Sourcing custom plastic parts is a critical phase in product development and manufacturing. Whether you’re producing specialized components for industrial machinery, creating unique packaging solutions for the food industry, or crafting robust display cases for collectibles, the decisions you make during this stage can significantly impact cost, product quality, and time to market. Even minor oversights—such as choosing the wrong materials or underestimating production timelines—can cause sizable production delays, expensive redesigns, and disappointed end users.
These challenges can be avoided by taking a methodical approach and partnering with an experienced injection molding company that understands both the technical intricacies and broader market demands. An expert manufacturer can offer guidance on custom injection molding, product design, material selection, and scheduling from the earliest stages. They can also provide advanced engineering services for plastics to transform your idea into a finished product that meets both performance standards and budgetary constraints.
This guide addresses six common mistakes that organizations and individuals make when sourcing custom plastic parts, providing you with valuable insights on how to find the right balance between cost and quality. You’ll also learn about additional strategies—such as embracing flexibility and continuous improvement—that further minimize risks and optimize outcomes. By investing in thoughtful planning, clear communication, and reliable partnerships, you can steer your project toward success from conception to completion.
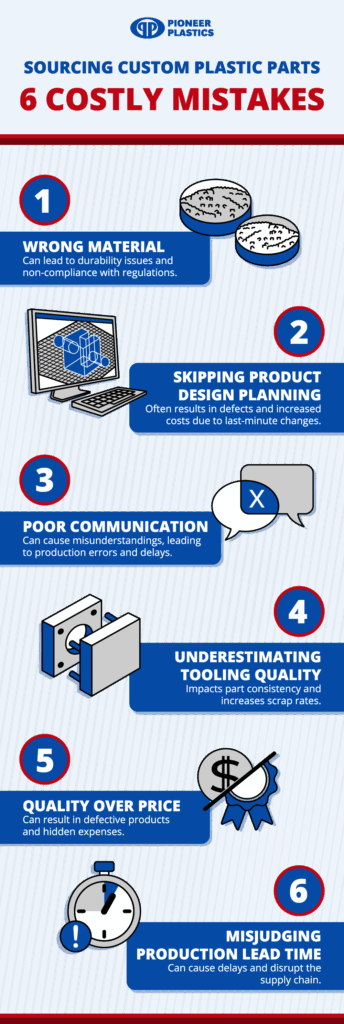
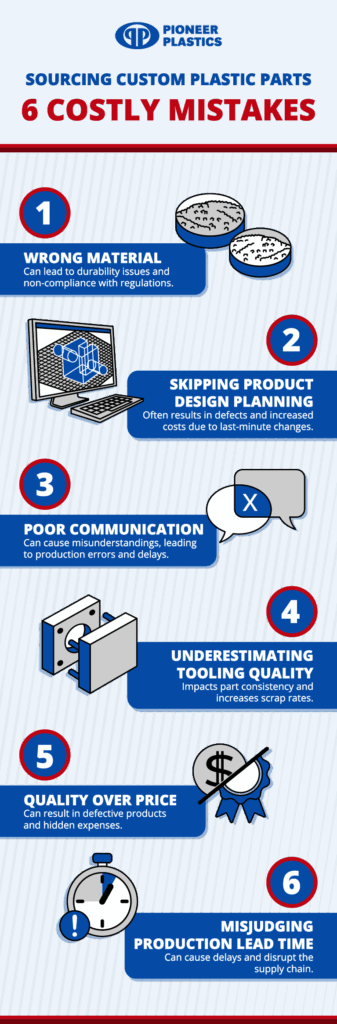
Mistake #1: Neglecting to Select the Right Material
Materials form the backbone of every plastic product. Selecting a resin that can withstand environmental conditions, operational stresses, and regulatory requirements is critical for ensuring the overall reliability of your custom parts. Disregarding the importance of proper material selection can lead to a host of issues, such as warping, cracking, or failing to meet safety standards. Low-grade plastics may reduce upfront costs but often compromise the part’s durability and longevity.
These material pitfalls are especially relevant in industries with strict regulations, such as food packaging, where food-safe plastics must be used to ensure compliance and consumer wellbeing. Similarly, any component subject to high stress or temperature extremes requires engineering-grade resins specifically designed for durability and impact resistance.
To avoid this mistake, consult with expert engineering teams—like those at Pioneer Plastics—to identify the resin that best matches your project’s functionality and budget. Consider the product’s end-use environment, mechanical requirements, and any compliance certifications needed. By testing sample materials early and ensuring they meet both performance goals and safety standards, you can evade costly recalls and guarantee a better end-user experience.
