Injection molding has drastically changed the way everyday items are produced. The process involves melting plastic pellets and injecting them into custom molds to create detailed, consistent products that meet modern standards for durability and design. Thanks to precision engineering, advanced tool building, and skilled craftsmanship, injection-molded items are reliable, lightweight, and safe for daily use.
Additionally, this process provides a cost-effective route for large-scale production. Manufacturers can achieve high output at relatively low per-unit costs, making top-quality products more accessible. Injection molding also allows for rapid prototyping and shorter lead times—key benefits for businesses striving to stay ahead in fast-paced markets. The technology accommodates diverse material options, including engineering-grade plastics, ensuring an ideal balance of strength, temperature resistance, and aesthetics. This flexibility has sparked an ongoing wave of innovation, prompting designers to push the boundaries of form and function.
Below, we delve into the top ten household items shaped by injection molding and examine how they enhance our daily routines.
1. Food Storage Containers
Food storage containers are a kitchen staple, vital for keeping leftovers fresh and organizing pantry items. Injection molding ensures these containers have uniform walls and secure sealing mechanisms, preserving food quality. Many people also rely on clear plastic containers for better visibility when storing and locating food.
How Injection Molding Enhances Food Storage Containers
- Airtight Seals – Custom-designed lids lock in freshness and prevent leaks.
- Consistent Strength – Uniform construction withstands daily cleaning and temperature changes.
- Food Safety – Certain food-safe plastics, such as many containers labeled for microwave and dishwasher use, are designed to endure these conditions safely.
In addition, injection molding allows manufacturers to introduce features like integrated measuring guides or snap-in compartments for portion control. Even subtle design elements—such as contoured corners for easier pouring—stem from the precision of this approach. When you combine durability, clarity, and space-saving stackability, it’s clear why injection molding is a go-to method for bringing high-quality food storage containers to market.
2. Plastic Utensils and Kitchenware
Everyday kitchen tools—such as spatulas, cutting boards, and plastic utensils—benefit from the precision of injection molding. This process guarantees that each utensil is designed for functionality and ease of use, offering consistently high standards in form and finish.
How Injection Molding Elevates Kitchen Tools
- Heat Resistance – Specially engineered plastics resist deformation in moderate cooking temperatures.
- Ergonomic Design – Contoured handles and textured grips reduce hand fatigue during prolonged use.
- Smooth, Seamless Surfaces – Minimize areas where food particles can accumulate, making maintenance simple.
Some plastic utensils and cookware feature reinforced edges or dual-material construction for added resilience. This is especially useful for items like tongs or spatulas that undergo frequent wear. As a result, homeowners enjoy long-lasting, affordable pieces that look stylish in any kitchen setting. Pioneer Plastics’ expertise in custom injection molding also enables the creation of proprietary designs and quick modifications, ensuring each customer’s requirements can be met promptly.
3. Organizational Storage Bins and Boxes
Keeping a home organized is made easier with thoughtfully designed storage bins and boxes. Injection molding delivers products with structural integrity and a uniform look, essential for storing seasonal items, toys, or craft supplies. Rapid prototyping combined with short-run flexibility allows manufacturers to cater to niche organizational needs without compromising quality.
How Injection Molding Improves Storage Solutions
- Stackability – Integrated grooves allow for secure stacking, optimizing space indoors.
- Enhanced Stability – Consistent wall thickness and reinforced edges ensure these items bear heavy loads.
- Custom Designs – A variety of sizes and colors cater to different storage needs, whether for hobby supplies or seasonal décor.
Additional features can include built-in clipboard compartments or labeled slots for quick identification. Optimized mold designs further improve material efficiency, reducing weight while maintaining strength.
4. Bathroom Accessories
Every bathroom accessory—from soap dispensers to toothbrush holders—must withstand moisture, heat, and constant cleaning. Injection molding produces these items to be both resilient and visually appealing, with uniform finishes that resist discoloration and daily wear.
How Injection Molding Benefits Bathroom Accessories
- Waterproof Durability – High-quality plastics resist water damage and chemical degradation.
- Hygienic Finish – Smooth surfaces reduce areas where bacteria can accumulate, simplifying upkeep.
- Design Flexibility – Custom color palettes and finishes allow these products to complement a wide range of bathroom décors.
