk of mass-scale molding until final design details are locked in.
3. Small-Run Projects: Supporting Low-Volume Manufacturing
When demand is project-specific or specialized, 3D printing is a practical solution. It offsets high upfront tooling costs and offers:
- Low-volume production without expensive molds
- Customized or brand-specific elements for niche markets
- Lean operations, since items can be produced on demand
As an example, a startup might create a short run of custom plastic housings to satisfy initial orders without overcommitting to tooling investments.
Advantages of Integrating 3D Printing with Injection Molding
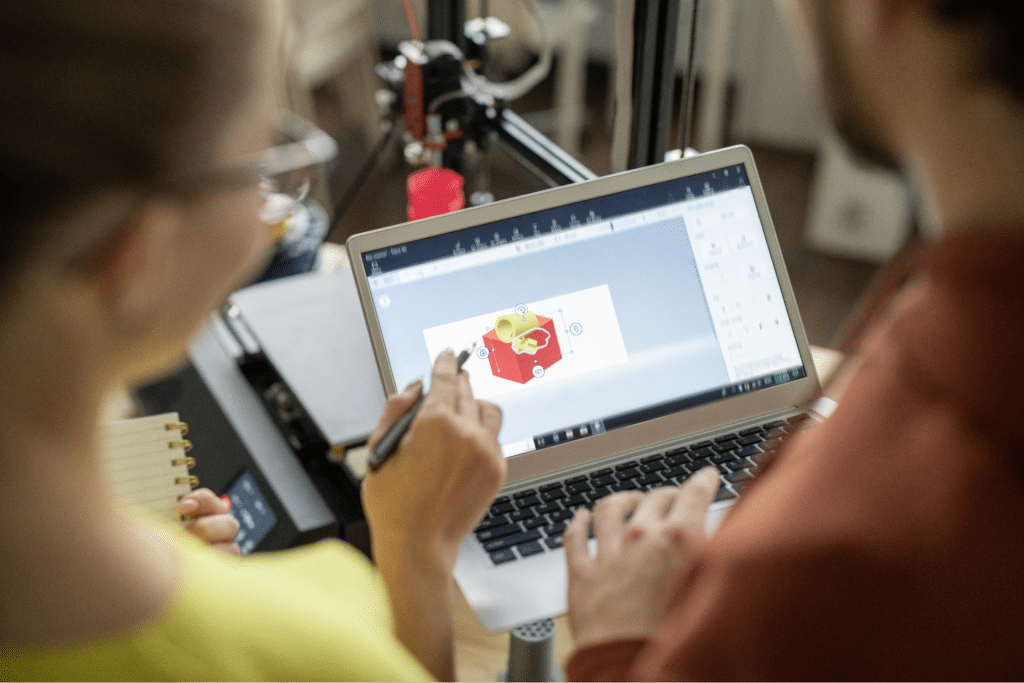
Uniting 3D printing with injection molding amplifies the strengths of both processes for a well-rounded manufacturing strategy. Hybrid manufacturing merges multiple technologies to boost productivity and adapt quickly.
Early Design Validation and Reduced Risk
- Detects and corrects design issues before investing in molds
- Reduces the likelihood of major errors at later stages
- Yields refined prototypes ready for scaling
Accelerated Development Timelines
- Shortens feedback cycles from weeks to days
- Facilitates faster time-to-market for new products
- Improves the efficiency of iterative design testing
Tangible Cost Savings
- Avoids premature mold expenditures
- Curbs rework through early design refinement
- Optimizes overall costs for high-volume production
Enhanced Design Flexibility
3D printing grants unmatched versatility in form and structure:
- Allows integration of complex geometries that may be impossible to mold directly
- Balances standard molded components with custom printed ones
- Adapts rapidly to shifting market requirements
Seamless Transition from Prototype to Production
Partnering with a single provider for both 3D printing and injection molding paves the way for:
- Consistent quality checks at every stage
- Reduced communication gaps between different teams
- A unified workflow that respects the original design intent
By adopting these integrated manufacturing strategies, companies can continually adapt to emerging trends and materials, securing a competitive edge in the long term.
Pioneer Plastics 3D Printing Services
At Pioneer Plastics, we merge decades of injection molding expertise with modern 3D printing to deliver a holistic manufacturing experience. Our comprehensive capabilities and state-of-the-art equipment allow clients to move from concept to full production smoothly, reducing risk and boosting return on investment.Our solutions cater to every phase—from inception to final product.