Mistake #2: Overlooking Thorough Product Design Planning
Comprehensive product design is another foundation of successful custom injection molding. A well-structured design takes into account factors like mold flow, part geometry, and the need for consistent wall thickness. Overlooking these considerations often causes defects such as sink marks, uneven cooling, or structural weakness. Additionally, last-minute changes to critical features—like draft angles or gate placement—can incur sizable overtime costs and complicate production timelines.
The best way to prevent these challenges is to engage in close collaboration with a manufacturer’s design and engineering team early on. Sharing 3D models, rough prototypes, or even functional mock-ups allows experienced engineers to pinpoint potential trouble areas, suggest improvements, and validate design concepts prior to full production. These collaboration points can also foster creative problem-solving, ensuring the final design supports efficient manufacturing without compromising functionality or appearance.
By integrating robust design planning with realistic manufacturability checks, you reduce the likelihood of mid-production changes and help your product reach the market faster. Capturing each stage of your design revisions, whether through formal documentation or digital revision tracking, keeps everyone aligned and allows for a more accurate estimation of costs and timelines.
Mistake #3: Underestimating the Importance of Communication
Effective communication throughout the manufacturing process is often the difference between a smooth launch and a project fraught with setbacks. Even minor misunderstandings—such as ambiguous design notes or incomplete feedback—can lead to production errors that derail scheduling and inflate budgets. Poor communication also increases the risk of using outdated specifications, particularly if there are multiple design iterations.
Maintaining consistent dialogue, supported by clear documentation of any changes or updates, is key to avoiding confusion. Regularly scheduled check-ins enable both the client and the manufacturer to raise concerns if something appears off-track, allowing for timely course corrections. This level of transparency fosters trust and reliability, as both parties remain fully aware of how the project is progressing.
At Pioneer Plastics, priority is placed on open lines of communication, ensuring that questions are answered promptly and any technical clarifications are thoroughly addressed. If you want to learn more about best practices in manufacturing communication, consistent contact with production partners can help fine-tune the design, verify material selections, and confirm project milestones, thereby minimizing the risk of costly oversights.
Mistake #4: Overlooking the Critical Role of Tooling
The quality of your tooling directly impacts the consistency, dimensional accuracy, and surface finish of your custom plastic parts. In injection molding, a well-made mold can last through countless production runs, maintaining tight tolerances that keep your parts uniform. Conversely, underestimating the importance of precision tooling can drag out lead times and skyrocket scrap rates.
Investing in robust tooling may carry higher initial costs, but it quickly pays for itself by reducing maintenance, rework, and rejected batches. High-quality molds also ensure that the aesthetic and functional aspects of your parts remain reliable and intact over time. For example, collectible display cases, which often have tight tolerances and require a clear, clean finish, significantly benefit from a carefully engineered mold designed to reduce gate marks or flow lines.
Choosing a manufacturer with in-house tool building services streamlines the revision process and allows for faster turnaround. If a design tweak is needed or if unexpected wear and tear arise, having immediate access to tooling experts accelerates adjustments. This synergy between tooling refinement and production floor feedback helps avoid production delays and maintains a consistently high standard of quality.
Mistake #5: Prioritizing Price Over Quality
In any manufacturing project, cost-consciousness is important. However, placing too much emphasis on securing the lowest per-unit price often leads to larger issues that can negate any initial savings. Suppliers who offer bargain pricing might cut corners on material quality, operational safety measures, or inspection protocols. As a result, you risk receiving batches of defective products requiring expensive fixes or complete re-runs.
Evaluating a manufacturer’s production capacity and quality control system can reveal the potential for hidden costs. Features like a well-documented quality control process, dedicated testing labs, and thorough operator training usually translate to fewer production standstills and more consistent results. Such elements may slightly increase the quoted price, but the premium pays off by reducing the likelihood of part failures and missed deadlines.
When analyzing quotes, consider the total cost of ownership. This includes the time spent on corrective measures, the possibility of reversing major design mistakes, and the intangible cost of damaging your reputation with clients or end users. Selecting a partner like Pioneer Plastics, which balances competitive pricing with uncompromising quality, can help you establish a foundation that supports your business for the long term.