Some designs incorporate suction cups or weighted bases for additional stability. By leveraging injection molding, manufacturers can seamlessly integrate intricate details, such as textured surfaces or decorative patterns, without compromising structural integrity. This approach ensures that bathroom accessories can blend style with practical performance for a truly modern space.
5. Home Décor Items
Injection molding is not just about utility; it also plays a significant role in modern home décor. Lampshades, picture frames, and decorative storage containers enhance interiors through intricate shapes and premium finishes.
How Injection Molding Enhances Home Décor
- Lightweight and Practical – Décor items are easy to handle and reposition as trends change.
- Design Versatility – Complex patterns and textures are achievable, offering high-end aesthetics at a lower cost.
- Affordable Elegance – Homeowners can enjoy stylish, durable pieces that look polished and contemporary.
- Longevity – Injection molding supports color stability and impact resistance, ensuring décor pieces maintain their vibrancy and shape over time.
From minimalist sleek lines to ornate patterns, the flexibility of this process accommodates a full spectrum of designer preferences.
6. Children’s Toys
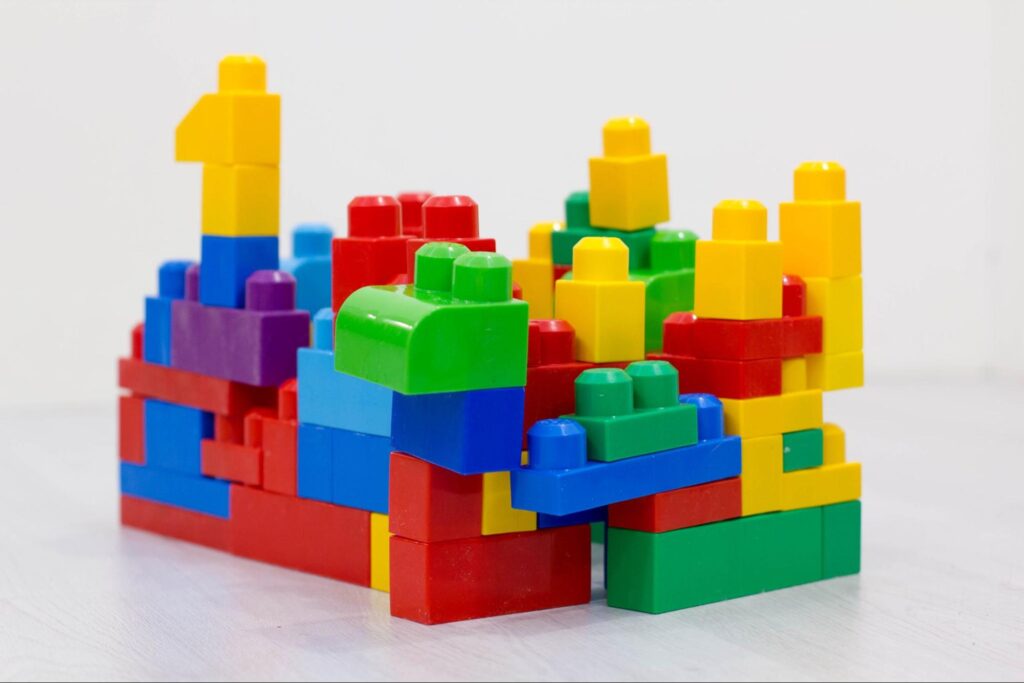
Safety and durability are crucial when it comes to children’s toys. Injection molding allows manufacturers to produce toys that meet stringent safety standards while offering engaging designs that inspire creativity. Some collectors even use diecast display cases to protect toy car collections or model vehicles, underscoring the importance of quality plastic manufacturing for both play and preservation.
Why Injection Molding Is Essential for Toy Production
- Child-Safe Design – Smooth, rounded edges minimize injury risk during play.
- Vibrant Colors – Integrated pigments provide bright, fade-resistant hues that delight children.
- Detail and Precision – Intricate mold designs yield complex shapes and textures that spark imagination.
The ability to combine multiple plastics in a single component means toys can have soft-touch sections and rigid frames in the same product. Features like snap-fit components also allow for easy assembly or part replacement. By offering an array of size and color options, injection molding caters to wide-ranging themes and characters loved by younger audiences.
7. Household Maintenance Supplies
Everyday maintenance tools, such as buckets, toolboxes, and dustpans, rely on injection molding for their rugged durability and lightweight design. They are engineered to handle the toughest household tasks, from mopping floors to organizing hardware in a garage.