Our In-House Techniques
We offer Stereolithography (SLA) for exceptional detail with light-cured resin and Fused Deposition Modeling (FDM) for strong, functional parts using thermoplastics. These techniques allow us to offer a wide variety of 3D plastic parts.
Our Process
Our team begins the process by meticulously reviewing your 3D model files to ensure optimal design execution. This involves providing expert insights on necessary dimension adjustments and appropriate material choices to enhance the product’s functionality and aesthetic appeal. We then proceed with printing prototypes for thorough functional trials, consistently verifying quality at each stage. Based on the feedback received from these trials, we implement strategically targeted improvements before moving to large-scale production. By integrating 3D printing with our comprehensive engineering services, we guarantee that your designs are subjected to rigorous testing and refinement, significantly mitigating the risk of unforeseen complications during production.
Tailored Solutions for Custom Requirements
At Pioneer Plastics, we understand that customization is a crucial aspect of our service, and we offer tailored solutions to meet your specific requirements. Our team can even modify standard Pioneer Plastics products with unique features to better align with your needs.
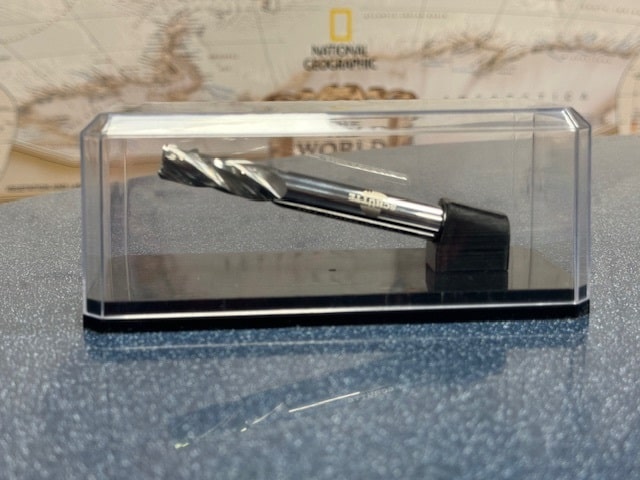
Seamless Transition to Injection Molding
When your design has reached its final iteration, our mold-building experts work closely with our 3D printing team to ensure a smooth and efficient transition to injection molding. This collaboration guarantees that dimensional accuracy is maintained from prototype to mold, ensuring that your design objectives are preserved in every detail. With production timelines streamlined under one roof, we provide comprehensive guidance in material selection tailored to your product’s needs.
Exceptional Support Throughout the Process
Our 60+ years in the industry have forged a culture of reliability at Pioneer Plastics. We provide personalized guidance from an experienced engineering team who is dedicated to achieving high standards of accuracy for both prototypes and full-scale products. Our flexible options cater to both short and long runs, ensuring that we can meet a diverse range of manufacturing needs with precision and efficiency.
Maximizing Innovation through Integrated Manufacturing Solutions
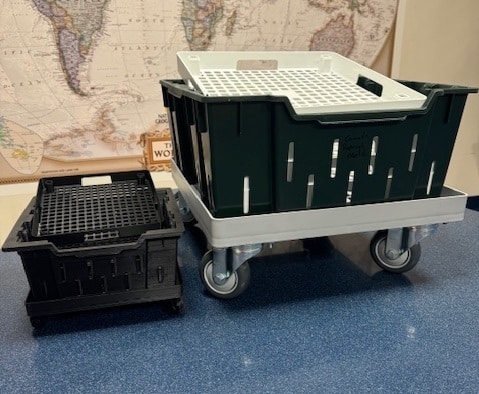
Integrating 3D printing with injection molding reshapes modern production by combining quick prototyping, small-scale pilot runs, and flexible iterations with the robust output of large-volume manufacturing. Businesses that fuse these technologies gain the advantage of reduced risk, accelerated timelines, and thorough design optimization.
At Pioneer Plastics, our specialized team harnesses the power of 3D printing alongside decades of injection molding expertise. Under one roof, we unify 3D printing and injection molding, backed by decades of practical experience. This dual proficiency keeps communication fluid, reduces lead times, and ensures high-quality outcomes—from first prototype to large-scale run.
Contact Pioneer Plastics today to explore how our 3D printing services can elevate your production strategy. We also invite you to learn more about our custom injection molding capabilities and discover our range of custom plastic solutions. Let our knowledge, cutting-edge technology, and proven processes guide you confidently from initial idea to market success.