Mistake #6: Misjudging Production Lead Times
Time is critical in the manufacturing world. Underestimating the time it takes to develop tooling, refine designs, and work through production trials can lead to unnecessary stress and cascading delays across your supply chain. While it’s tempting to set ambitious deadlines, failing to account for potential hiccups—like material shortages or complex mold revisions—often forces last-minute rushes that jeopardize quality.
A thorough timeline should include built-in buffer periods that can absorb unplanned obstacles. This approach offers room to address unforeseen revisions or small production snags without derailing the entire schedule. Additionally, open communication with your manufacturer at each key milestone ensures that any creeping delays are identified and mitigated early. If you’re curious about managing lead times effectively, planning well ahead allows you to keep production running smoothly.
Careful timeline management also extends to post-production activities such as assembly, packaging, and shipping. By mapping these processes accurately, you can streamline distribution to your target market. An experienced injection molding company can help you gauge realistic time frames for each stage, giving you the confidence to coordinate further logistics without guesswork.
Embracing Flexibility and Continuous Improvement
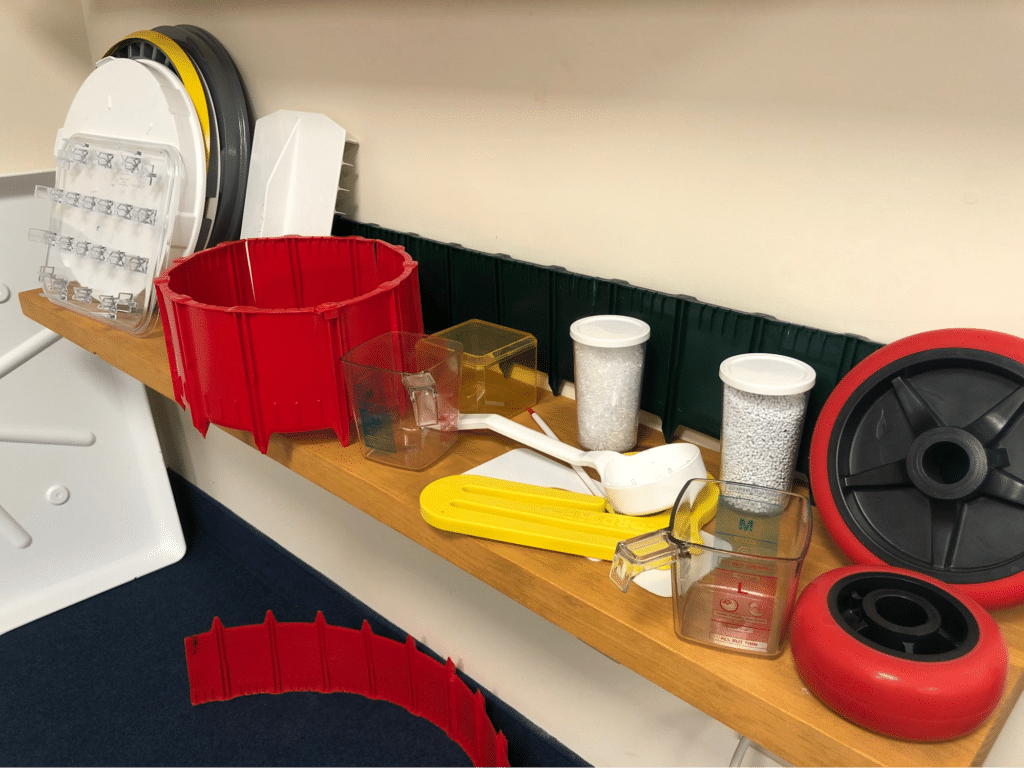
Beyond the six primary pitfalls, success in custom plastic part sourcing often hinges on a willingness to adapt. Market demands can evolve rapidly, and manufacturing technologies are continually advancing. Forward-thinking companies encourage a culture of continuous improvement, seeking to refine processes, adopt new techniques, and integrate innovative materials that can enhance product performance.
Flexibility includes being ready to pivot if your target market expands or if you decide to modify your plastic part’s functionality. When your manufacturing partner offers agile production options—such as the ability to handle both small runs for prototyping and large runs for full-scale manufacturing—you can adapt more quickly to emerging opportunities. Pursuing these improvements incrementally helps maintain momentum while guiding you ever closer to optimal efficiency.
Staying open to change also means reevaluating existing capabilities, from rethinking mold designs to exploring proprietary plastic products that can complement your offering. By embracing ongoing improvements, you are more likely to reduce cost, improve product quality, and maintain a competitive edge.