Why Injection Molding Excels in Maintenance Supplies
- Superior Durability – High-strength plastics withstand impacts and daily wear.
- Ergonomic Features – Built-in handles and balanced designs reduce physical strain.
- Lightweight Construction – Despite their robustness, these items are easy to transport and handle.
This efficient design process ensures that your household maintenance supplies are built to last, making day-to-day chores more manageable. Many of these products include molded-in hooks, clips, or measuring lines, extending functionality without adding extra components.
8. Electrical Accessories
Electrical accessories such as cord grips, outlet covers, and cable organizers require precise dimensions and materials that guarantee safety. Injection molding delivers these components under tight tolerances and high standards, protecting homes and workplaces from potential hazards.
How Injection Molding Enhances Electrical Accessories
- Excellent Insulation – High-grade plastics naturally resist heat and provide safe electrical insulation.
- Precision Fit – Consistent manufacturing ensures perfect fits, reducing hazards.
- Long-Lasting Finish – Scratch-resistant surfaces maintain a clean look over time.
Many modern devices come with cable management built into their design, often created through specialized molding techniques. Elements like hinged covers or sliding compartments can be seamlessly incorporated.
9. Scrapbook and Craft Storage Solutions
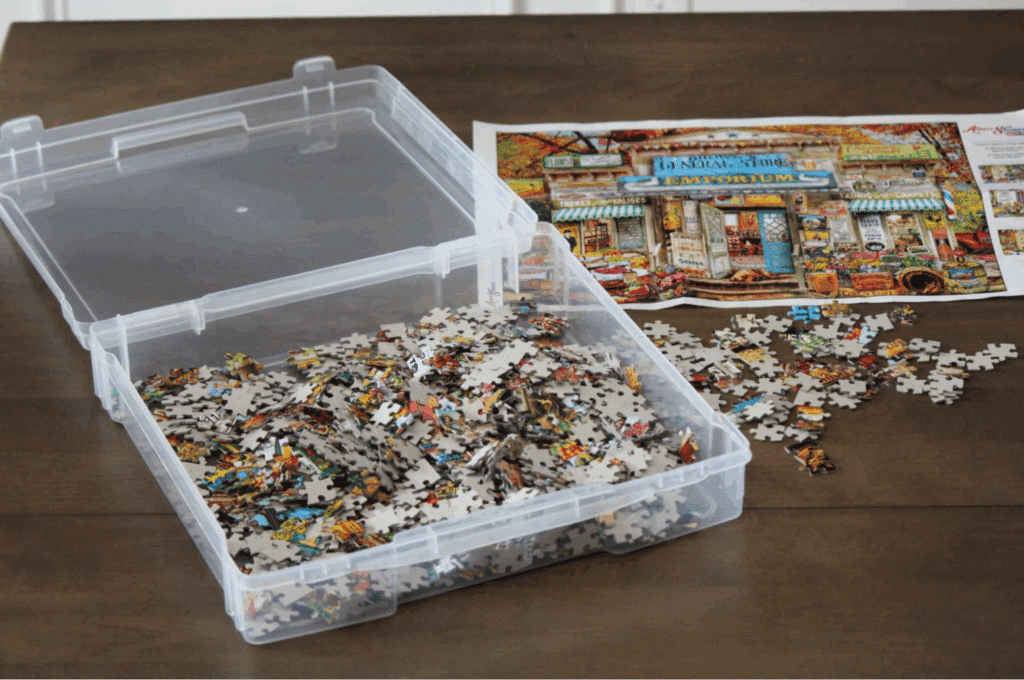
For artists and hobbyists, efficient organization of supplies is essential. Injection molding creates storage solutions that are both functional and attractive, from stackable bins with flip-top lids to color-coded compartments that simplify sorting.
Why Injection Molding Matters for Craft Storage
- Custom Compartments – Cleverly designed interiors help separate a variety of craft materials.
- Dependable Materials – Durable plastics resist wear from frequent use, ensuring long-term performance.
- Transparent Options – Clear materials allow quick location and easy access to stored items.
In some cases, manufacturers add modular inserts that snap in and out, allowing individuals to customize storage arrangements as needed. Because injection molding accommodates precision tooling, these inserts fit snugly without wasting interior space. This capability is essential for crafters dealing with items like beads, ribbons, and embellishments that can easily get mixed up.
10. Drink and Plate Combination Products
Host gatherings with ease using drink-and-plate combination products, which integrate a plate with a built-in drink holder. Injection molding makes it possible to blend functionality with clever design innovations ideal for parties and casual dining.
Benefits of Injection Molding for Drink-and-Plate Products
- Ergonomic Integration – Thoughtful design features ensure comfort during use.
- Spill-Resistant – Raised edges and drainage channels help contain spills and simplify clean-up.
- Versatile Compatibility – Custom molds accommodate a range of cup sizes, making these products adaptable for any event.
Such items often incorporate subtle details like thumb grips or indented grooves for secure handling. By limiting the need for multiple utensils or balancing acts, these combination products transform how groups gather around food. They also leverage the inherent flexibility of injection molding, allowing for color variations and brand personalization.
Technological Innovations in Injection Molding
The field of injection molding is continuously evolving as new technologies push the boundaries of what is possible. Recent advancements have improved production efficiency and enabled the creation of more complex, customized products. One area of growth is micro injection molding, a technique that allows for extremely small components with intricate features—often seen in medical devices and electronics.
Automation and real-time quality monitoring systems have further streamlined production, resulting in shorter lead times and reduced waste. Moreover, sophisticated 3D simulations help predict how molten plastic will flow inside a mold, enabling manufacturers to optimize designs before production begins. This not only cuts down on costly revisions but also boosts the production of ultra-precise parts for industries like electronics, automotive, and healthcare.
Pioneer Plastics continues to invest in these emerging technologies, applying them to projects that demand custom injection molding solutions. Their tool-building services provide a quick turnaround, allowing businesses to respond to changing market trends without sacrificing product quality. Drawing from a wealth of industry knowledge, each step of the manufacturing process is continually refined to help ensure efficiency and reliability across a wide range of applications.
Sustainability and Future Trends in Injection Molding
Beyond practical applications, injection molding is central to sustainable manufacturing. The process maximizes material usage, reduces waste, and increasingly incorporates recycled and bio-based plastics. As environmental considerations take center stage, companies are opting for greener materials and sophisticated recycling programs.
Key Sustainability Benefits
- Material Efficiency – Optimized mold design reduces material consumption.
- Energy Conservation – Modern machines and process controls help minimize energy usage.
- Environmentally Friendly – The growing use of recycled plastics and biodegradable polymers supports a circular economy.
Future Trends
The future of injection molding lies in automation and smart systems that refine quality control while minimizing waste. As demand for eco-friendly products rises, ongoing innovations promise even more sustainable and cost-effective solutions. Some manufacturers are also exploring the role of additive manufacturing for prototyping, merging 3D printing with injection molding to further shorten development cycles.
Pioneer Plastics embraces these trends, focusing on incorporating environmentally friendly strategies. They work with clients to identify materials and production approaches that balance ecological responsibility with performance requirements. This holistic approach allows businesses to differentiate their products in a crowded marketplace.
Collaborative Design and Customization
A critical advantage of injection molding is its flexibility in collaborative design throughout product development. Pioneer Plastics works closely with clients from the initial concept to final product testing. This teamwork ensures that every molded part meets precise specifications and aligns with unique requirements. Clients can participate in design reviews and prototyping, enabling rapid modifications to meet market feedback.
Furthermore, advanced simulation software allows manufacturers to predict product performance under various conditions, ensuring both durability and functionality. This collaborative process not only enhances product quality but also offers cost-saving benefits compared to traditional manufacturing techniques. For instance, an initial prototype might reveal critical points of stress that can be addressed before mass production—reducing the risk of costly recalls or redesigns later on.
From Household Name to Your Next Big Idea
Injection molding is the driving force behind many indispensable household items, delivering precision-engineered products that are both innovative and resilient. From airtight food storage containers all the way to ergonomic kitchenware and durable maintenance supplies, this process underpins modern living through efficiency, practical design, and consistent quality. Pioneer Plastics harnesses advanced injection molding technologies to develop everything from custom plastic parts to specialized display solutions for collectors.
Ready to see how injection molding can transform your ideas into high-quality household products? Contact Pioneer Plastics to discover how their engineering services, tool building, and rapid production can help your business thrive in today’s competitive market.