Ongoing Quality Assurance and Performance Monitoring
Quality assurance doesn’t stop once the mold is built—it should be a continuous process throughout the product’s lifecycle. Implementing rigorous performance monitoring at regular intervals helps you spot early signs of potential defects, wear in tooling, or increasing variance in production runs. This kind of proactive evaluation allows you to make small corrections before they escalate into systemic problems.
In practical terms, this means setting clear metrics for acceptable tolerances, color consistency, and structural integrity. Regular audits—whether conducted in person or via remote data collection—give you confidence that the manufacturing process remains aligned with your quality goals. By incorporating precision measurement, statistical sampling, and part testing under real conditions, you establish a feedback loop that sustains excellence over time.
Working collaboratively with a manufacturer that values continuous improvement ensures that each production run is at least as good as the last—and often better. This ongoing effort reinforces trust between both parties and helps maintain a steady flow of high-quality products that meet or exceed customer expectations.
Achieve Success with the Right Manufacturing Partner
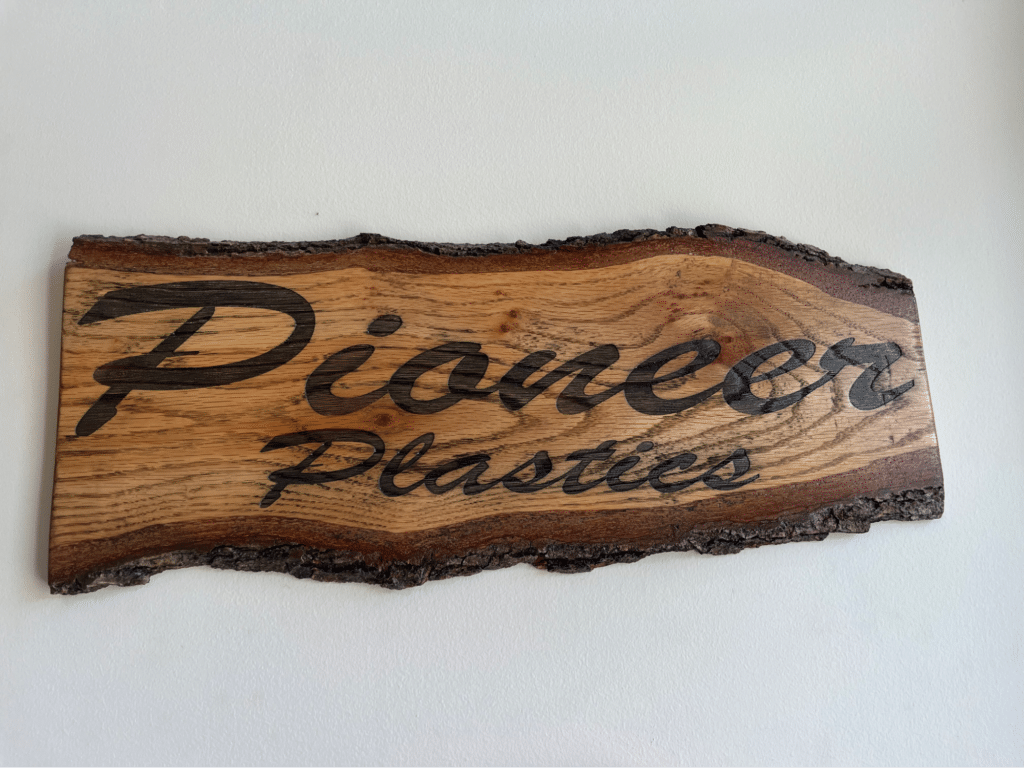
Avoiding costly mistakes in sourcing custom plastic parts starts with making informed, strategic decisions at each phase. From selecting the right resin and developing robust part designs to fostering open communication and planning realistic schedules, every step you take can either mitigate or magnify risk. Thoughtful preparation ultimately leads to higher-quality products, fewer reworks, and more satisfied customers.
Equally important is the partnership you choose. An experienced, trustworthy manufacturer provides you with a wealth of knowledge and streamlined processes that remove guesswork from the equation. Pioneer Plastics has the expertise to handle custom injection molding, tooling, engineering services, and custom plastic parts manufacturing, ensuring that your concepts transition seamlessly into production.
Ready to reduce risks and achieve reliable production outcomes? If you’d like to learn how Pioneer Plastics can be the right fit for your custom plastic part needs, contact us today to transform your sourcing journey into a streamlined, cost-effective path from concept to completion.